Une imprimante 3D métal grand public et made in France – Strong Print
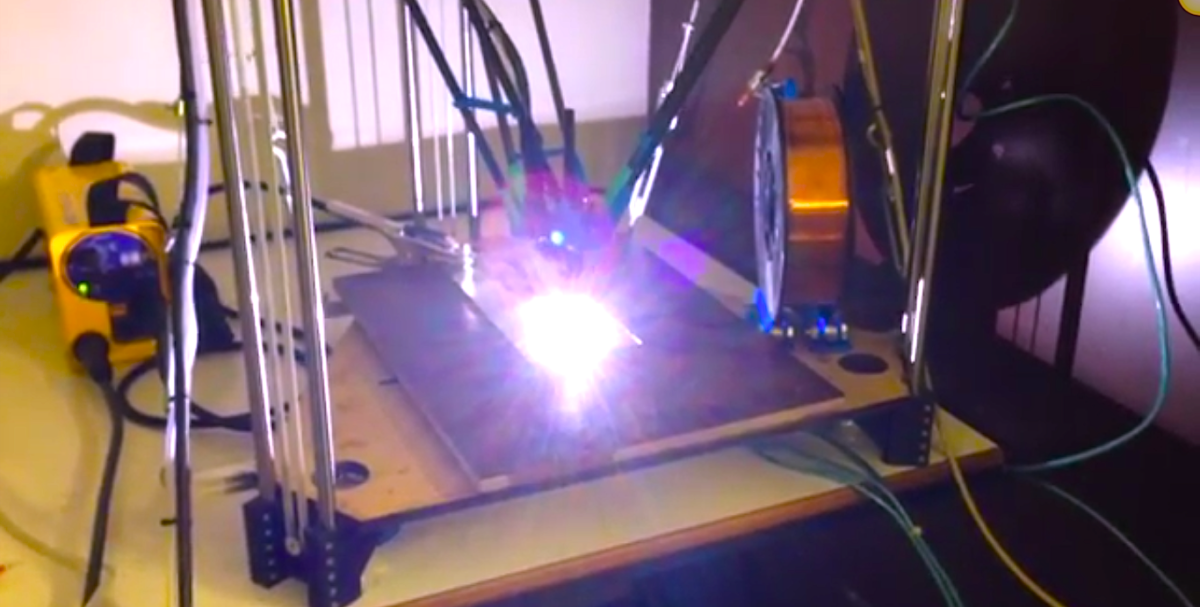
Certains aiment prédire qu’un jour l’impression 3D de pièces métalliques sera accessible au grand public. Mais Jean-Michel Rogero, habitant de la région Toulousaine, a préféré prendre les choses en main pour tenter d’atteindre ce but.

La Strong Print
C’est en voyant les articles sur l’imprimante 3D métal fabriquée pour moins de 1500€ par une équipe de chercheurs américains, qu’il se dit qu’il pourrait utiliser la structure de son imprimante Delta pour réaliser une machine similaire. Le projet des américains étant open-source, il récupère les plans en ligne pour étudier son fonctionnement. Le principe de la machine repose sur le dépôt d’un cordon métallique sur un plateau mobile en utilisant un poste de soudage à l’arc. Alors que les américains utilisent un poste de soudage MIG (Metal Inert Gas) qui leur permet d’atteindre une précision de 5mm, Jean-Michel Rogero s’oriente vers un poste de soudage TIG (Tungsten Inert Gas). Si ce dernier est plus lent, il permet en revanche d’atteindre une meilleure précision.
N’ayant pas de garage ou d’atelier pour mener à bien ses expériences, le maker installe sa machine au sein du Fablab toulousain Artilect qui lui offre l’espace nécessaire ainsi qu’un support technique et matériel. De plus, l’échange avec les autres membres lui permet de résoudre certains problèmes plus rapidement. La tête de soudage est placée à la place de la buse d’injection de son imprimante de pièces en plastique. Comme avec une imprimante 3D plastique, le câble est situé sur une bobine à coté de la machine. Cependant, deux éléments font leur apparition autour de la machine. Premièrement, le transformateur qui permet d’apporter l’énergie nécessaire pour créer l’arc électrique, mais aussi une bonbonne d’argon qui sert de gaz protecteur lors du soudage. Le déplacement des axes, le déroulement du fil métallique ainsi que le déclenchement du poste de soudage sont contrôlés par des cartes Arduino. L’objectif de Jean-Michel Rogero est d’atteindre des pièces ayant une précision de 1mm. Cela semble être bien parti puisqu’il arrivait déjà à fabriquer des épaisseurs de 2mm quelques jours après avoir monté la machine pour la première fois.

Détail de la tête d’impression
Si le coût de la machine, que son concepteur annonce inférieur à 1000€, la rend accessible à un certain grand public, il ne sera pas évident pour un particulier de l’installer chez soi. Au delà du problème d’espace adéquat pour accueillir la machine et son équipement, les risques sont beaucoup plus importants qu’avec une imprimante 3D plastique. L’échauffement du métal est très important (plus de 1000°C pour le faire fondre). L’argon n’est pas inflammable mais les vapeurs dégagées par le soudage sont nocives et il est indispensable de porter un masque spécifique pour ne pas s’endommager la vue en regardant l’arc de soudure. Si ces risques ne vous effraient pas, vous pouvez télécharger les plans de la machine sur le wiki du projet. Ceux-ci sont redistribués à la communauté selon le même modèle open-source qui a permis à Jean-Michel Rogero de fabriquer sa machine afin que d’autres puissent apporter leurs modifications à leur tour.
Pour ceux qui auront le courage de se lever suffisamment tôt, Jean-Michel Rogero présentera sa machine le samedi 17 mai à 5h du matin lors du marathon des créatifs de Futurapolis.
D’ici là vous pouvez toujours regarder la machine en action dans la vidéo ci dessous :
En septembre 2013, la société Vader Systems présentait une machine permettant de fabriquer des pièces de petite dimensions (250x250x250 mm) en projetant des gouttelettes de métal en fusion de l’ordre de 100 à 1000 microns. Cette machine, si elle venait à être commercialisée, devrait coûter autour de 10.000€ ce qui ne la rend pas totalement grand public bien que ce prix soit bien inférieur aux machines industrielles. Quelques mois après, la Newton 3D était présentée, une machine qui devrait permettre d’imprimer à partir d’une large palette de métaux : or, argent, bronze, cuivre ou acier et dont la commercialisation est annoncée courant 2014 à un prix encore inconnu.
Pour rester informé abonnez-vous à notre flux RSS ou pages Facebook et [follow id= »3Dnatives » ]