Recuit VS pressage isostatique à chaud (HIP) : quel traitement thermique choisir en impression 3D ?
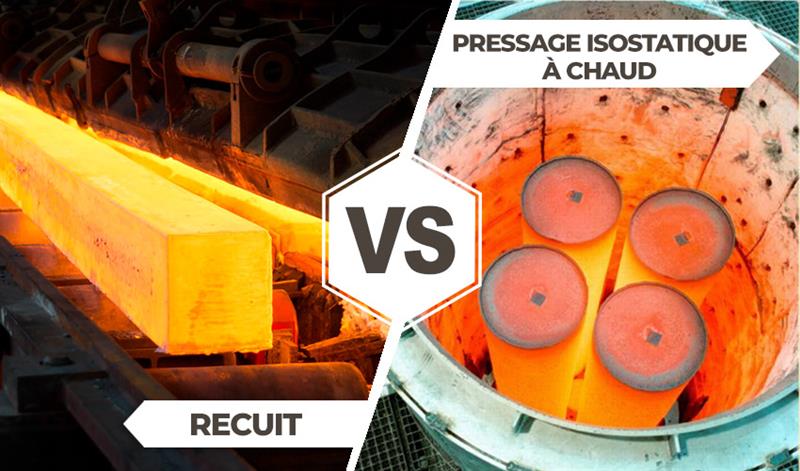
Alors que la fabrication additive continue de s’industrialiser, le post-traitement devient de plus en plus crucial. Cette étape critique permet aux utilisateurs d’améliorer les pièces, de les rendre plus résistantes et plus denses, voire de leur donner des propriétés spécifiques, afin qu’elles puissent être utilisées pour des applications finales importantes. Parmi les différents types de post-traitement, l’un des plus importants pour l’impression 3D sur lit de poudre, en particulier pour les métaux, est le traitement thermique. Mais quel traitement thermique convient à une pièce ? Comment fonctionne-t-il ? Pour répondre à ces questions, nous avons voulu examiner deux processus de traitement thermique couramment utilisés : le pressage isostatique à chaud (HIP) et le recuit.
Les deux sont compatibles avec les procédés métalliques, y compris le LPBF, l’EBM, le liage de poudre, le DED et même la projection de nanoparticules. Ils peuvent également être utilisés avec les céramiques et les polymères, bien qu’à des degrés différents. Les deux méthodes présentent de nombreux avantages, notamment celui de renforcer les matériaux, de les rendre plus faciles à travailler et d’en améliorer les propriétés. À la base, ces deux techniques permettent d’optimiser les composants, mais leurs processus et leurs résultats spécifiques diffèrent.
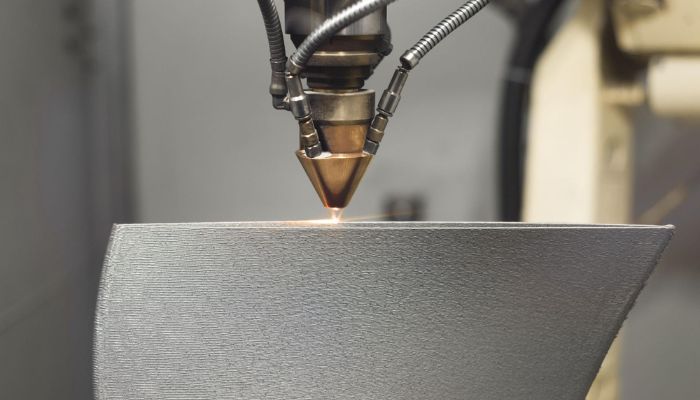
Une pièce métallique en cours d’impression (crédits photo : Industrial Metal Service)
Comment fonctionnent le pressage isostatique à chaud et le recuit
Pour comprendre les différences et les similitudes entre le HIP et le recuit, nous allons passer en revue chaque procédé. Tout d’abord, le recuit est un traitement thermique qui consiste à chauffer des métaux, du verre, des céramiques ou des polymères et à laisser le matériau refroidir lentement pour éliminer les tensions internes. Ce processus modifie les propriétés physiques, et parfois chimiques, d’un matériau, en augmentant sa ductilité et en réduisant sa dureté pour le rendre plus facile à travailler.
Le HIP, quant à lui, consiste à exposer une pièce à une combinaison de températures élevées et de pressions de gaz afin d’éliminer la porosité des matériaux métallurgiques. Il peut également augmenter la densité de nombreuses céramiques, les transformant en composants entièrement denses.
N’oubliez pas que le « I » de HIP signifie isostatique. Dans ce cas, il s’agit du gaz qui est appliqué de manière isostatique, ce qui signifie qu’il exerce une pression égale dans toutes les directions sur un matériau. Il en résulte une force uniforme autour de l’objet. Comme le recuit, le HIP améliore les propriétés mécaniques et l’aptitude au façonnage d’un matériau. Ce procédé permet également d’assembler des matériaux dissemblables pour en faire des pièces uniques.
Le processus de recuit
Le recuit a lieu dans un four adapté. Ceux-ci diffèrent en fonction des besoins des matériaux et du coût, mais en général, ils peuvent être chauffés entre 300°C et 1 000°C (pour les modèles plus haut de gamme). La température dans le four doit être soigneusement contrôlée, c’est pourquoi ces fours de recuit sont souvent recommandés – notez toutefois que s’il répond aux exigences de température, n’importe quel four atteignant la bonne température peut théoriquement être utilisé.
Le recuit se déroule en trois étapes, toutes déterminées par des paramètres de température qui dépendent du type de matériau utilisé. Pour effectuer un recuit, il est essentiel de connaître le matériau et ses exigences en matière de température.
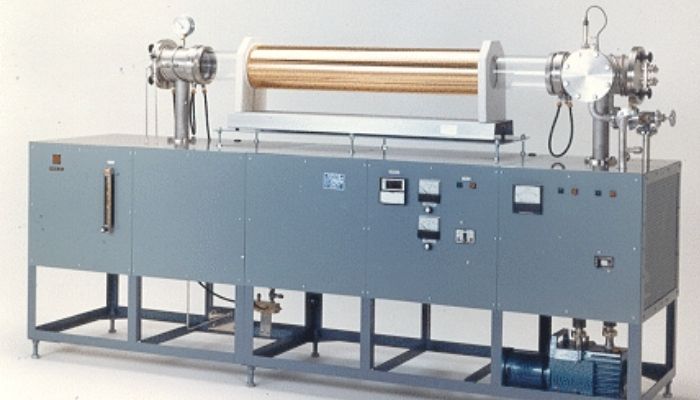
Un four de recuit (crédits photo : Thermcraft)
1. Étape de récupération
Au cours de la première étape du recuit, l’étape de récupération, la température du matériau est portée à un niveau supérieur à la température de cristallisation afin que les atomes aient l’énergie nécessaire pour se déplacer. Le mouvement des atomes permet de redistribuer et d’éradiquer les dislocations (irrégularités au sein d’une structure cristalline), en particulier dans les métaux. Cela rend le métal plus déformable et donc plus ductile. Le même effet peut se produire avec les céramiques, mais à un degré moindre. Globalement, cette étape permet de réduire les contraintes internes du matériau.
2. Étape de recristallisation
À mesure que le matériau continue à chauffer, il finit par atteindre le stade de la recristallisation, c’est-à-dire une température suffisamment élevée pour permettre la recristallisation, mais toujours inférieure au point de fusion. À ce stade, de nouveaux grains sans contrainte se forment et croissent, remplaçant l’espace laissé par les dislocations précédentes.
3. Phase de croissance des grains
Une fois la recristallisation terminée, l’objet peut commencer à refroidir et entrer dans la phase de croissance des grains. Au fur et à mesure qu’il refroidit, de nouveaux grains se développent et croissent. Toutefois, la croissance de ces grains n’est pas aléatoire. Elle est contrôlée en fonction de la vitesse de refroidissement et de l’atmosphère dans laquelle l’objet se refroidit.
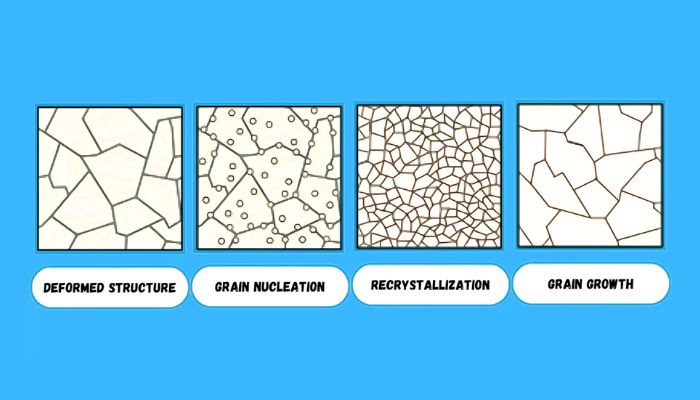
Représentation graphique de ce qui arrive aux molécules pendant le recuit (crédits photo : MechDaily)
En fonction du matériau, le recuit peut durer de quatre heures à une journée entière. Il convient également de noter qu’il existe plusieurs types de recuit. Bien qu’il ne s’agisse pas d’une liste exhaustive de tous les procédés de recuit, certains des plus couramment utilisés sont le recuit complet, le recuit isotherme, le recuit de sphéroïdisation, le recuit de diffusion et le recuit de détente.
Les pièces fabriquées de manière additive, ou du moins celles qui sont fabriquées avec des matériaux appropriés, peuvent bénéficier de tous ces procédés. Si vous devez choisir entre différents types de procédés de recuit, votre matériau et votre application seront des facteurs déterminants.
Le procédé de pressage isostatique à chaud
Le HIP consiste à charger des pièces dans une enceinte de confinement à haute pression et à les exposer à une température élevée et à une forte pression de gaz isostatique. Cette température peut atteindre 2 000 °C et la pression 310 MPa, soit à peu près la pression de la fosse des Mariannes à 11 000 m de profondeur dans l’océan Pacifique. Le matériau se contracte alors, conservant sa forme initiale jusqu’à ce que les pores disparaissent à l’intérieur, densifiant ainsi la pièce. Ce procédé est largement utilisé pour réduire les tensions dans les pièces frittées, moulées et fabriquées de manière additive
L’argon est le gaz de pressurisation le plus utilisé pour ce procédé. Étant un gaz inerte, l’argon n’entraîne pas de réaction chimique du matériau. Le type de métal utilisé peut également minimiser les effets d’une réaction chimique. Certains systèmes utilisent également un pompage de gaz associé pour atteindre le niveau de pression nécessaire. Ces gaz sont appliqués uniformément sur l’objet et maintenus pendant une durée déterminée.
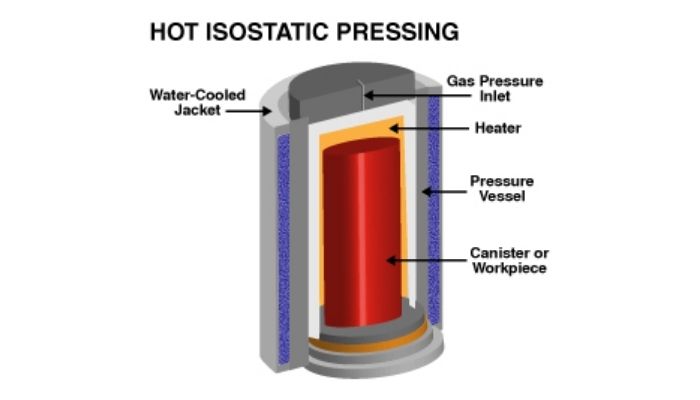
Crédits photo : Metal Powder Industries Federation
Les niveaux de température et de pression du gaz, ainsi que la durée du cycle, sont tous déterminés par le type de matériau utilisé et les propriétés souhaitées du produit final. Les cycles peuvent durer de huit à douze heures ou jours. Le processus confère aux pièces une microstructure uniforme, ce qui améliore leurs propriétés.
En ce qui concerne les procédés d’impression 3D, Hiperbaric, leader dans le domaine du pressage isostatique à chaud, note que le HIP peut être facilement combiné avec la fusion laser sur lit de poudre et l’EBM pour obtenir des pièces de qualité supérieure. Le liage de poudre, le DED, l’extrusion de matériaux métalliques et la projection de matériaux métalliques (comme dans la projection de nanoparticules) sont également compatibles.
Compatibilité des matériaux pour le HIP et le recuit
Nous l’avons brièvement mentionné ci-dessus, mais les procédés HIP et de recuit se recoupent en ce qui concerne les matériaux. En effet, ils peuvent être utilisés avec différents métaux, quel que soit le type d’ailleurs.
Prenons l’exemple du recuit. Cette méthode de post-traitement est compatible avec les matériaux amorphes et cristallins. Il peut donc être utilisé pour les métaux réfractaires, les alliages et l’acier, entre autres. L’acier inoxydable est considéré comme l’un des matériaux les plus couramment utilisés pour les pièces recuites, mais le bronze, l’aluminium, le cuivre et le laiton sont également mentionnés. Côté HIP, tous les métaux semblent être compatibles. Il peut même être utilisé avec des matériaux difficiles à travailler comme les superalliages de nickel et les alliages de titane.
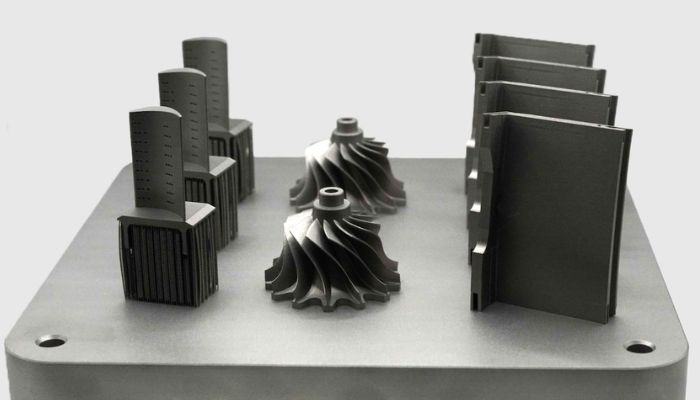
Exemple de superalliage de nickel imprimé en 3D (crédit photo : Alloyed / Aubert & Duval)
Cependant, les métaux ne sont pas les seuls matériaux compatibles. Les pièces en céramique peuvent également être post-traitées par HIP ou par recuit. Là encore, il semble que tant que les propriétés du matériau sont respectées, toutes les céramiques soient compatibles avec l’un ou l’autre procédé.
Le recuit, quant à lui, se distingue par sa compatibilité avec la plupart des polymères. Comme il n’implique pas de pression, mais plutôt des changements de température, de nombreux polymères utilisés en fabrication additive peuvent être recuits.Par exemple, il est souvent employé pour améliorer la résistance des pièces en ABS. D’autres matériaux standard qui n’ont pas les meilleures propriétés, tels que les pièces en PLA et PETG, sont de plus en plus recuits, même par les fabricants. Ce n’est pas nécessairement le cas pour le HIP.
Avantages et inconvénients des procédés
Bien que le recuit et le HIP impliquent des processus différents, leurs avantages sont similaires. Tous deux améliorent la ductilité et éliminent les imperfections du matériau, qu’il s’agisse de pores (HIP) ou de dislocations dans la structure cristalline (recuit). Le recuit et le pressage isostatique à chaud éliminent essentiellement les défauts et les contraintes internes et améliorent l’homogénéité de la microstructure et les propriétés du matériau. Ces deux procédés permettent également de consolider les étapes, car de nombreuses pièces métalliques imprimées en 3D nécessitent de toute façon un traitement thermique pour réduire les contraintes thermiques résiduelles.
Le recuit, qui provoque la migration des molécules dans la microstructure, élimine les contraintes qui ont pu être introduites lors de la formation du matériau. Ce processus permet également d’éviter les fissures et d’améliorer l’usinabilité. De plus, les dislocations du réseau cristallin du métal étant rectifiées, la conductivité électrique est améliorée, de même que ses propriétés magnétiques. Le recuit peut permettre de manipuler un matériau avec précision pour obtenir les caractéristiques souhaitées en le chauffant et en le refroidissant de manière sélective, ce qui permet d’obtenir le type de grains souhaité et d’influer sur les propriétés physiques du matériau.
Le procédé HIP permet d’augmenter la densité d’un matériau, car il forme des liaisons métallurgiques entre différents matériaux par diffusion. Ces améliorations sont essentielles pour les applications nécessitant une résistance et une fiabilité élevées. La méthode permet également de réparer les défauts d’un matériau. Par exemple, une pièce métallique présentant un trou à l’intérieur peut être soumise au procédé HIP, de sorte que le trou soit comblé par un matériau comprimé. D’une manière générale, le HIP et le recuit peuvent contribuer à réduire les déchets de matériaux, car ils permettent d’améliorer ceux existants, garantissant ainsi leur longévité et réduisant la nécessité d’en acquérir d’autres.
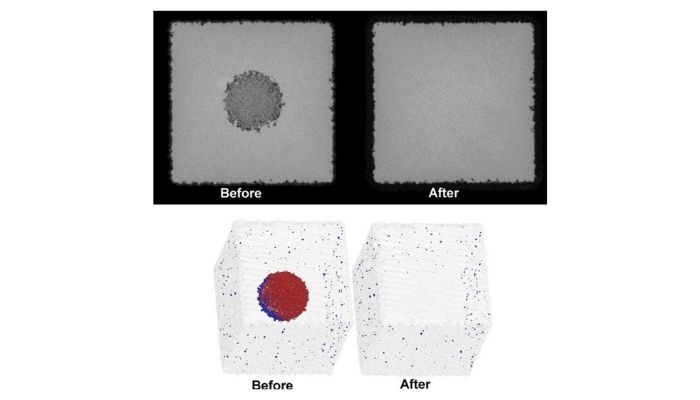
Représentation avant et après d’un matériau soumis au HIP (crédits photo : Hot isostatic pressing in metal additive manufacturing X-ray tomography reveals details of pore closure, Science Direct, A. du Plessis a b, E. Macdonald)
L’inconvénient de ces deux procédés est le temps nécessaire pour achever le processus. Ils peuvent prendre plus de 24 heures, et le HIP en particulier peut prendre plusieurs jours. Bien entendu, ces deux technologies entraînent également des dépenses supplémentaires. Elles nécessitent des coûts initiaux pour l’équipement et les opérateurs qualifiés, puis elles requièrent de grandes quantités d’énergie pour la chaleur. Le recuit peut également impliquer un refroidissement forcé, ce qui signifie encore plus d’énergie. Pour les deux méthodes, la durée et le coût dépendent fortement du matériau utilisé et de la taille de votre production.
Enfin, les deux procédés peuvent affecter les dimensions finales d’une pièce, ce qui n’est pas nécessairement un inconvénient, mais un élément à prendre en considération. Le recuit peut entraîner une modification des dimensions parce que la microstructure du matériau est modifiée, ce qui peut également se produire avec le procédé HIP parce que le matériau est comprimé. Le degré de modification dépend de facteurs tels que le matériau utilisé et les paramètres du processus.
Finalement, quand faut-il éviter le recuit ou le pressage isostatique à chaud ? Si vos pièces ne nécessitent pas de propriétés mécaniques améliorées, il n’est peut-être pas utile de payer pour ces procédés. Le HIP, en particulier, peut ne pas convenir si votre pièce comporte des cavités internes ou des canaux complexes qui pourraient s’effondrer sous l’effet de la pression. Le procédé HIP est idéal lorsque vous souhaitez qu’une pièce soit dense. Si vous avez une pièce imprimée en 3D qui est déjà entièrement dense (comme une pièce de haute qualité fabriquée par fusion laser sur lit de poudre), il n’est pas nécessaire de recourir à ce procédé.
Applications du recuit et du pressage isostatique à chaud
Techniquement, le recuit et le pressage isostatique à chaud peuvent être utilisés dans tous les secteurs où les propriétés des matériaux sont importantes. Il est toutefois nécessaire de mentionner que si le pressage isostatique à chaud est relativement inaccessible, sauf au niveau industriel, le recuit peut être réalisé beaucoup plus facilement, ce qui l’ouvre à un public plus large.
Il existe toutefois des secteurs spécifiques où ces méthodes de post-traitement sont couramment utilisées. Le HIP, par exemple, a été utilisé pour la première fois dans un cadre commercial dans l’industrie aérospatiale. Plus précisément, il a été utilisé pour produire des pales de turbines de moteurs à réaction. Bien entendu, à l’époque, il ne s’agissait pas de pièces fabriquées par fabrication additive.
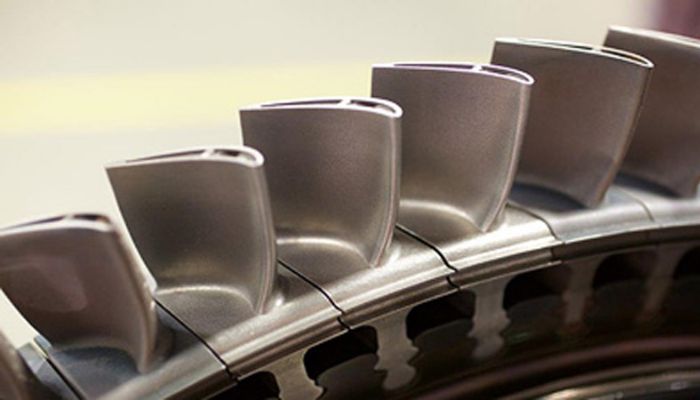
Des pales de turbines imprimées en 3D (crédits photo : Siemens)
Si l’on s’intéresse spécifiquement à l’utilisation du HIP combiné à l’impression 3D, on pense au secteur médical, où les deux procédés permettent de créer des prothèses de hanche et de genou à partir d’alliages de titane. Dans l’aérospatiale, les superalliages de nickel sont utilisés avec le LBPF pour les aubes de turbine et le CoCR pour les injecteurs de carburant. Le HIP est également présent dans le secteur automobile, car il permet d’avoir une plus grande confiance dans les pièces imprimées en 3D.
Le recuit se retrouve dans des industries similaires, car il améliore la ductilité, élimine les tensions et réduit la dureté des matériaux. La fragilité des métaux peut également être réduite tout en améliorant les propriétés magnétiques. Par conséquent, les applications dans lesquelles ces propriétés sont appréciées sont les mieux adaptées.
Les industries clés pour le recuit sont le médical, l’aérospatiale, l’automobile et les équipements à semi-conducteurs. Dans l’aérospatiale, il est couramment utilisé pour les composants des avions et peut être utilisé de la même manière pour les panneaux de carrosserie dans le secteur de la construction automobile. En médecine, il peut être utilisé pour les dispositifs médicaux tels que les implants orthopédiques, car il permet de former des alliages et des métaux biocompatibles présentant la résistance et la durabilité requises. Enfin, comme le recuit peut améliorer la conductivité électrique, il peut être utile dans l’industrie électronique pour la fabrication de semi-conducteurs ou de cellules solaires.
Fabricants et prix
Pour recuire une pièce, vous n’avez pas nécessairement besoin d’un four de recuit. Parfois, des fours standard comme les fours de laboratoire conviennent, en particulier pour les projets à petite échelle ou de bricolage, lorsqu’une précision extrême n’est pas nécessaire, principalement avec les polymères. Toutefois, si c’est le cas, un four de recuit spécialisé peut s’avérer indispensable. Les fabricants de tels équipements sont notamment Precons, Gasbarre Products, Inc et CM Furnaces, Inc.
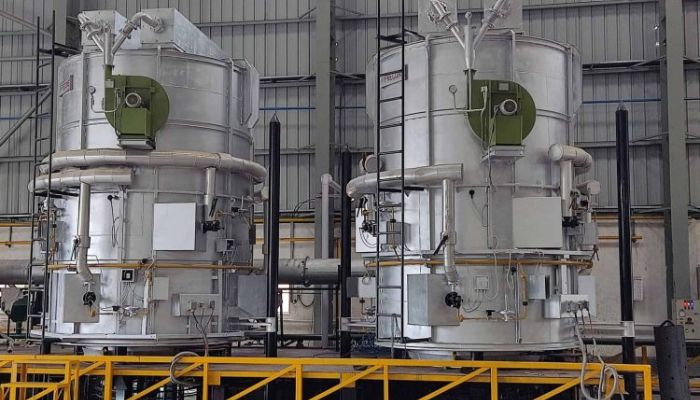
Des fours de recuit (crédits photo : Precons)
Contrairement au recuit, le HIP nécessite des machines spécialisées. Vous pouvez soit faire appel à un service, soit envisager d’acheter une machine vous-même. Parmi les principaux fabricants, citons Bodycote, Kobe Steel, Aalberts, Quintus et ESPI.
Le coût du recuit et du traitement HIP dépend de plusieurs facteurs, tels que le matériau utilisé, l’échelle de production, les exigences de l’application et le fait que vous souhaitiez externaliser le service ou effectuer le traitement en interne.
Pour le recuit, les fours de laboratoire peuvent coûter environ 500 dollars, et les fours de recuit industriels se situent entre 3 000 et 100 000 dollars. Les machines de pressage isostatique à chaud suivent une fourchette de prix similaire : les plus petites solutions sont disponibles à partir d’environ 7 000 dollars, tandis que les grandes peuvent coûter des centaines de milliers de dollars, voire plus.
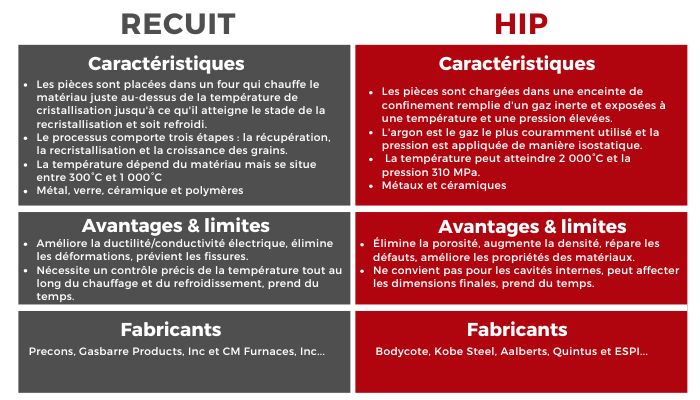
Crédits photo : 3Dnatives
Utilisez-vous le recuit ou le pressage isostatique à chaud ? Quelle méthode préférez-vous ? N’hésitez pas à partager votre avis dans les commentaires de l’article. Retrouvez toutes nos vidéos sur notre chaîne YouTube ou suivez-nous sur Facebook ou LinkedIn !
*Photo de couverture: Recuit (crédits photo : Aria) et HIP (crédits photo : ThermalProcessing.Com)