Schneider Electric accélère le prototypage industriel avec l’impression 3D
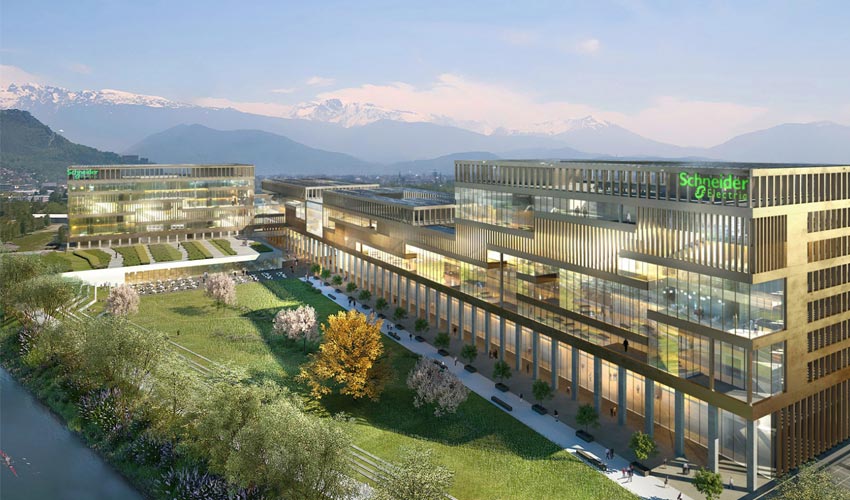
Le groupe industriel français Schneider Electric s’est tourné vers les solutions de fabrication additive du fabricant français Prodways et l’expertise de Platinium 3D afin d’accélérer son cycle de développement de produits industriels. Il a ainsi imprimé en 3D plusieurs empreintes de moule d’injection plastique, lui permettant d’injecter des centaines de pièces. Un gain de temps important pour l’industriel français qui confirme son intérêt pour les technologies 3D et accélère leur intégration dans la chaîne logistique.
Les entreprises françaises sont de plus en plus nombreuses à intégrer la fabrication additive dans leur cycle de production; on pense au groupe aéronautique Latécoère qui a adopté la technologie de Stratasys pour créer prototypes, outils et pièces finies. L’impression 3D permet en effet de réduire les temps de certification pour ces groupes industriels : en produisant plus rapidement leurs prototypes aux normes industrielles, ils peuvent alors tester leurs nouveaux produits facilement. Cette fois-ci c’est le géant Schneider Electric qui a recours à l’impression 3D pour créer des outils, notamment pour accélérer le processus de mise sur le marché de nouveaux produits, recourir à l’outillage classique étant une méthode plus lente.
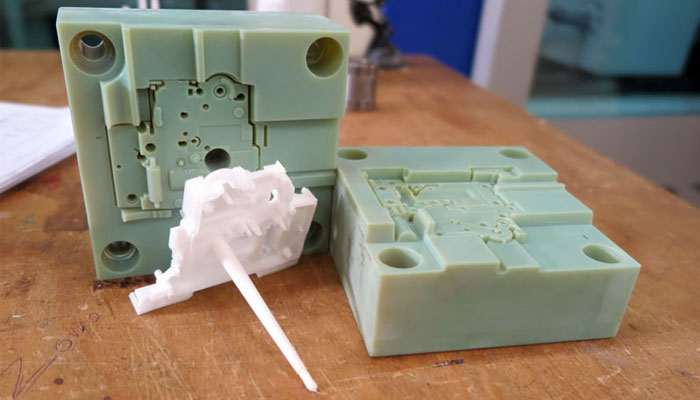
Les premiers moules imprimés en 3D à l’Openlab sur des machines Stratasys
Des moules d’outillage imprimés en 3D
Schneider Electric possède une unité de prototypage à Grenoble, baptisée Openlab : tournée vers l’innovation, elle accompagne les projets de développement de nouvelles offres. Son directeur, Frédérick Choupin, explique : « Notre objectif est de réduire le cycle de développement des produits via des technologies de pointe. Avec l’impression 3D et une gestion agile des projets, nous sommes capables de nous affranchir des barrières traditionnelles des processus classiques et d’accélérer la mise à disposition d’un produit innovant sur le marché, de 60%.«
C’est donc avec cet objectif en tête que Schneider Electric a travaillé avec le fabricant français Prodways et la plateforme Platinium 3D pendant un an. Grâce à la technologie MOVINGLight de Prodways, le groupe industriel affirme avoir créé près de 25 moules d’outillage imprimés en 3D. Cette technologie combine une source de lumière à base de LED à forte puissance et des puces micro-électroniques (DLP) afin de solidifier couche par couche une résine liquide. Avec ces moules imprimés en 3D, Schneider Electric explique qu’il a pu injecter des centaines de pièces en polyamide chargées et ininflammables, conformes à la géométrie finale souhaitée et surtout aux normes de certification de l’industrie.
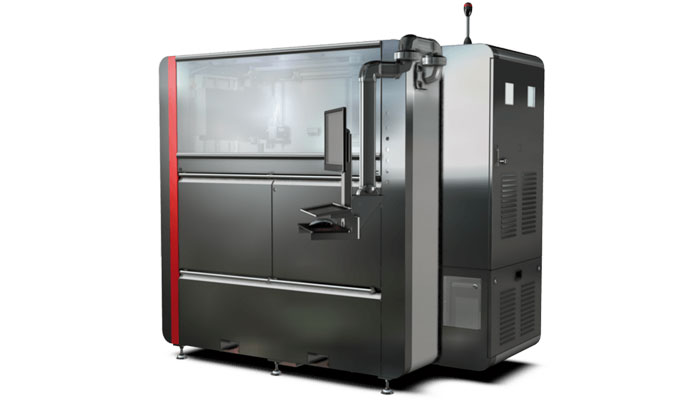
Une des imprimantes 3D de Prodways, basée sur la technologie MOVINGLight
Le Directeur Général chez UIMM Pôle Formation Champagne-Ardenne, Sébastien Guenet, poursuit : « Habituellement, produire un moule en aluminium pour les prototypes d’outillage des pièces qui doivent passer en certification en bonne matière demandent un délai de plusieurs semaines voire jusqu’à 2 mois d’attente, ce qui ralentit considérablement le cycle de développement. Avec l’impression 3D, nous pouvons produire les prototypes des outillages en quelques heures, les modifier immédiatement selon les besoins des tests fonctionnels et y injecter des pièces en bonne matière. Ces pièces bonnes matières sont envoyées directement en certification pendant que le moule aluminium est encore en cours de production. Grâce à ce procédé, nous accélérons considérablement le cycle de développement des nouveaux produits puisque les pièces bonne matière sont déjà certifiées avant même que le moule série en aluminium soit finalisé. » Retrouvez plus d’informations sur le site officiel de Prodways.
Que pensez-vous de l’utilisation de la fabrication additive chez Schneider Electric? Partagez votre avis dans les commentaires de l’article ou avec les membres du forum 3Dnatives.