L’impression 3D au service de la restauration d’une église
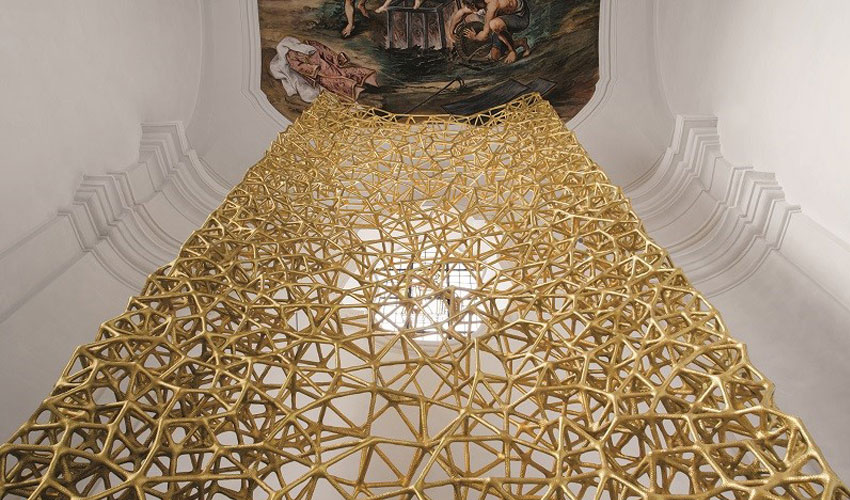
La fabrication additive est partout, même là où on ne l’attend pas vraiment : en Allemagne, si vous vous baladez à Altmühldorf en Bavière, vous aurez sûrement l’opportunité de voir un retable imprimé en 3D dans l’église du village. Conçue par Oliver Tessin et les artistes Corbinian Böhm et Michael Gruberen, en partenariat avec le service d’impression 3D allemand FIT AG, la structure dorée s’étend sur 8 mètres de haut, 2,5 mètres de large, et est un bel exemple d’optimisation topologique. Elle rappelle en effet un nid d’abeille où toutes les branches sont imbriquées méticuleusement.
Toute la phase de modélisation 3D qui précède l’étape d’impression permet à l’utilisateur de jouer avec les formes, la matière et de vérifier si son design est optimisé pour la fabrication additive. Souvent, le modèle 3D est imaginé avec le moins de matériau possible pour éviter d’augmenter les coûts et les étapes de post-traitement. L’optimisation topologique nous permet de faire cela et vient supprimer la matière là où aucun effort ne transite : le poids final de la pièce est donc réduit, son coût aussi. Dans l’élaboration d’une pièce telle qu’un retable, c’est un avantage clé – celui-ci est souvent imposant et chargé en détails. Pourtant, la fabrication additive n’est pas une méthode de production qui vient à l’esprit quand il s’agit de restaurer une église. Les équipes derrière le projet ont d’ailleurs dû prouver à la ville que les technologies 3D étaient une méthode viable.
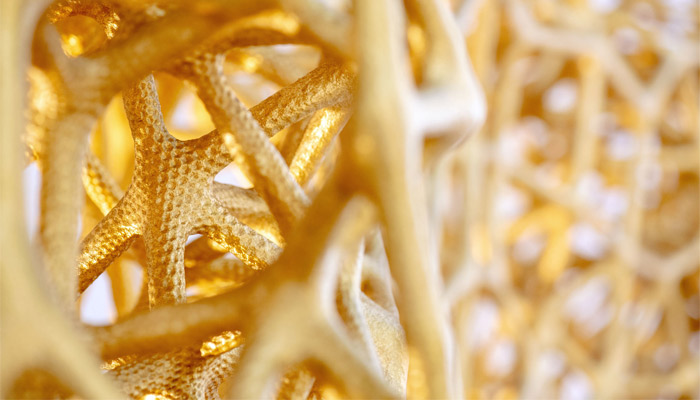
La structure du retable fait penser à un nid d’abeille
Le processus de fabrication du retable imprimé en 3D
A l’origine, les architectes chargés du projet souhaitaient utiliser la technologie WAAM, attirés par son aspect uniques, ses propriétés et surtout la possibilité d’utiliser du métal. Toutefois, en se rapprochant du service d’impression 3D FIT AG, ils se sont rendus compte que d’autres procédés et matériaux pouvaient être plus intéressants en termes de coûts, restrictions géométriques et durabilité des pièces. C’est le frittage laser qui s’est avéré le plus pertinent, offrant des performances mécaniques élevées, un poids réduit et une grande liberté de conception.
FIT AG explique qu’il a imprimé les 60 pièces de la structure sur une machine EOS P 770 à partir de PA12, chaque pièce mesurant 680 x 550 x 380 mm. Il affirme qu’il a fallu 120 jours-machines, soit 3 semaines compte de son parc d’imprimantes, pour tout produire. Une fois l’impression terminée, elles ont été recouvertes d’un alliage structurel bronze-aluminium via une projection thermique et d’un vernis métallique pour créer le brillant final. Ce revêtement aurait surtout été appliqué pour garantir une durabilité du polyamide dans le temps, avoir une certaine résistance à l’oxydation et à l’environnement (poussière, suie, etc.)
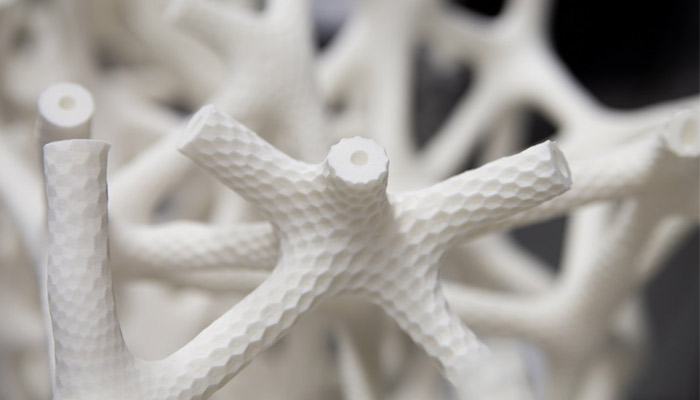
Les pièces imprimées en polyamide avant revêtement
Selon les équipes, le processus d’assemblage a été l’étape la plus compliquée : l’ensemble de la structure pesant 350 kilos, il a fallu imaginer un moyen efficace de monter le retable sur site. 2 000 connecteurs individuels auraient été collés à la main. Le projet aurait duré 6 mois, la partie impression 3D étant la plus rapide. Le résultat est assez bluffant ! Bruno Knychalla, Ingénieur Projet chez FIT AG, conclut : “Les nouvelles technologies et les objets spirituels ne sont pas si souvent combinés. Je pense que notre large éventail de connaissances technologiques et notre équipe interdisciplinaire ont convaincu les gens que nous pouvions faire quelque chose d’audacieux et de nouveau qui laisse une impression d’artisanat de qualité, avec une élégance intemporelle. Je pense que les gens ont été vraiment étonnés.” Vous pouvez retrouver davantage d’informations ICI.
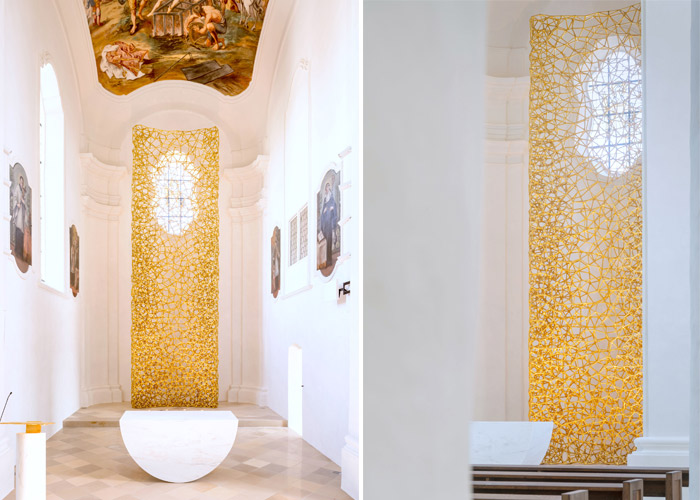
Le retable imprimé en 3D (crédits photo : Studio Tessin)
Que pensez-vous de ce retable imprimé en 3D ? Partagez votre avis dans les commentaires de l’article ou avec les membres du forum 3Dnatives. Retrouvez toutes nos vidéos sur notre chaîne YouTube ou suivez-nous sur Facebook ou Twitter !