Soliquid développe un procédé d’impression 3D en suspension
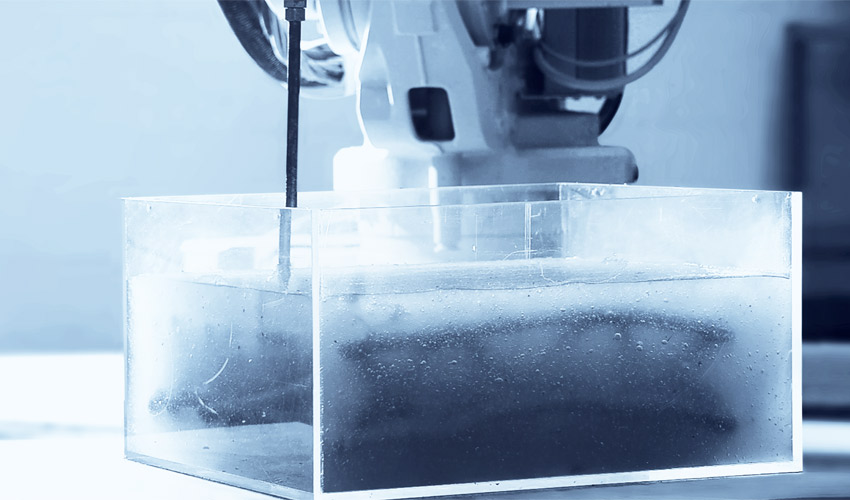
Soliquid est une startup française qui a développé une technologie d’impression 3D unique : au lieu de déposer le matériau couche par couche sur un plateau, elle vient l’extruder dans une matrice de gel durable et réutilisable à l’aide d’un robot à 6 axes. La jeune pousse propose ainsi un procédé plus rapide qui permet de concevoir des pièces complexes, tout en économisant de la matière : aucun support d’impression n’est nécessaire puisque c’est le gel qui maintient la pièce au fur et à mesure que le matériau est extrudé. Nous avons rencontré l’un des fondateurs, Jim Rhoné, afin d’en savoir plus sur la technologie, son fonctionnement, ses avantages et ses limites.
3DN : Pouvez-vous présenter Soliquid et son lien avec l’impression 3D ?
Lancée à Paris en 2018, Soliquid est une startup spécialisée dans le domaine de la fabrication additive et développe un procédé unique d’impression 3D grande échelle en suspension dans une matrice de gel réutilisable et durable. À l’initiative d’Amaury Thomas et moi-même, tous deux architectes de formation spécialisés dans le design computationnel et la fabrication robotisée, et fondée avec Impulse Group, Soliquid a été créée avec pour objectif d’élargir le champ des possibles de l’impression 3D en proposant des logiques innovantes de production d’éléments non-standard, sur-mesure, complexes et sans support pour de multiples industries.
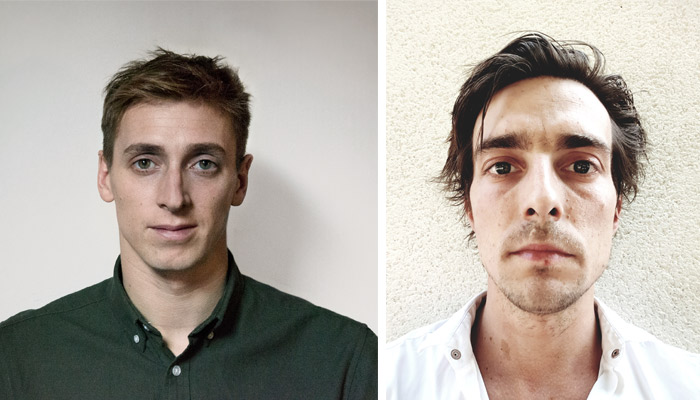
Les fondateurs de Soliquid : Jim Rhoné (à gauche) et Amaury Thomas
Notre activité intègre aujourd’hui le développement de la technologie mais également celui du logiciel associé, notamment sur les questions de design génératif, de conception 3D paramétrique et d’optimisation ; en parallèle de l’expérimentation de matériaux innovants.
3DN : Pouvez-vous nous expliquer le fonctionnement de votre technologie en suspension ?
Notre technologie d’impression 3D grande échelle en suspension, dont le brevet a été déposé, diffère de l’impression 3D « couche par couche » en ceci que la matériau d’impression est déposé dans une matrice de gel plutôt que sur le cordon d’impression antérieur. Le dispositif général est constitué d’un bac d’impression dans lequel se trouve la matrice de gel et d’un robot industriel à 6 axes, à l’extrémité duquel est fixée la tête d’impression que nous développons. Cet ensemble constitué du robot et de son « end-effector » est directement contrôlé par ordinateur.
C’est en effet depuis ce dernier que la phase d’impression est préparée puis initiée : le modèle 3D de l’élément à imprimer est d’abord analysé, adapté si besoin, puis converti en courbes 3D correspondant au futur « parcours outils » du robot pendant l’impression. Ce parcours est ensuite décomposé en une succession de plans dans l’espace XYZ et auxquels sont associés certains paramètres qui définissent les spécifications du mouvement et des processus de l’impression. Les logiciels que nous utilisons permettent enfin de convertir ces données en langage RAPID, utilisé pour contrôler le robot. L’ensemble des caractéristiques de l’impression comme le parcours outils, les vitesses de déplacement du robot, mais aussi le démarrage/arrêt (« start & stop ») de l’impression et les variations de son débit sont donc programmables.
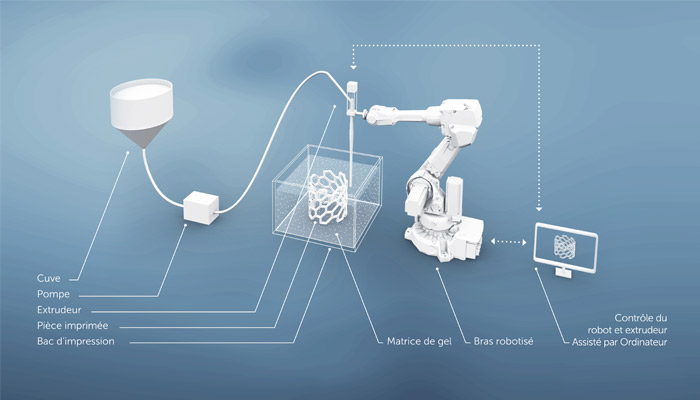
Le procédé d’impression 3D de Soliquid
En parallèle, une pompe permet d’acheminer le matériau d’impression depuis la cuve de stockage et malaxage jusqu’à la tête d’impression. Lorsque l’impression est lancée, la tête d’impression alimentée par la pompe plonge dans la cuve d’impression et dépose le matériau en suivant le parcours outils préalablement déterminé. C’est alors que toute la spécificité de notre technologie intervient : plutôt que de couler, le matériau d’impression est maintenu en suspension dans la matrice, principalement grâce à la combinaison de la force de résistance visqueuse et de la poussée d’Archimède générées, et donc d’un savant équilibre entre viscosité et densité des matériaux utilisés.
Au terme de la phase d’impression, l’élément est maintenu en suspension dans la matrice, assurant ainsi le rôle de coffrage/moule/support adaptatif, jusqu’à ce que sa solidification, ou durcissement, soit suffisante pour permettre son extraction du bac. Une fois l’extraction de la pièce réalisée, une nouvelle impression peut être amorcée dans le même bac ; la stabilité et la durabilité de la matrice d’impression permettant de répéter le processus à de nombreuses reprises et sur de longues durées avec un même volume initial.
3DN : Quels matériaux utilisez-vous ?
Au démarrage de l’aventure Soliquid, les premières démonstrations de notre procédé à petite échelle se faisaient avec de la résine de scellement bi-composant. C’est au moment d’engager la phase de R&D destinée à passer à une échelle supérieure que nous avons choisi d’utiliser un matériau très répandu dans le secteur de la construction, le béton. Plus précisément, nous utilisons des BHP, BTHP et BFUP, dont les performances en compression, traction et flexions permettent de réaliser les structures filaires, résilles et maillages 3D caractéristiques de notre procédé, tout en conservant un comportement structurel satisfaisant.
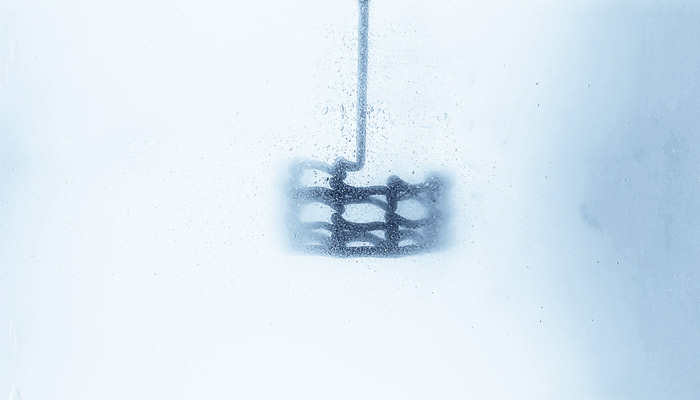
Le robot vient extruder du béton (crédits photo : Soliquid)
Au cours de cette première phase de R&D, nous avons fait tout un travail de caractérisation de matériaux compatibles avec notre technologie, travail qui a pris la forme d’un cahier des charges de propriétés et spécifications. La principale contrainte reste la capacité du matériau imprimé à exister en phase liquide, pour la phase d’impression, et à pouvoir solidifier en milieu anaérobie par réaction interne, amorcée sans apport extérieur d’énergie. Ce dernier permet donc la mise en œuvre de nombreux produits aux propriétés extrêmement variées comme les bétons résineux, le silicone, les résines mono composant ou bi-composant, ou encore certains mastics, polymères et composites, dont l’utilisation est déjà industrialisée dans de nombreux secteurs. Le matériau injecté étant maintenu en suspension jusqu’à son durcissement, ce procédé d’impression permet également l’utilisation de plusieurs matériaux pour un même élément, avec la possibilité d’imprimer directement en multi-matériaux ou d’imprimer successivement avec des matériaux de nature différente. On privilégie l’utilisation de composants biosourcés ou issus de processus de recyclage et de réemploi.
3DN : Quels sont les secteurs que cible Soliquid ?
La création de Soliquid avait pour objectif initial de révolutionner la préfabrication dans le secteur de l’AEC (Architecture, Ingénierie et Construction) et du Design, en proposant un nouveau mode de production industriel d’éléments constructifs, complexes et sur-mesure, plus légers et performants, sans l’utilisation de moule ni de support. Avec ce procédé, une grande variété d’applications peut en effet être imaginée et commence d’ailleurs à voir le jour, allant de l’optimisation de systèmes structurels (dalles, poteaux, poutres, modules de construction…), à la fabrication d’éléments architecturaux non-standards (panneaux de façade…), à la production de gammes de mobilier innovantes. Conscients de la longue temporalité de ce type de processus, principalement liée à des aspects normatifs et à des questions de certification et de règlementation, nous avons également fait le choix de cibler d’autres secteurs.
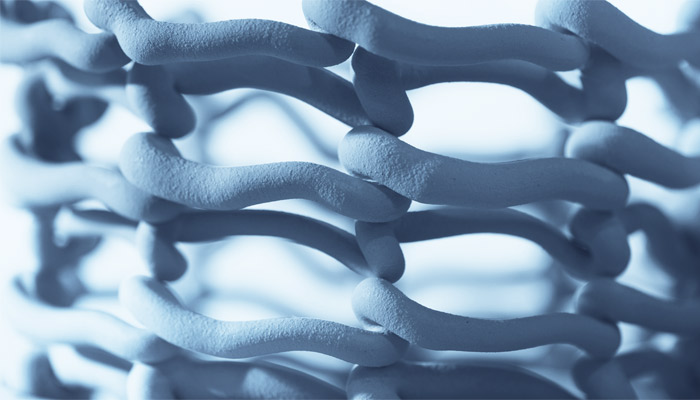
La technologie développée trouve des applications concrètes dans le secteur de l’architecture (crédits photo : Soliquid)
Parmi eux, le domaine de l’industrie écologique et plus précisément la production de solutions de génie écologique est en phase de devenir un de nos marchés privilégiés. En effet, face aux nouveaux enjeux auxquels sont confrontées nos sociétés, l’association de l’ingénierie et de l’écologie contribue à la résilience d’écosystèmes fragilisés et au développement durable par la conception, l’application et la gestion de processus, produits et services permettant d’empêcher, limiter ou réparer les dégradations subies par l’environnement. Depuis plusieurs années, des projets intègrent ainsi le génie écologique à l’écoconception d’aménagements maritimes sous la forme de récifs artificiels ou de modules d’habillage. Ces dispositifs, censés créer des habitats artificiels aux poissons et crustacés et stimuler le développement de la biomasse sont issus d’une logique biomimétique et donc souvent compliqués à réaliser. La logique d’impression 3D Soliquid, en permettant la production d’éléments aux géométries complexes et organiques (maillage tridimensionnel, arborescence, pontage, cavités…), se prête donc extrêmement bien à l’impression d’éléments dont la morphologie est proche de celle des récifs sous-marins naturels, de type corallien par exemple.
Enfin, le secteur médical fait également partie des domaines d’applications envisagés, notamment pour la réalisation de dispositifs sur-mesure, de prothèses et orthèses adaptées à l’utilisateur, ultra légères, résistantes et imprimées en un temps extrêmement court.
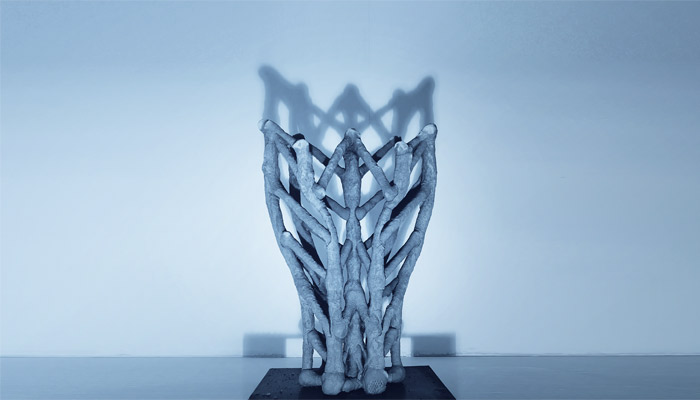
Crédits photo : Soliquid
3DN : Quels sont les avantages de votre technologie ? Quels défis avez-vous rencontrés ?
De nombreux acteurs des filières Construction et Bâtiment tentent aujourd’hui d’adopter les technologies de fabrication additive comme stratégie de production. À ce jour, ces dernières jouent pourtant un rôle très limité dans les processus industriels, et ce pour quatre principales raisons : temps de production, scalabilité du dispositif, limitations matérielle et formelle. Avec un concept unique, le procédé que nous développons répond aux défis soulevés par les techniques de fabrication additive existantes avec trois différenciations majeures : la rapidité d’impression, la liberté morphologique et l’économie de matière. En effet, en utilisant une matrice de gel pour maintenir le matériau imprimé en suspension, notre stratégie d’impression ne nécessite pas de matériaux de support, ni de coffrage. Le matériau peut ainsi être injecté en continu sans nécessiter sa solidification progressive au cours de l’impression, rendant le processus d’impression extrêmement rapide.
Compte tenu de sa logique, le procédé d’impression Soliquid relève plus des techniques d’injection ou d’extrusion que de l’impression 3D par dépôt de matière ou « couche par couche ». Cette caractéristique permet d’envisager des parcours outils extrêmement libres en termes de direction et d’orientation de l’extrudeur dans l’espace 3D et de profiter pleinement des degrés de liberté offerts par le robot industriel 6-axes. Grâce aux outils d’optimisation topologique que nous utilisons, l’impression d’un élément peut ainsi être programmée de manière à être optimisée en trois dimensions et à différents niveaux : réduction de la quantité de matière, réduction des émissions carbone et performance structurelle. Ce principe de suspension permet également d’envisager de nouvelles logiques d’impression, difficiles à mettre en œuvre avec les procédés d’impression 3D classiques : des pièces peuvent par exemple être imprimées selon des principes d’intrication (ex : les unes dans les autres, maillons de chaînes reliés les uns aux autres…).
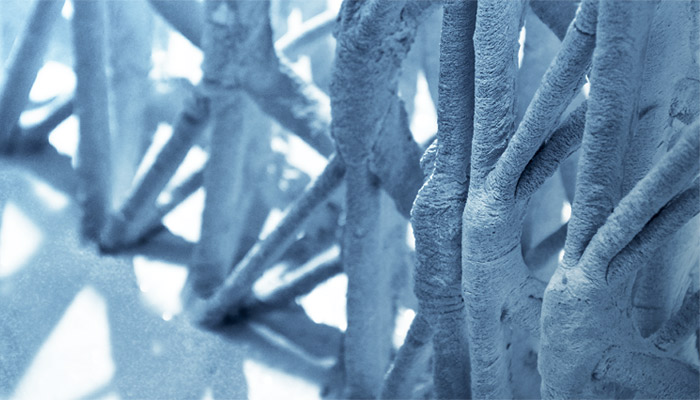
La technologie permet de créer des formes selon des formes d’intrication (crédits photo : Soliquid)
Enfin, la stabilité et durabilité de la matrice d’impression contribuent à la réduction de la quantité de matière globale de notre procédé. En plus de son caractère non nocif pour l’environnement, la réusabilité de la matrice faisait partie des critères essentiels pour le bon développement de notre technologie. Après l’extraction de chaque pièce imprimée, un premier nettoyage permet de récupérer l’essentiel du gel afin de limiter les pertes et de pouvoir procéder à d’autres impressions avec le même volume initial. Un second lavage élimine ensuite toute trace de gel sur la pièce imprimée, principalement pour des questions esthétiques, de finition et de manipulation.
D’un point de vue technologique, les principaux défis rencontrés pendant cette première année de développement ont principalement été liés à des questions de scalabilité de la technologie, d’utilisation de nouveaux matériaux aux densités bien supérieures aux résines utilisées initialement. Cette phase de validation étant maintenant achevée, c’est la conquête de nouvelles applications et de nouveaux marchés qui reste le défi majeur, avec un procédé aussi disruptif.
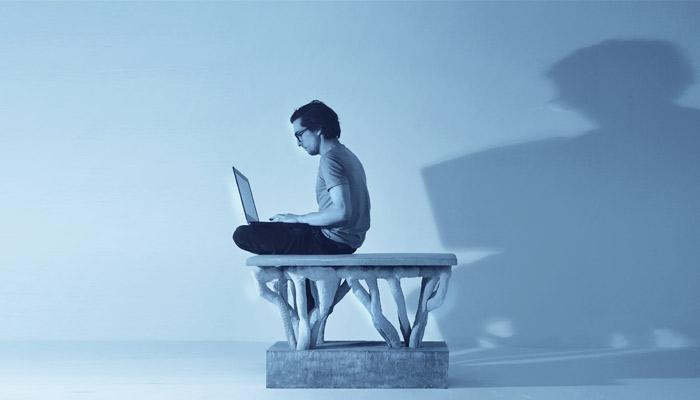
Crédits photo : Soliquid
3DN : Un dernier pour nos lecteurs ?
Soliquid reste une jeune startup dynamique et en pleine expansion, au sein de laquelle les possibilités de recherche et de développement dans les domaines du hardware, du software et de l’ingénierie des matériaux sont sans limite. Nous avons pour ambition la conception de technologies matérielles et de solutions logicielles d’impression 3D toujours plus performantes et restons convaincus que le procédé unique que nous développons saura émerger et participer, aux côtés d’autres dispositifs complémentaires, à la création de nouvelles stratégies de production dans de nombreuses industries. Si vous êtes intéressés pour faire partie de notre aventure ou pensez que des synergies intéressantes peuvent être mises en place entre votre activité et la nôtre, n’hésitez pas à nous contacter.
Que pensez-vous du procédé développé par Soliquid ? Partagez votre avis dans les commentaires de l’article ou avec les membres du forum 3Dnatives.