SABIC et Local Motors cherchent à améliorer la circularité de l’impression 3D grand format
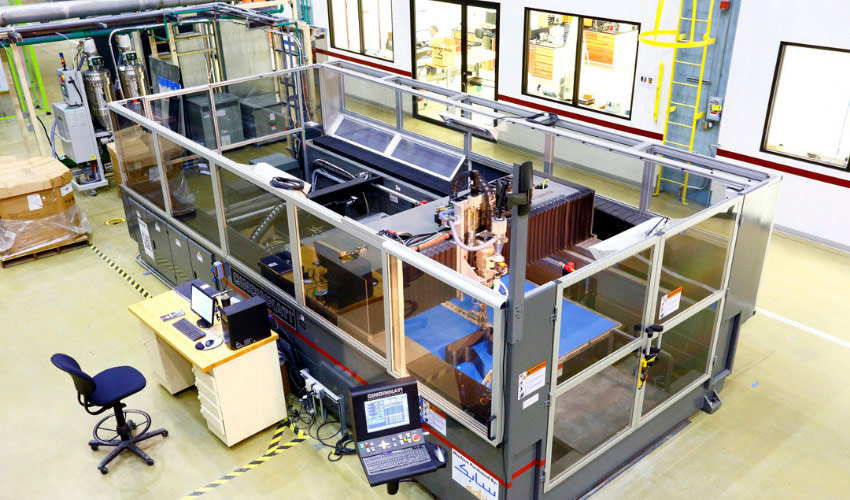
SABIC, un des leaders mondiaux de la chimie, et Local Motors, un constructeur automobile réputé pour son mini bus Olli, ont annoncé qu’ils avaient terminé une étude visant à déterminer si les pièces fabriquées à l’aide de la fabrication additive grand format (LFAM) pouvaient être recyclées en nouveaux matériaux avant d’être finalement transformées en nouvelles pièces. L’étude conjointe a été réalisée sur la faisabilité du recyclage des pièces thermoplastiques usagées et des économies réalisées grâce au processus d’impression 3D. Pour le déterminer, les chercheurs ont suivi l’imprimabilité et les propriétés mécaniques de pièces fabriquées avec le matériau renforcé LNP™ THERMOCOMP™ AM de SABIC après son recyclage. Les résultats ont été extrêmement prometteurs, même si les chercheurs ont souligné que des travaux supplémentaires doivent être effectués avant que cette solution ne soit réellement efficace.
Les enjeux environnementaux sont de plus en plus importants dans une variété d’industries, y compris la fabrication additive surtout lorsqu’il s’agit de l’élimination des pièces. Les fabricants réfléchissent à la manière de devenir plus durables, à la fois pour préserver notre environnement mais aussi pour réduire les coûts. L’une des façons d’y parvenir est d’essayer de se tourner davantage vers un processus de fabrication circulaire. L’idée est de recycler les pièces déjà fabriquées en matériaux, ce qui leur permet de les réutiliser pour de futures pièces. C’est le coeur de cette étude conjointe particulière.
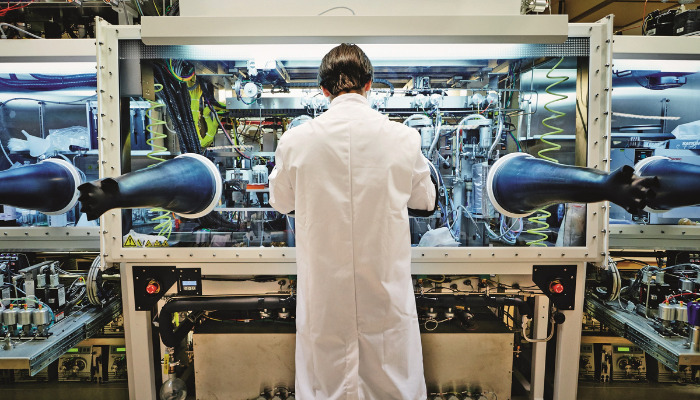
Le laboratoire de recherche SABIC aux Pays-Bas, où sont menées des études comme celle-ci (crédits photo : SABIC)
L’étude de faisabilité de SABIC et Local Motors
Comme mentionné précédemment, l’objectif de cette étude de faisabilité était d’explorer des alternatives durables à la mise en décharge de pièces imprimées de grande taille afin de faciliter l’adoption plus large de la LFAM. Actuellement, il n’existe pas de chaîne de valeur établie pour la récupération des pièces et des déchets de post-production liés à cette technologie. Et jusqu’à présent, la plupart des pièces recyclées étaient plus petites et utilisaient souvent des matériaux tels que le PLA qui est déjà conçu pour être biodégradable.
Dans l’étude elle-même, SABIC et Local Motors ont testé l’imprimabilité et les propriétés mécaniques du composé renforcé LNP™ THERMOCOMP™ AM de SABIC après avoir été imprimé, récupéré, broyé et retraité sous forme de granulés. L’objectif était de voir comment ce matériau se comportait et si la dégradation due à de multiples cycles thermiques limiterait les possibilités de réutilisation du matériau. Pour le test, six échantillons de matériau du composé ont été préparés, contenant respectivement 0, 15, 25, 50, 75 et 100 % de contenu retraité.
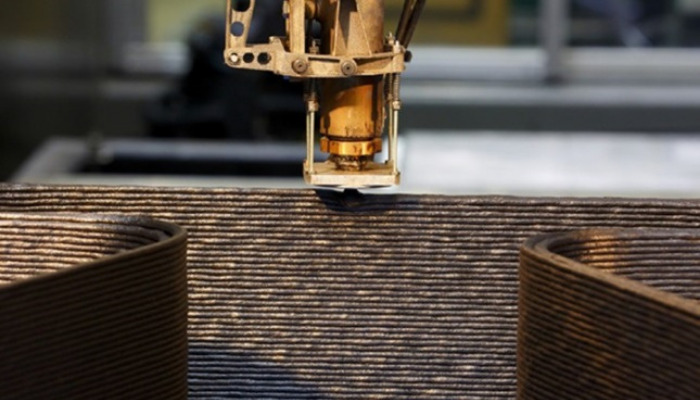
Le composé LNP™ THERMOCOMP™ AM (crédits photo : SABIC)
Les résultats sont prometteurs. Chaque échantillon a été utilisé pour fabriquer un hexagone à paroi simple sur la machine de fabrication additive Big Area de SABIC. Tous les échantillons ont bien été imprimés, montrant « une surface lisse et brillante, et des couches droites et régulières qui ne présentaient aucun problème de flux de matériau« . De plus, les propriétés mécaniques ont été testées. Dans ce cas, les résultats ont montré d’excellentes propriétés de traction, mais uniquement pour les échantillons contenant de faibles pourcentages de matière rebroyée. Des « déclins progressifs » ont été constatés dans les échantillons contenant des pourcentages plus élevés de rebroyage, ce qui a entraîné une réduction de 20 % des propriétés de traction sur l’axe x et de 15 % sur l’axe z pour l’échantillon 100 % rebroyé. Toutefois, selon le communiqué de presse, cette constatation est typique des matières rebroyées utilisées dans d’autres procédés, notamment le moulage par injection.
S’exprimant sur les résultats, Walter Thompson, ingénieur en développement d’applications chez SABIC, a conclu : « Alors que l’adoption de la fabrication additive grand format s’accélère, il est essentiel de trouver des alternatives durables à la mise en décharge des pièces imprimées de grande taille. SABIC et Local Motors ont étudié l’aspect pratique de l’utilisation de matériaux de rebut broyés mécaniquement et de pièces en fin de vie générées par la LFAM. Notre étude a montré un grand potentiel de réutilisation de ces matériaux et marque une première étape dans le soutien de la réutilisation au sein de la chaîne de valeur. » Vous pouvez en savoir plus en lisant le communiqué de presse ICI.
Que pensez-vous de l’étude menée par SABIC et Local Motors ? N’hésitez pas à partager votre avis dans les commentaires de l’article ou avec les membres du forum 3Dnatives. Retrouvez toutes nos vidéos sur notre chaîne YouTube ou suivez-nous sur Facebook ou Twitter !