Honda conçoit un vilebrequin imprimé en 3D plus léger
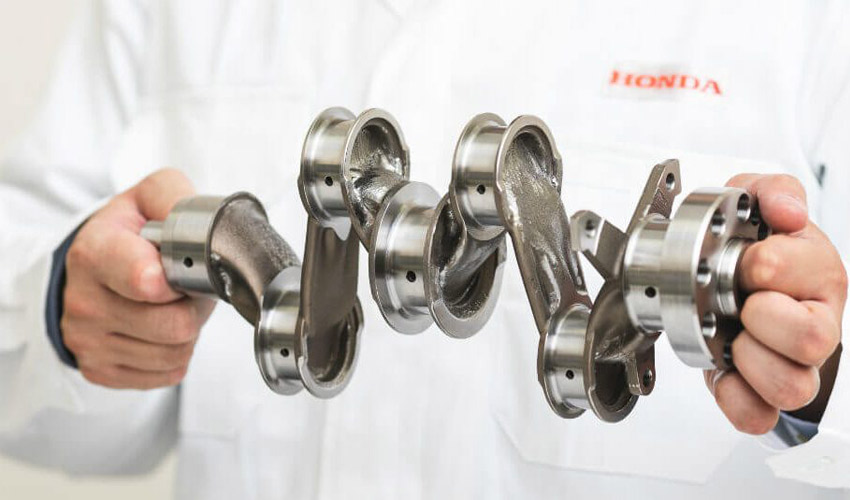
En 2016, le constructeur automobile japonais Honda nous avait présenté sa petite voiture utilitaire, Micro Commuter, conçue en partie grâce à l’impression 3D : 4 ans plus tard, l’entreprise frappe plus fort en exposant un vilebrequin imprimé en 3D en métal. Créé en collaboration avec Autodesk, le design du composant a été entièrement repensé afin de réduire le poids final de la pièce et la consommation de carburant. Le vilebrequin est un élément essentiel du moteur de la voiture, nécessitant résistance et endurance, souvent conçu en acier via des méthodes de fabrication traditionnelles comme le forgeage. Toutefois, la fabrication additive pourrait bien apporter une légèreté supplémentaire, très recherchée par les constructeurs automobiles qui veulent réduire leur impact environnemental. Pour l’instant, Honda ne présente qu’un prototype fonctionnel : une mise à l’échelle et une production en série seraient l’objectif final.
Cela fait des années que les fabricants conçoivent les vilebrequins de la même façon afin qu’ils répondent à des exigences élevées : résistance aux pressions de combustion ou encore maintien de l’équilibre de rotation. Honda, qui emploie la fabrication additive depuis plusieurs années afin d’alléger le poids de différentes pièces (supports de ceinture de sécurité, unités de commande du moteur, cadres de moto), a voulu dupliquer cette méthode de conception : pourquoi ne pas imprimer en 3D le vilebrequin et proposer un composant 30% plus léger ? Il a donc fait appel à la société Autodesk, réputée pour ses nombreuses solutions de modélisation 3D comme AutoCAD, Fusion 360 ou encore Netfabb. Hirosumi Todaka, concepteur de machines mécaniques et fluides chez Honda R&D, ajoute : “Il fallait une nouvelle approche qui utilise des méthodes comme la conception générative et la fabrication additive. Nous devions nous débarrasser des idées préconçues et voir les choses sous un nouveau jour. C’est pour cela que nous nous sommes fixé l’objectif ambitieux de concevoir un vilebrequin qui soit 30 % plus léger que les modèles actuels.”
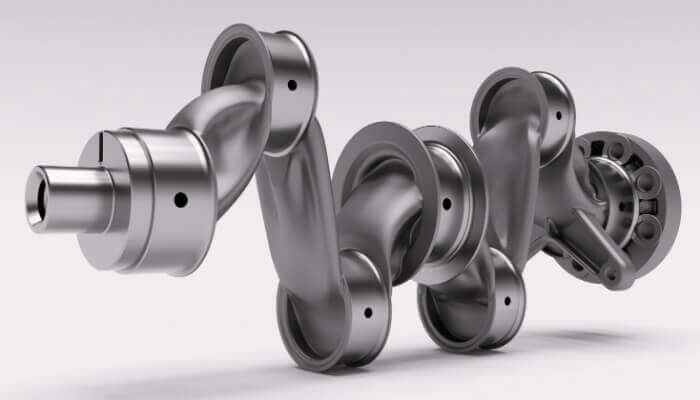
Un rendu du vilebrequin modélisé (crédits photo : Honda R&D)
Grâce aux solutions de conception générative proposées par Fusion 360 et Netfabb, Autodesk a pu proposer plusieurs itérations possibles pour le vilebrequin. Celles-ci reposaient toutes sur une structure organique, inspirée par la nature. Une fois que Honda a sélectionné le design qui lui plaisait le plus, des équipes ont été envoyées au Centre technologique Autodesk en Angleterre pour aller plus loin et en savoir plus sur les possibilités de la conception générative et de la fabrication additive. Une session qui aurait permis d’affiner davantage le design et de proposer un prototype amélioré.
Finalement, le prototype imprimé en 3D présente une réduction de poids de 50% selon les équipes de Honda. Celles-ci affirment qu’elles n’auraient jamais pu obtenir un tel composant via des méthodes de fabrication classiques. On ne sait pas quelle technologie d’impression 3D métal a été utilisée ni quel matériau mais le résultat est là : l’impression 3D et la conception générative ont permis de produire une pièce plus performante. Il fallait bien entendu la tester : pour l’instant, Autodesk doit encore affiner le design pour que le vilebrequin imprimé en 3D soit plus efficace.
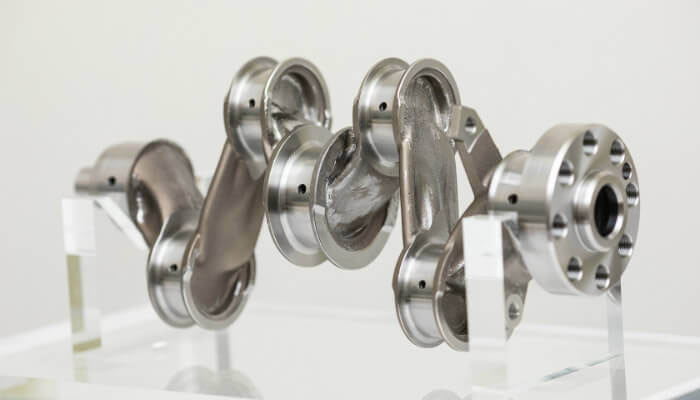
Le prototype final (crédits photo : Autodesk / Honda)
Hirosumi Todaka conclut : “Bien que certains émettent encore des réserves sur cette nouvelle forme, l’attention qu’elle a apportée à la technologie en a valu la peine. Bien qu’il y ait encore beaucoup à faire pour alléger les pièces, nous pouvons maintenant voir une voie à suivre pour atteindre nos objectifs. À l’avenir, je m’attends à ce que les produits innovants créés à l’aide de la conception générative soient la norme.” Vous pouvez retrouver davantage d’informations ICI.
Que pensez-vous de ce vilebrequin imprimé en 3D ? Partagez votre avis dans les commentaires de l’article ou avec les membres du forum 3Dnatives. Retrouvez toutes nos vidéos sur notre chaîne YouTube ou suivez-nous sur Facebook ou Twitter !
c’est une pub pour dire que Autodesk et Honda il est beau.
Le poids d’un vilebrequin participe à la régularité cyclique. Avec un vilo plus léger ils vont mettre un volant plus lourd ?
Pas étonnant la réduction de 30% car il n’y a plus de contrepoids ! Comment a été calculer la dynamique cinétique de cet élément qui est rotatif et contraint au mouvement des pistons ?
Quel intérêt de phosphorer sur une techno en voie d’obsolescence accélérée comme le moteur thermique ? sur un moteur électrique pas besoin de vilebrequin.
vilebrequin 3 paliers = moins de friction mais moins de puissance , il y a un dessin plus simple 3 paliers et plus efficace . l’avenir est au moteur électrique …