Thales Alenia Space envoie plus de 400 pièces imprimées en 3D dans l’espace
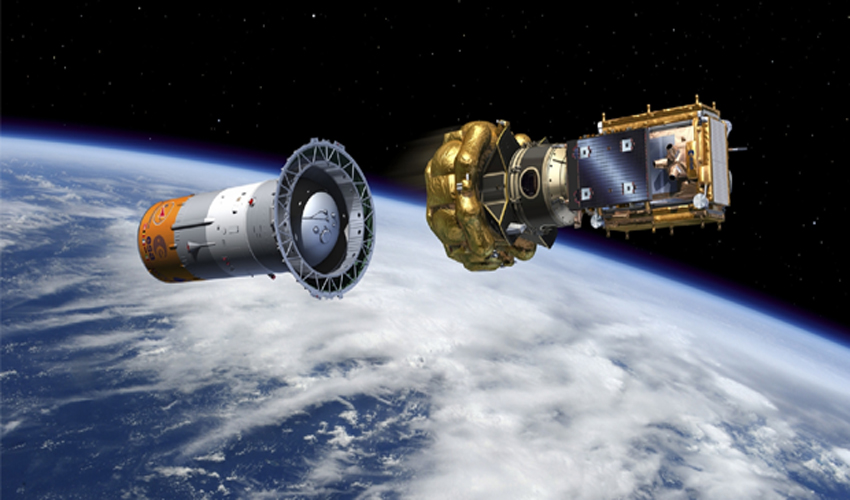
L’impression 3D accompagne la construction de plus en plus de pièces pour satellites et autres engins spatiaux. Thales Alenia Space est un bon exemple de cette tendance qui semble s’accroître. L’entreprise vient d’envoyer plus de 400 pièces en métal et en plastique imprimées en 3D en orbite.
Thales Alenia Space est un spécialiste des systèmes spatiaux depuis plus de 40 ans, fruit d’une joint-venture entre Thales et Leonardo. L’entreprise conçoit et teste ces systèmes afin de répondre aux besoins en termes de navigation, télécommunication, exploration, observation, etc. Elle a commencé s’intéresser à la fabrication additive en avril 2015 et a conçu un support d’antenne en aluminium grâce à cette méthode de production. Il a été mis en orbite sur le satellite Turkmenalem Monacostat avec succès. Depuis, chaque satellite envoyé possède une antenne similaire imprimée en 3D, rendue plus légère grâce aux technologies 3D.
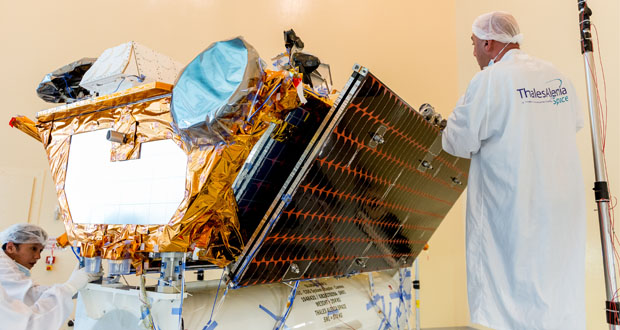
Le satellite Iridium Next comporte des pièces imprimées en 3D (crédits photo : Thales Alenia Space)
Thales Alenia Space vient de placer 79 pièces en métal en orbite et 350 supports de tubes pour la propulsion chimique en polymère. Les pièces en métal ont été imprimées en 3D pour différents satellites à partir de la technique du Laser Beam Melting qui vient fusionner une poudre métallique couche par couche dans un environnement contrôlé. L’entreprise a travaillé avec Polyshape pour créer certaines de ces pièces et a principalement utilisé l’imprimante 3D de Concept Laser, la X-Line 1000R. Sur l’ensemble de ces pièces, 47 ont un design différent et remplissent 13 fonctions distinctes.
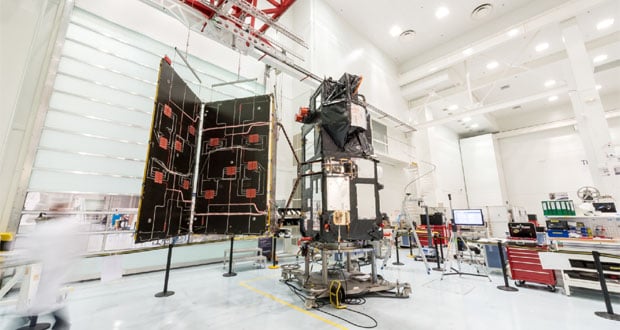
Le Sentinel-3 comporte également des pièces imprimées en 3D (crédits photo: Thales Alenia Space)
En ayant recours à la fabrication additive, Thales Alenia Space peut fabriquer des pièces en un seul morceau, sans avoir besoin d’assembler différentes parties d’une même structure. C’est un gain de temps, de coût mais aussi de masse important. Cette méthode de fabrication permet aussi de créer des structures plus complexes tout en conservant une vitesse de production plus élevée. Plusieurs experts de l’aérospatial se sont d’ailleurs tournés vers la fabrication additive pour concevoir leurs appareils – c’est le cas d’Airbus par exemple.
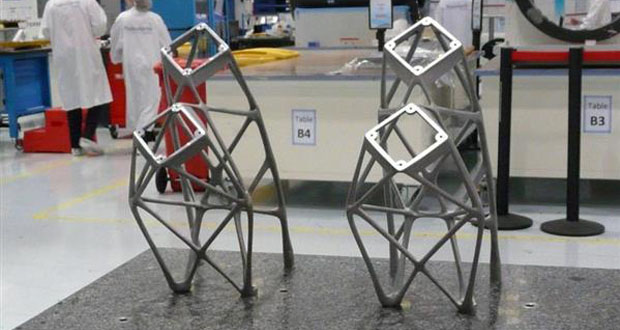
Des pièces métal conçues grâce à la fabrication additive
Les lancements réussis des différents satellites encouragent Thales Alenia Space à continuer à utiliser la fabrication additive dans ses développements futurs. L’entreprise souhaite aujourd’hui créer des pièces de plus en plus grandes. Florence Montredon, Responsable Développement des Technologies de Fabrication Additive chez Thales Alenia Space, explique : « Nos développements tournent autour de l’intégration de plusieurs fonctions dans une même pièce telles que la mécanique, la thermique, ou encore la radiofréquence. Le challenge se situe tout autant dans le processus de conception que dans la technique de production elle-même. »
Retrouvez le communiqué de presse officiel ici.
Quel est l’avenir de la fabrication additive dans le domaine aérospatial ? Partagez votre avis dans les commentaires de l’article ou avec les membres du forum 3Dnatives.