3D Printing Could Reduce Waste and Emissions When Retreading Tires
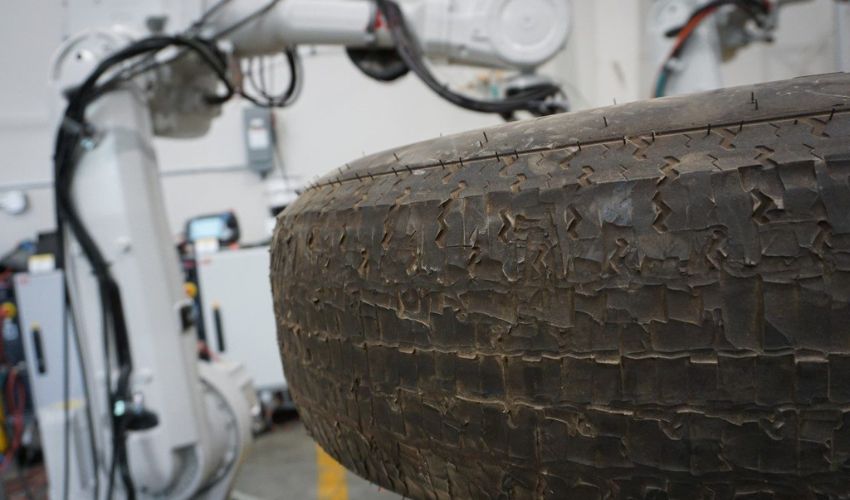
A team from Virginia Tech has been selected by the REMADE institute for a $1.5 million project to improve tire retreading using additive manufacturing. Tire retreading is a common part of commercial vehicle maintenance. Essentially, when a tire is worn out, its surface must be buffed away before a new layer of tire is adhered to it. The action is critical for the safety of tires, but the process itself is relatively inefficient. To address this, the team is turning to 3D printing and 3D scanning to improve efficiency, thereby reducing waste and emissions.
In the United States, the shipping industry in the country is almost entirely dependent on commercial vehicles notably tractor trailers, also known as semi-trailer trucks. Indeed, according to the Bureau of Transportation, there are 13 million trucks operating in the US including 2.9 million tractor trailers. Furthermore, nearly 70% of all freight in the US is transported by trucks making it one of the country’s biggest industries. As a result, about 14.5 million tires are retreaded each year in the US according to a press release from Virginia Tech. Subsequently, the waste, an estimated 9 pounds of excess material per tire, and inefficiencies really add up over time. That is why Chris Williams, the L.S. Randolph Professor in Mechanical Engineering as well as the REMADE institute believe it is so important to seek enhancement in the efficiencies of tire retreading. Including through the use of 3D printing.
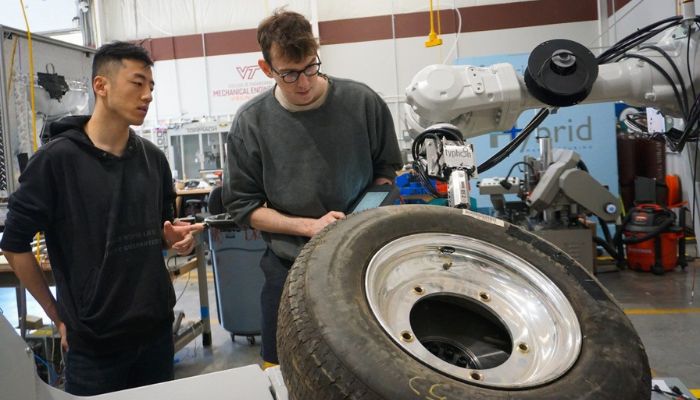
Graduate students Yigun Fu and Tadek Kosmal monitoring the 3D printing process
But how exactly will these technologies be used for tire retreading? Well according to information from Virginia Tech, the team’s approach will be to use 3D scanning, 3D printing and industrial robotics to create a new process for retreading. The combination of these different technologies and material science is critical in fact for the success of the project. Williams explains, “The only way to address this project’s grand challenge of reimagining the tire retreading process is through a team-based transdisciplinary approach focused in simultaneous considerations of materials, the additive manufacturing process, and the final tires’ performance.”
In terms of 3D printing, the chosen method seems to be a new method of extrusion using attachments on a robotic arm. This will in tern be combined with high-performance 3D printing elastomers that will be synthesized through a collaboration with Arizona State’s Biodesign Center for Sustainable Macromolecular Material and Manufacturing. Finally, with the flexibility of the robotic arms, it will be possible to 3D print directly on the necessary areas on the worn tire using extrusion, similar in idea to Directed Energy Deposition (DED) though with polymers. This will enable the creation of durable tires that are able to meet even the strictest safety requirements.
Williams concludes, “We are really excited to undertake this challenging project, which integrates advances in polymer science and manufacturing including 3D scanning, 3D printing, and industrial robotics. If all goes well, the resulting retreading technology could result in annual reductions of about 90 metric kilotons of tire waste and 800 metric kilotons of CO2 [carbon dioxide] emissions across the retreading industry.” You can find out more about the project on Viriginia Tech’s website HERE.
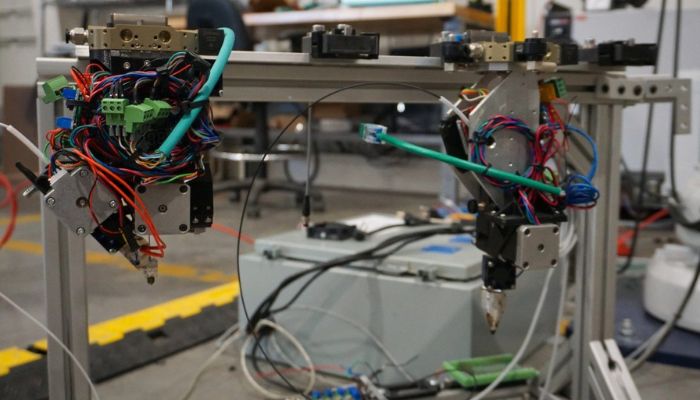
Different attachments for the robotic arm which is used to print polymer materials directly onto worn tires
What do you think of the choice to use 3D printing to improve tire retreading? Let us know in a comment below or on our LinkedIn, Facebook, and Twitter pages! Don’t forget to sign up for our free weekly Newsletter here, the latest 3D printing news straight to your inbox! You can also find all our videos on our YouTube channel.