Der 3D-Druck in der Windenergie
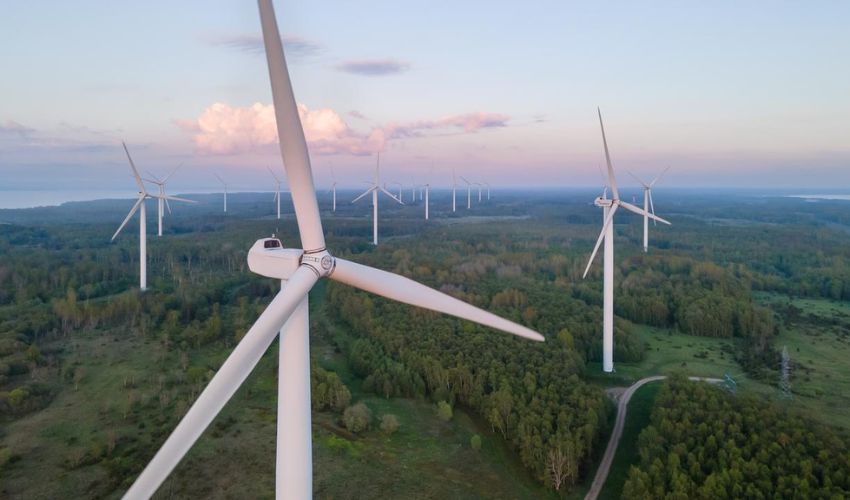
Der 3D-Druck findet in einer wachsenden Vielfalt an Branchen immer mehr Anwendungsfälle. Die Vorteile der innovativen Fertigungstechnologie in Produktionsprozessen werden von einer steigenden Anzahl an Unternehmen erkannt, woraufhin sie die Technologie in ihre Prozesse integrieren. Dies trifft auch auf die Energiebranche zu. Laut eines Marktberichts vom „Additive Manufacturing Research“ soll das Marktvolumen des 3D-Drucks in der Branche bis 2032 auf 17 Milliarden Euro ansteigen. Im Rahmen der Studie „Additive Manufacturing in the Energy Sector: market Analysis & Forecast” wurde eine Analyse der Einsatzmöglichkeiten und Potentiale additiver Fertigungstechnologien – unter anderem in erneuerbaren Energien wie der Windenergie – vorgenommen. Im Anschluss wurde insbesondere die Wichtigkeit, die der 3D-Druck in der Windenergie für die Entwicklung und Wartung wichtiger Anlagen und Ausrüstungen hat, sowie die Notwendigkeit, Maßnahmen zu ergreifen, um sein Potential auszuschöpfen, betont.
Die Vorteile, die der 3D-Druck im Bereich der erneuerbaren Energien und insbesondere in der Windenergie mit sich bringt, werden von Marktakteuren mittlerweile langsam aber sicher erkannt. So besteht mit der additiven Fertigung die Möglichkeit, die Kosten der Windturbinenherstellung zu senken sowie die Größe der Windkraftanlagen (WKA) durch den Druck vor Ort an die Bedürfnisse des jeweiligen Standortes anzupassen. Zudem stellt sich bei der herkömmlichen Fertigungsweise von Windturbinen die Herausforderung, dass die Flügel der WKA aus Glasfaser verstärktem Kunststoff produziert werden, welcher so gut wie gar nicht recycelt werden kann. Zudem werden die Flügel per Hand gefertigt, was ein großer Treiber für die hohen Kosten bei der traditionellen Herstellungsweise darstellt.
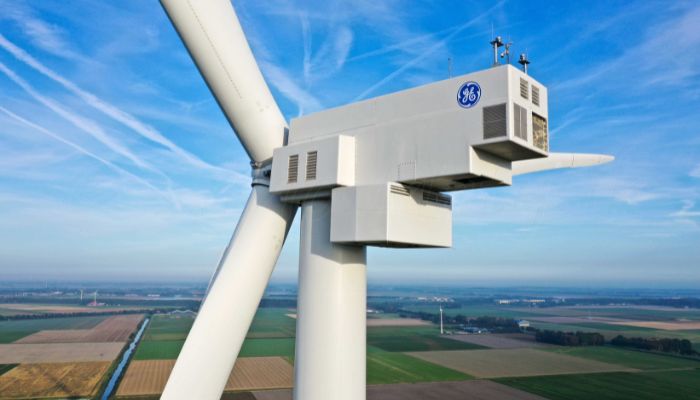
(Bild: GE General Electric)
Verwendete 3D-Druck-Verfahren, Drucker und Materialien
Eines der am häufigsten angewendeten Verfahren im 3D-Druck in der Windenergie ist wohl das Fused Deposition Modeling (FDM). Diese Methode, die in dem Aufeinanderschichten von geschmolzenem Kunststoff besteht, wird für die Herstellung von Prototypen und Teilen verwendet. Ein weiteres Verfahren stellt das Selective Laser Sintering (SLS) dar, bei dem ein Laser verwendet wird, um Materialien auf Pulverbasis – wie etwa Nylon – zu schmelzen, woraufhin sich die Struktur verfestigt. Die Vorteile der Methode bestehen insbesondere in dem Erhalt besonders stabiler Prototypen und Endprodukte sowie Komponenten für die Windenergie, und zwar besonders für kleinere Teile. Auch das Verfahren des Binder Jetting findet häufig im Bereich der Windenergie Anwendung, wie zum Beispiel im Rahmen des Advance Casting Cell (ACC)-Projekts für die Herstellung von Formen für den Metallguss von Windturbinen mit Hilfe des gleichnamigen 3D-Druckers.
Das Verfahren des Direct Metal Laser Sintering (DMLS) wurde ebenfalls bereits im 3D-Druck in der Windenergie angewendet, etwa für die Herstellung hochpräziser und komplexer metallischer Bauteile – ob für Prototypen, Endteile oder Reparaturen bestehender WKA. Die Siemens Gamesa Renewable Energy und Vestas nutzten die Technologie beispielsweise in der Vergangenheit für die Herstellung und Optimierung ihrer Turbinen. Für die Herstellung von Prototypen und Gehäusen in Windturbinen werden in der Windindustrie häufig Materialien wie Polyactid (PLA) und Acrylnitril-Butadien-Styrol (ABS) im FDM-3D-Druck verwendet. Auch Nylon, Polyamid, Metallpulver, Glas- und Kohlenstofffasern sowie Harze finden Anwendung im 3D-Druck in der Windindustrie.
Vorteile und Limits des 3D-Drucks in der Windenergie
Wie bereits erwähnt, eignet sich der 3D-Druck in der Windenergie insbesondere für die Herstellung von Prototypen. Dies rührt daher, dass der 3D-Druck eine kostengünstige und schnelle Produktion von Teilen ermöglicht, wodurch Innovationen in der Windenergie relativ schnell umgesetzt werden können. Mit dem 3D-Druck lassen sich außerdem komplexere Formen realisieren als bei herkömmlichen Methoden, wo diese schwieriger zu realisieren sind, sowie die Leistung von Rotorblättern verbessern, wie beispielsweise innerhalb eines Forschungsprojekts der TU Berlin. Im Rahmen des Projekts gelang es den Forschern zudem mit Hilfe des BigRep 3D-Druckers, eine ganze Windturbine am Stück zu drucken.
Außerdem lassen sich kundenspezifische Teile für WKA herstellen, sodass diese an die jeweiligen Standorte der WKA angepasst werden können. Zudem bietet der 3D-Druck in der Windenergie die Möglichkeit, WKA-Elemente vor Ort zu produzieren. Die additive Fertigung bietet außerdem eine erhöhte Flexibilität, Gussformen und damit Bauteile im und am Maschinenhaus immer neu anzupassen. Damit wird ermöglicht, den Guss mit Hilfe der 3D-gedruckten Formen nah an den jeweiligen Produktionsstandorten und die Fertigung näher an den Baufeldern von etwa Offshore-Windparks stattfinden zu lassen. Auf diese Weise lassen sich mit dem 3D-Druck in der Windenergie auch die Transportkosten für Gusskomponenten senken, was zur Folge hat, dass Gießereien für WKA-Bauteile einfacher mit neuen, kostengünstigeren und schnell gedruckten Gussformen versorgt werden könnten. Beispielsweise in den USA ist der Transport von Rotorblättern wegen der bestehenden Infrastruktur der Schienen und Straßen auf Rotorblattlängen zwischen 53 und 62 m beschränkt, weshalb der 3D-Druck – eventuell sogar in Kombination mit Robotik – mit seiner Möglichkeit der Fertigung vor Ort großes Potential aufweist, etwa für die Herstellung größerer und leistungsfähigerer Anlagen.
Angesichts langer Lieferzeiten bei herkömmlichen Produktionsweisen lassen sich durch den 3D-Druck in der Windenergie außerdem Ersatzteile schneller und nach Bedarf produzieren. Die Bestell- und Herstellungszeiten können demnach gesenkt werden. Somit entfällt auch die Notwendigkeit, Lagerbestände dauerhaft auf einem hohen Füllgradniveau halten zu müssen. Darüber hinaus eignet sich die innovative Technologie zur Erstellung leichter und komplexer Strukturen von Windturbinen, sodass das Gewicht dieser insgesamt reduziert werden kann.
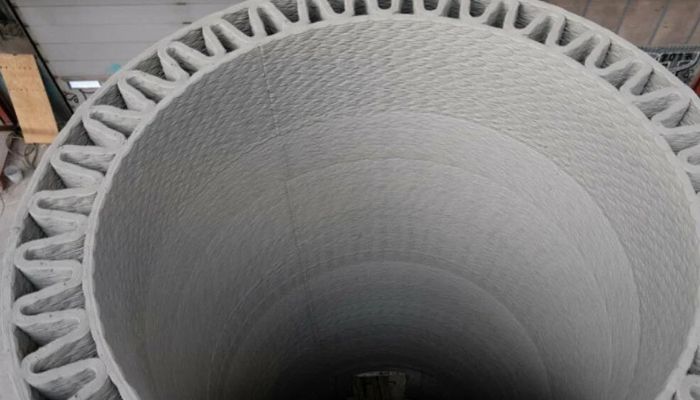
Der 3D-Druck bietet den Vorteil, Windräder direkt vor Ort produzieren zu können (Bild: en-former)
Zwar lassen sich mit Hilfe des 3D-Drucks bei der Produktion von Prototypen die Kosten senken, jedoch sind die Anschaffungskosten der 3D-Drucker und der für den Druck verwendeten Materialien sehr hoch, wodurch die Kosten bei Verwendung des 3D-Drucks für die Herstellung von WKA auch insgesamt sehr hoch ausfallen können. Zudem ist es häufig schwierig, unter Anwendung des 3D-Drucks die Anforderungen von Normen und Zertifizierungen zu erfüllen. Die Erfüllung dieser ist häufig mit Aufwänden verbunden, die bei traditionellen Produktionsweisen nicht aufkommen. Außerdem existieren derzeit noch Beschränkungen was die erreichbare Größe der mit 3D-Druck hergestellten Bauteile für Windturbinen anbelangt und Projekte wie das ACC sind aktuell noch eine der wenigen, die besonders große Drucke in der Herstellung von Windturbinenteilen ermöglichen. Weil zum 3D-Druck in der Windenergie bisher erst relativ wenige Erfahrungswerte gesammelt werden konnten, bleibt außerdem noch abzuwarten, ob 3D-gedruckte Teile von WKA zuverlässig und über die Zeit stabile Eigenschaften aufweisen.
Anwendung des 3D-Drucks in der Herstellung von Windkraftanlagen
Der 3D-Druck in der Windenergie kann für verschiedene Aspekte im Laufe des Produktionsprozesses von Windkraftanlagen angewendet werden. Insbesondere wird die additive Fertigung für die Produktion von Komponenten und Gussformen verwendet. Außerdem findet sie besonders häufig Anwendung in der Produktion von Prototypen für neue Komponenten der WKA, da diese mit Hilfe des 3D-Drucks zügig erstellt werden können, und sich somit für Tests und weitere Verbesserungen eignen, bevor sie für die Massenproduktion eingesetzt werden. Beispielsweise hat der US-amerikanische Konzern General Electric (GE) bereits 2019 mit dem 3D-Druck von Großkomponenten für Windenergieanlagen begonnen und 2021 eine 3D-Druckanlage in den USA eröffnet, an der 20 Mitarbeiter zu Forschungszwecken arbeiteten. Darüber hinaus nutzte das Unternehmen den 3D-Druck schon, um leichtere Turbinenblätter für seine GE9X-Triebwerke herzustellen. Außerdem hat es sich mit dem dänischen Unternehmen COBOD zusammengetan, das sich auf die Entwicklung von 3D-Drucktechnologien für den Bauwesenbereich spezialisiert hat, um 3D-gedruckte Windturbinentürme zu produzieren.
Ein weiteres Unternehmen, das im Rahmen eines Projekts den 3D-Druck in der Windenergie zur Herstellung von Windturbinen anwendet, ist das Cleantech-Startup Orbital Composites, welches Turbinen, Windflügel, Fundamente und Türme mit Hilfe der additiven Fertigung an der Einsatzstelle vor Ort in hohem Durchsatz und in großem Maßstab produziert. Mit dem Projekt erhofft sich Orbital Composites, den Einsatz seiner 3D-Druckroboter für die Herstellung von Windflügeln zu demonstrieren sowie zu validieren. Orbital Composites verfolgt darüber hinaus die Vision, eines Tages große Systeme zu bauen, mit denen sich Windflügel mit über 100 m Länge 3D-drucken lassen und Off-Shore Windkraftanlagen direkt auf dem Schiff auf dem Meer in 3D zu drucken. Dabei kollaboriert das Unternehmen mit der Forschungs- und Entwicklungseinrichtung Oak Ridge National Laboratory (ORNL) sowie mit der University of Maine, auf deren Forschung wir in einem anderen Abschnitt nochmal zu sprechen kommen. Orbital Composites erhielt bereits finanzielle Zuschüsse durch das Departnment of Energy (DOE) sowie durch das Office of Energy Efficiency and Renewable Energy (EERE) – in Höhe von vier Millionen US-Dollar. Außerdem forschen das ORNL und das Sandia National Laboratory an 3D-gedruckten Formen für Windturbinenblätter und an einem 36 m langen 3D-Drucker der UMaine.
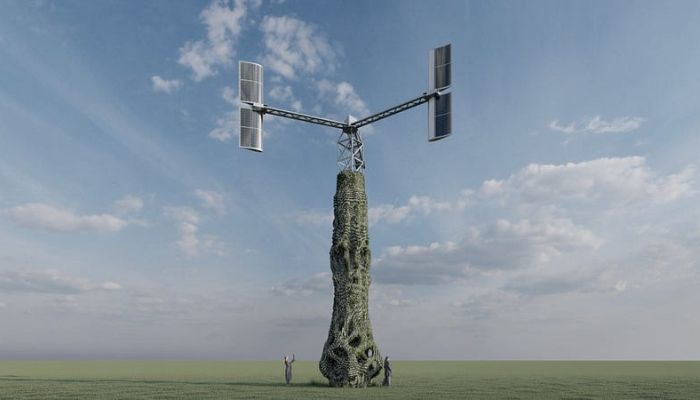
Bild: Soleolico
Auch das spanische Energieunternehmen Soleolico hat in der Vergangenheit den 3D-Druck für die Herstellung der weltweit ersten Windturbine mit Photovoltaik-Paneelen angewendet. Das Besondere an ihrer Anlage ist, dass sie in der Lage ist, sowohl Wind- als auch Sonnenenergie zu erzeugen und CO2 zu absorbieren. Für diese neue Entwicklung, für die das Unternehmen ein 3D-Druckverfahren von Pure Tech angewendet hat, benötigte Soleolico bis Oktober 2023 10 Jahre.
Forschung im Bereich 3D-Druck in der Windenergie
An mehreren Universitäten weltweit forschen Wissenschaftler im Bereich 3D-Druck in der Windenergie, wie etwa an der TU Berlin. Im Rahmen der „3D Printing Powers Wind Turbine Research“ untersucht das Team rund um Immanuel Dorn, Technik-Instrukteur, und Sascha Krumbein, Masterstudent in Ingenieurwissenschaften und ebenfalls Instrukteur des Projekts, wie sich Rotorblätter mit Hilfe des 3D-Drucks optimieren lassen. Zu ihren Untersuchungen gehört auch die Erprobung der verschiedenen Rotorblätter in ihrem großen Windkanal, wo sie die Leistungsperformance der Rotoren, die mit verschiedenen Materialien im 3D-Druck viele Produktionsiterationen durchlaufen, beobachten. Innerhalb ihres Projekts lassen sich mit dem 3D-Durck komplexere Formen realisieren und die Leistung verbessern. Bei ihrer Forschung hat das Team zunächst mit dem aerodynamischen Design begonnen, bevor es zum strukturellen Design – verwendetes Infill sowie Materialien – übergegangen ist. Dafür benötigte es einige Iterationsprozesse, um das Material immer wieder auszutauschen und anzupassen. Zu guter Letzt führte das Forscherteam „real life“ aerodynamische Tests in ihrem Wind Tunnel durch, die unter anderem crash-tests beinhalteten.
Zudem forscht insbesondere in den USA eine Vielfalt an Universitäten zum 3D-Druck in der Windenergie, wie etwa die Purdue University in Indiana, welche zusammen mit RCAM Technologies und der Floating Wind Technology Company kostengünstigere Anker und Turbinenkonstruktionen auf Betonbasis entwickelt und ein Projekt zum Thema additive Fertigung von Werkzeugen für Windkraftrotorblätter durchführt. Dies realisiert sie zusammen mit unterschiedlichen Unternehmen und finanzieller Unterstützung seitens des US-Energieministeriums (Department of Energy, DOE) in Höhe von 2,8 Millionen US-Dollar. Ziel ist es dabei, durch 3D-Druck die Herstellung der Werkzeuge zu beschleunigen und die Kosten des fertigen Produkts zu senken. Darüber hinaus forscht die University of Maine zusammen mit dem National Renewable Energy Laboratory (NREL) an der Entwicklung von Methoden zur Verbesserung der Rotorblätter und der Formen von Windkraftanlagen. Sie arbeiten sogar an der Entwicklung des größten 3D-Druckers der Welt, um aus vergleichsweise günstigen Biopolymer Formen Rotorblätter von Windkraftanlagen in Originalgröße am Stück zu drucken. Darüber hinaus untersuchen Ingenieure der Universitäten McGill und Ryerson in Kanada, wie sie Abfälle von Rotorblättern von Windkraftanlagen in neues 3D-druckbares Material umwandeln können.
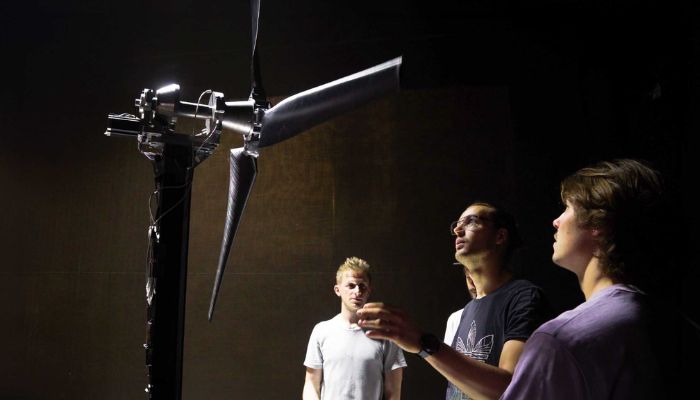
Das Team der TU Berlin untersucht im Rahmen des Projekts „3D Printing Powers Wind Turbine Research“, wie sich Rotorblätter mit Hilfe des 3D-Drucks optimieren lassen (Bild: BigRep)
Förderungen im 3D-Druck in der Windindustrie
Im Bereich 3D-Druck in der Windenergie hat es bereits mehrere Förderungen von 3D-Druck-Projekten gegeben, wie etwa seitens des Bundesministeriums für Wirtschaft und Energie (BMWi) für das Verbundvorhaben „Advance Casting Cell (ACC)“, welches auch der Name des dabei verwendeten Großformat-3D-Druckers ist, mit dem Sandformen gefertigt werden. Das Fraunhofer-Institut für Gießerei-, Composite- und Verarbeitungstechnik (IGCV) ist ebenfalls an dem Projekt beteiligt – als Verbundpartner sowohl für gieß- und werkstofftechnische Fragen als auch für die digitale Prozessüberwachung – sowie das 3D-Druckunternehmen Voxeljet aus Bayern. Für das Jahr 2022 hatte der Hersteller von Windkraftanlagen an Land GE Renewable Energy angekündigt, die 3D-gedruckten Gussformen für den Metallguss verschiedenster Schlüsselkomponenten des vollständigen Maschinenhauses der Offshore-Windenergieanlage Haliade-X von GE zu testen. Mit Hilfe des verwendeten 3D-Druckers ließen sich Gussformen für bis zu 60 Tonnen schwere metallgegossene Turbinenteile mit bis zu 9,5 m Durchmesser produzieren. Ziel des Projektes ist es, die Produktionszeit von Gussformen für Offshore-Windturbinen von mindestens zehn auf zwei Wochen zu reduzieren sowie Transportkosten zu verringern durch die Herstellung der Gussformen vor Ort, was auch eine Senkung der CO2-Bilanz in der WKA-Produktion zur Folge hat.
Eine weitere interessante Förderung im Bereich des 3D-Drucks in der Windenergie ist die des Verbunds des Instituts für angewandte Forschung Berlin (IFAF), welches bereits das Projekt Winddruck – mit Laufzeit bis September 2024 – unterstützt, dessen Ziel es ist, die Flügel von Windkraftanlagen mittels 3D-Druck auch im großen Maßstab wirtschaftlich und nachhaltig produzierbar zu machen. Zudem wird innerhalb des Projekts erforscht, wie Flügel zukünftig aus recycelbaren nachwachsenden Materialien im 3D-Druck gefertigt werden könnten, sodass die Flügel der WKA direkt am Aufstellungsort der WKA maßgeschneidert gedruckt werden könnten. Darüber hinaus fördert die Metropolregion Nordwest ein Forschungsprojekt der Constructor Universität in Bremen-Nord vom Mai 2023 zu Windkraftanlagen aus dem 3D-Drucker. Im Rahmen des Projekts mit dem Namen “Wind.EnergieAutarke Schulen in der Metropolregion Nordwest” verfolgten die Wissenschaftler in Zusammenarbeit mit dem Landkreis Friesland das Ziel, vertikale 3D-gedruckte Windkraftanlagen zu entwickeln und zu erproben.
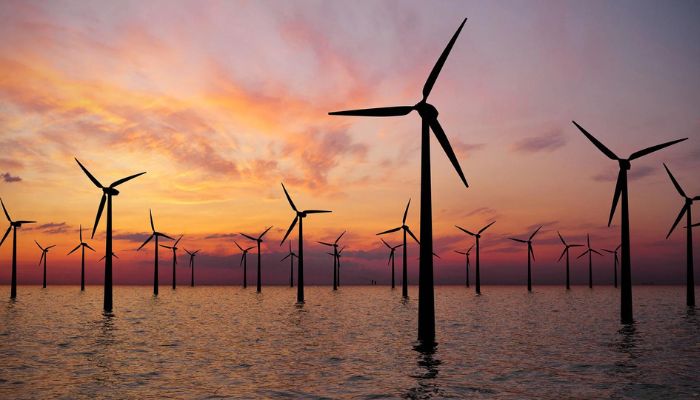
Bild: Shutterstock
Der Einsatz von 3D-Druck in der Windenergie gewinnt zunehmend an Bedeutung und zeigt großes Potential für Innovationen und Effizienzsteigerungen. Unternehmen und Forschungseinrichtungen weltweit erkennen die Vorteile dieser Technologie und investieren in die Entwicklung und Anwendung von additiven Fertigungsmethoden. Die vielfältigen Anwendungen des 3D-Drucks erstrecken sich von der Produktion von Prototypen und Komponenten bis hin zur Herstellung ganzer Windturbinen und ermöglichen eine Flexibilität und Anpassungsfähigkeit, die herkömmliche Fertigungsmethoden nicht bieten können. Während noch Herausforderungen wie die Erfüllung von Normen und Zertifizierungen sowie die Skalierung von Produktionsprozessen zu bewältigen sind, ist der Weg für den 3D-Druck in der Windenergie geebnet, um die Branche nachhaltig zu transformieren und den Zugang zu sauberer Energie weiter zu verbessern.
Was halten Sie von dem 3D-Druck in der Windenergie? Stufen Sie ihn als eine vielversprechende Herstellungsmethode in diesem Bereich ein? Lassen Sie uns dazu einen Kommentar da, oder teilen Sie es uns auf Facebook oder LinkedIN mit. Möchten Sie außerdem eine Zusammenfassung der wichtigsten Neuigkeiten im 3D-Druck und der additiven Fertigung direkt und bequem in Ihr Postfach erhalten? Dann registrieren Sie sich jetzt für unseren wöchentlichen Newsletter.
*Titelbildnachweis: Photocase