Velettrica utilise l’impression 3D pour un transport maritime plus durable
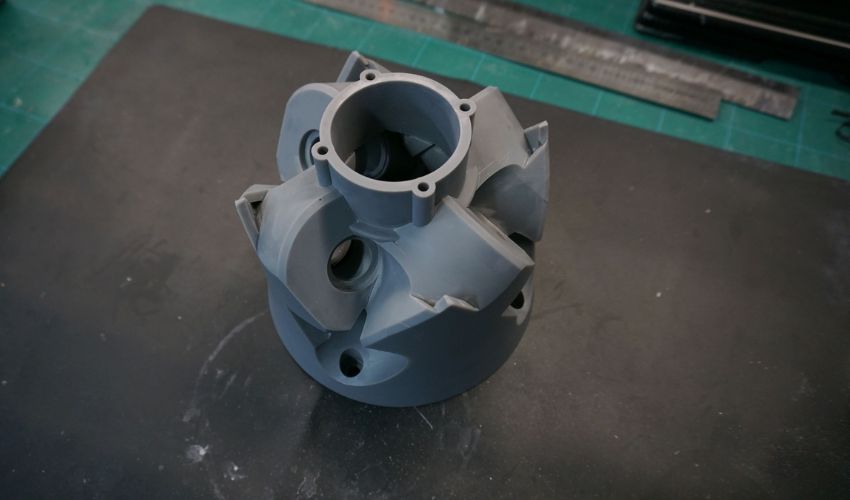
La fabrication additive a atteint un tel niveau de maturité qu’elle permet de créer toutes sortes de pièces avec des matériaux avancés qui garantissent des solutions efficaces et rentables même dans les environnements les plus extrêmes, du ciel à l’espace en passant par les profondeurs de l’océan. Un exemple emblématique de cette révolution technologique est Velettrica, une startup italienne qui a utilisé l’impression 3D pour développer des composants clés pour le prototype fonctionnel du moteur du voilier SAIL-POD 25. Pour en savoir plus et découvrir comment l’utilisation de technologies de pointe, telles que l’impression 3D et la conception biomimétique, ouvre de nouvelles frontières à la « voile durable », nous avons rencontré le fondateur de Velettrica, Roberto Baffigo.
3DN : Pouvez-vous vous présenter et nous parler de votre lien avec l’impression 3D ?
Bonjour, je m’appelle Roberto Baffigo, je suis né en 1972 à Rome et dans ma vie j’ai toujours fait du sport, de l’aviron, de la voile, du VTT, du ski et maintenant de la nage avec palmes. J’ai étudié la physique, ce qui a stimulé ma curiosité et mon désir d’expérimenter. Mon lien avec l’impression 3D vient du monde de la bijouterie : le passage du prototypage manuel au numérique a été une véritable révolution qui a explosé avec la disponibilité de techniques d’impression de plus en plus fiables et peu coûteuses. Par la suite, l’impression 3D m’a permis de tester rapidement toutes les inventions contenues dans l’hélice inédite de Velettrica.
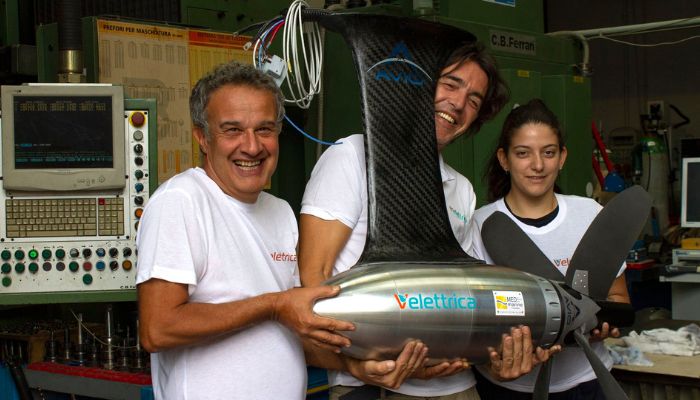
Roberto Baffigo et l’équipe de Velettrica avec le moteur SAIL-POD 25
3DN : Comment est née Velettrica et quelle est sa mission ?
Velettrica est née en 2021 du rêve d’explorer la voile sans impact, une idée qui a mûri pendant les vacances en mer avec ma femme Chiara et nos enfants Stella et Pietro Noè. J’ai toujours rêvé de pouvoir voyager avec eux en équilibre avec la nature. J’ai voulu rendre le voilier encore plus respectueux de l’environnement en utilisant un moteur électrique, non seulement pour la propulsion, mais aussi pour produire de l’énergie lorsqu’il est poussé par le vent. Le moteur développé dans le cadre du projet Velettrica s’appelle le SAIL-POD 25.
La mission de Velettrica est claire : développer des systèmes de propulsion économes en énergie, alimentés principalement par des sources renouvelables, afin de réduire la pollution des mers. Le cœur de l’innovation de Velettrica réside dans une hélice multifonctionnelle dotée d’un système de contrôle électronique, conçue selon une approche biomimétique inspirée des ailerons du requin-baleine. Lorsqu’elle n’est pas utilisée, cette hélice se referme en forme de fleur, minimisant ainsi la résistance à l’eau et optimisant l’efficacité énergétique du système de propulsion.
3DN : Pouvez-vous nous en dire plus sur le moteur SAIL-POD 25 ? Comment la fabrication additive a-t-elle été utilisée pour sa réalisation ?
Nous avons utilisé l’impression 3D pour plusieurs composants du SAIL-POD 25, dans certains cas les pièces finales ont été fabriquées directement, dans d’autres cas le prototypage rapide a été utilisé pour fabriquer les moules ou les noyaux pour le composite. Il s’agit d’un système de propulsion et de recharge électrique très efficace pour les voiliers, avec une hélice pliable et à pas variable. Facile à installer, il ne prend pas de place à l’intérieur du bateau, ne pollue pas et ne nécessite pas d’entretien. Il ne produit ni bruit, ni vibration, ni chaleur.
Conçu en Italie par Velettrica, 3DiTALY a imprimé en 3D certains des composants d’un prototype fonctionnel du moteur en combinant plusieurs matériaux et technologies d’impression. L’imprimante SLS Fuse 1 de Formlabs et la poudre de Nylon 12 ont été utilisés pour fabriquer le noyau des pales de l’hélice : ce thermoplastique présente une résistance élevée à la traction et une stabilité environnementale, ce qui le rend particulièrement adapté à la production d’assemblages complexes et de composants durables avec une absorption d’eau minimale. Le premier prototype du moyeu de l’hélice pour les essais à sec, en revanche, compte tenu de sa forme complexe, a été fabriqué à l’aide de l’imprimante SLA Form 3L de Formlabs et d’une résine Grey, afin d’obtenir un niveau de détail élevé, une finition de surface lisse et mate et des propriétés mécaniques optimales. Enfin, les pièces mécaniques « spéciales » sont produites à partir d’Inconel ou d’aluminium grâce à la technologie DMLS et le moule de l’aileron est fabriqué à partir d’un photopolymère HDT grâce à la technologie SLS.
3DN : Pourquoi Velettrica a choisi l’impression 3D ?
Pour de nombreux composants, il s’agissait d’un choix obligatoire ; compte tenu de la nature « nouvelle » et complexe des mécanismes brevetés, il aurait été impossible ou excessivement coûteux de les produire à l’aide des technologies traditionnelles.
Pour aller plus loin, l’impression 3D offre de multiples avantages, tels que la possibilité de réaliser des prototypes rapides en moins de 24 heures ; des réductions de coûts allant jusqu’à 90% par rapport à l’usinage ; la production de pièces complexes telles que des hélices, des pales de turbines pour des équipements sous-marins ; la possibilité d’utiliser des matériaux avancés dotés de propriétés intéressantes telles que la résistance au feu, la réduction des émissions toxiques et la résistance à la corrosion ; et enfin, la production à la demande, qui permet aux concepteurs d’obtenir des pièces exactement au moment et à l’endroit où ils en ont besoin, réduisant ainsi les coûts de stockage, le risque de surproduction et l’impact sur l’environnement, et favorisant l’efficacité et la durabilité.
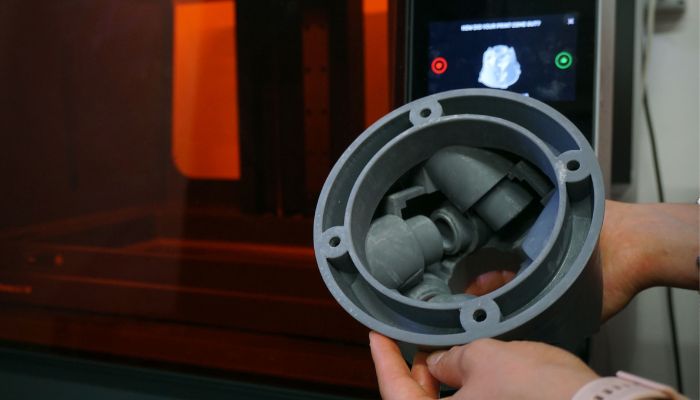
Une partie de l’hélice a été réalisée par impression 3D résine
3DN : Comment voyez-vous le rôle de la fabrication additive dans le secteur maritime ?
Le secteur naval, en particulier dans le domaine de la propulsion électrique, est souvent caractérisé ou bénéficie d’une production sur mesure ou semi-personnalisée. La fabrication additive, comme nous l’avons mentionné, offre une grande liberté en réduisant les coûts des composants fabriqués sur mesure. De plus, les avantages en termes de durabilité sont à la fois l’économie de matières premières et d’énergie dans la production par rapport à d’autres techniques, et la facilité de recyclage des matériaux utilisés à la fin de la vie du composant, ceci principalement pour les thermoplastiques. Enfin, les matériaux polymères sont beaucoup plus proches d’une protection anti-salissure que les métaux, ce qui permet, par exemple dans les hélices, une moindre dispersion de produits chimiques dans l’environnement et un maintien de l’efficacité avec les économies d’énergie qui en découlent.
3DN : Un dernier mot pour nos lecteurs ?
Nous avons de nombreux projets et rêves pour l’avenir. Dans le futur, nous voulons voler, dans le même esprit que la voile-électricité, pour sillonner le ciel de la manière la plus durable possible. Un message pour ceux qui nous lisent : utilisez l’impression 3D pour « toucher » vos idées, c’est l’outil qui permet de réaliser les rêves.
Que pensez-vous de la jeune pousse Velettrica ? Partagez votre avis dans les commentaires de l’article. Retrouvez toutes nos vidéos sur notre chaîne YouTube ou suivez-nous sur Facebook ou LinkedIn !
*Crédits de toutes les photos : Velettrica/3DiTALY/Formlabs
Il n’y a rien à ajouter, tout est clair ! C’est magnifique !
Prof Abdo MAALAOUI, retraite, Fondateur du Laboratoire de recherche et d’Innovation « LBL » dont le but est de former les jeunes de la Ruralité aux nouvelles technologies.
Projet de la Coopération Canada -Tunisie