Quelles sont les tendances qui ont marqué la fabrication additive en 2020 ?
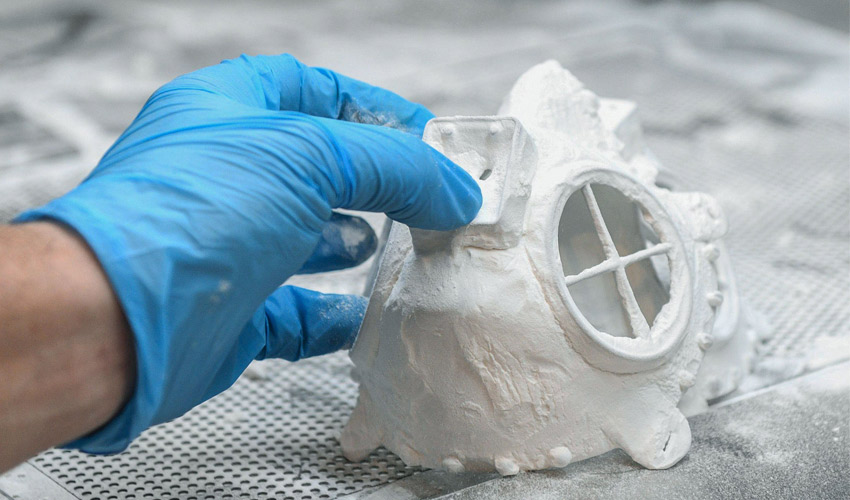
Ca y est, l’année 2020 touche à sa fin ! Et celle-ci, on s’en souviendra pendant longtemps…Alors oui, la crise sanitaire est sans nul doute ce qui a le plus marqué cette année, mais nous avons voulu revenir sur les principales tendances du marché de la fabrication additive en 2020, sur tous les faits qui ont bouleversé l’Industrie. Qu’est-ce qui a façonné le marché cette année, quelles ont été les innovations à retenir, à quoi faut-il s’attendre pour 2021 ? On vous dit tout ! N’hésitez pas à nous faire part de votre ressenti et à nous dire ce que vous attendez pour l’année prochaine !
La COVID-19 bouleverse l’industrie de l’impression 3D
En 2020, la crise sanitaire a eu des répercussions sur presque tous les secteurs d’activité. L’un des plus vulnérables durant les premiers mois de la pandémie a été sans aucun doute le médical qui s’est soudainement retrouvé à court de matériel pour faire face à la propagation du virus. Des technologies de fabrication additive ont rapidement été utilisées pour produire des équipements d’urgence pour le personnel médical et les patients du monde entier. En quelques jours, les acteurs de l’industrie de l’impression 3D ont réussi à produire des dispositifs essentiels pour le marché de la santé, tels que des visières de protection ou des respirateurs, et plus tard, des écouvillons pour réaliser des tests de dépistage. Les hôpitaux ont mis en place des solutions en interne pour soutenir cette production, les universités ont également mis leurs équipements à disposition et les fabricants sont rapidement devenus des prestataires de services.
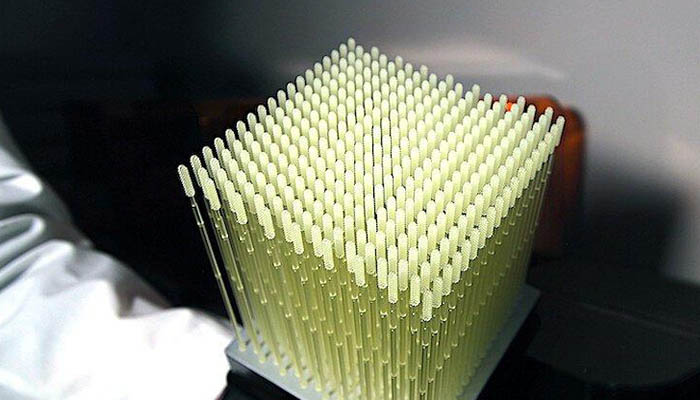
De nombreux acteurs de l’impression 3D ont produit des millions d’écouvillons (crédits photo : Formlabs)
En fin de compte, l’impression 3D a pu agir beaucoup plus rapidement que d’autres technologies de fabrication, ajoutant de l’agilité au processus de production. Elle ne reposait pas sur des chaînes d’approvisionnement complexes qui ne pouvaient plus fonctionner, la production et l’approvisionnement étant bloqués en Chine et en Asie du Sud-Est. En discutant avec Sumeet Jain, directeur général de 3D Printing Solutions by Arkema, il nous a confié : « La crise du COVID a été l’occasion pour l’impression 3D de démontrer sa proposition de valeur autour de la fabrication numérique et sa capacité à répondre aux besoins de production à la demande. De plus, la faculté de l’impression 3D à itérer des centaines de designs à court terme est une différenciation clé pour développer des solutions viables qui peuvent répondre à une demande imprévue. »
Plus globalement, le marché a été touché par la pandémie mais s’est redressé plus vite que prévu. Beaucoup d’entreprises ont investi dans des solutions d’impression 3D de bureau afin de produire facilement et rapidement des équipements de protection individuelle. Cela n’a pas entièrement compensé la perte des autres marchés (produits de consommation, l’éducation et les industries dentaire et automobile) mais la crise aura clairement démontré la flexibilité de la technologie. De nombreuses industries ont ainsi pris conscience du fait que les technologies d’impression 3D pouvaient renforcer les chaînes d’approvisionnement faibles et constituer un investissement judicieux pour l’avenir.
Pour la communauté de la fabrication additive, la COVID-19 a entraîné l’annulation de presque tous les événements. L’industrie a dû trouver de nouveaux moyens de se réunir, c’est pourquoi les événements virtuels sont devenus très populaires tout au long de l’année. Formnext, l’événement phare du marché, a également transformé son événement en édition digitale. Dans certains cas, le format virtuel a donné aux entreprises la possibilité d’adresser plus de personnes pour une fraction du coût que représente un événement physique.
En 2020, l’impression 3D continue de se développer en tant que technologie de production
Comme nous l’avons signalé l’année dernière, les technologies d’impression 3D ont montré à maintes reprises qu’elles ne sont pas seulement une technologie de prototypage. Elles peuvent être utilisées pour la production de grandes quantités et de pièces d’utilisation finale. Dans le dernier rapport de Sculpteo, 50 % des personnes interrogées ont confirmé qu’elles utilisaient cette technologie pour la production de pièces finales. De plus, la part des applications de prototypage rapide a diminué pour la première fois en cinq ans.
Pour la production en gros volume, la flexibilité et la répétabilité sont essentielles. C’est pourquoi, au cours des dernières années, l’ensemble du flux de travail de la fabrication additive s’est industrialisé afin de créer les conditions adéquates pour relever ces défis. D’énormes progrès ont été réalisés en termes de matériel, mais nous constatons également cette évolution au niveau des logiciels et du matériel de post-traitement. Par exemple, PostProcess Technologies a levé 20 millions de dollars cette année tandis que la levée de fonds de DyeMansion s’élève à 14 millions de dollars. Mais l’étape de post-traitement n’est qu’une partie de l’équation et une grande partie du développement s’est portée sur le logiciel en 2020.

Plus que jamais, les étapes de post-traitement doivent être automatisées
Le logiciel d’impression 3D devient impératif
Comme le dit Greg Kress, PDG de Shapeways : « La mise à l’échelle ne signifie pas seulement faire plus, mais aussi imprimer en 3D de manière efficace et cohérente. » Les logiciels sont essentiels pour de nombreuses étapes de l’impression 3D : imbrication, préparation des plateaux de construction, fixation des fichiers, mais aussi pour la planification de la production. En 2020, des sociétés comme AMFG, MakerOS ou 3YOURMIND sont devenues d’importants fournisseurs de solutions pour piloter la production. Par exemple, MakerOS fournit une plateforme basée sur le cloud pour centraliser tous les outils permettant de mettre à l’échelle un service d’impression ou de fabrication en 3D. De même, 3YOURMIND fournit des logiciels pour organiser les usines intelligentes de demain pour les prestataires de services mais aussi pour les entreprises qui ont intégré la technologie en interne. Le suivi du processus d’impression 3D, depuis la commande initiale de la pièce jusqu’à sa production et sa livraison, devient un facteur clé pour automatiser la production.
Des outils de CAO intégrés sont également en cours de développement. Par exemple, Netfabb est un logiciel de FAO qui soutient l’optimisation des processus de production, la réduction des temps de production et la minimisation des coûts de fabrication pour l’impression 3D. Il fournit les outils nécessaires pour rationaliser les flux de travail et réduire les erreurs de construction avant la fabrication. Autodesk a ajouté de nouvelles fonctionnalités au logiciel fin novembre 2020. De plus, des startups comme Shapeshift 3D ou PrintSyst.ai montrent également au secteur que certaines étapes du flux de travail de la fabrication additive peuvent être optimisées davantage.
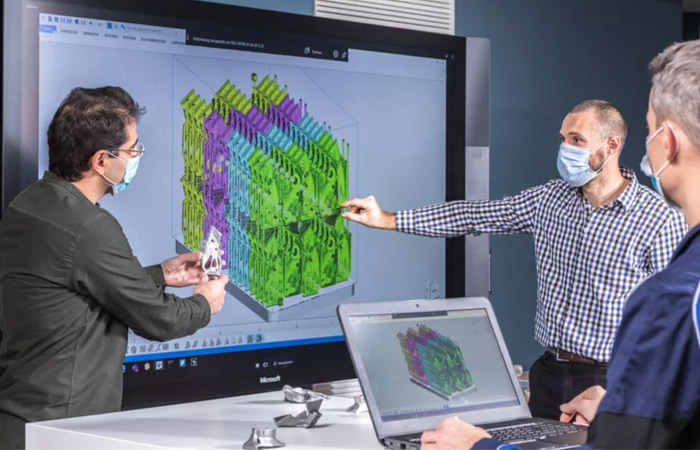
Le logiciel est une composante clé (crédits photo : BMW Group)
Enfin, le DfAM (Design for Additive Manufacturing) continue de se développer. Comme nous vous l’avons dit l’année dernière, un nombre croissant d’applications mettent en évidence l’utilisation de la conception générative ou de l’optimisation topologique pour améliorer les performances fonctionnelles, le coût et la fiabilité des pièces avec la fabrication additive. Un nouveau venu sur ce marché est TOffeeAM qui a levé plus d’un million de dollars pendant l’été. Son logiciel est une solution de conception intelligente pour la fabrication additive, basée sur la conception générative.
Le matériau est la clé pour débloquer de nouvelles applications
Les matériaux ont été au centre de nombreuses avancées cette année encore, avec deux fois plus de fournisseurs qu’il y a deux ans. Sur le marché des thermoplastiques, les polymères haute performance tels que le PEEK, le PEKK et l’ULTEM sont adoptés pour leurs propriétés uniques. De plus, le polypropylène, l’un des plastiques les plus utilisés dans le monde, s’est adapté au marché de la fabrication additive, notamment sur des procédés à base de poudre. C’est un matériau réputé pour sa résistance à la fatigue, sa semi-flexibilité et sa légèreté. BASF Forward AM a d’ailleurs développé cette année du polypropylène de qualité industrielle pour la gamme Jet Fusion 5200 de HP.
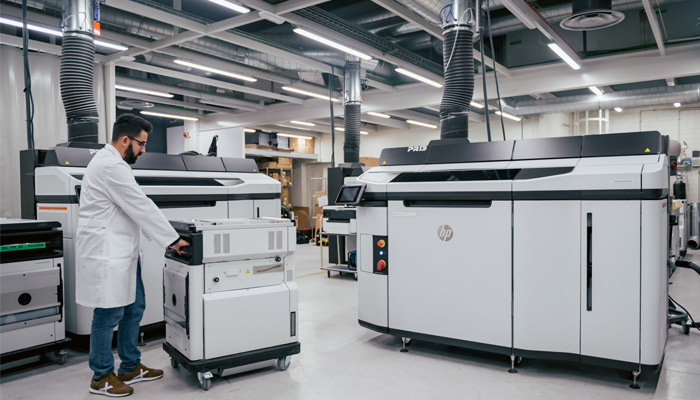
HP et BASF ont développé une nouvelle poudre PP
Le segment des composites est également en pleine croissance ; AREVO, qui vise à transformer la production de composites par la numérisation et l’automatisation, a levé 25 millions de dollars supplémentaires de financement cet été tandis qu’Arris Composites a obtenu un financement de 48,5 millions de dollars à la fin du mois d’août 2020. Quelques développements sont intéressants à soulever comme cette collaboration entre Additive Composite et Add North qui ont développé un filament en nylon renforcé en carbure de bore, l’un des matériaux les plus durs du marché après le diamant.
Enfin et surtout, la fabrication additive métallique reste un marché en pleine expansion, estimé à 1 milliard de dollars en 2020, et qui devrait croître de plus de 27 % par an au cours des prochaines années. Même si la croissance est certaine, le processus de production des poudres reste encore assez spécialisé et coûteux pour la fabrication additive, mais il est essentiel pour son industrialisation et la fabrication de pièces certifiées. Les poudres métalliques en impression 3D doivent répondre à des exigences et propriétés spécifiques qui, tant qu’elles ne seront pas atteintes, freineront la croissance du marché. De plus, l’impact environnemental de la fabrication additive métal serait plus important que les méthodes de production conventionnelles ; les entreprises et fabricants devront planifier des stratégies responsables autour de cette technologie dans les années à venir s’ils veulent assurer un avenir durable à ce matériau.
Justement, la startup 6K se concentre sur le développement de poudres métalliques à haute performance. Ils créent des poudres d’alliage qui sont véritablement sphériques, dépourvues de porosité et qui offrent une meilleure fluidité. Les poudres de titane de Sandvik ont quant à elles été certifiées pour être utilisées dans des dispositifs médicaux. Enfin, un développement intéressant est le procédé multi-métaux d’Aerosint permettant d’imprimer des pièces complexes avec deux métaux différents. La pièce la plus complexe qu’ils ont créée a été réalisée avec de l’acier inoxydable et un alliage de cuivre.
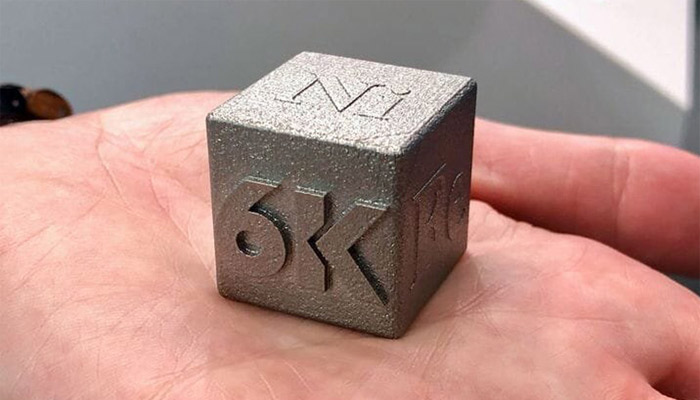
Le développement de poudres métalliques adaptées à l’impression 3D est une réelle préoccupation (crédits photo : 6K)
L’adoption de la technologie par secteur évolue en 2020
Vous le savez déjà, des secteurs comme le médical, l’aérospatial ou encore l’automobile sont les premiers adaptes de la fabrication additive et 2020 n’est pas une exception. Cette année, nous avons toutefois constaté que des marchés comme la construction, l’électronique et l’Oil & gas l’ont davantage intégrée dans leurs processus de production.
Suite à l’introduction des imprimantes 3D robotisées, l’activité dans le secteur de la construction s’est accélérée cette année. Le fabricant danois COBOD a présenté un projet de bâtiment résidentiel de trois étages aux murs imprimés en 3D à Wallhausen, en Allemagne. D’autre part, ICON, dans son dernier projet avec la NASA, estime que sa solution est bien adaptée à la construction sur la Lune. L’entreprise a obtenu un financement de 35 millions de dollars cette année. En parlant d’exploration spatiale, Relativity Space, qui a développé une fusée à moteur entièrement imprimée en 3D, a levé la somme astronomique de 500 millions de dollars. Ce dernier cycle de financement montre également que les technologies d’impression 3D ont un avenir dans la conquête de l’espace.
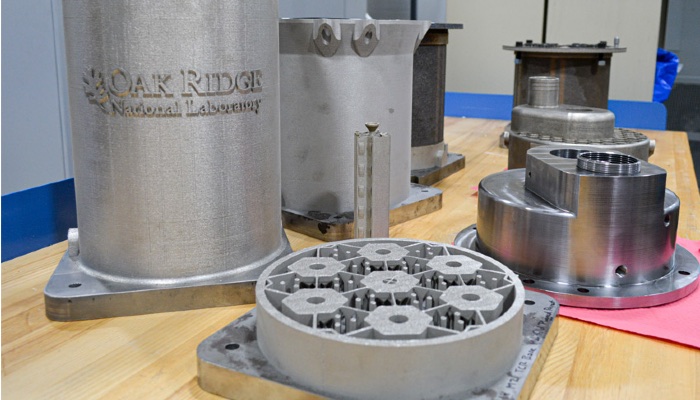
Le secteur du nucléaire se penche de plus en plus sur l’intégration de la fabrication additive (crédits photo : ORNL)
Un nombre croissant d’applications dans le domaine du pétrole et du gaz ont vu le jour. En effet, au Oak Ridge National Laboratory, les chercheurs construisent le premier réacteur nucléaire imprimé en 3D. Le laboratoire espère mettre en service le premier réacteur nucléaire de ce type en 2023, ce qui permettrait au secteur nucléaire de produire des systèmes énergétiques plus avancés et durables. Enfin, l’industrie électronique évolue également grâce aux méthodes de fabrication additive à l’échelle micro et nanométrique. Des startups comme Voltera démontrent les avantages de l’impression 3D pour concevoir des composants plus petits, plus fins et plus précis que les méthodes de production classiques !
Une chose est sûre, l’année 2020 aura été riche, bouleversée par une crise sanitaire mondiale mais qui n’a pas empêché le marché de la fabrication additive à innover et rebondir. N’hésitez pas en tout cas à nous dire ce qui vous a marqué en 2020 dans les commentaires de l’article ou avec les membres du forum 3Dnatives. Retrouvez toutes nos vidéos sur notre chaîne YouTube et suivez-nous sur Facebook et Twitter.
*Crédits photo de couverture : Michal Kamaryt / CTK / Alamy
Très bel article.