Reducing Costs And Lead Times For Large Thermoforming Molds With Pellet 3D Printers
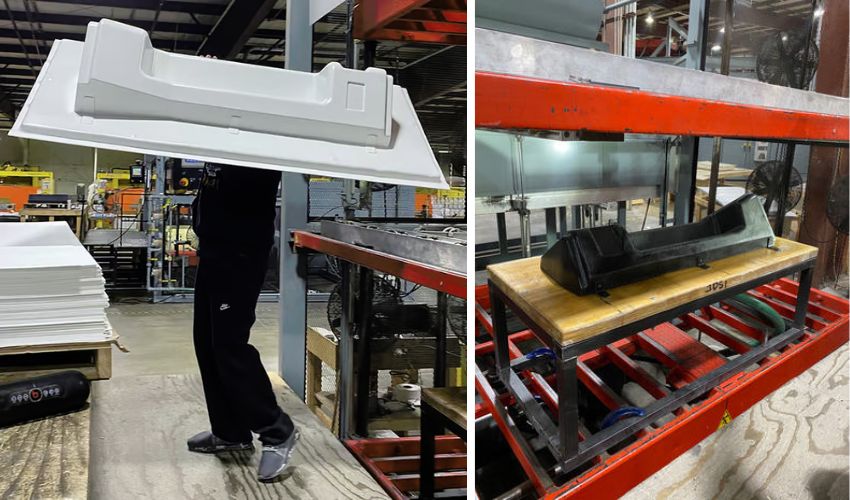
Over the past few years, we have seen a number of growing supply chain pressures. Starting of course with the COVID-19 pandemic wherein suddenly not only were crucial products running out quickly due to increased demand, but there were also a number of shortages just due to the nature of the crisis. Indeed, it has continued through 2023 notably due to exacerbations related to the Russian Invasion of Ukraine with some statistics showing that up to 80% of companies experienced at least one disruption. This is equally the case in the United States.
As a direct result, there has been a growing interest in adopting local, flexible manufacturing. Which is why more and more manufacturers are turning to additive manufacturing (AM) to create quality, cost-efficient products faster. One notable example is plastic thermoforming companies like Duo Form who have discovered how to leverage large-format extrusion 3D printing using low-cost plastic pellets to gain a competitive edge. They are producing medium-to-large-sized thermoforming molds in less than half the time, and at a fraction of the cost compared to traditional mold-making methods.
To learn more about this, join the next SPE live webinar “Reduce Costs And Lead Times For Large Thermoforming Molds With Ext Titan Pellet 3D Printers” on 3D printing large production molds for thermoforming with experts from 3D Systems and Duo Form on October 24 at 9:00 AM-10:00 AM EDT. Attendees will be able to learn more about how Duo Form has integrated AM into their manufacturing process, gaining agility by 3D printing production molds, tools and representative samples for thermoforming and vacuum forming.
Register for free to get access to the event and learn about:
- How pellet extrusion 3D printing enables up to 10X faster mold print times, with up to 10X savings on material costs
- Duo Form specific case studies and ROI examples
- Best practices that improve AM production and mold performance such as: how to print porous molds, using infill settings for improved vacuum pulls, and more!
- How to select the right AM solution, including options for additive-subtractive hybrid systems
Speakers
Dave Rheinheimer has 40 years of experience in thermoforming, working in all aspects of the industry including sales, production, product design, operations management, mold shop management and more. Throughout his career, Dave’s focus has been on improving designs and processing of thermoformed tooling and parts. Dave started his own thermoforming company, Majestic Formed Plastics, which was acquired by Duo Form in 2009. Dave currently leads the development of new products and improved products at Duo Form.
Nino Pecina is a robotics programmer and CAD engineer at Duo Form with 10 years of experience in the thermoforming industry. With three years of experience working with 3D printers and five years in tool and mold making, Nino currently operates the Titan pellet extrusion 3D printer at Duo Form to 3D print large molds and other parts as part of Duo Form’s manufacturing process.
Clay Guillory is a mechanical engineer with extensive experience in additive manufacturing, pellet extrusion 3D printing and CNC machining. Clay founded Titan Robotics in 2014, specializing in large-format 3D printer manufacturing and launching the Titan pellet extrusion and hybrid additive and subtractive systems. After the acquisition of Titan Robotics by 3D Systems in April 2022, Clay now leads the Titan branch of 3D Systems’ Application Innovation Group, expanding and developing new solutions for production additive manufacturing for industrial customers.
Bradley Mount is a 25-year veteran of additive manufacturing, including multiple plastic and metal AM solutions. Brad, as a technology sales and operations executive, has worked with hundreds of companies, enabling their successful adoption of additive manufacturing to address specific business, engineering, and manufacturing challenges. He now leads 3D Systems – Titan business development as Global Director.