Bimota usa la stampa 3D per produrre le sue motociclette
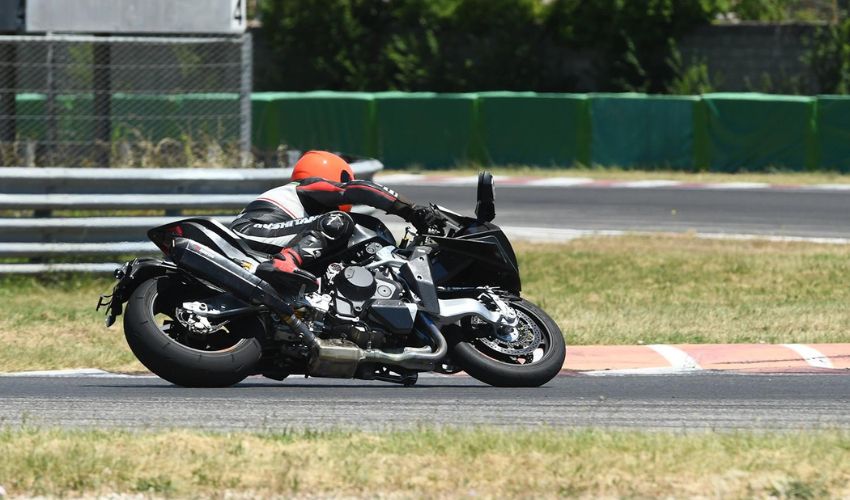
L’utilizzo della produzione additiva nel settore automotive continua a produrre applicazioni entusiasmanti. Abbiamo più volte raccontato dell’utilizzo della stampa 3D per la produzione di auto o moto da corsa, come nel caso di Tesla o Audi per le auto o Yamaha e Ducati per le moto. Oggi abbiamo un altro caso studio che arriva dall’Italia. La storica casa motociclistica riminese Bimota ha infatti adottato negli ultimi anni la stampa 3D per la produzione delle sue motociclette. A detta del team, l’azienda non tornerà più indietro per le enormi possibilità offerte dall’additive manufacturing in termini di flessibilità, velocità di processo e risparmio sui costi di produzione.
Ottimizzare tempi e risorse grazie alla stampa 3D
La storica casa motociclistica Bimota è stata fondata a Rimini nel 1973. Nel corso degli anni l’azienda ha vissuto diversi cambiamenti ed evoluzioni, fino alla rinascita grazie all’acquisizione da parte di Kawasaki Heavy Industries a partire dal 2019 e completata nel 2023. Questo ha permesso all’azienda italiana di continuare la produzione di motociclette di alta gamma, contando in più sulla fornitura di tecnologia e motori di Kawasaki e sulla rete di vendita del partner giapponese.
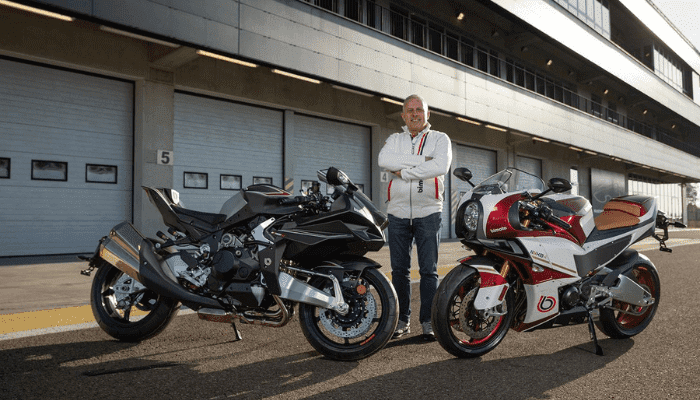
Pierluigi Marconi, Direttore Tecnico Bimota con le moto Tesi H2 e KB4.
L’approccio alla stampa 3D per l’azienda è arrivato durante la progettazione della Tesi H2, una motocicletta con carrozzeria in carbonio, motore super performante con prestazioni elevate fino a 230 cavalli. Le difficoltà sono arrivate nel periodo della pandemia Covid-19 che ha costretto l’azienda a valutare nuove possibilità di sviluppo e produzione dei prodotti, anche a distanza. È stato a questo punto che il team di Bimota ha deciso di utilizzare la stampa 3D per la prototipazione rapida. Bimota ha così iniziato a progettare completamente in 3D i modelli di ogni parte della motocicletta, il che è risultato indubbiamente vantaggioso per la possibilità di eseguire test virtuali e valutare così, anche digitalmente, la correttezza del progetto. Il passo successivo è stato la stampa 3D dei prototipi tramite un service 3D, in questo caso la scelta è ricaduta su Prosilas, per verificare con mano la funzionalità delle parti.
“In passato era necessario realizzare manualmente dei prototipi in Clay, dai quali costruire stampi rapidi per vetroresina. Un processo costoso e laborioso, i cui risultati non sempre erano precisissimi. Ora invece, disponendo dei file 3D, abbiamo la possibilità di farli stampare tramite prototipazione rapida in appositi service” – ha commentato Pierluigi Marconi, Direttore tecnico di Bimota.
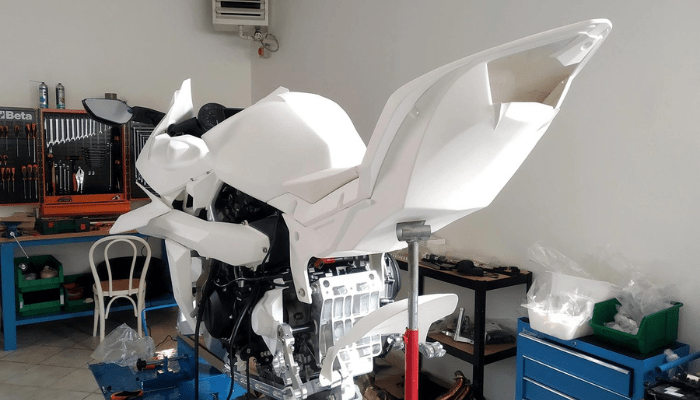
Prototipo stampato in 3D della Bimota Tesi H2
Dal prototipo ai test su pista
I risultati non hanno tardato ad arrivare poiché la stampa 3D ha permesso di accedere ai primi prototipi in soli 4 mesi, mentre prima ne erano necessari almeno 12. Prima di realizzare il prototipo perfetto, il team di Bimota controlla se le geometrie e le modifiche sono corrette o se è necessario intervenire ancora. In genere, dopo poche iterazioni si ottiene un risultato finale e ottimale, risparmiando tempi e costi rispetto ai metodi tradizionali. Lo sviluppo del prodotto è stato quindi molto velocizzato e ottimizzato. In precedenza, se il pezzo risultava inadatto, ad esempio, dover modificare completamente uno stampo risultava molto costoso e richiedeva tempistiche molto più lunghe.
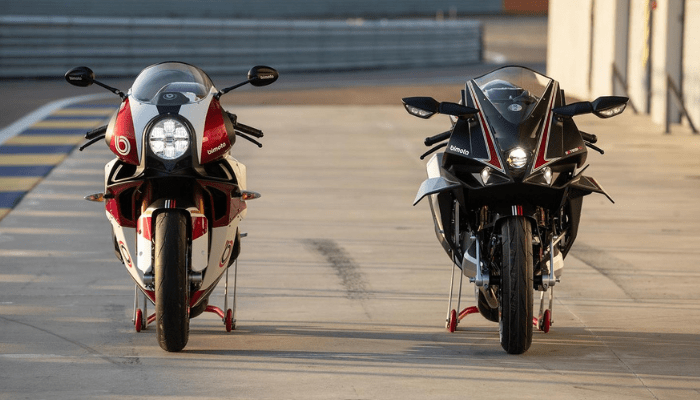
Le Bimota Tesi H2 e KB4.
I prototipi validati vengono quindi finalmente testati in pista e sottoposti a varie prove. “L’uso di Nylon caricato con fibra di vetro (PA12 GF) è ideale in termini di resistenza meccanica e alle alte temperature. Alcune parti sono infatti molto vicine all’impianto di scarico o ai radiatori e devono resistere a lungo, per offrirci i dati utili per comprendere se siamo sulla giusta strada. Inoltre è un materiale che non si deforma, caratteristica molto utile quando viene usato per l’accoppiamento di parti di carrozzeria” – ha spiegato Pierluigi Marconi.
La Tesi H2 non è stata che la prima di una lunga serie di motociclette Bimota realizzate con la stampa 3D. Nella KB4, l’additive manufacturing ha permesso ad esempio di realizzare un complesso sistema canalizzatore per l’aria. Mentre TERA, l’ultima creazione di Bimota, vedrà l’uso della stampa 3D per l’aggiunta di ulteriori appendici aerodinamiche. Siamo curiosi di scoprire quale sarà la prossima!
Che ne pensi dell’uso della stampa 3D di Bimota? Condividi la tua opinione e seguici sui nostri social Facebook e sul nostro gruppo italiano LinkedIn. Non dimenticare di iscriverti alla nostra Newsletter settimanale per ricevere tutte le notizie sulla stampa 3D direttamente nella casella di posta!
Crediti per tutte le foto: Prosilas/Bimota