Comment obtenir des pièces en ABS de qualité à grande échelle grâce à la fabrication additive ?
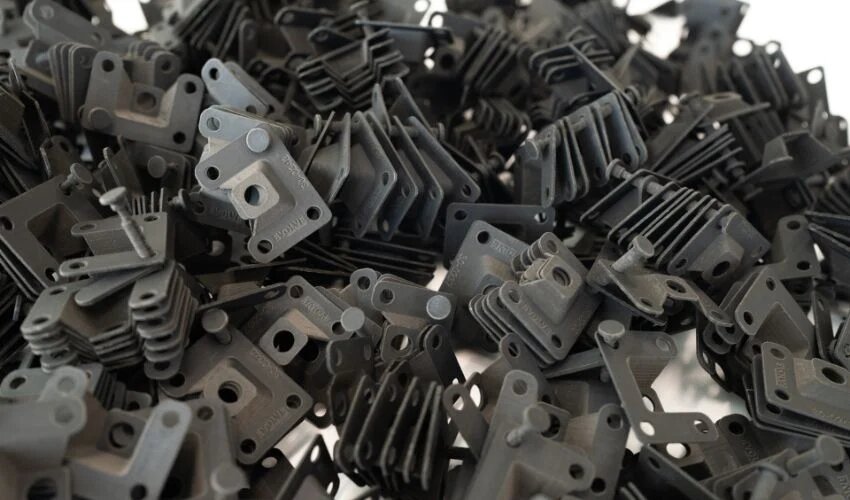
Selon un rapport de MarketsandMarkets, le marché de l’impression 3D polymères est en pleine croissance, avec une valeur calculée de 1,7 milliard de dollars en 2023 et une estimation de 4,4 milliards de dollars d’ici 2028. Parmi les thermoplastiques les plus utilisés dans l’industrie manufacturière figure l’ABS (Acrylonitrile Butadiène Styrène), connu pour sa résistance aux chocs, sa résistance aux basses températures et sa légèreté. Grâce à ces caractéristiques, il est utilisé dans de nombreuses applications : prototypes, pièces d’appareils électroménagers, intérieurs de voitures, engrenages, valves, outils, etc.
La méthode de production la plus utilisée pour les pièces en ABS en grande série est le moulage par injection, mais la fabrication additive est également utilisée pour le prototypage et les petites séries. Une des limites dans ce domaine est celle rencontrée par le segment des utilisateurs qui augmentent leur production et doivent donc passer rapidement du prototypage à la production en volume. La technologie STEP (Selective Thermoplastic Electrophotographic Process) d’Evolve Additive Solutions s’inscrit dans ce segment de marché, se présentant comme une alternative viable au moulage par injection pour la production de pièces ABS de qualité à grande échelle. Comment ? Approfondissons la question.
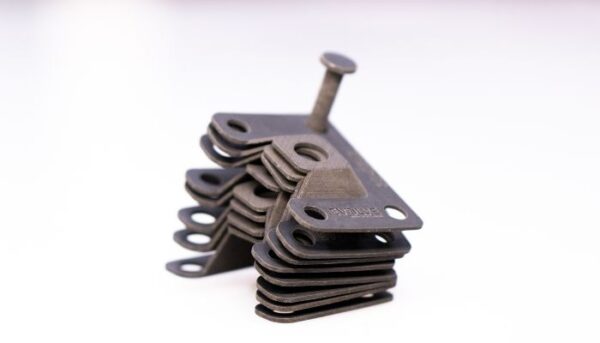
Jeu de crochets en ABS imprimés en 3D à l’aide de la technologie STEP
Comment fonctionne le procédé STEP ?
La technologie STEP d’Evolve fait partie de la famille des technologies additives, mais elle ne correspond exactement à aucun des processus actuellement décrits dans la norme internationale ISO/ASTM 52900:2021, qui décrit les processus de fabrication additive.
En fait, STEP implique la création de pièces couche par couche, mais le cœur de la technologie est basé sur l’impression numérique 2D à grande vitesse. Elle est structurée en trois étapes : la première est l’imagerie, au cours de laquelle des particules de la pièce et des matériaux de support sont déposées de manière sélective sur une bande mobile à l’aide de l’électrophotographie ; la deuxième est l’alignement, au cours de laquelle les images sont chauffées et transférées sur le plateau d’impression ; enfin, la fusion a lieu, c’est-à-dire que, sous l’effet de la chaleur et de la pression, les particules sont fusionnées à la couche du plateau, puis refroidies en dessous de la température de transition vitreuse. Des couches entièrement développées de la pièce et du matériau de support sont déposées l’une après l’autre, produisant ainsi la pièce en 3D. « Nous avons trouvé un moyen de microniser les thermoplastiques techniques pour qu’ils se comportent comme le toner d’une imprimante 2D« , explique John Lees, vice-président de l’ingénierie chez Evolve Additive.
Ce qui est intéressant avec STEP, et ce qui, selon Evolve, distingue cette technologie des autres procédés additifs, c’est qu’elle permet de produire des pièces entièrement denses. En effet, le rouleau presse l’image sur la couche d’impression en exerçant une pression qui, combinée à la chaleur, assure une adhérence optimale. La machine commercialisée par Evolve, la SVP™ (Scaled Volume Production), scanne également la couche à chaque passage pour identifier les éventuelles variations de hauteur, les compensant en ajustant le dépôt dans les couches suivantes. Selon Evolve, par rapport à d’autres procédés additifs, STEP permet ainsi d’obtenir des pièces d’une grande précision avec des propriétés mécaniques supérieures et évolutives.
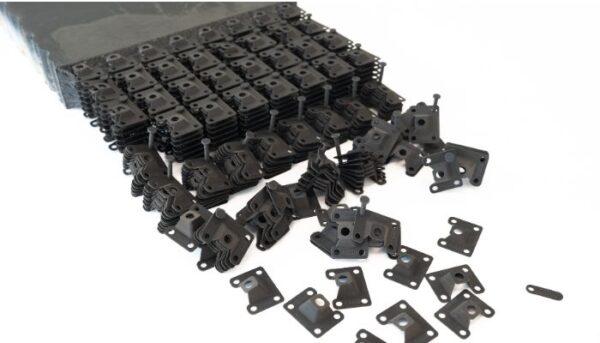
Un batch d’impression SVP comprend 92 jeux de crochets pour un total de 736 pièces, imprimées en 6 heures et 30 minutes
Production de pièces en ABS : comparaison entre STEP, d’autres technologies additives et le moulage par injection
Après avoir donné un aperçu de la technologie, entrons dans le vif du sujet : pourquoi cette technologie diffère-t-elle des autres processus de fabrication additive et pourrait-elle constituer une alternative viable au moulage par injection lorsqu’il s’agit de produire des pièces en ABS à grande échelle ? Tout d’abord, en ce qui concerne les matériaux, STEP utilise deux types d’ABS, l’un en noir et l’autre en gris clair. Le procédé fonctionne également avec un nylon PA11, qui offre une plus grande élongation et une température de ramollissement plus élevée.
En termes de vitesse d’impression, la technologie est plus rapide que, par exemple, les technologies additives de fusion sur lit de poudre. En effet, ces technologies nécessitent, à chaque impression, l’utilisation de la totalité du volume d’impression et donc des délais plus longs pour passer d’une production à l’autre, ce qui n’est pas nécessaire avec STEP. En fait, le processus peut être arrêté une fois que la pièce est prête et, une fois qu’elle est extraite, un nouveau processus peut être lancé immédiatement.
Si l’on considère la précision et le détail des pièces, l’épaisseur de la couche pour STEP est de 13 microns, avec des particules de 22μm permettant la production de pièces solides et de haute résolution ; la rugosité de la surface est de 3-6μm. Le moteur d’impression Kodak NexPress, que la technologie utilise, a une résolution de 600 points par pouce (DPI), ce qui équivaut à une taille de pixel de 40 microns. Comme il s’agit d’un procédé électrophotographique, il ne rencontre pas les mêmes défis thermiques que les autres procédés d’impression 3D, tels que les limites de densité de puissance. C’est pourquoi Evolve with STEP vise à surmonter les limites « historiques » de la fabrication additive et notamment la relation entre la vitesse d’impression et la résolution.
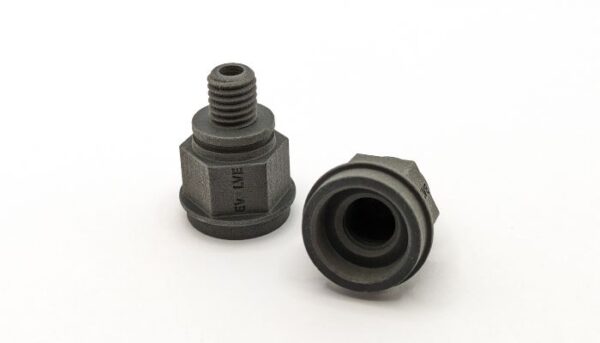
Une pièce en ABS entièrement dense peut répondre aux exigences de manipulation de l’air ou des fluides.
Par rapport au moulage par injection, le procédé STEP ne permet pas d’atteindre les mêmes volumes de production, mais il offre les mêmes propriétés mécaniques et la même qualité pour les pièces en ABS. Comme prévu, c’est un atout pour ce processus de fabrication additive, qui pourrait être une bonne solution pour les petites et moyennes entreprises (PME) désireuses de passer à l’échelle supérieure.
Compte tenu de la vitesse relative du STEP, la technologie peut effectivement servir de pont entre le prototypage et la production en série. En outre, en termes de coût, elle peut constituer une solution initiale pour les PME qui souhaitent passer à l’échelle supérieure mais n’ont pas les moyens d’investir dans une technologie de moulage par injection.
Impression 3D de pièces d’utilisation finale en ABS pour la production en série
Comme nous l’avons mentionné, les composants en ABS sont utilisés dans de nombreuses industries et applications. Il s’agit notamment des systèmes d’irrigation et des composants électriques. Ces deux secteurs, en plus de bénéficier des propriétés du matériau, ont en commun la nécessité de produire de petites pièces détaillées en petites séries. C’est pourquoi le moulage par injection n’est souvent pas le choix le plus judicieux, même si l’on tient compte du coût supplémentaire des moules.
Dans ce cas, la technologie STEP a permis, par exemple, de créer des vannes d’arrosage, des clapets anti-retour et des collecteurs d’essai de pression pour les systèmes d’irrigation. Dans ces cas, l’ABS est idéal car il est chimiquement résistant aux acides aqueux, aux alcalis et aux acides chlorhydrique et phosphorique concentrés. En outre, la technologie a permis d’obtenir les caractéristiques essentielles requises pour ces pièces, à savoir la densité, l’absence de vides et de problèmes de porosité.
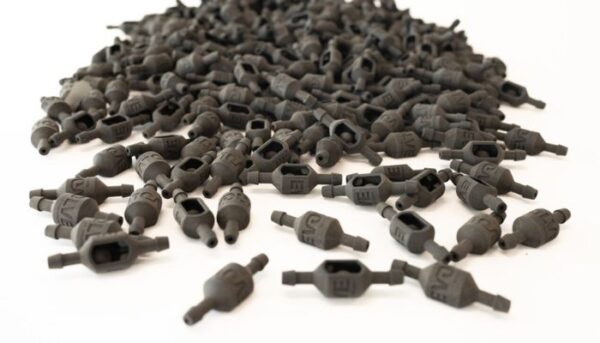
Clapets anti-retour avec une bille flottante à l’intérieur, fabriqués par le procédé STEP.
Un autre cas d’utilisation de la technologie STEP pour la fabrication de pièces d’utilisation finale en ABS est la production de boîtiers d’interconnexion électrique. Dans ce cas, l’utilisation de la technologie STEP s’est avérée utile en raison de sa capacité à combiner précision et rapidité, permettant à l’utilisateur final de créer 195 pièces en un peu moins de deux heures. Avec une rotation standard en trois équipes, cela représente une production de plus de 300 000 pièces par an.
L’utilisation de la technologie STEP pour ces applications, tant pour le prototypage que pour la production, a finalement permis aux utilisateurs de réduire les risques liés à l’utilisation de plusieurs processus de production. Découvrez la technologie STEP par vous-même en demandant un échantillon de pièce gratuit ICI.
Que pensez-vous de l’utilisation de la technologie STEP pour produire des pièces en ABS à grande échelle ? N’hésitez pas à partager votre avis dans les commentaires de l’article. Retrouvez toutes nos vidéos sur notre chaîne YouTube ou suivez-nous sur Facebook ou Twitter !
*Crédits de toutes les photos : Evolve Additive Solutions
Un article vraiment très intéressant !