La success story Weerg – Ursus : le guidon personnalisé réalisé avec la fabrication additive
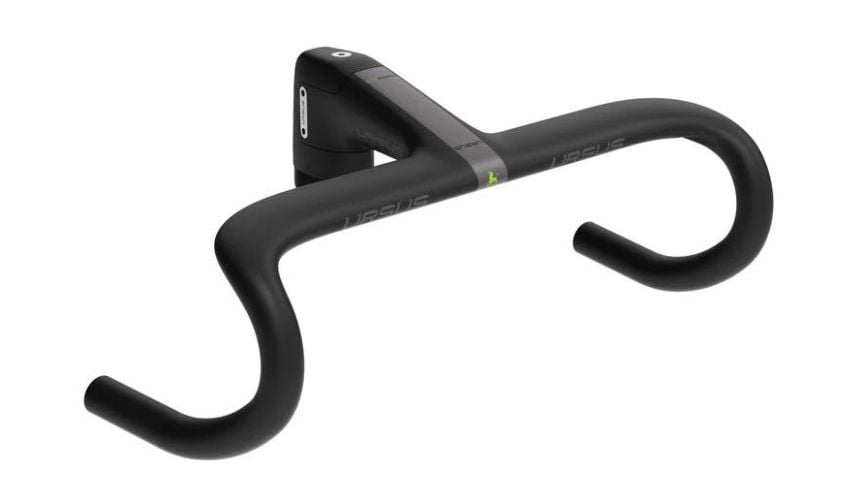
L’impression 3D rencontre de plus en plus de succès dans tous les secteurs où personnalisation, design et performance se rencontrent. La possibilité de créer des structures ad hoc, d’utiliser l’impression 3D pour un prototypage rapide et donc de tester des matériaux et des propriétés rapidement et à moindre coût, rend ces technologies adéquates, par exemple pour des secteurs tels que l’automobile, l’aérospatiale ou le sport. Le secteur du cyclisme, notamment, bénéficie de la fabrication additive pour la création de composants, de prototypes, mais aussi de pièces finies qui s’adaptent aux besoins des clients ou encore pour du sur-mesure ajusté au corps des athlètes. Le cas de la société Ursus, qui s’est tournée vers le service en ligne d’impression 3D Weerg pour créer un guidon sur-mesure, en est un bon exemple.
En effet, les entreprises qui ont besoin de produire des pièces de petites et moyennes dimensions, avec un design sur-mesure et en petites séries, rencontrent de nombreuses difficultés lorsqu’elles se tournent vers les méthodes de production traditionnelles. Le moulage par injection ne satisfait pas ces demandes en raison de la longueur des délais et du coût élevé des moules. La fabrication additive, en revanche, représente la solution idéale dans ces cas de figure. De nombreuses entreprises se tournent donc vers un service de fabrication additive pour optimiser le temps et les ressources, obtenant de meilleurs résultats tant en termes de performances que d’optimisation des processus de production.
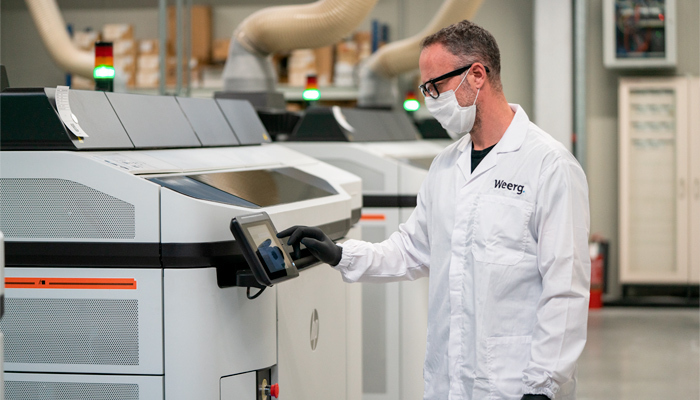
Un opérateur au siège du service de fabrication additive Weerg (crédits photo : Weerg)
Le recours au service en ligne Weerg et à la technologie HP Multi Jet Fusion
Voici une success story qui s’inscrit dans ce contexte. Elle est née de la collaboration entre la société Ursus, active depuis plus de 50 ans dans le secteur de la métallurgie et des composants de bicyclette, et le service de fabrication en ligne Weerg. Les deux sociétés ont collaboré à la création du guidon Magnus H.02 avec la technologie HP Multi Jet Fusion, mise à disposition par Weerg. Basé à Scorzè (Venise), Weerg est un service de fabrication en ligne qui propose des solutions d’impression CNC et 3D, avec une production 100% interne. Quant à la fabrication additive, la société propose les technologies FDM, SLA et HP Multi Jet Fusion (MJF), possédant la plus grande flotte d’imprimantes 3D MJF au monde. Ursus s’est donc tourné vers Weerg pour pouvoir d’abord tester puis produire le nouveau guidon Magnus H.02.
En tant qu’entreprise renommée dans le monde du cyclisme, Ursus est connue pour sa volonté d’innover à travers la recherche et le design de ses produits. En effet, le guidon Magnus H.02 représentait un défi pour les concepteurs d’Ursus, car c’est un guidon de vélo de course sur lequel Ursus a beaucoup travaillé pour allier légèreté, ergonomie et aérodynamisme. Lors de la conception du guidon, l’objectif était de créer un système de serrage qui pourrait s’adapter parfaitement à différents cadres.
« Souvent, lorsque certains fabricants de vélo nous contactent pour monter un de nos produits sur leurs cadres, ils nous fournissent des mesures différentes d’un projet à l’autre. Par conséquent, notre objectif est de créer des solutions personnalisées pour pouvoir adapter parfaitement notre produit à chaque cadre », a expliqué Matteo Cortese, Product Designer d’Ursus.
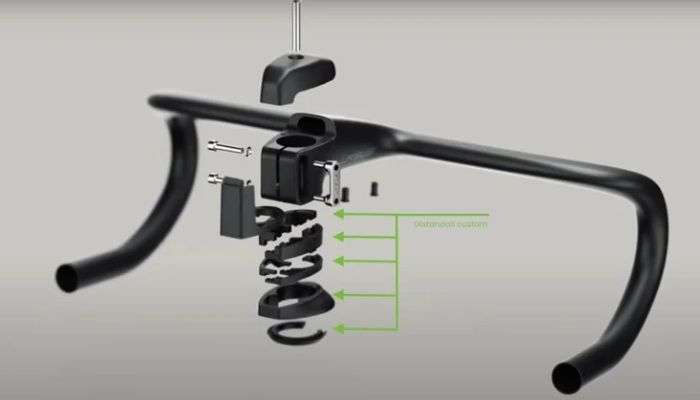
Crédits photo : Ursus/Weerg
Pour adapter le guidon Magnus H.02 à différents types de cadre, la solution a été de créer différentes entretoises qui ajustaient la hauteur du crochet sur les différents cadres. Compte tenu du faible nombre d’exemplaires d’adaptations et du besoin de personnalisation, l’utilisation de la technologie MJF fournie par Weerg a fourni la solution idéale. La technologie MJF est en effet l’une des plus intéressantes en termes d’optimisation du temps et des coûts, présentant d’énormes avantages en matière de flexibilité et de capacité à traiter une grande variété de géométries complexes par rapport aux autres technologies de fabrication additive. Elle permet également de garder intactes les propriétés mécaniques du matériau, ce qui le rend adapté à ce type d’application.
Le processus de production du guidon Magnus H.02 par Ursus
Pour les concepteurs de la société Ursus, le processus de production du guidon Magnus H.02 a commencé lorsqu’ils se sont tournés vers la plate-forme en ligne Weerg afin d’évaluer la faisabilité du projet. Étant un service entièrement en ligne, Weerg vous permet d’entrer des fichiers 3D, des spécifications sur les matériaux, les finitions et les délais de livraison dans une seule interface de manière simple et intuitive afin de recevoir un devis gratuit en quelques secondes. Côté matériaux, la plate-forme Weerg permet par exemple de choisir parmi de nombreux polymères pour l’impression 3D, dont la résine, le polypropylène, le PEEK, l’ABS et le nylon. Weerg a ensuite développé l’innovant PA 12 Blanc pour la technologie MJF en collaboration avec son fabricant, HP.
Le projet Ursus a ensuite été envoyé puis analysé en interne par un ingénieur de Weerg, qui a assisté Ursus dans la réalisation du guidon. La possibilité d’avoir un ingénieur spécialisé dédié à votre projet représente sans aucun doute une valeur ajoutée car elle vous permet d’allier l’efficacité du service en ligne à la compétence et l’assistance humaine, parfois nécessaires pour mener à bien les projets.
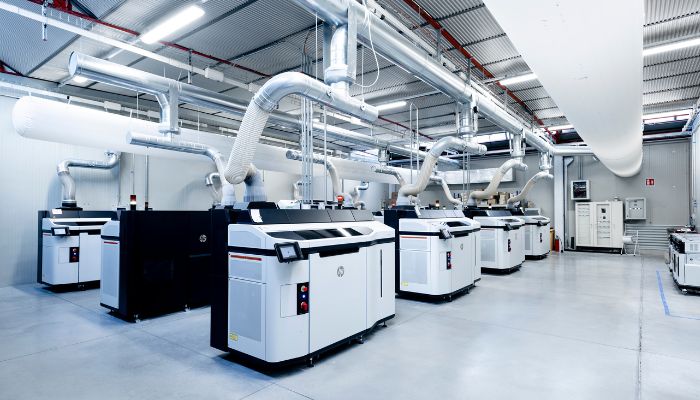
Le parc de machines HP Multi Jet Fusion de Weerg (crédits photo : Weerg)
En outre, le fait que la production s’effectue à 100% en interne a permis à Weerg de livrer rapidement les premiers modèles de guidon, à tester par les designers d’Ursus. Matteo Cortese a ajouté : « Grâce à la technologie MJF, Weerg nous a permis de créer d’excellentes pièces finies avec de bonnes propriétés mécaniques isotropes. Sur place, nous avons pu commander et recevoir les quelques milliers d’unités dont nous avions besoin pour le projet en une dizaine de jours« .
Dans le cas précis d’Ursus, pouvoir utiliser la technologie MJF pour le prototypage rapide du guidon a représenté un tournant pour les concepteurs, qui ont pu tester les propriétés mécaniques du guidon rapidement et à moindre coût, en le modifiant et en le personnalisant à chaque fois jusqu’à l’obtention du produit final. Une fois les tests achevés, ils ont ensuite pu commander les unités du produit fini nécessaires. Selon l’entreprise, l’utilisation de la technologie HP MJF fournie par Weerg a permis d’économiser jusqu’à 20 fois le budget et les temps de développement disponibles, confirmant le rôle de la fabrication additive en tant que méthode de production idéale pour des pièces performantes et personnalisées.
Pour plus d’informations sur la technologie Weerg et HP MJF, cliquez ICI.
Que pensez-vous de l’utilisation de la technologie MJF dans le cadre de la collaboration entre Weerg et Ursus ? Partagez votre expérience dans les commentaires de l’article. Retrouvez toutes nos vidéos sur notre chaîne YouTube ou suivez-nous sur Facebook ou Twitter !
Crédits photo de couverture : Ursus/Weerg