Les visages de la fabrication additive : Olaf Diegel
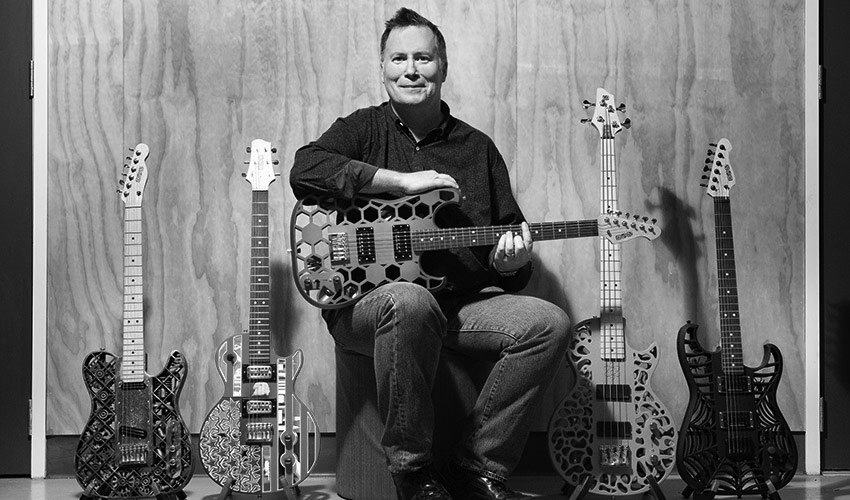
Notre série « Les visages de la fabrication additive » revient sur les pionniers qui ont façonné le secteur actuel de l’impression 3D. Suite à notre dernier portrait de Terry Wohlers, célèbre pour ses rapports annuels du secteur, on s’intéresse aujourd’hui à un profil totalement différent avec Olaf Diegel. Professeur en Fabrication Additive à l’Université de Auckland, Olaf a compris il y a déjà plusieurs années le potentiel de l’impression 3D pour la conception de pièces aux formes complexes, travaillant aussi bien sur des instruments de musique, des prothèses médicales ou des pièces de joaillerie. 3Dnatives est allé à sa rencontre pour en savoir plus sur sa vision du secteur.
3DN : Pouvez-vous vous présenter ainsi que votre travail dans le secteur de la fabrication additive ?
Je suis actuellement professeur de fabrication additive à l’Université d’Auckland, en Nouvelle-Zélande, où mon domaine de compétence est le design en fabrication additive. Auparavant, j’étais très impliqué dans le développement de produits, à la fois dans la recherche sur la manière de commercialiser plus rapidement de meilleurs produits et en tant que praticien où j’aidais les entreprises dans leur développement, de l’identification du problème à résoudre à la conception technique détaillée, en passant par la fabrication et à la commercialisation du produit. Au cours de ma carrière, j’ai commercialisé plus de 100 solutions dans des domaines tels que les produits d’éclairage de théâtre, les produits de surveillance de la santé à domicile, les produits marins, les instruments de musique, etc.
C’est ce travail qui a développé mon intérêt particulier pour la fabrication additive (ou prototypage rapide, comme on l’appelait à l’époque). C’était au milieu des années 90, où j’utilisais la technologie uniquement comme outil de prototypage pour vérifier que mes conceptions fonctionneraient avant d’investir beaucoup d’argent dans l’outillage de production. Mais au fur et à mesure que les technologies évoluaient au fil des années, je commençais à être de plus en plus intéressé par la façon de les utiliser pour la production, plutôt que pour le prototypage.
Plus je m’impliquais dans la fabrication additive, plus je réalisais que, parce que les technologies étaient relativement lentes et chères, il n’était pas rentable d’imprimer des pièces qui n’étaient pas spécifiquement conçues pour ces technologies. Cela m’a permis de commencer à trouver les meilleures techniques pour créer des pièces imprimables plus rapidement (et à moindre coût), nettement plus légères que les pièces d’origine grâce à des techniques telles que l’optimisation topologique et les structures lattices, ou pour ajouter des fonctionnalités au produit final.
3DN : Pouvez-vous nous présenter l’un de vos projets actuels ?
Récemment, nous avons travaillé sur un projet avec un artiste local appelé Gregor Kregar. Il travaille normalement sur des projets artistiques à grande échelle mais, dans ce cas, il souhaitait à la fois explorer le potentiel de production artistique de la fabrication additive et la possibilité de produire des œuvres plus petites. Dans ce cas particulier, il souhaitait jouer avec un contraste de poids en créant des dinosaures gonflables, à priori incroyablement légers, mais finalement fabriqués pour être aussi lourds que possible lorsque portés. Donc, bien que nous ayons imprimé les dinosaures comme une « coquille », avec une épaisseur de paroi extérieure de 2 mm, nous avons laissé toute la poudre non fondue piégée à l’intérieur afin de les alourdir le plus possible.
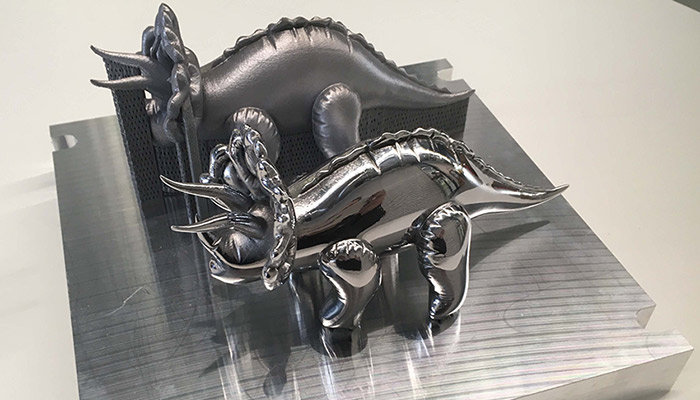
Ces dinosaures ont été imprimés à partir d’un aluminium AlSi10Mg sur une machine EOS
C’est l’une des choses les plus cool de notre laboratoire dans la mesure où nous travaillons avec tout le monde, des ingénieurs les plus sérieux aux artistes avec les idées les plus folles. Souvent, ce sont eux qui poussent les technologies le plus loin parce qu’ils ne sont pas aussi limités par ce que les ingénieurs savent ne pas pouvoir faire. Ils nous font donc réfléchir aux choses et ensuite trouver des moyens de réaliser l’impossible.
3DN : En tant que pionnier de l’industrie de la fabrication additive, pouvez-vous nous donner une idée de ce à quoi elle ressemblait il y a 10 ans ?
10 ans est en fait un assez bon nombre à regarder, car c’est à peu près à l’époque où certaines technologies de fabrication additive ont évolué à un point tel qu’elles pourraient créer des pièces résistantes, parfaitement adaptées à la production. Auparavant, presque toutes les technologies étaient principalement adaptées au prototypage. Indiscutablement, au cours des 20 précédentes années, les technologies de prototypage se sont considérablement améliorées et sont passées de technologies de prototypage esthétiques à des technologies de prototypage d’ingénierie fonctionnelle qui ont réellement contribué à accélérer le développement de produits.
Depuis lors, presque chaque année, nous constatons des progrès assez importants dans les technologies, les rendant de plus en plus adaptées à une gamme plus large de besoins de production. À mesure que les vitesses des machines augmentent et que les qualités de surface et les propriétés des matériaux continuent de s’améliorer, je pense que nous les verrons utilisées dans un plus grand nombre d’applications commerciales par d’autres entreprises qui pourraient ne pas les envisager aujourd’hui.
3DN : Quels ont été les changements les plus importants de l’industrie au fil des années ?
Je pense que le plus grand changement dans le secteur a eu lieu lorsque certaines entreprises pionnières ont compris que les technologies avaient évolué au point d’être utilisées pour produire des pièces finies. Cela a probablement nécessité un changement mental considérable dans l’entreprise et un peu de courage pour risquer de transformer des pièces imprimées en un produit réel. Ainsi, même si la technologie elle-même s’est progressivement améliorée au fil des ans, j’ai pensé que c’est le changement de mentalité des utilisateurs, pensant qu’elle pouvait être employée pour la production, qui a été le catalyseur permettant de faire de la fabrication additive ce qu’elle est aujourd’hui.
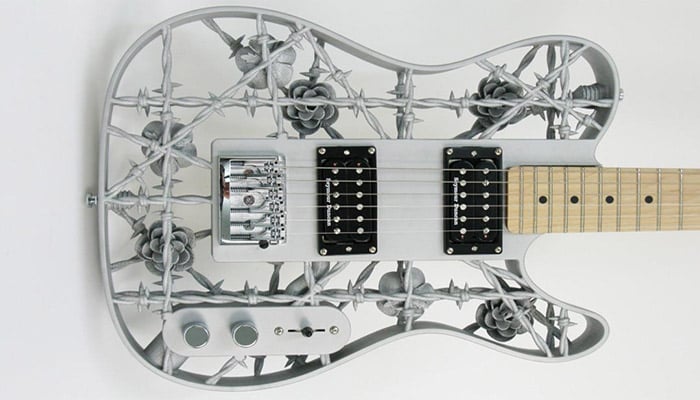
Passionné de musique, Olaf Diegel a travaillé sur différentes instruments imprimés en 3D
3DN : Pouvez-vous nous donner plus de détails sur les technologies et les matériaux qui, selon vous, connaîtront la plus grande croissance ?
Les technologies utilisant des matériaux en poudre (fusion sur lit de poudre métal et frittage polymère) sont celles qui conviennent le mieux à une production réelle. Cela tient en grande partie au fait que la plupart des photopolymères utilisés dans l’impression 3D sont durcis aux rayons ultraviolets et, par conséquent, sensibles aux rayons UV ambiants. Par conséquent, ils ne vieillissent pas bien (même s’il existe des exceptions). Une fois que le chimiste aura découvert comment faire durcir ces polymères en un plastique permanent, ils pourraient devenir des matériaux – et donc des technologies – très intéressants du point de vue du développement de produits en raison de leur capacité à fabriquer des structures multi-matériaux et de calibres fonctionnels. Cela pourrait aider à créer un tout nouveau type de produits qui tire parti de ces nouveaux matériaux, ce qui n’est pas possible aujourd’hui.
3DN : Quels sont les défis actuels qui empêchent l’adoption mondiale de la fabrication additive et comment sont-ils abordés ?
Aujourd’hui, je pense que le plus gros défi est que la majorité des concepteurs et des ingénieurs ne savent pas encore concevoir pour la fabrication additive (DfAM). La plupart des entreprises qui se rendent dans notre laboratoire arrivent avec une pièce conçue pour l’usinage ou le moulage par injection et nous demandent si nous pouvons l’imprimer pour elles. Nous leur disons que, oui, nous pouvons, mais ils ont ensuite une légère crise cardiaque lorsque nous leur disons le prix. En effet, toutes les technologies de fabrication additive sont aujourd’hui relativement lentes et les pièces qu’elles fabriquent sont donc très coûteuses. Elles ne peuvent donc être utilisées que pour les produits de la plus haute valeur. Cependant, avec une bonne conception pour l’impression 3D, les prix peuvent être considérablement réduits (souvent jusqu’à 80 ou 90% par rapport à une pièce qui n’était pas conçue pour la fabrication additive) tout en améliorant considérablement la fonctionnalité de la pièce – par exemple, l’alléger de 70% ou réduire le nombre de composants dans la conception.
La majorité des concepteurs et des ingénieurs ne savent pas encore concevoir pour la fabrication additive, c’est cela qui empêche une adoption mondiale de la technologie.
Avec l’accélération de la vitesse des technologies d’impression, l’adoption augmentera à un rythme toujours croissant, mais je pense que de bonnes pratiques de design pour la fabrication additive permettront de réduire beaucoup plus rapidement cet obstacle à l’adoption.
Il est vraiment agréable de voir que, en particulier au cours des deux dernières années, nous observons un nombre croissant de cours de DfAM pour remédier à ce problème d’éducation. Mais ce que nous ne voyons pas encore, c’est que les programmes universitaires incorporent cela dans leurs cours généraux de fabrication afin que les diplômés sortent de l’université sachant concevoir pour la fabrication additive (ou au moins sachant qu’ils doivent concevoir différemment pour cette technologie). Cela commence à arriver, mais juste un peu plus lentement que ce que je voudrais voir.
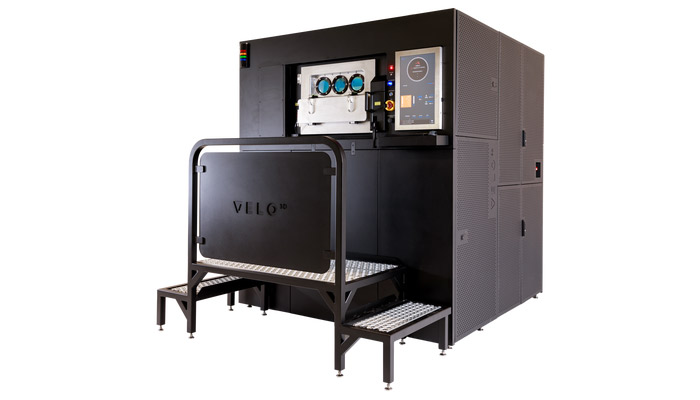
Selon Olaf Diegel, Velo3D est une technologie à suivre de près
3DN : Quelles sont les entreprises, technologies ou applications qui ont retenu votre attention ces derniers mois ?
Les deux technologies qui ont retenu mon attention au cours de l’année écoulée sont le potentiel de la machine Velo3D, capable d’imprimer des pièces métalliques sans aucun support (ou avec des angles de support très faibles), et la technologie LaserProFusion d’EOS dotée d’une rangée d’un million de diodes laser pour faire fondre une poudre polymère, ce qui pourrait considérablement augmenter la vitesse de l’imprimante. Mais nous devons toujours faire attention avec tout le battage marketing de l’industrie ; attendons que les résultats soient donnés lorsque ces nouvelles technologies commenceront à être testées par de vrais utilisateurs sur de vraies pièces.
*Crédits photo de couverture : Dean Carruthers/University of Auckland
Que pensez-vous des travaux d’Olaf Diegel ? Partagez votre avis dans les commentaires de l’article ou avec les membres du forum 3Dnatives. N’hésitez pas à nous suivre sur Facebook ou Twitter !