Everything You Should Know About Rapid Prototyping in 3D Printing
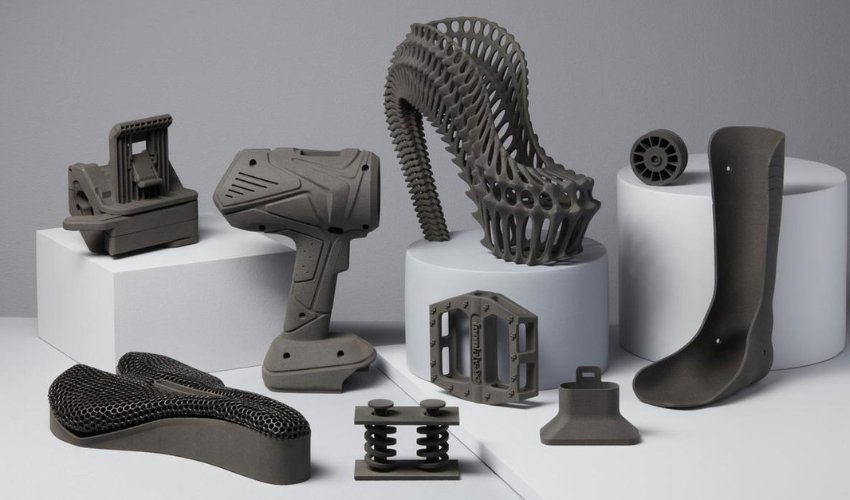
The product development landscape is constantly evolving, demanding innovative approaches to bridge the gap between ideas and reality. Rapid prototyping (RP) has emerged as a powerful tool in this realm, fostering creativity and efficiency. At its core, rapid prototyping is a methodology that revolutionizes the traditional design process, allowing for swift iteration and testing of ideas through the creation of tangible prototypes. This enables designers and engineers to receive valuable feedback early on and quickly implement suggestions, ultimately leading to a better, more reliable final product and increased user satisfaction. Below, we delve deep into the world of rapid prototyping, focusing particularly on its application within the domain of 3D printing.
What exactly is rapid prototyping? The process involves the rapid 3D printing of non-final, physical models from digital designs, allowing quick testing and refinement of parts and ideas based on real-world feedback and results. The first use of RP coincides with the emergence of additive manufacturing in the early 1980s. Initially used for rapid tooling and prototyping in industrial settings such as the automotive and aerospace sectors, continuous significant improvements within 3D printing technology have allowed RP to become monumentally more accessible and affordable for a broader range of industries and applications. Today, RP within additive manufacturing has facilitated significant innovations and is hailed for its flexibility and efficiency in product development, driving critical advancements across a variety of fields.
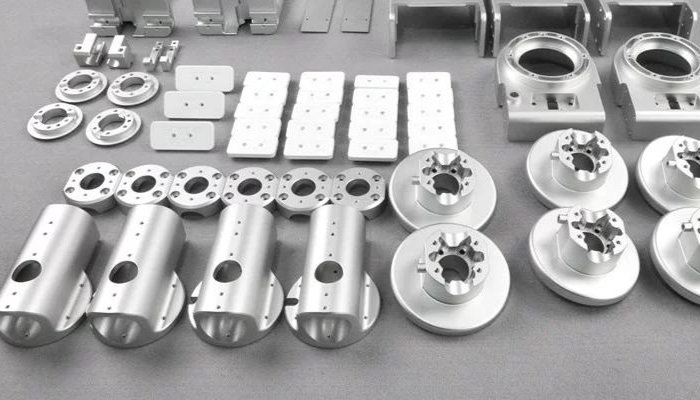
3D printed metal rapid prototypes. (Photo Credits: Wayken Rapid Manufacturing)
How Rapid Prototyping Works
Like all 3D printing processes, rapid prototyping done using AM begins with creating a digital design in CAD software. Once the design is finalized, it is sent to the 3D printer, which may print the prototype using thermoplastics, resins, metals, or composites. This results in a 3D printed, functional representation that closely mirrors the intended final part. The key advantage of this process is that it empowers designers to test their ideas thoroughly and rapidly.
Various printing processes are available for rapid prototyping, offering distinct advantages based on users’ requirements for visual appeal, material properties, and functionality. Choosing the most suitable method involves considering the trade-offs inherent in each and aligning them with the project’s specific needs.
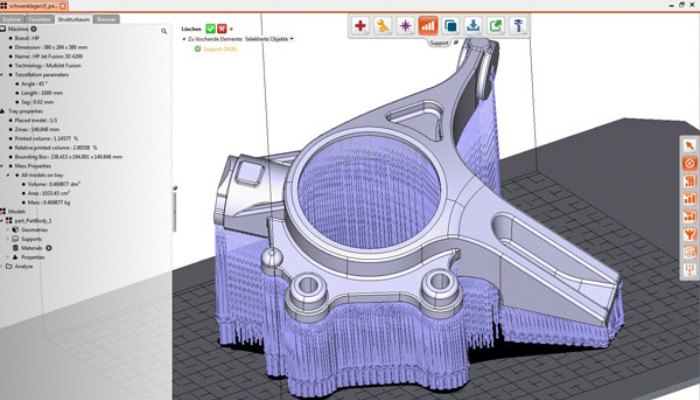
(Photo Credits: Additive Manufacturing Global)
Among these methods, Fused Deposition Modeling (FDM) is widely adopted, despite its relatively lower resolution and accuracy than other plastic 3D printing techniques, which may limit its ability to create intricate designs. Stereolithography (SLA) is often preferred for prototypes requiring high visual aesthetics, although a limited range of compatible materials constrains it, and it requires extensive post-processing. Selective Laser Sintering (SLS) stands out for its ability to deliver quick, high-quality prints with functional parts, but similarly to SLA, with restrictions on material options. Multi Jet Fusion can offer detailed visual output in prototyping with multiple materials, but at a much higher cost.
Although less popular, it is possible to also make prototypes using metal AM. For example, Direct Energy Deposition (DED) may be costly due to its industrial nature, but offers the capability to produce nearly net-shape metal prints. This has made it an attractive choice for prototyping in some applications despite its expense, even if it is not the main use of the technology. Similarly, Direct Metal Laser Sintering (DMLS) offers robust and functional parts, but at a higher material cost and within a limited build volume.
Types of Prototypes
But what kinds of rapid prototyping are there? Low-fidelity prototypes, more commonly known as proof-of-concept prototypes, represent the earliest and most basic stage of prototyping. These prototypes prioritize the most core functionalities with little to no consideration of the visual aspect of the part. While aesthetics and user experience aren’t primary concerns at this point, 3D printing’s speed and affordability can still be advantageous for creating these POC prototypes. This is where FDM is popular.
Visual prototypes, also known as appearance prototypes, place importance on aesthetics more than functionality. These models serve to showcase a product’s intended look and feel, including factors like shape, size, color, and surface texture. Vat photopolymerization or material jetting are often used.
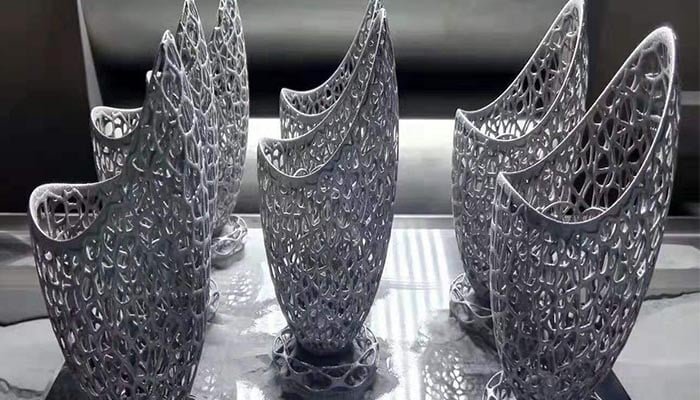
(Photo Credits: 3ERP)
In contrast, functional or working prototypes emphasize functionality with no regard to aesthetics. Designers utilize these prototypes to test individual features, one at a time. This allows them to verify if these features work well before incorporating them into the final product. This may be more suitable for SLS or DMLS.
Last but not least, engineering or pre-production prototypes are the culmination of all earlier iterations, as they integrate previous findings into a near-finished, final model. These prototypes can serve multiple purposes, including attracting customers and investors and establishing partnerships with resellers and manufacturers.
The Industry Applications of Rapid Prototyping
Rapid prototyping’s versatility extends across a broad spectrum of industries, each capitalizing on the process to streamline development and enhance product innovation. Within high-performance, high-output sectors like aerospace and automotive, RP plays a crucial role in designing and testing intricate components.
Aerospace engineers often use rapid prototyping to create lightweight, complex physical prototypes of components such as turbine blades and wing and satellite attachments for testing. This allows assessment of the final part’s performance, durability, and aerodynamics under real-world conditions. Similarly, automotive manufacturers leverage RP to develop and test prototypes for car parts like gears, engine components, and aerodynamic body panels, allowing for fast adjustments before mass production.
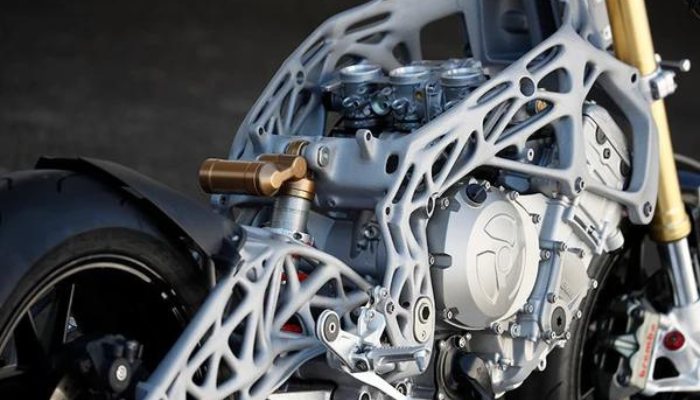
3D printed prototype of a motorcycle frame. (Photo Credits: Jian Hong Prototype)
Rapid prototyping has also revolutionized the medical field, enabling the creation of customized implants and prosthetics tailored precisely to individual patients’ needs. For example, surgeons can leverage this process to 3D print personalized bone grafts that match a patient’s unique anatomy or make modifications to prosthetics for easy integration with the body. Furthermore, rapid prototyping enables the development of complex medical devices, encompassing surgical instruments and patient-specific anatomical models crucial for training simulations and live surgical procedures.
As rapid prototyping has gained popularity, its use has transcended beyond industrial and medical applications. In the fashion and jewelry industry, designers increasingly turn to rapid prototyping to enhance their creative capabilities and more effectively realize their designs. Like aerospace and automotive engineers, these designers leverage rapid prototyping’s speed benefits. This enables them to easily create garment variations to keep up with evolving trends and meet the preferences of different customer segments without the need for extensive retooling.
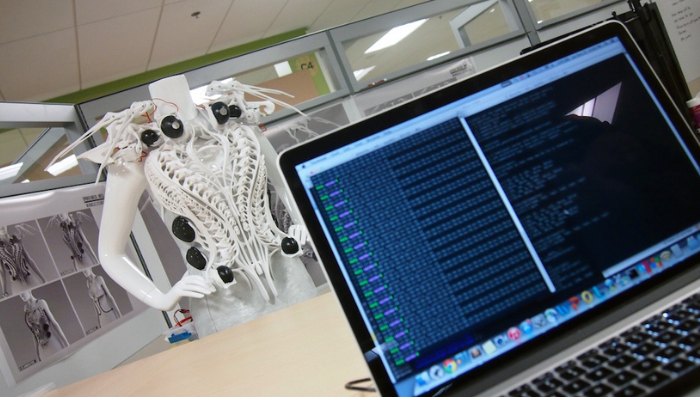
3D printed “Spider Dress” by Anouk Wipprecht. (Photo Credits: Anouk Wipprecht)
The Benefits of Rapid Prototyping
Rapid prototyping offers several unique benefits that significantly impact the product development process. One of its most notable advantages lies in its ability to improve the speed and efficiency of workflows, as it can greatly accelerate the development cycle. When designers and engineers turn to 3D printing, they can utilize the rapid prototyping process to quickly translate their digital designs into physical prototypes, reducing the time required to bring a product from concept to market. This substantial decrease in turnaround time can help companies stay ahead of their competitors and improve their flexibility and competitiveness, enabling them to respond to changing market demands and consumer preferences.
Additionally, rapid prototyping can fuel an iterative design process, allowing a broad spectrum of designs and concepts to be explored within a compressed timeframe. In the past, product development often meant waiting for a final product before receiving crucial user feedback, frequently leading to delays and potential rework. Unlike traditional manufacturing methods, rapid prototyping, when coupled with 3D printing, allows for immediate adjustments and implementation of feedback and test results. The outcome is a design process that fosters innovation and refinement in the product, as increased experimentation with different geometries, functionalities, and materials can optimize the final part.
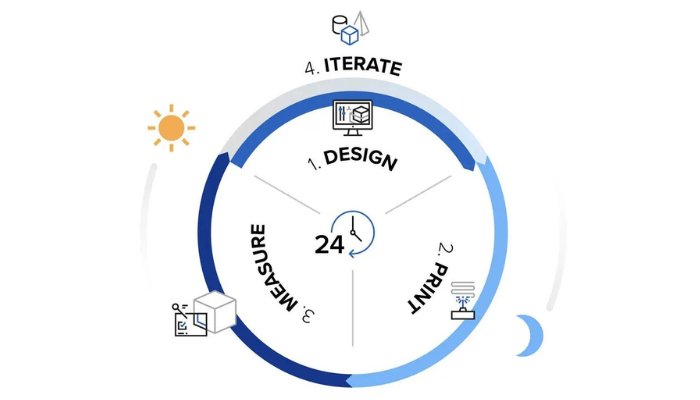
When coupled with 3D printing, rapid prototyping enables designers and engineers to cycle through digital designs and physical prototypes quickly, improving speed toward mass production. (Photo Credits: Formlabs)
Did you know about the Rapid Prototyping process and its benefits? Let us know in a comment below or on our LinkedIn, Facebook, and Twitter pages! Don’t forget to sign up for our free weekly newsletter here for the latest 3D printing news straight to your inbox! You can also find all our videos on our YouTube channel.
*Cover Photo Credits: Formlabs