APG Manufactures Lathe Chuck Jaws with Tritone’s MoldJet Technology
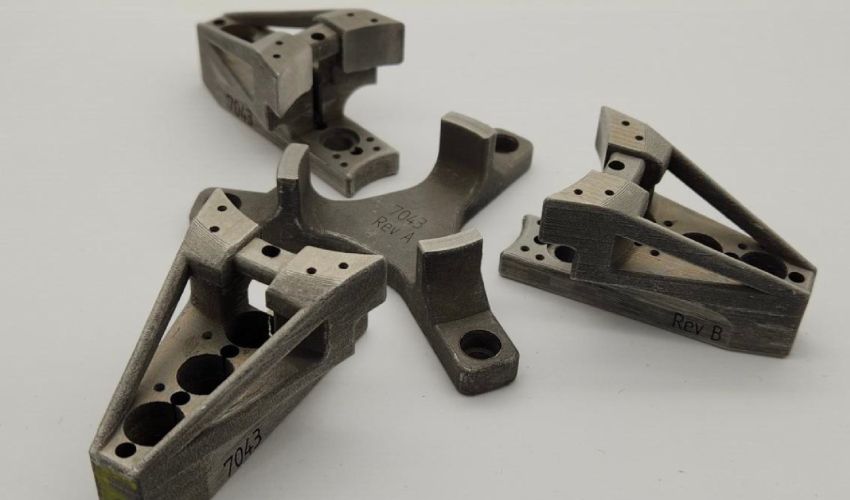
One of the best-known advantages of 3D printing, which is appreciated by different industries, is freedom of design. While still having to follow rules with certain limitations depending on the part to be produced, Design for Additive Manufacturing (DfAM) allows for geometries and performance that often cannot be achieved by other methods. Techniques such as generative design or topological optimization are increasingly being used in conjunction with 3D printing to reimagine the design of parts in unconventional ways and make them perform better, lighter, and more optimized.
U.S.-based Alpha Precision Group (APG), a leading supplier of precision components, specialty valves, and powder metal components, decided to use 3D printing for this very purpose, to find a solution to a problem that could not be solved by other techniques. By redesigning and 3D printing lathe chuck jaws, previously made by CNC machining, the company was able to improve its production process. But how did they do this?
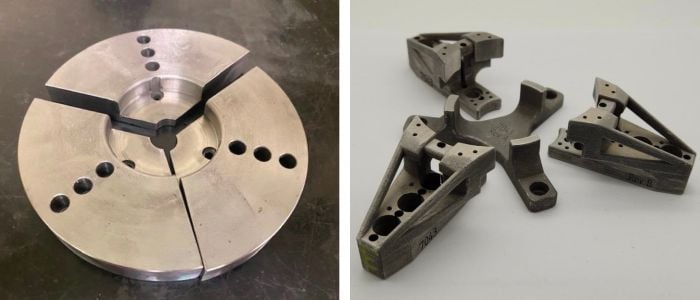
On the left, the original CNC-produced chuck design. At right, the new lightweight chuck jaw produced with Tritone‘s MoldJet additive technology.
Design for Additive Manufacturing to Achieve Lighter Spindle Jaws
In operation for more than 50 years, APG has brought together, under its brand, pioneering companies in materials and process improvement technologies. The company now works with a variety of techniques, including metal injection molding (MIM) and additive manufacturing.
One of the latest examples of APG’s use of metal additive manufacturing to produce end-use parts was the 3D printing of new lathe chuck jaws. The use of additive manufacturing was dictated by a specific issue at one of the company’s metal powder plants. The problem lay in the excessive weight of the chuck jaws, which jeopardized adherence to critical tolerances during part machining.
Conventional mild steel jaws, used to hold gears during machining, were too heavy and generated excessive centrifugal force when the lathe was spinning at high speed. High clamping force was therefore required to hold the part, which resulted in distortion.
After trying to reduce the weight of the jaws with CNC machining, without satisfactory results, the project was turned over to the company’s Additive group, which explored new ways to improve the mechanism. APG’s Additive group envisioned a redesign of the jaws, taking full advantage of the benefits from 3D printing, including the greater design freedom offered by DfAM.
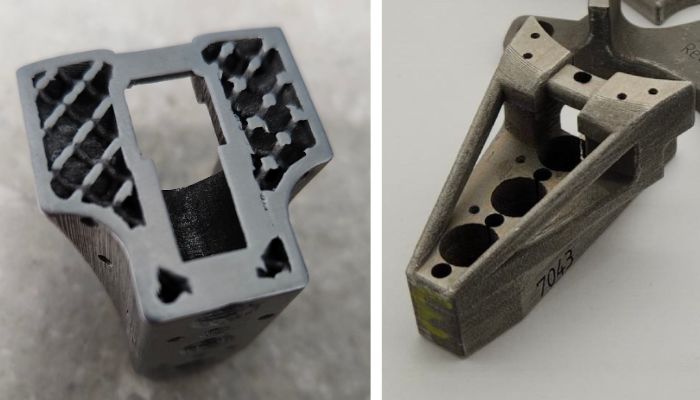
Left, the cross section of the new spindle jaw with internal lattice design. At right, the detail of the new outer jaw design.
To minimize the weight of each component of the system, APG had to redesign the exterior and interior of the components, opting for internal lattice structures. As for the technology used to achieve these complex structures, the choice fell on Tritone’s MoldJet metal additive manufacturing process.
Tritone’s MoldJet Additive Technology
MoldJet technology is an innovative additive process for metal and ceramics that, instead of relying on powders, uses a paste, enabling the production of parts at scale and at a remarkable speed. It was developed by Israeli manufacturer Tritone, which designed MoldJet to produce parts of complex geometry, with high density and in medium volumes. Tritone’s Dominant system was used to make the jaws.
The process works in several steps and with multiple print trays, which operate in parallel and independently. The first step is the printing of polymer molds, the second is the deposition of the metal paste in the molds, the third is the thermal phase, solidifying the material using hot air, and finally there is the quality control of the layers in real time with automated correction, using cameras equipped with AI.
One of the advantages of this technology is the flexibility offered, which allows, for example, to easily change material cartridges, to produce parts with different layer thickness or different geometries in one process. In addition, post-processing is very simple as the polymer molds are completely dissolved, leaving parts ready for sintering.
In the case of APG, these aspects were key to achieving the goal of jaw weight reduction through a proprietary lattice geometry for all components. This was achievable with MoldJet technology precisely because, during printing, all the void space in the lattice was occupied by soluble mold material. This material was then eliminated with Tritone’s hands-free post-processing, allowing for a much lighter structure than could have been produced with competing technologies.
Part and Manufacturing Process Optimization Through 3D Printing
The results of the project also exceeded APG’s expectations. The weight of the jaws was reduced by 84% (from 2.13 KG to 0.336 kg) and the clamping force was reduced by 67% from the original design (from 30 to 10 psi). This achieved the stated goals and resulted in tighter tolerances, less scrap, reduced lathe wear with lighter loading, and overall lower cost than other explored weight reduction alternatives.
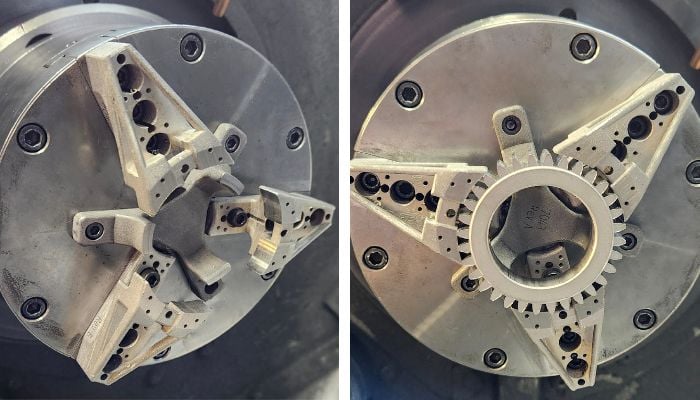
The new set of jaws installed on the lathe, with the gear component in place.
Joe Taylor, Manufacturing Engineer at APG commented “We are thrilled with the results of this program. We look forward to expanding this success internally across our facilities and offering these fixtures on a ‘turnkey’ basis to customers.”
Ultimately, Tritone’s MoldJet technology not only enabled the resolution of the clamping force issue, but also offered the potential to improve overall repeatability and throughput rates in manufacturing processes, bringing greater operational efficiency, accuracy and reliability to machining operations. You can learn more about MoldJet technology and its benefits HERE.
How could you envision using capabilities like this in your operation? Let us know in a comment below or on our LinkedIn, Facebook, and Twitter pages! Don’t forget to sign up for our free weekly newsletter here, for the latest 3D printing news straight to your inbox! You can also find all our videos on our YouTube channel.
*All Photo Credits: Tritone Technologies, Alpha Precision Group