The Complete Guide to Directed Energy Deposition (DED) in 3D Printing
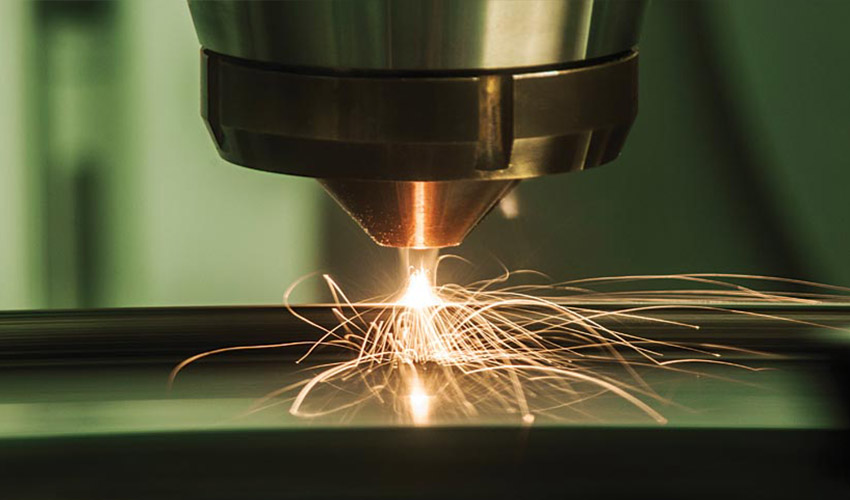
Directed Energy Deposition (DED) is a more complex 3D printing process, typically used to repair or add additional material to existing components. It is completely possible to fabricate parts from scratch using this technology, but it is often used for industrial applications such as repairing turbine blades or propellers that have been damaged.
Similarly to some Powder Bed Fusion (PBF) technologies (such as LPBF or EBM), Directed Energy Deposition uses a focused energy source, such as a laser or electron beam to melt the material. However, the material is melted at the same time as it’s deposited by a nozzle. In a way, the technology is at the frontier of material extrusion and powder bed fusion.
You should note that this technology is often referred to by other names such as Laser Engineered Net Shaping (LENS), Direct Metal Deposition (DMD), Electron Beam Additive Manufacturing (EBAM), etc. depending on the specific application or method.
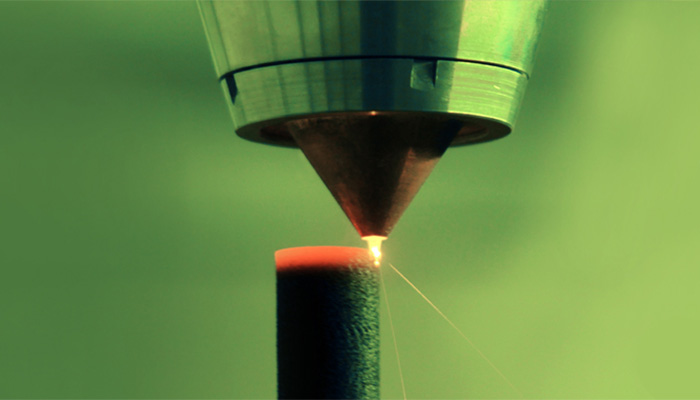
Image via BeAM
How does Directed Energy Deposition technology work?
As with any 3D printing technique, the design of a part begins with the creation of the 3D model using CAD software. The part is then cut into a multitude of layers by slicer software, representing the various layers of material needed to form the piece.
The technique works by depositing material onto a base or component that is being repaired through a nozzle mounted on a multi (usually 4 or 5) axis arm. The metal material that is fed to the nozzle is either provided in powder or wire form. As it is being deposited, a heat source melts the material simultaneously, usually using a laser, electron beam or plasma arc. This procedure is done repeatedly, until the layers have solidified and created or repaired an object.
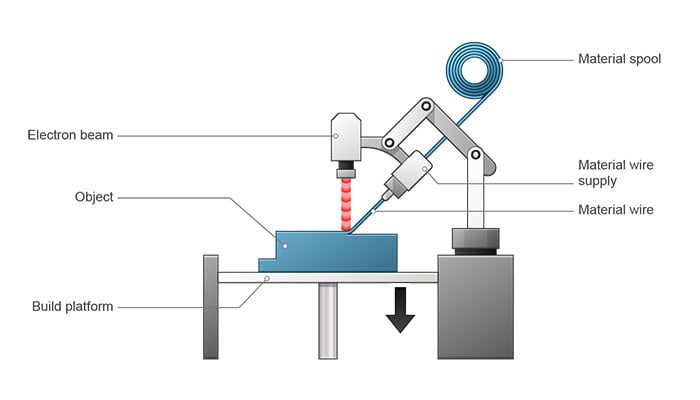
The DED additive manufacturing process, in this case using an electron beam | Figure from Dassault Systèmes
In the case of electron beam-based systems, the process must be performed in a vacuum to prevent the electrons interacting with or being deflected by air molecules. Laser-based systems require a fully inert chamber if working with reactive metals, requiring a significant amount of gas and time to achieve the desired oxygen levels. Alternatively, it is possible to use a shroud of shielding gas, which is sufficient to protect the metal being deposited from contamination.
Materials and Applications
It is true that this process is typically used with metals, in the form of either powder or a wire. However, it is possible to use DED with polymers and ceramics too. For example, AREVO uses Polymer DED with a filament of carbon fiber to fabricate lightweight composite parts for end use applications. The thermoplastic filament is melted by a heat source and compacted by a roller to generate the layers of the object.
For metals, almost any metal that is weldable can be 3D printed with DED. That includes titanium and titanium alloys, inconel, tantalum, tungsten, niobium, stainless steel, aluminium, etc. The wire used typically ranges from 1-3 mm in diameter and powder particle sizes are similar to those used in powder metallurgy processes, between 50 and 150 microns.
As previously mentioned, one of the unique applications of this technology is that it is possible to repair metal parts that have been damaged. According to ASTM International: “DED has the ability to produce relatively large parts (build volume > 1000 mm³) requiring minimal tooling and relatively little secondary processing. In addition, DED processes can be used to produce components with composition gradients, or hybrid structures consisting of multiple materials having different compositions and structures.”
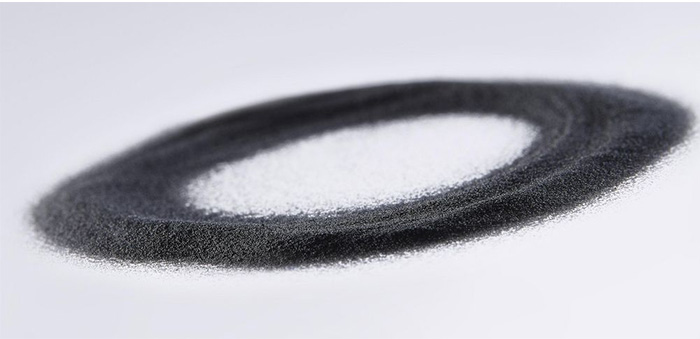
Metal powder | Image via Trumpf
Main Market Players
Today, the market counts quite a few manufacturers of DED 3D printers. BeAM is one of the main players in this field, they offer three solutions the Magic 80, and the Modulo 250 and 450, all using lasers as a heat source. Other manufacturers that create laser DED machines include Trumpf, Optomec, FormAlloy, DMG Mori, InssTek, Relativity, etc.
In terms of electron-beam DED systems, EBAM is a technology commercialised by Sciaky Inc., they offer as many as 5 different machines and also the possibility to create your custom system. Another manufacturer is Evobeam GmbH. Finally, plasma arc DED 3D printers manufacturers include Norsk Titanium, WAAM, GEFERTEC, Prodways and Lincoln Electric.
Was this guide on Directed Energy Deposition helpful? Let us know in a comment below or on our Facebook and Twitter pages! Sign up for our free weekly Newsletter, all the latest news in 3D printing straight to your inbox!
I am interested in purchasing a DED 3d printer. Would you provide the printer head separtely?