Caltech Progresses Research Into Nanoscale 3D Printed Metals
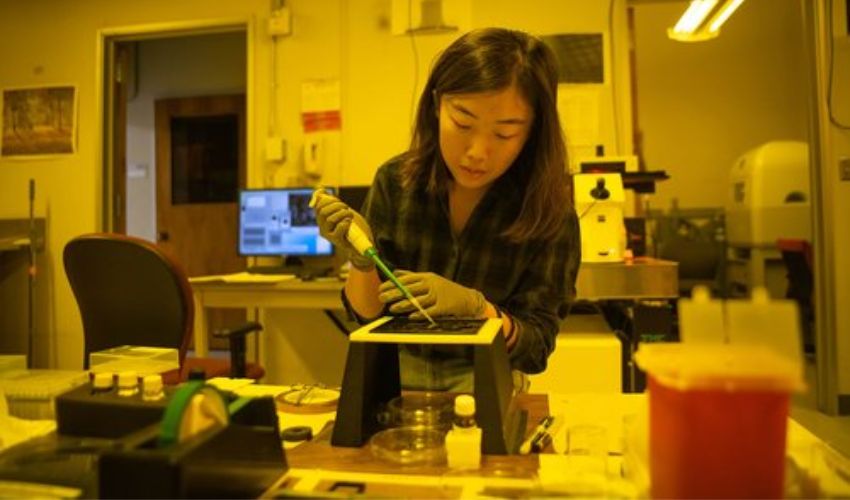
When it comes to 3D printing even the largest structures, understanding the smallest details or imperfections can prove the difference between success and failure. In order to better understand how 3D printed objects perform in the nanoscale, researchers from the California Institute of Technology (Caltech) have recently made a new discovery that has led to a new technique for 3D printing metals that are much stronger than similarly sized parts, which can be invisible to the naked eye.
The research was carried out by the lab of Julia R. Greer, Professor of Materials Science, Mechanics and Medical Engineering and director of the Kavli Nanoscience Institute. Building upon previous experiments in 2022, Greer’s lab developed a fabrication process technique for printing micro-sized metal objects that could be as thick as just a few pieces of paper. This year, the team has taken the size from the micro-scale to the nano-scale.

The nanoscale 3D printed lattice structure.
The shift takes the 3D printed parts and shrinks them down into a scale a thousandth the size of their previous experiments. The result revealed something somewhat unexpected: The smaller the print, the more disorderly the materials appeared on the atomic scale. In a normal-sized construction, that disorder would constitute a low-quality construction, prone to breakage and other weaknesses. However, in the nanoscale, the disorderly arrangement of these materials resulted in a part that was three to five times stronger than a construction with more ‘orderly’ arranged atoms.
Creating a More Stable Object Thanks to Nanoscale ‘Defects’
The intricate process involves a mixture of hydrogel, a polymer that can absorb a great amount of water, which is then shaped with a laser which causes the photosensitive material to harden into the desired shapes. After this hardening process, metal ions of nickel are introduced again, through a liquid solution. The metal is then absorbed by the formed hydrogel shape until exposed to heat, which burns away the hydrogel, leaving only the metal behind. In the final step, any oxygen is removed or converted from within the metal structure through a chemical stripping process which leaves behind a series of irregularities in the metal structure. Surprisingly, however, these contribute to the added strength of the object rather than take away from it.
“There are all these thermal and kinetic processes occurring simultaneously during this process, and they lead to a very, very messy microstructure,” says Professor Greer, “You see defects like pores and irregularities in the atomic structure, which are typically considered to be strength-deteriorating defects. If you were to build something out of steel, say, an engine block, you would not want to see this type of microstructure because it would significantly weaken the material.” However, these irregularities such as pores, which are so unwanted in larger sizes, form a sort of reinforcing boundary in the nanoscale. This boundary allows the material to move rather than break and gives it more support due to the even distribution of these deformations around the object.
“Usually, the deformation carrier in metal nanopillars—that is, a dislocation or slip—propagates until it can escape at the outer surface,” continues lead research author and mechanical engineering student Wenxin Zhang, “But in the presence of interior pores, the propagation will quickly terminate at the surface of a pore instead of continuing all the way through the entire pillar. As a rule of thumb, it’s harder to nucleate a deformation carrier than to let it propagate, explaining why the present pillars may be stronger than their counterparts.”
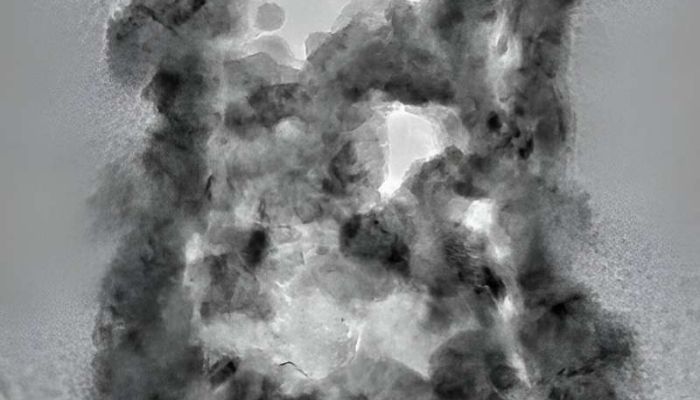
Evenly distributed, these defects allow the nanoscale 3D printed object to be less brittle and withstand more.
The end result provides a fascinating look at nanoscale structures that are effectively invisible to the naked eye. Professor Greer and her team are hopeful that this could lead to a multitude of uses where the increased durability of 3D printed metal in nanoscale can open up new avenues of study and innovation. For further information on their research, look HERE.
What do you think of Caltech’s research into nanoscale 3D printed metal? Let us know in a comment below or on our LinkedIn, Facebook, and Twitter pages! Don’t forget to sign up for our free weekly Newsletter here, the latest 3D printing news straight to your inbox! You can also find all our videos on our YouTube channel.
*All Photo Credits: Caltech