#Startup3D : LEAM améliore la densité des couches des pièces XXL imprimées en 3D
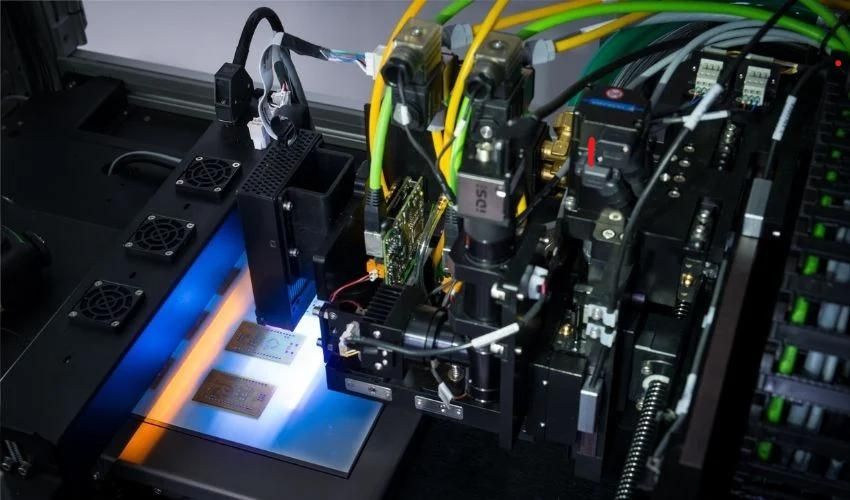
De la science à l’impression 3D et finalement à l’entreprise – tel a été le parcours de LEAM jusqu’à présent. La spin-off de l’université technique de Munich a en effet posé la première pierre de la technologie désormais commercialisable au sein de l’université. Avec son système DEMEX, LEAM emprunte de nouvelles voies dans le secteur de la fabrication additive, car l’entreprise n’utilise pas de laser pour faire fondre le matériau comme d’autres startups, mais un spectre lumineux continu. De cette manière, le matériau est chauffé juste avant la buse et la technologie assure également une meilleure adhérence entre les couches. Le système DEMEX développé par LEAM est disponible en tant que module complémentaire pour les imprimantes 3D grand format et la jeune entreprise a déjà pu enthousiasmer ses premiers clients. Nous nous sommes entretenus avec l’équipe de LEAM afin d’en savoir plus sur les étapes franchies par la startup, sur sa technologie et d’évoquer ses projets d’avenir.
3DN : Pourriez-vous vous présenter et nous dire comment vous avez découvert l’impression 3D ?
Nous sommes trois fondateurs (Patrick Consul, Ting Wang et Benno Böckl) et nous nous intéressons à l’impression 3D depuis nos études de génie mécanique ou depuis que nous avons commencé à travailler comme collaborateurs scientifiques à la chaire de composites de carbone (LCC) de l’université technique de Munich, où nous nous sommes rencontrés. Patrick avait déjà essayé, lors de son travail de master, de fabriquer des noyaux pour des structures dans l’aéronautique en PEEK par impression 3D. Mais cela n’était pas possible à l’époque, car les résistances nécessaires ne pouvaient pas être atteintes. Il a toutefois poursuivi ce thème à partir de 2017 en tant que collaborateur scientifique à la chaire de composites de carbone. Dans les années qui ont suivi, il a demandé et traité plusieurs projets de recherche dans lesquels il a continué à explorer le sujet.
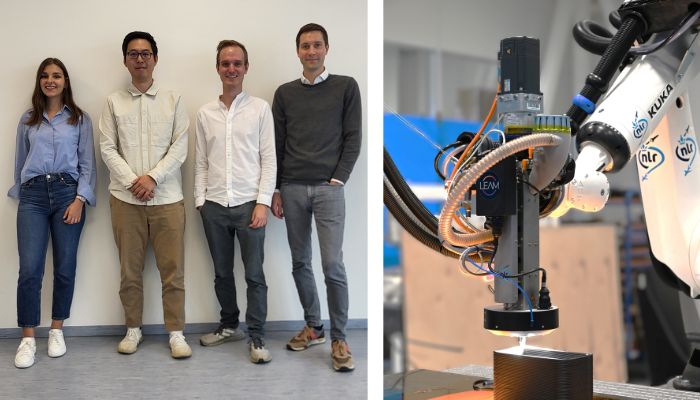
À gauche, l’équipe LEAM ; à droite, le système DEMEX
Ting Wang a travaillé sur un projet de recherche visant à étudier de manière ciblée le chauffage du substrat afin d’obtenir une meilleure liaison avec la couche suivante. Ting a donc déjà effectué les premiers travaux préparatoires concrets, sur lesquels se sont basés les développements ultérieurs du système DEMEX, lorsqu’il était collaborateur scientifique. Benno a également travaillé plusieurs années en tant que collaborateur scientifique à la chaire de composites de carbone, où il s’est intéressé au procédé de placement automatisé de fibres pour la fabrication de composants en carbone. Ce procédé présente certaines similitudes avec l’impression 3D. Nous sommes donc arrivés à l’impression 3D par la science, ce qui nous a permis de bien connaître les défis de ce procédé. Cela nous permet aujourd’hui d’élaborer des solutions qui ouvrent de nouvelles possibilités à l’impression 3D dans la fabrication de pièces.
3DN : Comment LEAM a-t-il été créé et quelles ont été ses principales étapes jusqu’à présent ?
Dans ses projets de recherche, Patrick a étudié les approches les plus diverses pour augmenter l’adhérence des couches et donc la résistance des composants dans l’impression 3D par extrusion. Il est apparu de plus en plus clairement que la seule approche vraiment prometteuse était de chauffer et de faire fondre ponctuellement la couche sous-jacente. Ting a étudié cette approche concrète dans le cadre d’un projet de recherche et a développé un premier prototype de notre futur système DEMEX, qui utilisait toutefois encore des lasers comme sources d’énergie. Cette approche a donné des résultats prometteurs, mais sa commercialisation était discutable, car les coûts et les dispositifs de protection nécessaires auraient rendu le produit non rentable. Nous avons alors eu l’idée d’utiliser des LED blanches à spectre large à la place des lasers. Celles-ci sont beaucoup plus sûres et moins chères que les lasers et, après que les premiers essais préliminaires ont montré que cela pouvait fonctionner, nous avons décidé de créer une entreprise qui proposerait le système comme produit.
L’obtention d’une subvention dans le cadre du transfert de recherche Exist a ensuite constitué une étape importante. Cela nous a permis de financer les 18 premiers mois et de mettre en place LEAM de manière à ce que nous puissions exister en tant qu’entreprise. L’année dernière, nous avons également reçu la promesse de l’ESA Business Incubation Centre Bavaria, qui soutient notre projet. Une autre étape importante a été la première preuve de concept avec un client, qui a non seulement montré que notre système fonctionne, mais aussi qu’il existe un grand potentiel de marché. Nous avons ensuite pu vendre et installer les premiers systèmes à des clients. Au milieu de l’année dernière, nous avons embauché notre première collaboratrice à temps plein, qui travaille chez nous en tant qu’ingénieure de développement, ce qui fait que nous sommes désormais également devenus un employeur. Enfin, nous avons pu déposer une demande de brevet pour notre technologie, ce qui est décisif pour le développement futur de l’entreprise.
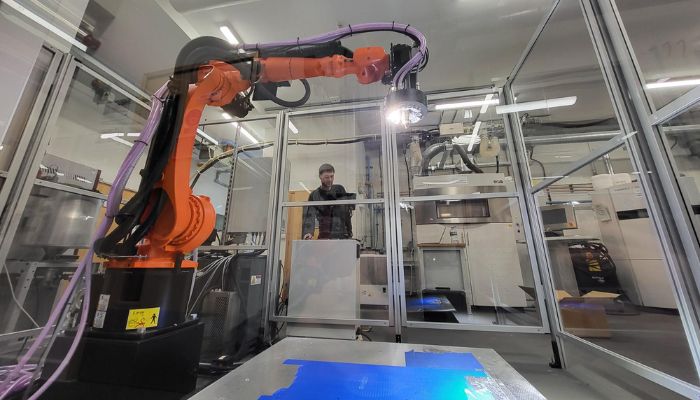
LEAM a déposé un brevet pour son système DEMEX.
3DN : Pourriez-vous présenter votre système DEMEX ? Quels sont ses avantages par rapport à d’autres procédés ?
Le système DEMEX est un composant complémentaire pour les imprimantes 3D grand format. Le système combine des émetteurs LED et des caméras infrarouges répartis autour de la buse de l’extrudeur. À l’aide des émetteurs LED, le système DEMEX peut chauffer le substrat de manière très ciblée et très localisée devant la buse, garantissant ainsi un soudage parfait des couches. L’atteinte de la température cible souhaitée est garantie par un circuit de régulation fermé avec les caméras infrarouges. Au lieu de la résistance z maximale de 60 % qui pouvait être atteinte jusqu’à présent, la pièce peut atteindre 100 % de la résistance indiquée dans la fiche technique du fabricant de matériaux – et ce dans toutes les directions ! De plus, il est possible d’utiliser des matériaux de qualité nettement plus avantageuse, comme par exemple des matériaux moulés par injection, qui étaient jusqu’à présent totalement inadaptés à l’impression 3D, car il était impossible d’obtenir une adhérence des couches. Le système DEMEX communique avec la commande de l’imprimante et sait donc toujours dans quelle direction l’imprimante se déplace actuellement et quelle zone doit être chauffée. Il n’est donc pas nécessaire d’en tenir compte lors de la création du G-code, ce qui ne perturbe pas les processus actuels d’utilisation de l’imprimante.
Notre technologie permet de résoudre les problèmes courants de l’impression 3D. Une approche souvent choisie dans l’impression 3D est celle des espaces d’impression chauffés. L’inconvénient est que la température ne peut pas être choisie à n’importe quelle hauteur, sinon la pièce devient instable et s’effondre. Ce problème n’existe pas avec notre système DEMEX, car nous ne chauffons qu’une couche très fine à la surface dans une zone très limitée devant la buse. Nous pouvons donc aller au-delà de la température de fusion du matériau, ce qui nous permet d’atteindre des résistances beaucoup plus élevées. Une autre approche consiste à utiliser des émetteurs infrarouges répartis dans l’espace d’impression ou installés localement sur la buse. Ces derniers présentent toutefois l’inconvénient d’avoir des temps de réaction très longs, de l’ordre d’une à trois secondes, ce qui rend les émetteurs infrarouges très difficiles à régler. En revanche, la puissance de notre système à base de LED peut être ajustée en quelques millisecondes et la densité de puissance obtenue est également plus élevée que celle des émetteurs infrarouges. Par rapport aux lasers, nos LED présentent en outre un avantage de prix très clair. D’une part, les sources d’énergie en elles-mêmes sont déjà 90 % moins chères qu’un système laser comparable. D’autre part, les dispositifs de protection nécessaires, qui peuvent coûter plus cher pour une imprimante 3D grand format que l’ensemble du système DEMEX que nous proposons, sont supprimés.
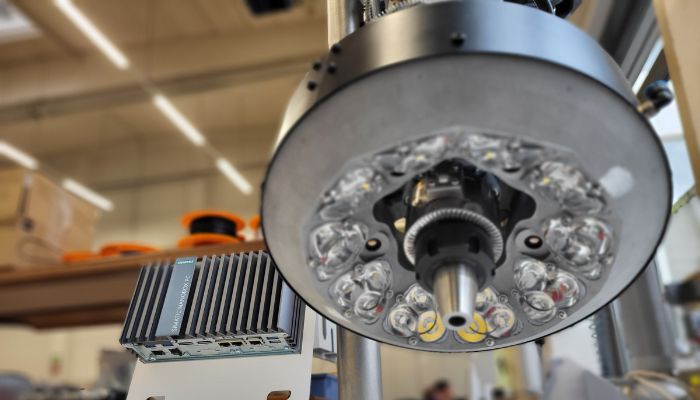
Avec DEMEX, LEAM utilise des LED et non des lasers. Les LED peuvent être adaptées rapidement et sont également moins chères que les lasers.
3DN : À qui s’adresse le système DEMEX et quelles sont les applications qui en profitent le plus ?
Les avantages du système DEMEX sont particulièrement évidents dans les applications qui utilisent des matières plastiques hautes performances ou des composants de très grande taille, par exemple dans l’industrie aérospatiale ou pétrolière. C’est là que les problèmes que nous résolvons ont le plus d’impact. Si nous considérons par exemple un grand composant qui s’interrompt pendant l’impression, la pièce est jusqu’à présent un rebut, avec des coûts qui peuvent se chiffrer en milliers. Avec l’aide de DEMEX, l’impression peut être facilement poursuivie après l’interruption, car la liaison avec la couche inférieure est assurée. Le système convient également à d’autres industries qui utilisent des plastiques techniques ou des plastiques renforcés par des fibres. En principe, tous ceux qui souhaitent imprimer des pièces soumises à des contraintes mécaniques pour lesquelles les résistances obtenues jusqu’à présent avec l’impression 3D ne suffisent pas en profitent. On peut penser ici par exemple à la construction navale, à la construction de véhicules ferroviaires ou encore à l’industrie automobile.
3DN : Quels ont été les projets de LEAM les plus passionnants jusqu’à présent ?
L’installation de nos deux premiers systèmes a certainement été particulièrement passionnante. Nous avons mis en place le premier DEMEX au NLR, l’équivalent néerlandais du Centre allemand pour l’aéronautique et l’aérospatiale (DLR). Peu après, nous avons pu mettre en service le deuxième système à l’université d’Exeter en Angleterre. Mais les projets actuellement en cours sont aussi très intéressants. De plus, il y a toujours de nouvelles demandes dans des secteurs auxquels on n’aurait jamais pensé. Par exemple, nous sommes actuellement en discussion avec des clients du secteur de la construction, mais il y a même des personnes intéressées par l’élevage de poissons, il n’y a donc vraiment pas de limites.
3DN : Un dernier mot pour nos lecteurs ?
La prochaine étape que nous voulons franchir avec notre système est de l’adapter à des imprimantes plus petites. Actuellement, nous ne pouvons utiliser que des imprimantes 3D grand format, car nous avons encore besoin d’un certain espace d’impression. Mais nous travaillons déjà à la réduction de la taille des différents composants et nous voulons être prêts, dans le courant de l’année, à équiper également des imprimantes à filament avec le système DEMEX. Nous avons reçu de nombreuses sollicitations dans ce sens, il y a donc une forte demande. De plus, nous allons déployer le passage à Siemens Industrial Edge dans les semaines à venir. Cela implique de nouveaux composants matériels et logiciels dans notre système, qui offrent de toutes nouvelles possibilités en termes de maintenance et de mises à jour du système, mais aussi de fiabilité.
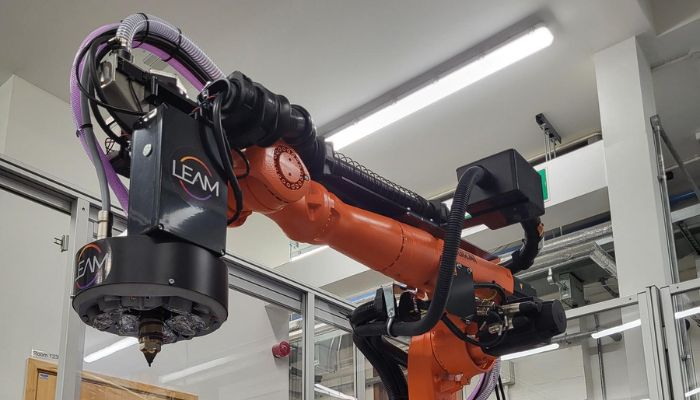
Actuellement, le système DEMEX n’est disponible que pour les imprimantes 3D grand format.
Que pensez-vous de la startup LEAM et de son système DEMEX ? N’hésitez pas à partager votre avis dans les commentaires de l’article. Retrouvez toutes nos vidéos sur notre chaîne YouTube ou suivez-nous sur Facebook ou LinkedIn !
*Crédits de toutes les photos : LEAM