Composite 3D Printing Unlocks Applications in Aerospace and Robotics in China
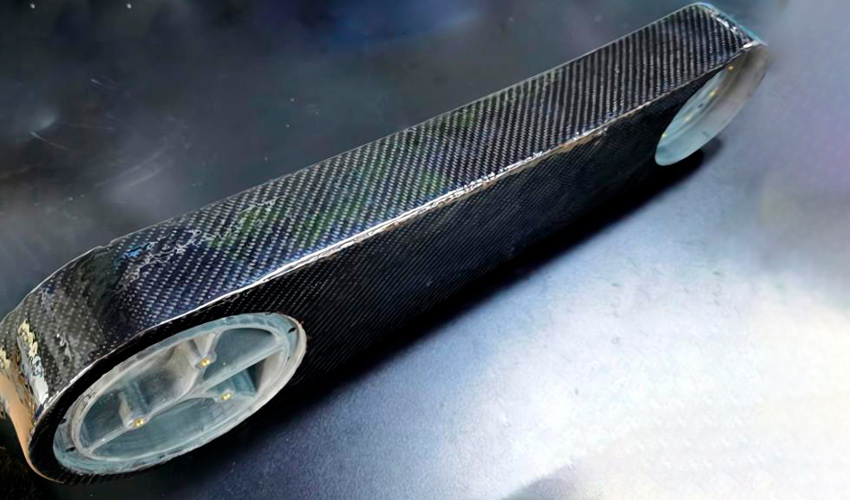
Though much focus has been put on 3D printing with polymers and metals in recent years, there is one material family that has shown immense growth in the additive manufacturing sphere: composites. As strong as metal and as light as many polymers, composites for FFF 3D printing often include a polymer matrix and infill such as glass fiber or carbon fiber. They have become so prevalent that the global composite 3D printing market is expected to reach $490.47 million by 2030, having already achieved a value of $198.31 million in 2023. And the importance of composites for 3D printing has also been recognized by the Institute of Industrial New Materials in Dezhou, China.
Founded in January 2021, the institute is dedicated to research, developing and commercializing composite materials for applications in sectors like maritime, 5G communication, advanced manufacturing processes and high-end equipment. A provincial “new-style R&D institution” in China, it has also seen the advantage of turning to 3D printing. In partnership with INTAMSYS, the institute is spearheading two initiatives to apply 3D printing in the development of composite product parts.
Replacing Traditional Material Molding
It is hardly new that 3D printing has been put forth as a replacement or even supplement to many traditional production processes. The reason for this is because with 3D printing, complex geometries are more easily achieved. Additionally, the design can be optimized even further to reduce costs and lead times.
In one case, the institute was tasked with developing intake manifolds for a specific aircraft engine. Intake manifolds are critical components within engine systems with a direct impact on overall engine performance as they supply fresh air to cylinders to ensure the proper mixture of air and fuel burned in an engine. However, development can be difficult due to their complex design as well as the difficulties related to making molds, high costs, and the time-consuming vibration welding process. This is where 3D printing came in.
The institute decided to make these intake manifolds using FFF 3D printing. More specifically, they turned the 610HT 3D printer and PEEK-CF from INTAMSYS. These were chosen for material performance, equipment capabilities and service support.
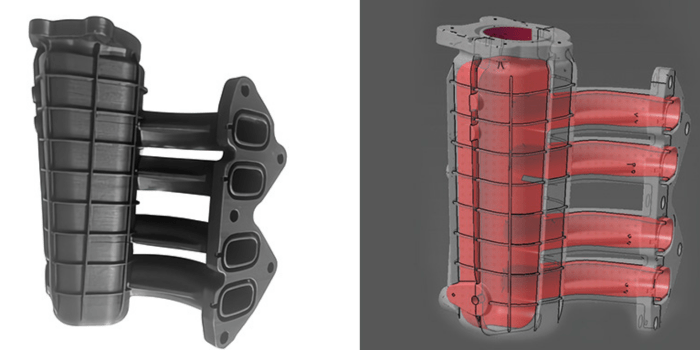
The finished (left) design manifold and the design of the part including the interior (right)
We have already previously told you about the FUNMAT PRO 610HT. The dual nozzle, large-format 3D printer has been designed to print high-temperature thermoplastic materials such as PEEK, ULTEM, and PPSU and can handle a wide range of materials including custom polymers. This is possible thanks to nozzles that can reach up to 500°C and a chamber that can be heated to 300°C. This enables the printing of high-performance materials without distortion.
Furthermore, experts from the institute and INTAMSYS used DfAM to optimize the design and printing processes to make the 218.4 × 216.4 × 95.4mm part. This resulted in a 30% weight reduction, with the thickness of the thinnest wall measuring only 1.7mm. The part dimensions were also able to be controlled for a precise fit and tests showed a mechanical strength of 100mPA, exceeding traditional injection-molded PA66-GF products by over 30% all while being able to withstand long-term temperatures of 114°C.
Considering that parts made with traditional injection molding processes (including tooling) would have cost around $27,803 with a 45-day lead time, the value of 3D printing became immediately obvious. The institute was able to manufacture the intake manifolds as a single integrated piece, thus reducing costs to 1/10 of ones made with traditional methods and shortening the production lead time to only 4–7 days.
Hybrid Manufacturing With Composite 3D Printing
Of course, composite 3D printing is not only useful as a way to replace traditional methods. It can also be integrated into existing processes. This was done by the institute in collaboration with a Chinese university to develop a robotic composite material manipulator arm.
For example, to make the manipulator arm, the FUNMAT PRO 610HT and PEEK-CF were used for internal support structure. The resulting component was not only a large size, but featured curved surfaces, high stiffness-to-weight ratio, and exceptional specific strength. This showcases the capability of composite 3D printing to create complex, high-performance parts.
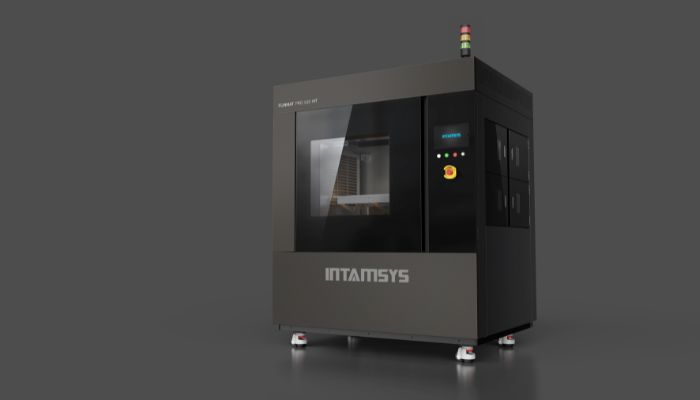
The FUNMAT PRO 610HT was used for both the intake manifolds and the robotic arm component
The university then used a pre-impregnated layup method to envelop carbon fiber around the 3D-printed structure. This enabled the affordable and swift creation of a lightweight, robust, composite manipulator arm. The best part? It was possible to circumvent costly mold tooling while still achieving a structural strength comparable to aluminum alloys. Furthermore, composite 3D printing could also be merged with other traditional techniques like traditional filament winding, automated layup and compression molding processes.
In any case, it is clear that the Institute of Industrial New Materials has shown the advantages of both replacing and supplementing traditional processes with composite 3D printing. Namely, through enhancing efficiency and reducing costs in the manufacturing of composite parts.
What do you think of the Institute of Industrial New Materials’ decision to turn to composite 3D printing? Let us know in a comment below or on our LinkedIn, Facebook, and Twitter pages! Don’t forget to sign up for our free weekly newsletter here, the latest 3D printing news straight to your inbox! You can also find all our videos on our YouTube channel.
*Cover: The robotic arm component, printed using composite 3D printing (photo credits: INTAMSYS)