Sinterit Is Paving the Way for Industry 4.0 With its SLS 3D Printers
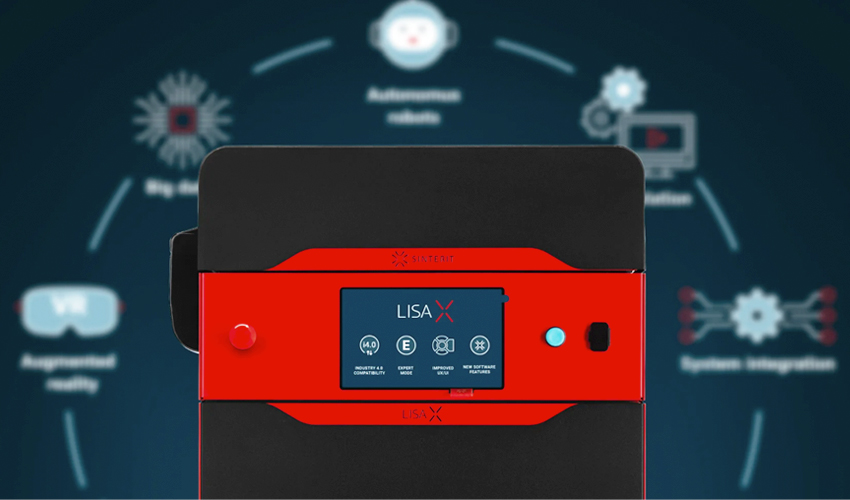
In recent years, there has been a substantial change in the way industries and companies operate. This transformation, known as Industry 4.0 or the Fourth Industrial Revolution, consists of the integration, automation and digitalization of all industrial manufacturing and production processes. In it, we find different technological tools, such as simulation, augmented reality, cybersecurity, big data, and of course, additive manufacturing. 3D printing plays a fundamental role in this shift, offering advanced technologies for different industrial applications. One widespread polymer additive manufacturing process is selective laser sintering (SLS). In this market, one of the first companies born with the aim of offering SLS 3D printers is Sinterit. A specialist in powder technology since its inception, Sinterit has long been strengthening its position in the industry through its Lisa, Lisa X and Lisa Pro 3D printers. The question now is, how are these SLS solutions and technological advances changing the additive manufacturing sector? And what is Sinterit’s role in all this digital transformation?
Headquartered in Krakow, Poland, Sinterit has been in business since 2014, when the first wave of companies offering compact, accessible and affordable SLS 3D printers emerged. Since the launch of its first machine, the Lisa, the company has gradually grown in the industry to position itself as one of the leaders in SLS 3D printing. And while additive manufacturing is now close to the prerogatives of Industry 4.0, there are still many improvements to be made. To dig deeper into this topic, we will delve into how an application programming interface (API) tailored to Sinterit SLS printers can optimize production. Furthermore, we will take a closer look at why a company should consider implementing Industry 4.0 in its additive manufacturing projects. Finally, we will learn of the success stories of users who have already used Sinterit machines as a complement in their production to get closer and closer to this digital transformation.
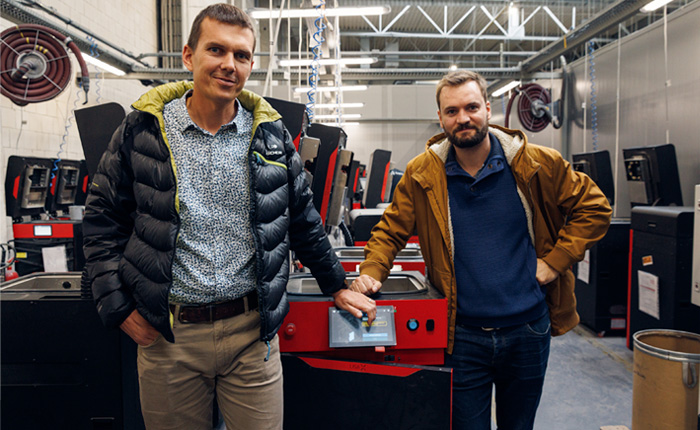
The Lisa X is one of the SLS 3D printers that are ready for Industry 4.0.
Sinterit and Industry 4.0
As we can see, the fourth industrial revolution and additive manufacturing have a close collaborative relationship. This means that, although 3D printing is a key element in this digital transformation, the tools that are part of Industry 4.0 can also be a significant factor in companies’ additive manufacturing projects. So how can both elements be used in a complementary way, and what are the benefits of each? 3D printing makes it possible to create complex final parts with a lower expenditure of materials, with lower costs and in a much shorter time. Industry 4.0, on the other hand, is characterized as a smart, connected manufacturing system that aims to provide information and identify potential mishaps. The reason that should motivate organizations to consider its implementation is the improvement of productivity, optimization of energy resources and workers’ safety, as well as production efficiency.
Having understood both aspects, let’s see how companies can combine them and make the most of them in their production processes. Sinterit has developed an API (application programming interface) for the Lisa X, which enables its integration into Industry 4.0. Sinterit’s Lisa X is the fastest and largest compact SLS 3D printer in its product portfolio. Moreover, thanks to this API, the printer shares data with the production system via bidirectional communication. In addition, it allows more print jobs to be queued, speeding up the transition from one process to the next, even if for safety reasons the print start is done manually. There is also the possibility of live monitoring of the 20 most important operational and security parameters. In short, these new features make the Lisa X 3D printer ready for Industry 4.0. With it, companies will be able to make better use of resources, resulting in higher throughput and fewer quality problems in the final parts. In turn, program optimization results in faster production, making this solution an ideal choice for a multitude of applications.
Regarding the implementation of the fourth industrial revolution in additive manufacturing processes, the Sinterit team explains: “This will allow you to fully integrate 3D printing into the structure of your company and better understand the entire manufacturing process. It goes hand in hand with achieving total transparency. With Industry 4.0 implemented in your additive manufacturing projects, you will be able to predict maintenance needs and proceed with them smoothly.” Added to this is the significant reduction in associated costs through better use of equipment and optimization of production batches. It is worth noting that for users residing in EU countries it is also possible to apply for Industry 4.0 grants, an initiative that further promotes the adoption of new technologies by companies.
Uses of SLS Technology in Industry 4.0
To demonstrate the capabilities of SLS 3D printing in this industrial transformation, Sinterit has shown a couple of success stories of its technology. The first is the Jetson One aircraft, designed to bridge the gap between driving a car and flying a plane. To create the prototypes and final components, Jetson turned to additive manufacturing in search of a system that would make high quality and precise parts. According to the founders, access to SLS technology was made much easier by Sinterit’s Lisa X 3D printer. Alec Bialek, R&D director at Jetson, emphasized the importance of rapid iteration in their development process and the value of a 3D printing partner like Sinterit. As such, the machine proved to be a valuable tool for Jetson in enabling them to create final parts for their aircraft, such as brackets, bezel trims and jigs. All of this also improved efficiency and reduced errors in the assembly process.
Another example is Somfy, a leader in the automatic operation of doors and windows, which has adopted additive manufacturing for prototyping and improving its designs. Based in Cluses, France, the company made a bet on new technologies by creating its own in-house 3D printing lab. Although it initially only had FFF solutions, it decided to make the leap to SLS manufacturing for its productivity and design freedom. To this end, Sinterit’s Lisa Pro and Lisa X SLS 3D printers became a key part of Somfy’s prototyping and manufacturing processes, offering cost savings and increased accuracy. They could create complex parts and durable components without the expense of traditional manufacturing methods. Jonathan Caillat, additive manufacturing and machine shop manager, explains, “It’s a good way to start with a compact 3D printer. It gives room for improvement, and also a good compromise in terms of cost and capabilities.”
If you want to learn more about Sinterit and their 3D printing solutions, feel free to visit them during the next edition of Formnext (Hall 11.1, Stand C29). You can also visit their website, HERE.

Sinterit has developed an API which makes Lisa X ready for industry 4.0 integration.
What do you think of Sinterit’s role in Industry 4.0? Let us know in a comment below or on our LinkedIn, Facebook, and Twitter pages! Don’t forget to sign up for our free weekly Newsletter here, the latest 3D printing news straight to your inbox! You can also find all our videos on our YouTube channel.
*All Photo Credits: Sinterit