Choosing a 3D Printer: A Closer Look at 5 Models on the Market
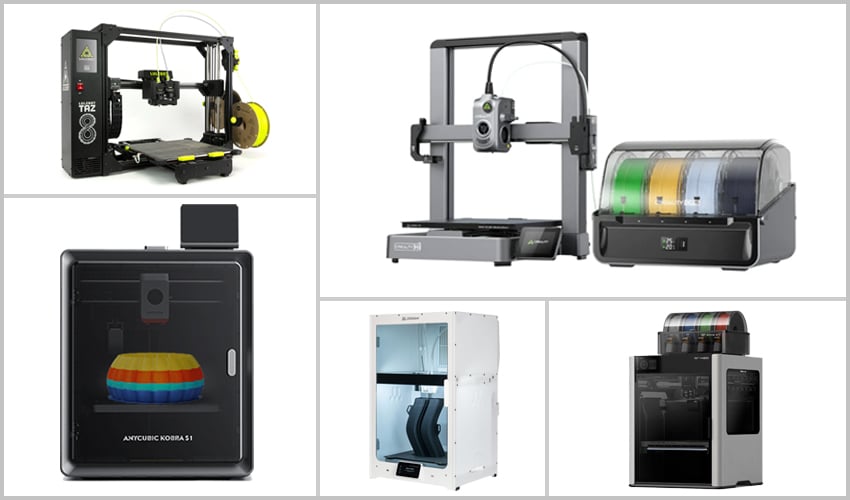
The number of 3D printers on the market has increased exponentially in recent years, giving anyone access to machines of different brands and price ranges available, making a wide range of printing technologies accessible, including FDM, SLA, SLS, and PBF. And 2025 has been a particularly prolific year in this respect. Indeed, there have been numerous anticipations and revelations of new 3D printers that have stirred both the industrial sector and maker community. That is why, today, we will introduce you to the five printers that have broken into the additive manufacturing market this year. If you are undecided on which printer to buy to bring your projects to life, this article is here to help.
H2D 3D Printer – Bambu Lab
On March 25, the long-awaited new 3D printer from Bambu Lab was finally officially unveiled. What’s exciting about it? Well, the H2D goes beyond a simple 3D printer and also features tools for laser engraving and laser cutting, thus providing creative professionals with an all-round device. This is why the H2D is also equipped with a 455 nm laser in either 10 W or 40 W. Furthermore, the device also impresses with its functions and innovations related to 3D printing. The printer has a volume of 250 x 320 x 325 mm and a dual nozzle system. The hotend can be heated up to 350° and the maximum printing speed is 1000 mm/s. The range of materials has also been extended. It is also possible to print carbon fiber or glass fiber reinforced filaments. The functions of the device can be controlled remotely via the cloud, which makes it even more user-friendly. Another highlight is the revised AMS. This tool for drying, storing and feeding filaments now has servo motors. These further accelerate printing and ensure fast results.
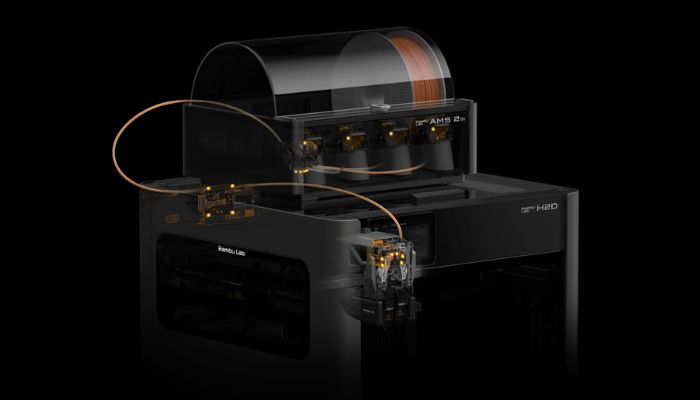
Image Credits: Bambu Lab
S8 – UltiMaker
Another new 3D printer to highlight this month is the UltiMaker S8. According to the manufacturer, this machine boasts four times higher productivity as compared to the previous machine as well as improved quality, thanks to the new UltiMaker Cheetah motion planner. This provides increased speed thanks to an integrated accelerometer, a new feeding system, and improved firmware. The dual FDM printhead design allows any two materials, including composites, to be combined with minimal material waste and high reliability. In terms of specifications, among others, the machine features: a print volume of 330 x 240 x 300 mm, a dimensional accuracy of ± 0.15 mm ± 0.15 percent, extrusion speeds of up to 35 mm3/s, and nozzles of 0.25 millimeter, 0.4 millimeter, 0.6 millimeter, and 0.8 millimeter.
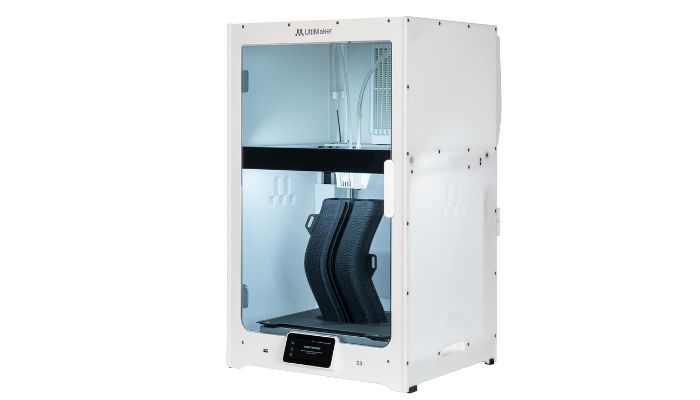
Image Credits: UltiMaker
TAZ 8 3D Printer – LULZBOT®
TAZ 8 is the newest FFF 3D printer from American manufacturer LULZBOT®. With a large print volume of 295 x 295 x 285 mm and an extrusion speed of 500 mm/s, it is a robust and versatile solution, ideal for making jigs, durable prototypes and production support tools. One of the strengths of the TAZ 8 is the ability to choose the extrusion head best suited to specific printing needs. Options include Meteor 285, for processing flexible materials such as TPU; Asteroid 285, useful for printing large parts with thick layers; and Twin Nebula 175, suitable for projects requiring the use of multiple colors or materials. The print bed, which is magnetic and easily interchangeable, can reach 110 degrees. The TAZ 8 supports a wide range of materials, including PLA, TPU, ABS, PETg, PVA, PVB, Nylon and PC, as well as all those with a melting temperature below 290 degrees Celsius.
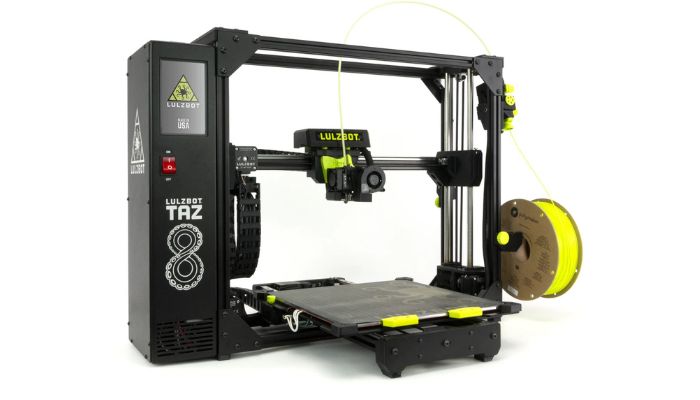
Photo Credits: LULZBOT
Hi Combo – Creality
The manufacturer Creality recently presented its new FDM 3D printer, the Hi Combo. With a print volume of 260 x 260 x 300 mm and a speed of up to 500 mm/s, it can design objects with multiple colors (up to 16, according to the company). It is compatible with PLA, PETG and carbon-fiber-reinforced PLA. Its touch screen makes it quick and easy to manage the colors available, so you can play with the hues to take your creations to the next level. As an option, you can equip your Creality Hi Combo with the Creality CFS, a solution that manages your filaments: it enables automatic loading and drying of spools to guarantee high-quality prints.
Kobra S1 3D Printer – Anycubic
Anycubic has launched the Kobra S1, a CoreXY-designed 3D printer, which enables print speeds of up to 600 mm/s without compromising quality. Its 250 x 250 x 250 mm build volume makes it ideal for medium-sized projects. Compatible with a wide variety of plastic filaments, its easy-to-remove hotend can reach 320°C, ensuring smooth, clog-free printing. In addition, it incorporates an aerospace ceramic throat tube, offering high thermal resistance and a low-friction surface. Among its outstanding features, it has an adjustable 4.3-inch touch screen, an ultra-quiet printing system of up to 44 dB and quick installation. It also supports nozzles from 0.2 mm to 0.8 mm, providing versatility for different levels of detail and speed.
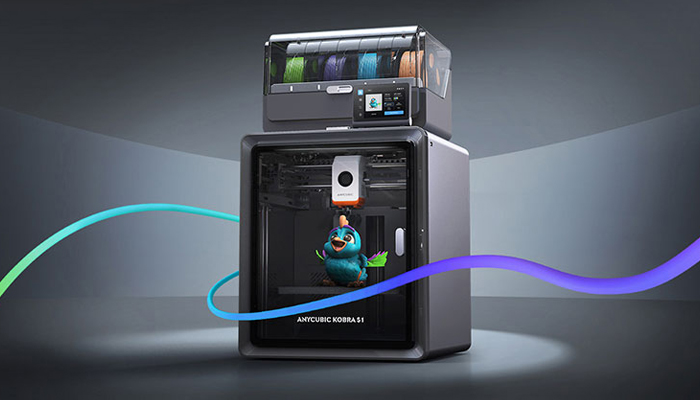
Image Credits: Anycubic
What printer do you prefer? Let us know in a comment below or on our LinkedIn, Facebook, and Twitter pages! Don’t forget to sign up for our free weekly newsletter here for the latest 3D printing news straight to your inbox! You can also find all our videos on our YouTube channel.
I appreciate your advice. Here, I learned a lot of intriguing things.