#Startup3D : Azul 3D et son imprimante 3D résine grand format ultra-rapide
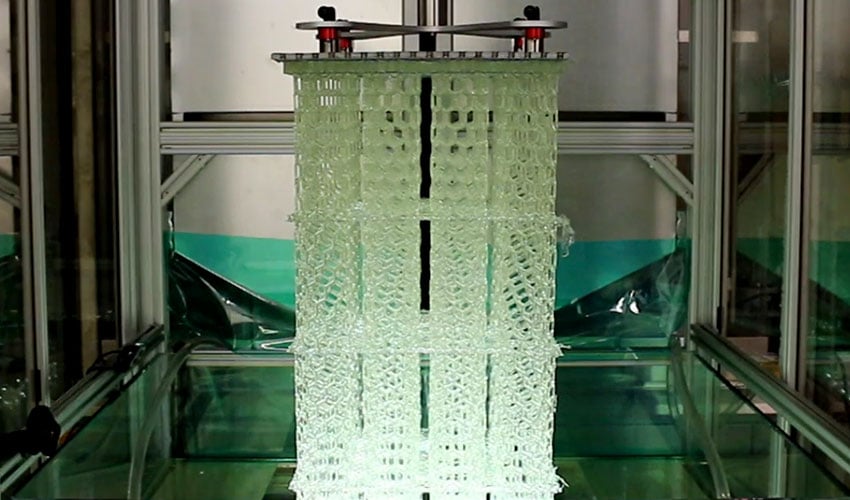
Les procédés d’impression 3D résine font aujourd’hui partie des plus utilisés sur le marché de la fabrication additive, offrant des détails très importants et une précision élevée. Un des défis auxquels ils restent toutefois confrontés est la taille du plateau de l’imprimante et la vitesse d’impression : celle-ci est assez lente et les machines ne permettent pas de concevoir de grandes pièces ou de produire en volume. Toutefois, certaines entreprises innovent et développent des méthodes pleines de promesses : c’est le cas de la startup américaine Azul 3D à l’origine du procédé HARP. Elle a développé une machine basée sur la photopolymérisation capable de créer des pièces de la taille d’un adulte en seulement 2 heures ! Nous avons voulu rencontrer l’équipe afin d’en savoir plus sur cette imprimante 3D inédite qui pourrait bien impacter le marché de l’impression 3D résine !
3DN : Pouvez-vous vous présenter et nous parler de votre lien avec l’impression 3D ?
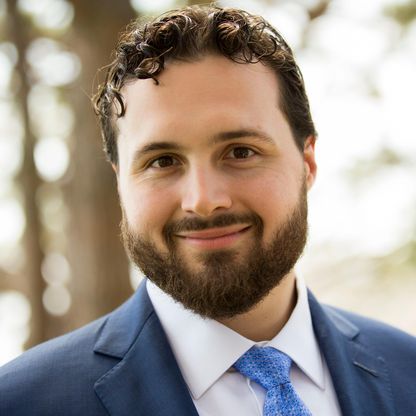
James Hendrick
Je suis le Dr James Hedrick, PDG et co-fondateur d’Azul 3D qui commercialise la première technologie d’impression 3D capable de rivaliser avec la vitesse, la résistance et les économies d’échelle du moulage par injection. J’ai créé ma première entreprise à l’âge de 16 ans. Les bénéfices ont permis de payer mes frais de scolarité au MIT, où j’étais également étudiant-athlète. J’ai ensuite obtenu mon doctorat à la Northwestern University avec le professeur Mirkin, au cours duquel j’ai fait partie de l’équipe qui a développé la technologie HARP, au cœur d’Azul 3D. Cette technologie HARP a été ma première approche de l’impression 3D qui a été appliquée pour la première fois à la nano-impression 3D. Nous sommes rapidement passés à la macro-impression 3D dans les mois qui ont suivi.
3DN : Comment l’idée de créer Azul 3D est-elle née ?
Je faisais mon doctorat sous la direction du professeur Chad Mirkin. Tout en travaillant le Dr David Walker, un post-doctorant au laboratoire, nous avons commencé à développer une nouvelle nano-imprimante 3D. Au début, nous avons fait une percée technologique, mais nous nous sommes rendus compte que nous pouvions imprimer de plus grandes structures en apportant quelques modifications à la technique, en plus de l’impression de structures minuscules. Nous avons immédiatement reconnu qu’avec HARP, nous avions la capacité de transformer la fabrication. Nous sommes passés de la nano à la macro impression et nous avons tous les trois fondé Azul 3D pour faire passer la technologie du laboratoire à l’usine.
3DN : Pouvez-vous nous expliquer comment fonctionne la technologie HARP et quelles sont les possibilités qu’elle offre ?
La technologie HARP s’appuie sur le procédé de stéréolithographie et de l’impression 3D résine liquide en général. L’innovation clé réside dans la modification de ce procédé, donnant lieu à HARP (High-Area Rapid Printing). C’est une méthode qui utilise une interface liquide fluide qui fait deux choses essentielles à la fois. Premièrement, le mouvement de l’interface permet une traction continue avec une vitesse d’impression verticale rapide. Deuxièmement, elle régule thermiquement la température de l’impression, ce qui est essentiel pour imprimer de grandes pièces à ces grandes vitesses.
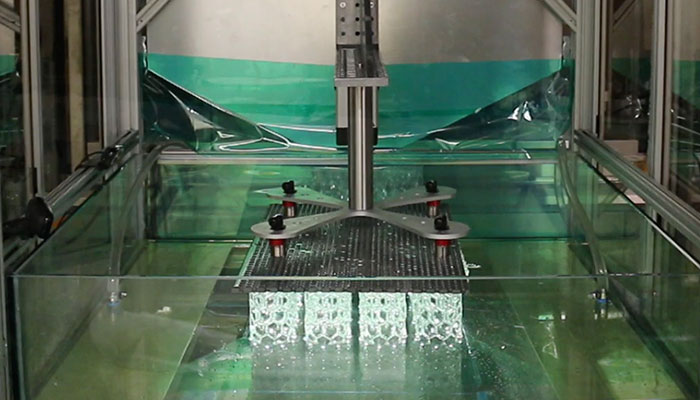
La machine d’Azul 3D
3DN : Quel(s) secteur(s) Azul 3D cible-t-elle ? Pouvez-vous nous citer certains de vos clients ?
Pour l’instant, nous ne citons pas nos clients, mais nous restons à l’écoute. Ce que je peux dire, c’est que nous travaillons avec des entreprises qui sont prêtes à utiliser l’impression 3D pour la fabrication de biens d’utilisation finale. Nous ciblons les secteurs qui n’ont pas un long processus réglementaire afin de permettre une fabrication plus rapide.
3ND : Selon vous, quelle est l’importance et les possibilités réelles de l’impression 3D à grande échelle aujourd’hui ?
L’impression 3D à grande échelle ne se limite pas qu’aux pièces géantes. Elle permet également d’imprimer en masse des pièces de taille moyenne. Par exemple, nous fabriquons des visières qui sont données aux travailleurs de la santé et aux premiers intervenants dans tout le pays. Avec notre plus petite imprimante, nous en avons produit en 250 heures d’impression. De plus, nous avons constaté que nos coûts de production étaient compétitifs par rapport aux visières fabriquées traditionnellement. Le rendement et cette économie réunis montrent les possibilités que l’avenir réserve à HARP.
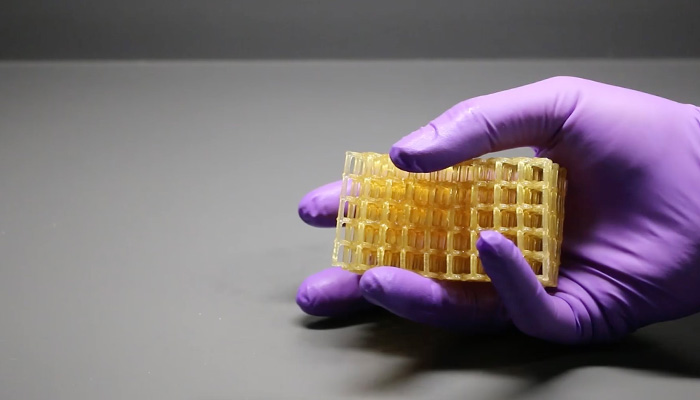
Une pièce conçue avec la technologie HARP
3DN : Où voyez-vous Azul 3D dans 5 ans ?
Au cours des 5 prochaines années, j’espère voir Azul 3D avancer encore plus loin dans la fabrication. En tant qu’entreprise, nous avons choisi de commencer petit et concentrés. Nous travaillons beaucoup avec chaque client pour nous assurer qu’il est capable de fabriquer avec notre imprimante dès le début. Cela nous permet de maximiser l’impact que chaque machine peut avoir. Cela nous empêche d’entrer dans tous les domaines que nous voulons dès le premier jour. Au fur et à mesure de notre croissance, cela ne sera plus une limite. Par ailleurs, je suis également enthousiaste de voir comment les logiciels de personnalisation évoluent. Nous avons produit des pièces sur mesure et nous constatons que la limite se situe au niveau de la conception, et non de l’impression. Dans 5 ans, je pense que la fabrication sur mesure sera devenue une réalité plutôt qu’un rêve.
3DN : Un dernier mot pour nos lecteurs ?
Si vous avez une application que vous souhaitez explorer avec l’impression 3D, n’hésitez pas à nous contacter ! Les clients sont aujourd’hui les mieux placés pour nos imprimantes, car ce sont eux qui connaissent le mieux le procédé et le produit.
Que pensez-vous de notre startup 3D ? N’hésitez pas à partager votre avis dans les commentaires de l’article ou avec les membres du forum 3Dnatives. Retrouvez toutes nos vidéos sur notre chaîne YouTube ou suivez-nous sur Facebook ou Twitter !