Scawo3D libère l’architecture grâce à l’impression de béton par jet de matière
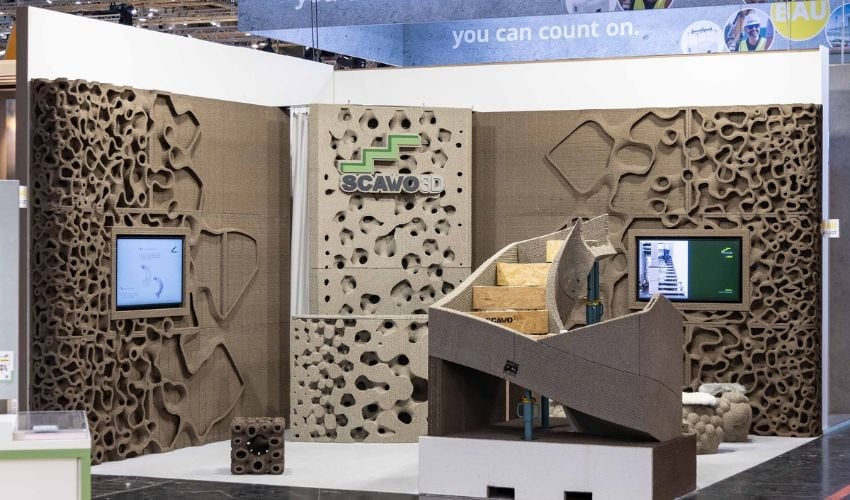
Si vous suivez l’actualité de la fabrication additive, alors vous savez à quel point elle est utilisée dans le secteur de la construction et de l’architecture, notamment pour construire les maisons de demain. Le plus souvent, c’est l’impression 3D par extrusion qui est employée, avec d’impressionnants bras robotisés permettant d’atteindre des distances et volumes importants. L’entreprise Scawo3D adopte toutefois une approche différente. Avec sa technologie « Selective Paste Intrusion », la société italienne a trouvé un moyen de produire des éléments en béton sur la base d’un lit de poudre. L’entreprise produit un béton isotrope à haute résistance, qui résiste également aux intempéries. Avec cette technologie, l’imagination n’a pas de limites et même des géométries complexes peuvent être réalisées à des coûts de production raisonnables. Nous nous sommes entretenus avec Philip Schneider de Scawo3D pour en savoir plus sur l’approche innovante de l’entreprise.
3DN : Pouvez-vous vous présenter ainsi que votre rôle chez Scawo3D ?
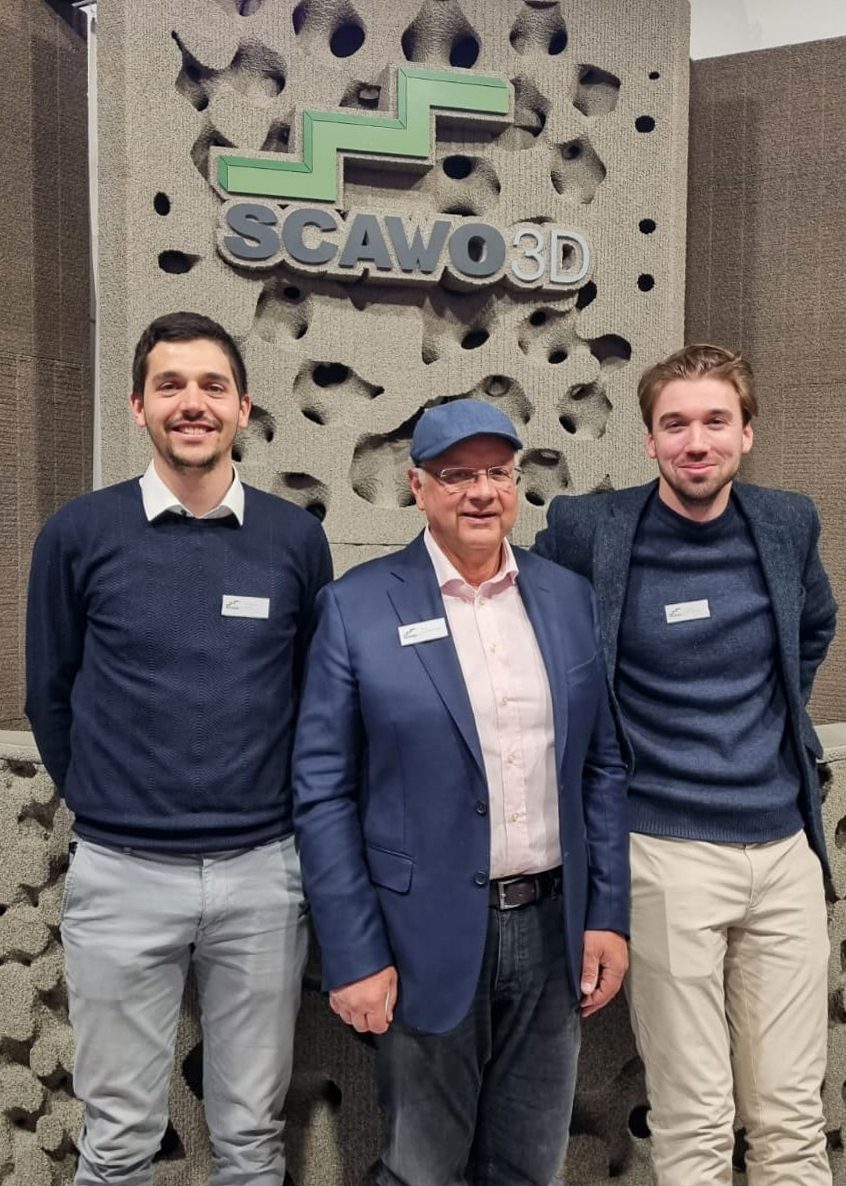
De gauche à droite : Andreas Spiess (programmation de machines), Kurt Wohlgemuth (fondateur) et Philip Schneider (architecture et conception informatique)
Bonjour, je m’appelle Philip Schneider, j’ai étudié l’architecture avec un accent sur la conception computationnelle et la fabrication numérique à l’Université technique de Munich. J’ai découvert l’impression 3D béton et Scawo3D au début de l’année 2022 grâce à la conception d’un pont piétonnier imprimé en 3D pendant mes études, qui a finalement été réalisé avec Scawo3D.
Scawo3D est l’inventeur de la première tête d’impression au monde compatible avec un béton sous forme de pâte, dans le cadre d’un nouveau procédé d’impression 3D béton appelé Selective Paste Intrusion (SPI). Nous sommes le développeur et l’unique fabricant de cette tête d’impression, ainsi qu’un fournisseur de services dans le domaine de l’impression 3D béton. Nous développons et optimisons constamment le processus afin de fournir à nos clients les meilleures machines possibles et de rendre notre service plus accessible en termes de prix.
Au sein de l’entreprise, je suis responsable de l’architecture et de la conception computationnelle, c’est-à-dire que je m’occupe des applications potentielles du processus SPI pour l’industrie de la construction. Comme notre procédé permet de réaliser les géométries les plus complexes en béton, les logiciels utilisés pour la modélisation et la planification sont de plus en plus sollicités. Il m’incombe également de veiller à ce que nous soyons équipés de logiciels permettant de modéliser des géométries complexes et à ce que nous développions nos propres solutions pour certaines applications. Par exemple, nous travaillons actuellement avec les entreprises Skeno GbR et Timo Harboe ApS sur un plugin basé sur Rhinoceros et Grasshopper pour la planification d’escaliers complexes de forme libre.
3DN : Pourquoi avez-vous décidé de mettre en œuvre l’impression 3D ?
À l’origine, Scawo était un procédé que nous avions breveté pour la production de coffrages fraisés par ordinateur en polystyrène expansé (EPS) pour les escaliers en béton armé. Toutefois, après un certain temps, la classe de protection incendie inadéquate de l’EPS a empêché son utilisation à plus grande échelle dans le secteur de la construction. L’entreprise a donc décidé de mettre au point un procédé d’impression 3D permettant de produire du béton présentant l’indice de protection incendie le plus élevé. À partir de là, le projet a été baptisé Scawo3D.
Au cours de la dernière décennie, le procédé SCA (Selective Cement Activation) a été développé pour la première fois, dans lequel un lit de poudre de mortier sec est activé de manière sélective. Cependant, seules des propriétés matérielles insuffisantes pour des pièces porteuses ont pu être obtenues. Finalement, après de nouveaux développements, nous sommes parvenus au procédé SPI, avec lequel nous avons commencé la production à la mi-2022. Au cours du développement, le coffrage d’escalier est resté l’objet d’essai. L’idée était que les escaliers combinent à la fois des géométries complexes et des exigences statiques. Une fois que l’escalier a fonctionné, nous avons pensé que le procédé pourrait également être utilisé pour d’autres objets. Heureusement, nous pouvons aujourd’hui affirmer que ce raisonnement était juste.
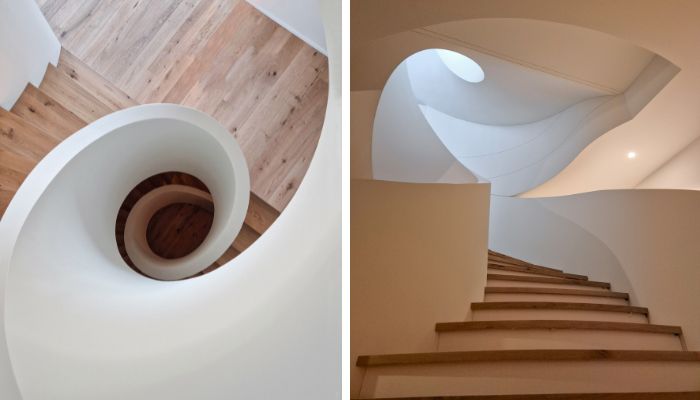
Un projet d’escalier terminé, réalisé par impression 3D (crédits photo : Tschanen/André Wäspi).
3DN : Pouvez-vous nous expliquer plus en détail votre procédé SPI ?
SPI est un nouveau procédé d’impression 3D béton. Il diffère de l’impression 3D par extrusion déjà connue, qui est souvent utilisée directement sur le chantier de construction. Notre système est stationnaire et basé sur un lit de poudre. Le principe fonctionne de la même manière que d’autres procédés à lit de poudre, comme le procédé SLS. La seule différence est que notre lit de poudre est rempli d’agrégats et que le béton ou le mortier est imprimé.
Pendant le processus d’impression, le lit de poudre est rempli couche par couche. Les agrégats en vrac et la pâte de ciment sont appliqués alternativement sur chaque couche. La pâte de béton, composée de ciment, d’eau et de superplastifiant, est appliquée de manière sélective par notre tête d’impression dotée de plusieurs centaines de buses et lie localement les agrégats. Une nouvelle couche de granulats libres est ensuite appliquée et le processus est répété jusqu’à ce que l’impression soit terminée. Pendant tout le processus d’impression et de durcissement, le grain libre sert de coffrage pour les pièces imprimées. Cela nous permet d’imprimer n’importe quelle géométrie sans restrictions dues à des angles de surplomb ou à des cavités.
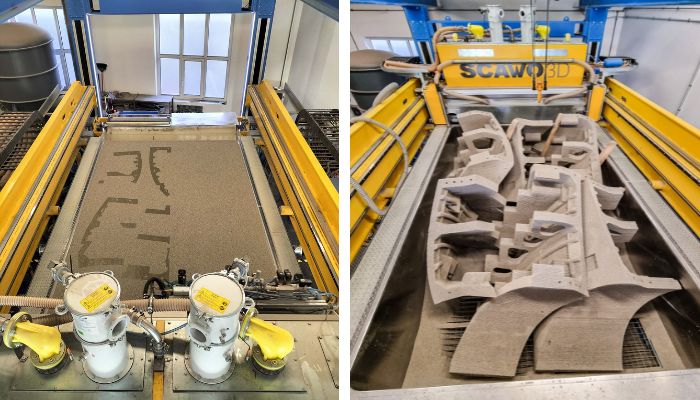
À gauche : le plateau de 4 x 2,5 x 1,5 m pendant la production du coffrage de l’escalier. A droite : éléments de coffrage pour un escalier de 3,5 m de haut. (crédits photo : Scawo3D)
La chambre d’impression de notre grande machine a une capacité de 15 mètres cubes avec des dimensions de 4 x 2,5 x 1,5 mètres et fonctionne actuellement avec une hauteur de couche de 3 millimètres. Cette combinaison d’une faible hauteur de couche et d’un grand nombre de buses nous permet de produire des éléments en béton avec une résolution très fine de 3 millimètres pour la construction. Malgré la haute résolution, nous produisons relativement rapidement. Nous pouvons imprimer 15 mètres cubes en huit heures. Toutefois, l’optimisation de la machine permettra bientôt de réduire ce délai à quatre heures.
Comme le matériau obtenu a des propriétés similaires à celles du béton normalisé des classes de résistance C25/30 – C60/75, la technologie peut être utilisée pour un large éventail d’applications. La résistance élevée à la compression permet d’utiliser des pièces imprimées par SPI ayant une fonction portante, qui peuvent également être exposées aux intempéries sous nos latitudes. Cela signifie qu’il est possible de fabriquer des éléments tels que des murs porteurs et des plafonds voûtés, ainsi que des façades. Bien entendu, il est également possible de produire des objets pour l’intérieur et l’extérieur, tels que des meubles de jardin ou des sculptures.
3DN : Quels sont les avantages de l’impression de béton par jet d’encre par rapport à l’extrusion ?
La plus grande différence entre le processus d’extrusion et le processus SPI est probablement le fait que notre processus est nettement moins complexe. D’une part, cela s’explique par le fait que nous fabriquons exclusivement en usine – du moins pour l’instant – et non directement sur le chantier. Cela peut être considéré comme un avantage ou un inconvénient. Dans tous les cas, l’avantage est que nous travaillons dans des conditions constantes, c’est-à-dire que nous ne devons pas adapter la machine ou le matériau à des environnements différents avec des températures ou une humidité variables. Le matériau avec lequel nous imprimons est donc simple et ne contient que du ciment, de l’eau et, à l’exception d’une petite quantité de superplastifiant, aucun produit chimique. Cela est également possible parce que le temps de passage d’une couche à l’autre est toujours le même – quelques secondes seulement.
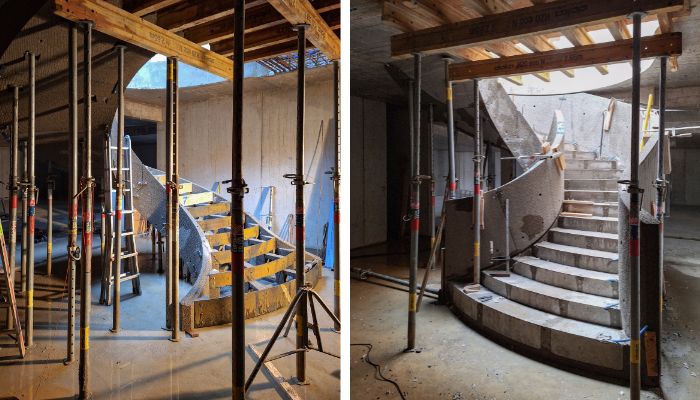
Assemblage du coffrage de l’escalier sur le chantier (crédits photo : Skeno/Scawo3D)
L’avantage suivant résulte du temps constant d’une couche à l’autre : quelle que soit la complexité de la géométrie à imprimer ou l’encombrement de notre espace de construction, le temps d’impression pour une impression de 15 mètres cubes reste toujours le même. Nous pouvons donc contrôler le prix grâce à l’utilisation de la capacité d’une chambre d’impression. Enfin, la production en usine présente l’avantage que la technologie est également adaptée à la construction dans des bâtiments existants. Dans ce domaine, on rencontre souvent des chantiers difficiles d’accès. Avec le procédé SPI, il n’y a pas besoin d’espace sur le chantier pour un grand portique d’impression, mais les pièces peuvent être dimensionnées en fonction du chantier. En résumé, l’« impression de béton par jet d’encre » donne simplement plus de liberté au concepteur.
3DN : Quels sont les projets les plus impressionnants réalisés par Scawo3D jusqu’à présent ?
J’aimerais mentionner deux projets : « Bridge the Gap » a été développé en collaboration avec le centre de recherche collaborative “Additive Manufacturing in Construction” (AMC TRR 277) et l’université technique de Munich. Ce projet a été le premier à démontrer que le béton imprimé en 3D dans un lit de poudre peut servir de structure de soutien. Il s’agit d’un prototype de pont piétonnier avec des travées porteuses de 5 x 2,5 mètres, qui a été imprimé en 21 parties puis assemblé à sec, c’est-à-dire sans mortier ou autre matériau de compensation dans les joints. Les détails de la conception des éléments de tension intégrés ont également été pris en compte au stade de la planification, également sans liaison permanente. Grâce à cette configuration, l’ensemble du pont a pu être assemblé en une journée, puis monté et démonté plusieurs fois sans avoir à endommager ou à détruire des pièces. Le projet montre comment utiliser efficacement un matériau – le béton a une résistance élevée à la compression mais une faible résistance à la traction – et comment le faire avec un matériau d’origine unique pour faciliter le recyclage ou le déclassement.
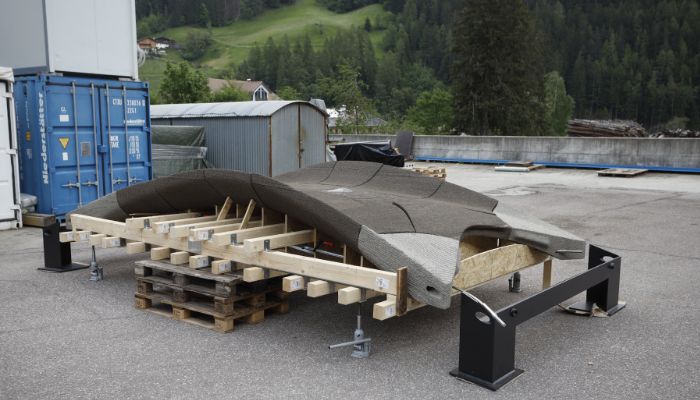
Premier assemblage du pont sur une sous-structure spécialement développée à Sarnthein. (crédits photo: AMC TRR 277 / Ema Krakovska)
Le deuxième projet, l’escalier H., est le plus grand escalier que nous ayons réalisé à ce jour avec notre coffrage imprimé en 3D : il s’agit d’un escalier de forme libre avec un plan elliptique et un diamètre de plus de trois mètres sur deux étages. L’entreprise de construction suisse Tschanen AG nous a contactés parce que les autres solutions auraient dépassé le budget disponible. Grâce à une bonne coopération entre les planificateurs, l’entreprise de construction et nous en tant que producteurs, nous avons également pu prouver avec ce projet que le processus SPI est adapté à diverses applications. Un avantage particulier de ce projet a été le transport simple de pièces maniables – contrairement au transport lourd d’un escalier préfabriqué entier – et le montage rapide sur le site en quelques jours. Alors que Scawo3D était encore en train d’assembler la première volée d’escaliers, Tschanen AG était déjà bien préparé pour l’installation de la deuxième volée et l’a achevée tout aussi rapidement. Les pièces imprimées en 3D constituent également une bonne base pour le traitement de surface ultérieur : le plâtrier a pu appliquer l’enduit directement sur le coffrage sans avoir à égaliser les irrégularités majeures.
3DN : Que peut apporter l’impression 3D à l’architecture ? Quels sont les défis à relever ?
Jusqu’à présent, les procédés d’impression 3D béton étaient limités dans leurs domaines d’application. Soit il n’était pas possible de réaliser toutes les géométries, soit la solidité et la résistance aux intempéries étaient considérablement réduites en raison de la structure de la couche liée au processus ou du matériau. Le procédé SPI nous a permis de surmonter ces deux problèmes. Il en résulte une liberté totale de forme lors du processus de conception, ce qui permet non seulement de concevoir des éléments différents d’un point de vue esthétique, mais aussi d’un point de vue structurel. Cela signifie que les éléments en béton peuvent désormais être optimisés sur le plan statique à un degré qui n’était auparavant possible qu’avec des travaux de coffrage complexes. C’est pourquoi je pense que l’impression 3D a le potentiel de déclencher une révolution dans l’architecture, en s’inspirant de méthodes de construction qui ont été oubliées pendant un certain temps.
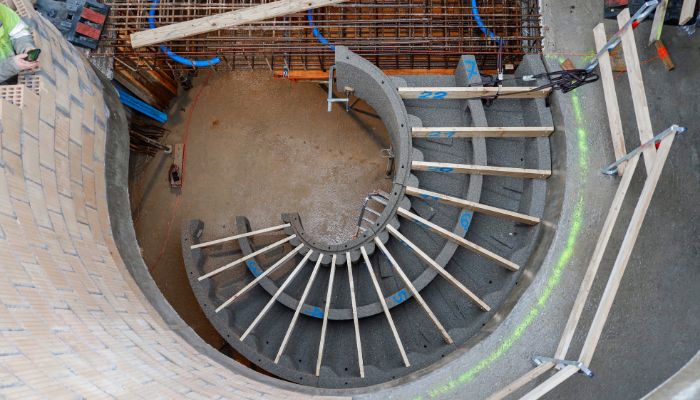
Assemblage du coffrage de l’escalier sur le chantier : première volée d’escalier entièrement installée sans balustrades (crédits photo : Skeno/Scawo3D)
Le plus grand défi, en revanche, est de mettre en pratique ce processus relativement nouveau à plus grande échelle. Depuis un certain temps, nous recevons des demandes et acceptons des objets de design ou d’art et des constructions gérables telles que des escaliers. Cependant, nous voyons plus de potentiel dans le processus SPI. Bien que les Romains connaissaient déjà les liants hydrauliques, il a fallu attendre le XIXe siècle et l’industrialisation pour que le ciment soit plus largement accepté. Ce que j’essaie de dire, c’est que nous n’en sommes qu’au début et que cela prend du temps.
La fabrication additive dans la construction a pris un bon départ. Il y a une pénurie de travailleurs qualifiés, alors qu’il faut créer rapidement plus d’espace habitable, ce qui permet enfin d’accorder plus d’attention à la discussion sur la durabilité, qui est nécessaire et urgente. En principe, les conditions sont réunies pour qu’une nouvelle technologie puisse être utilisée pour construire différemment et plus rapidement. L’inconvénient est que l’industrie est encore structurée par des normes qui ne sont pas très transparentes et sont basées sur un corpus de connaissances qui ne rend pas nécessairement justice aux exigences d’aujourd’hui, mais aussi aux possibilités actuelles en matière d’architecture.
Nous attendons que des clients extérieurs au secteur de la recherche fassent preuve de courage et, dans un premier temps, de la volonté financière d’adopter une nouvelle technologie telle que le procédé SPI. Nous avons démontré et continuerons à démontrer que la construction à grande échelle sous forme de composants porteurs est possible. Pour en savoir plus sur Scawo3D, consultez notre site web.
Que pensez-vous du procédé développé par Scawo3D ? N’hésitez pas à partager votre avis dans les commentaires de l’article. Retrouvez toutes nos vidéos sur notre chaîne YouTube ou suivez-nous sur Facebook ou LinkedIn !
*Crédits photo de couverture : Skeno/Scawo3D