AMGTA Study Tests Sustainability of Energy Dynamics in Metal AM Feedstock
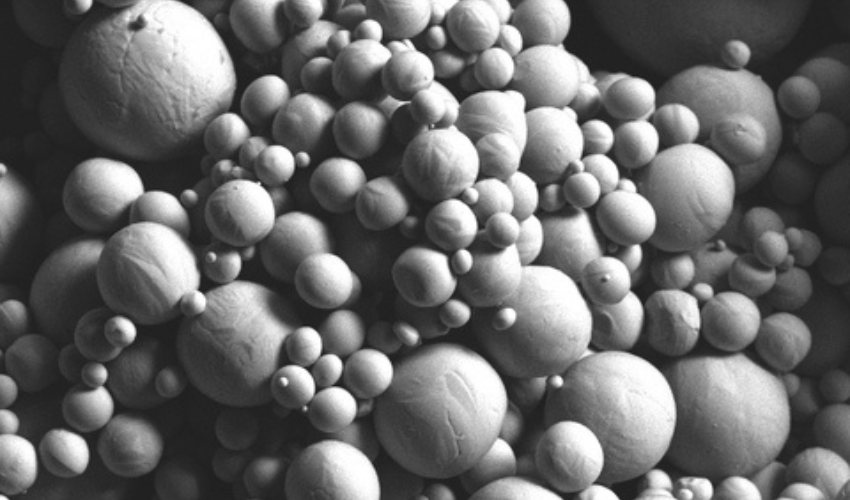
In recent years, additive manufacturing has seen a surge in focus on sustainability, driven by the combined efforts of industry leaders and organizations like the Additive Manufacturer Green Trade Association (AMGTA). Last week, a research study shed light on the intricate balance between energy consumption, environmental impact, and manufacturing efficiency within the AM ecosystem.
The AMGTA, a driving force in testing and promoting environmentally beneficial AM practices, recently unveiled the first results of its new study, “Specific Energy of Metal AM Feedstock: A Comparison.” This study, conducted in partnership with research consultancy Syntec Associates and industry innovator Divergent Technologies, delved into the energy requirements of various metal AM feedstock processing approaches.
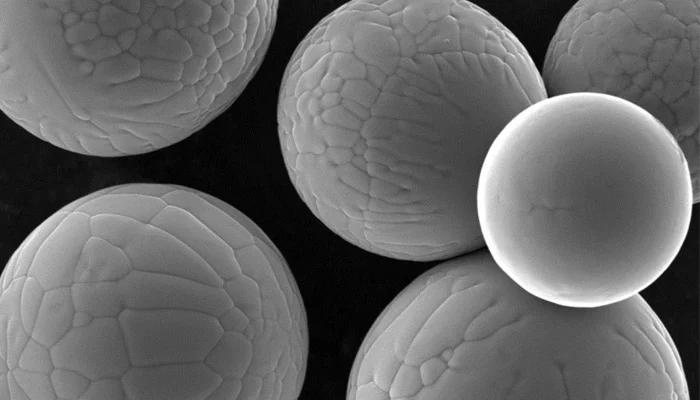
Powder is one of the main obstacles to the development of metal additive manufacturing
Gas atomization, mechanical milling (specifically ball milling), and wire drawing emerged as the primary focus for sustainable feedstock production. Gas atomization, while often praised for its potential in producing stock powders, faced criticism within the study due to producing wide variations in reported energy consumption. The research delved further, detailing the interplay of material properties, gas selection, and process parameters influencing energy consumption during gas atomization.
On the other hand, mechanical milling, a process synonymous with particle size reduction, showcased promising potential as a more energy-efficient alternative to gas atomization within additive manufacturing. The study revealed significant improvements in specific energy consumption (the amount of energy needed to produce a specific material), with mechanical milling, which is strongly evident in the ball milling process. Two key findings of this portion of the AMGTA study include that Harder materials require more energy to break down during the ball milling process, while producing finer particles requires significantly more energy.
Wire drawing, a method often overlooked in discussions of AM feedstock production, also emerged as a critical player in the sustainability narrative. The study highlighted the material-dependent characteristics of wire drawing and its potential for reducing energy consumption compared to traditional methods.
Additionally, the study analyzed helium, finding that although there are several disadvantages for energy consumption regarding gas atomization overall, helium boasts a notable decrease in specific energy consumption compared to argon (the second most efficient gas) and nitrogen. Brian R. Neff, Board Chair of AMGTA, spoke on these findings, stating:
A primary goal of the AMGTA is to educate the consumer on the most sustainable methods of production within the additive supply chain. This important piece of research provides guidance on which methods of gas atomization require the least amount of specific energy per kilogram. At the same time, it indicates to the market that mechanical production methods of powder feedstock, such as ball milling, are themselves an order of magnitude better than gas atomization from an energy perspective.”
Sherri Monroe, AMGTA Executive Director, highlighted the importance of the study, stating, “These findings highlight key considerations for manufacturers seeking environmentally friendly feedstock production methods. To advance sustainability in additive manufacturing, research is vital in order to make informed decisions.” To learn more about this study by AMGTA, click here.
What do you think about this study released by the AMGTA? Let us know in a comment below or on our LinkedIn, Facebook, and Twitter pages! Don’t forget to sign up for our free weekly newsletter here for the latest 3D printing news straight to your inbox! You can also find all our videos on our YouTube channel.