Neue recyclingfähige 3D-Druck-Strukturen für die Weltraumforschung
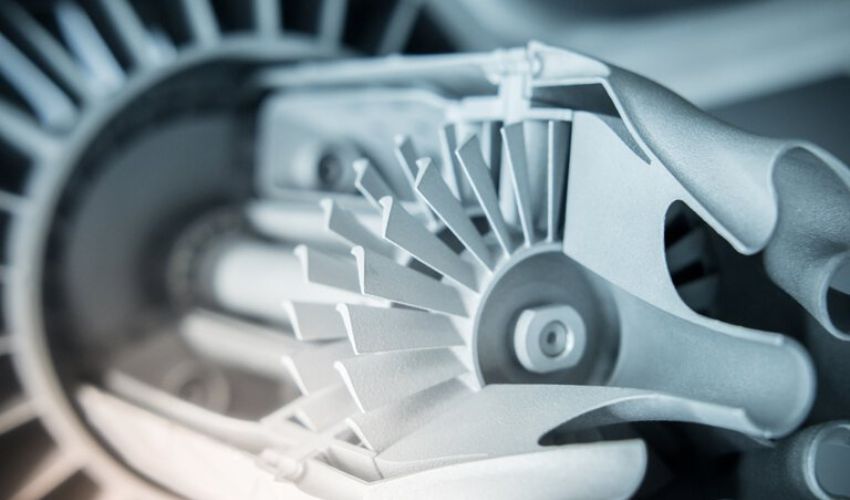
Die additive Fertigung hat sich in bereits zahlreichen Branchen etablieren können. Einer der womöglich wichtigsten Industrien, die maßgeblich von der Technologie profitieren ist die Luft- und Raumfahrtindustrie. Neben Raketen die im 3D-Druckverfahren hergestellt werden, wie die Terran 1 von Relativity Space beispielsweise, werden auch Satelliten und Antennen mithilfe der Technologie gefertigt. Der Markt für additive Fertigung in der privaten Raumfahrtindustrie soll bis 2026 einen Marktwert von 2,1 Milliarden US-Dollar erreichen. Gründe, weshalb Unternehmen auf den 3D-Druck in der Weltraumforschung zurück greifen sind vielseitig. Das Verfahren ermöglicht es unter anderem effizienter zu produzieren. Nun wurde ein Projekt ins Leben gerufen, welches recyclingfähige 3D-Druck-Strukturen für die Luftfahrt untersucht.
Das Projekt JoinTHIS wurde am Institut für Fertigungstechnik und Werkzeugmaschinen (IFW) der Leibniz Universität Hannover ins Leben gerufen. Hierbei wird ein Prozess entwickelt, welcher die additive Fertigung von recyclingfähigen, thermoplastischen Faserverbundwerkstoffen für die Luft- und Raumfahrt ermöglicht. Ein weiteres Ziel war es, den Prozess besonders nachhaltig zu gestalten. Aus diesem Grund arbeiteten das IFW in den letzten vier Jahren mit dem Institut für Polymerwerkstoffe und Kunststofftechnik (PuK) der TU Clausthal und dem Institut für Flugzeugbau und Leichtbau (IFL) der TU Braunschweig zusammen. Das Projekt wird von dem Europäischen Fond für Regionale Entwicklung und dem Land Niedersachsen gefördert.
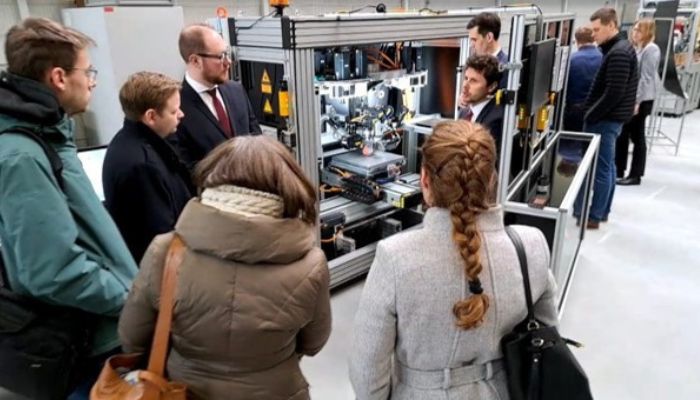
Das neue Verfahren wurde demonstriert (Bild: IFW)
Die innovative Automated Fiber Placement (AFP) Technologie, die von dem IFW entwickelt wurde, beinhaltet dünne thermoplastische Faserhalbzeuge, auch Tapes genannt. Diese werden Schicht für Schicht zusammengefügt, sodass die Struktur additiv erzeugt wird. Dadurch, dass es sich um eine in-situ – lat. für „am (Ursprungs-) Ort“ – Fertigung handelt, kann auf einen Autoklavprozess verzichtet werden. Autoklaven werden für gasdicht verschließbare Druckbehälter verwendet und sind sehr energieintensiv. Mit der Vermeidung dieses Prozesses wird das entwickelte Verfahren besonders energieeffizient gestaltet.
Das Fertigungssystem wurde getestet, indem Modelle der einzelnen Module aufgebaut und in einen digitalen Prozesszwilling überführt wurden. Zusätzlich wurden numerische und experimentelle Analysen verwendet, um ein besseres Verständnis der optischen, thermischen und mechanischen Wechselwirkungen während des Prozesses zu bekommen. Bei den verschiedenen Tests konnte die Basis für die in-situ Fertigung von zylindrischen Medienbehältern entwickelt werden. Diese dreidimensionalen Strukturen könnten in Zukunft für Mobilitätsanwendungen verwendet werden. Hierbei wird der Aspekt der Nachhaltigkeit ebenfalls in den Vordergrund gestellt, da gewährleistet wird, dass weniger CO2 ausgestoßen wird. Mehr über zum Projekt finden Sie HIER.
Was halten Sie von den 3D-Druck-Strukturen für die Luftfahrt? Lassen Sie uns gerne einen Kommentar da, oder teilen Sie es uns auf Facebook oder LinkedIN mit. Möchten Sie außerdem eine Zusammenfassung der wichtigsten Neuigkeiten im 3D-Druck und der additiven Fertigung direkt und bequem in Ihr Postfach erhalten? Dann registrieren Sie sich jetzt für unseren wöchentlichen Newsletter.
*Titelbildnachweis: EOS