Plasmics Combines Individual Requirements and High Quality Standards With Innovative FDM Printing
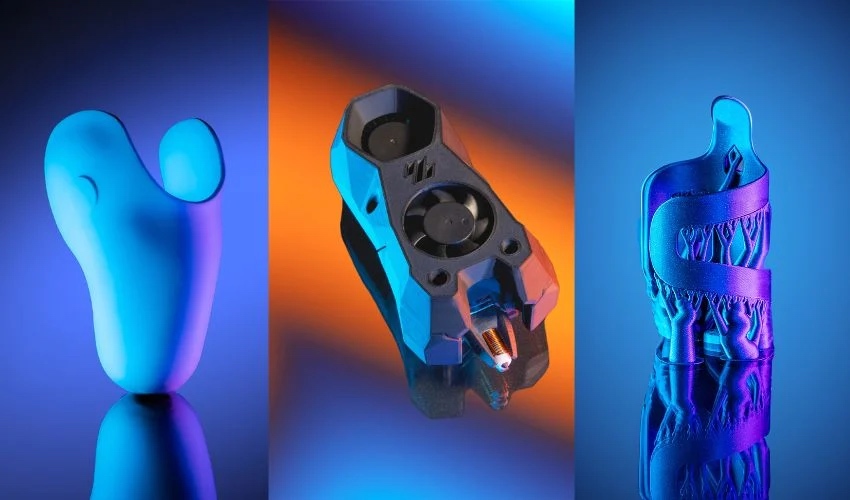
Plasmics, Austrian company based in Vienna, was founded in 2018. What is interesting about the company is that it seeks to develop pioneering 3D printing solutions that do not require years of specialist knowledge. This has lead to Plasmics estbalishing itself in numerous industries with its claim to high-quality and innovative printing solutions and currently primarily covers applications in medical technology, industry and sport.
For example, last year, the company presented its DeltaS FDM printer at Formnext, which is known for its design and user-friendliness. The open system makes it possible to print numerous materials with outstanding quality and speed. The in-house INo Trident hotend is responsible for this. This induction hotend is able to heat up to 250° in just four seconds and amazed more than just the 3Dnatives team at Formnext 2023.
In an interview with founder Konrad Schreiner, we had the opportunity to find out more about how Plasmics was founded and the development of its innovative products. We also talked about how 3D printing will develop in the coming years and what contribution Plasmics would like to make to this.
3DN: Could you briefly introduce yourself and tell us how you got into 3D printing?
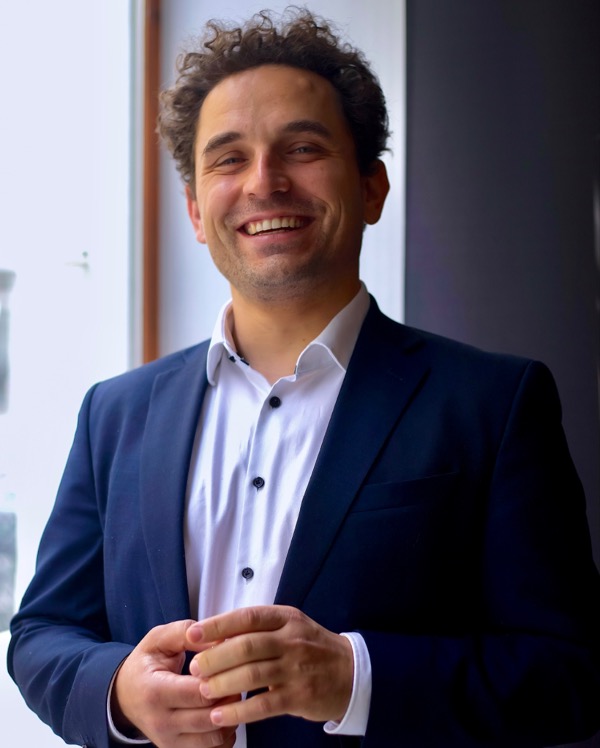
Konrad Schreiner, founder of Plasmics
Hello, my name is Konrad Schreiner and I am the founder of Plasmics. I got into 3D printing after I almost lost my big toe while skiing. The fact that there was no sensible solution for personalized ski boots and insoles came as quite a shock to me at the time.
Although I had a business degree, I had always had a passion for mechanics and technology. Back then, even before the first kits, I had a lot of fun experimenting and building functional parts. Even at that time, I found building a machine that could produce things rewarding and, because of my personal history, I decided to leave my job in the pharmaceutical sector and enter this exciting field. The fascination with 3D printing and its potential to solve problems in innovative ways then motivated me to found Plasmics.
3DN: How did Plasmics come about and what is the aim of the company?
Originally, we wanted to specialize in ski boots. But after the first prototypes and further research, we identified the key problem as to why there was no one doing this. It was the lack of quality and reliability in FDM printing.
If you are skiing in a steep and inaccessible area, for example, the reliability and quality of the equipment can be the difference between life and death in the worst case scenario. This experience inspired me to look for a solution that would allow us to produce personalized products using multi-material 3D printing with reliable quality to address the key problem. This challenge needs to be addressed in the areas of sports equipment, medical devices and protective equipment. These are also the areas in which we specialize.
Our team at Plasmics is revolutionizing manufacturing and supply chains. We are on a mission to develop high-quality, qualifiable 3D printing that is accessible to everyone and requires no specialized skills. Our pursuit of innovation and our commitment to quality and sustainability drive us to push the boundaries of 3D printing and shape a future where our customers combine individual needs and the highest standards.
3DN: Could you go into more detail about the different products from Plasmics? Who are the products targeting?
Plasmics offers a number of specialized solutions for various applications. Our flagship technology is the DeltaS 3D printer, which we have equipped with our innovative INo Trident hotend. We have designed the DeltaS as a complete printing solution and it is capable of processing, tracking and recording almost all particularly demanding materials. This makes it particularly suitable for prototyping and the production of small batches of everything from spare parts to orthopaedic products.
Our solutions include the induction-heated hotend with the best temperature control currently available in FDM printing and the filament sensor array for precise control of filament quality dimensions. Both are unrivaled on the market and we hope that with them, poor prints due to filament quality fluctuations during printing are a thing of the past.
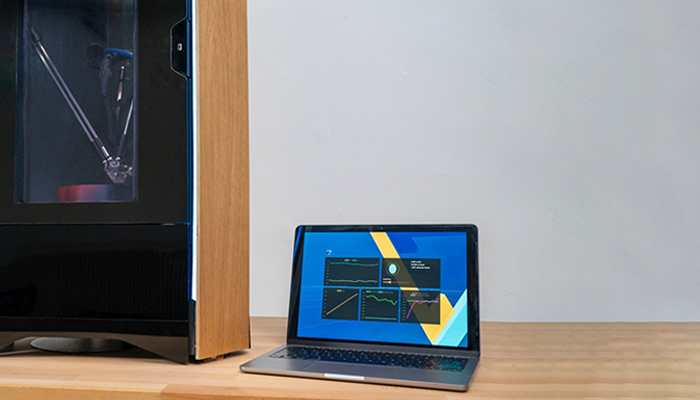
The filament sensor array ensures precise filament quality dimensions.
Furthermore, our inline auditing allows our customers a complete, automated quality analysis of all printed parts. The machines are also equipped with a machine learning mechanism. The more frequently the printers are put into operation worldwide, the more the underlying AI will help our customers to always achieve the best possible print quality.
We also have a custom-made solution for printing insoles that can rival those made by a Podiatrist! Feetneeds, our latest addition, is an innovative solution for the production of customized insoles. By using Plasmics’ own 3D printing technologies and working closely with medical experts, we provide them with a hands-off solution for insole production. The Feetneeds printers are therefore aimed at shoe manufacturers, shoe sellers, orthopaedic companies and other facilities where customer foot health is a priority.
Our 3D printing technologies provide our users with an ultra-compact and fully automated production machine that produces insoles within an hour. Our insoles meet medical standards and offer an optimal fit, shock absorption and durability, alleviating or even preventing foot problems. We work closely with medical experts and shoe manufacturers to ensure that our products meet the highest quality and safety regulations. We are currently working on being able to manufacture such solutions via the DeltaS.
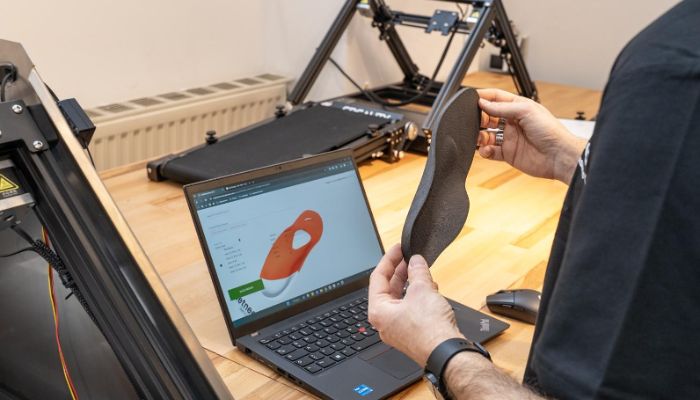
Feetneeds is an innovative solution for the customization of insoles
3DN: To what extent are the DeltaS printers self-learning and how does this benefit the end user?
We have equipped our printer with a camera that captures the printed objects from predefined perspectives, derives information from them and then makes the aggregated data available for a learning algorithm. The machines are thus distributed around the globe – and thus decentralized – but all learn independently and for a common purpose.
By combining computer vision and machine learning, our customers achieve automated quality control and error correction. This increases the user-friendliness of our printers and reduces the need for specialized expertise. The purpose of this technology is to make 3D printing accessible to all users and improve the efficiency of printing processes.
3DN: Could you tell us more about the INo Trident hotend? Why did you choose an induction hotend and what advantages does it offer?
The INo Trident is an essential component of our 3D printing solutions. It is an inductively heated hotend. Instead of using conventional heating cartridges, the INo Trident converts energy into heat by using a modulated magnetic field. This magnetic field transfers the energy “wirelessly” from the coil to the nozzle. This works in a similar way to an induction stove. This has allowed us to reduce the mass on the nozzle, enabling much faster heating and cooling, as well as constant temperature control during the printing process.
This innovative solution allows for consistent extrusion and thus contributes to improved print quality, especially when used in multi-material printing and when using temperature-dependent filaments. I am convinced that our hotend will open up even more functions in 3D printing in the future.
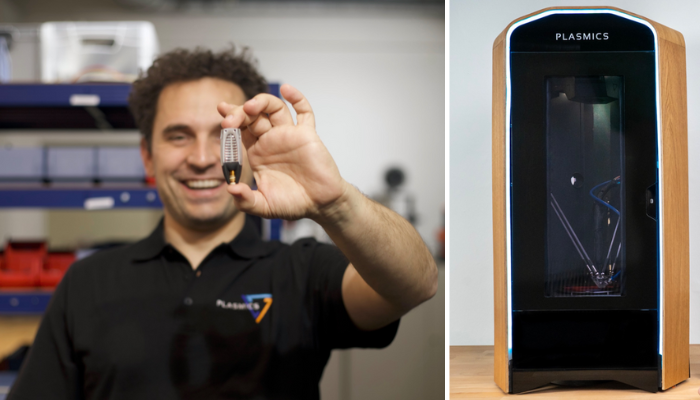
The innovative Plasmics Hotend INo Trident (left) and the DeltaS 3D printer (right)
3DN: Where do you see Plasmics’ products in the current market for 3D printers and accessories?
In fact, we also sell the INo, the induction nozzle, and the FourRunner, our 4-wheel-driven extruder, separately! Both products are competitively priced. Even though the INo has higher initial costs than regular hotends, the purchase pays for itself very quickly, especially for professional use (OEE >70%). Even we haven’t used a nozzle to its full extent yet, and the energy savings of 25-40% compared to conventionally heated hotends are also interesting. In any case, the unique internal geometry makes it easier to press any material.
The INo is an effective tool for “professional users” who are looking for a reliable product and want to turn away from low-performance cheap alternatives. In addition, with the hotend we guarantee an improvement in print quality, efficiency and user-friendliness and save resources in terms of energy and filament, as INo users hardly ever produce misprints.
At Plasmics, we have developed our core technologies in the heart of Europe. We are at the leading edge of what is possible with FDM 3D printing and also produce locally. We are proud that innovation comes from our company and that we are talking to customers from Europe to the USA and Japan.
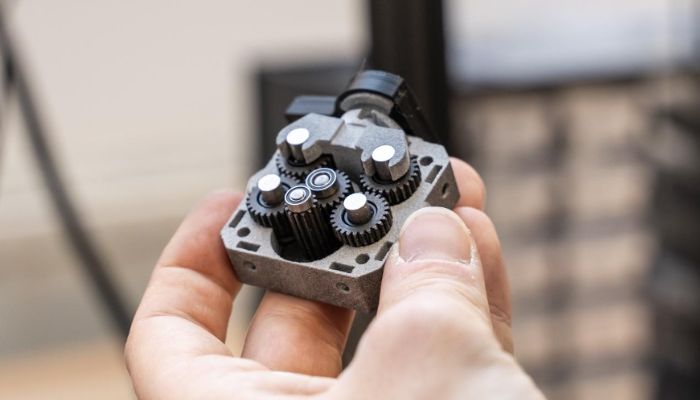
The Plasmics FourRunner extruder can also be purchased individually
3DN: Where do you see Plasmics and 3D printing in the next 5-10 years?
In the next 5-10 years, I see Plasmics as the leading provider in the production of 3D-printed insoles through our Feetneeds brand. We are once again providing orthopedic technicians and medical professionals with direct product (ion) expertise. At Plasmics, our induction nozzle in particular will help to localize manufacturing processes – keyword “nearshoring” – as well as significantly accelerate and customize them. We will make a significant contribution to the further development of 3D printing.
Thanks to our expertise in the field of additive manufacturing, we bring important impetus to the market with the most reliable combination of hardware and software. We show that our customers use FDM technology as a cost-effective and high-quality scaling technology and take FDM to a new level.
3D printing as a production method has undergone rapid development in recent years and I continue to see it as a driving force for innovation and change in various industries. Over the next 5-10 years, additive manufacturing will continue to gain traction in areas such as industrial manufacturing, medicine, aerospace and many other sectors, providing innovative solutions to complex challenges.
Moreover, in 10 years, 3D printing will replace further steps of current manufacturing and thus stabilize production chains. Even if a container ship gets wedged in the Suez Canal, we will be less dependent on such imports in the future. This will also make 3D printing more sustainable. So the future looks bright.
3DN: Do you have any last words for our readers?
Innovation is particularly important to us. From the very beginning, Plasmics has focused on innovative solutions to bring about change in order to respond even better to customer requirements. We also see innovation as the only logical way forward. There are some very interesting 3D printing companies in Europe at the moment and we celebrate all those who are going out on a limb to achieve something new in FDM 3D printing.
We are convinced that many new ideas will emerge and that FDM printing in particular will continue to develop thanks to its ease of use. We are already excited and look forward to being part of this journey. If you would like to find out more about us and our products, take a look at our website!
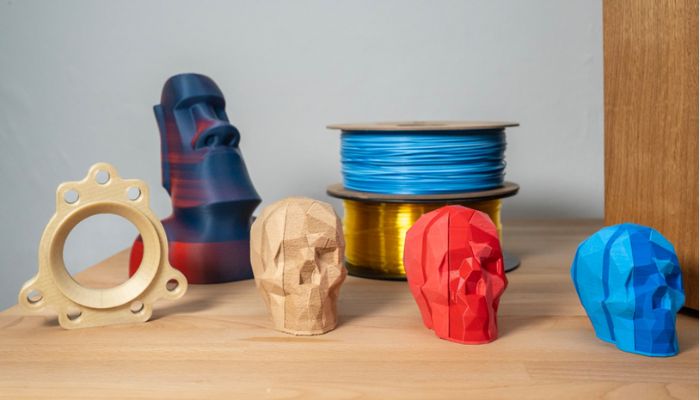
Plasmics is committed to high-quality FDM 3D printing with its products.
What do you think of Plasmics? Let us know in a comment below or on our LinkedIn, Facebook, and Twitter pages! Don’t forget to sign up for our free weekly newsletter here, the latest 3D printing news straight to your inbox! You can also find all our videos on our YouTube channel.
*All Photo Credits: Plasmics