Cambridge Researchers 3D Print Smart Wall on UK National Highways
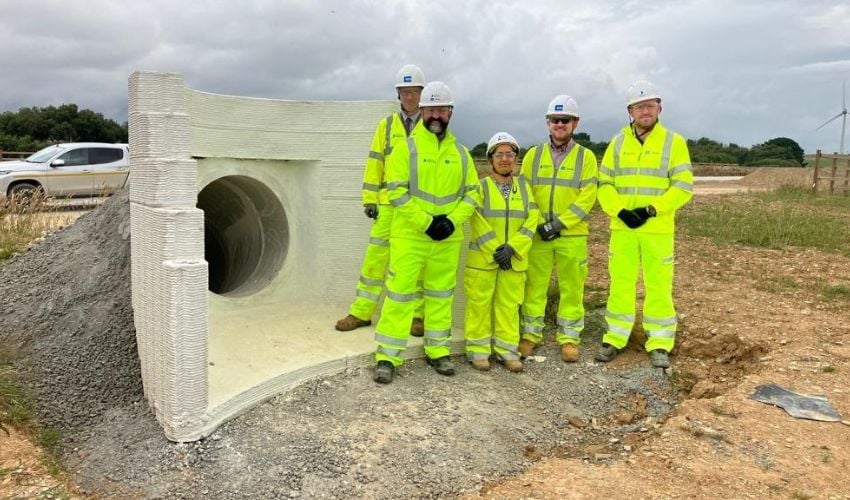
Cambridge researchers have achieved a significant milestone by developing the first 3D printed concrete infrastructure for a National Highways project. The innovative structure, known as a headwall, has been installed on the A30 in Cornwall and is equipped with sensors developed by Cambridge University. These sensors provide real-time information on temperature, strain, and pressure, enabling early detection of faults. By using 3D printing technology, the team was able to construct a curved hollow wall without the need for formwork or steel reinforcement, reducing costs, materials, and carbon emissions.
Over the past six years, Professor Abir Al-Tabbaa’s team at Cambridge’s Department of Engineering has been at the forefront of developing advanced sensor technologies and exploring the potential of self-healing concrete. Their expertise and collaboration with industry partners have resulted in the successful implementation of the 3D printed headwall on the A30. This pioneering project showcases the immense possibilities of additive manufacturing in the construction industry.
The wall, which measures approximately two meters in height and three and a half meters in width, was printed using a robot arm-based concrete printer at the headquarters of Versarien, an advanced engineering company in Gloucestershire. This cutting-edge printing method not only saved on costs and materials but also significantly reduced carbon emissions compared to traditional construction techniques. The curved hollow design of the wall, devoid of conventional formwork or steel reinforcement, derives its stability from its unique geometry.
To ensure the structural integrity and performance of the 3D printed wall, Cambridge researchers embedded a range of sensors within the concrete. These sensors monitor various parameters such as temperature, moisture, pressure, strain, electrical resistance, and electrochemical potential. By collecting real-time data, these sensors enable the early detection of any anomalies or potential issues, allowing for timely intervention and maintenance.
In addition to the sensor technology, the team employed LiDAR scanning during the printing process to create a detailed digital twin of the wall. This digital representation provides a comprehensive understanding of the structure’s behavior and facilitates better analysis and decision-making. The combination of advanced sensors and a digital twin enhances the wall’s ability to communicate its own status and aids in accelerating the acceptance and adoption of 3D printed structures in the construction industry.
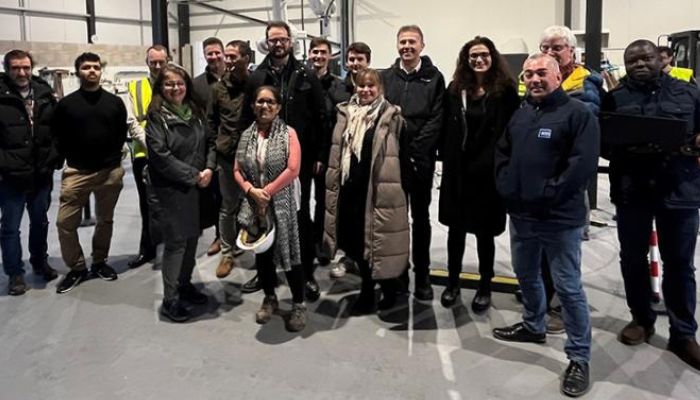
Members of the Cambridge team
Professor Abir Al-Tabbaa highlighted the significance of the project, stating, “Making the wall digital means it can speak for itself. And we can use our sensors to understand these 3D printed structures better and accelerate their acceptance in the industry.” The successful implementation of the 3D printed headwall on the A30 will serve as a living laboratory, continuously generating valuable data over its lifespan. This data will contribute to a deeper understanding of how 3D printing can be used to print larger and more complex cement-based materials for the strategic road network.
The project, part of the Resilient Materials for Life Program and the Digital Roads of the Future Initiative, is supported by the Engineering and Physical Sciences Research Council (EPSRC) and the European Union. With this groundbreaking achievement, Cambridge researchers have not only demonstrated the feasibility of 3D printed concrete infrastructure but also paved the way for further advancements in additive manufacturing within the construction industry. The successful integration of intelligent sensors and digital twins in 3D printed structures holds immense potential for enhancing the efficiency, durability, and sustainability of future infrastructure projects.
What do you think of the first ever 3D printed concrete infrastructure for a National Highways project? Let us know in a comment below or on our LinkedIn, Facebook, and Twitter pages! Don’t forget to sign up for our free weekly Newsletter here, the latest 3D printing news straight to your inbox! You can also find all our videos on our YouTube channel.
*All photo credits: University of Cambridge