Un composant de quadripôle radiofréquence (RFQ) imprimé en 3D en cuivre
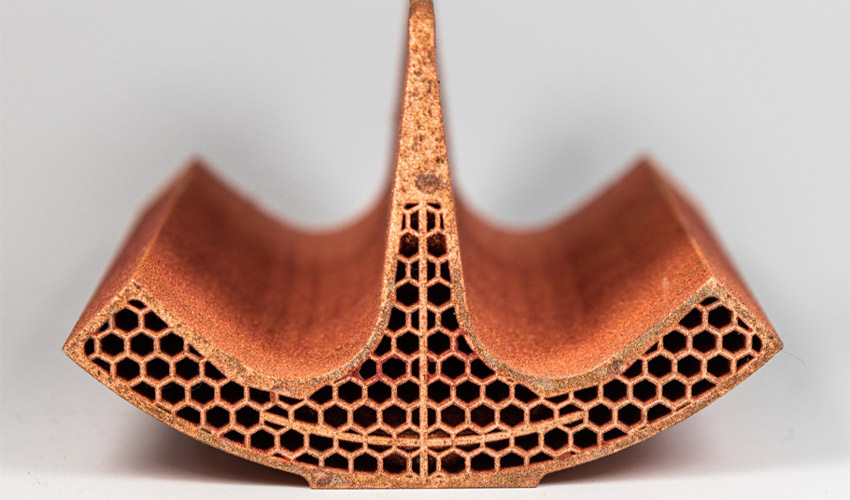
Le CERN, ou Organisation européenne pour la recherche nucléaire, intègre actuellement le plus grand accélérateur de particules au monde. Appelé le Grand collisionneur de hadrons (LHC), son objectif est de transmettre de l’énergie à des particules grâce à des champs électriques ou magnétiques. Et si le LHC nous intéresse aujourd’hui c’est parce qu’il pourrait comprendre pour la première fois un quadripôle radiofréquence imprimé en 3D en cuivre. Il s’agit plus particulièrement d’un accélérateur linéaire quadripolaire à radiofréquence (RFQ), l’une des pièces les plus difficiles à concevoir et à assembler. C’est sans doute pourquoi l’institut Fraunhofer IWS, en collaboration avec le CERN, l’université technique de Riga et l’université polytechnique de Milan, a choisi la fabrication additive pour le produire, plus particulièrement la fusion laser sur lit de poudre.
Les partenaires de cette première mondiale font tous partie du projet I.FAST, financé par l’Union européenne, qui a pour objectif de développer de nouvelles conceptions d’accélérateurs de particules. Avec 49 partenaires, il devrait permettre d’accélérer l’innovation autour d’un sujet confronté à de nombreux défis. C’est donc dans ce cadre-là que la fabrication additive métal a été employée, nouvel exemple concret du potentiel de la technologie.
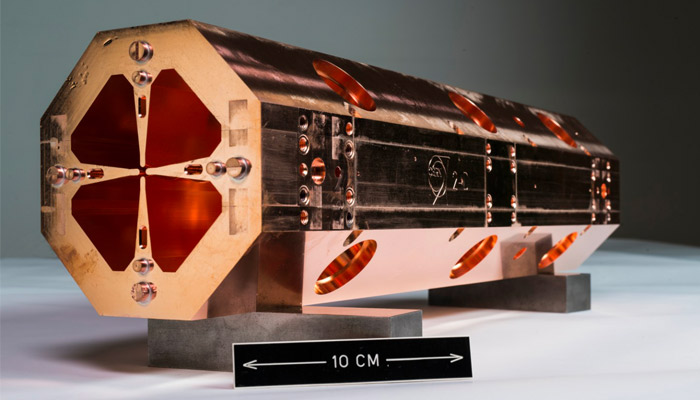
Le modèle classique d’un quadripôle complet (crédits photo : CERN)
La fabrication additive pour contourner des problématiques d’assemblage
Selon les partenaires du projet, le RFQ est traditionnellement fabriqué à partir de matériaux et d’alliages hautement conducteurs, via un fraisage multi-axes de “composants monoblocs préfabriqués et forgés à grande échelle”. Concrètement, le RFQ intègre 4 modules qui sont assemblés par brasage au four. Or, ce dernier vient généralement libérer des contraintes résiduelles entraînant alors une distorsion géométrique. Plusieurs traitements thermiques pendant l’usinage sont alors nécessaires pour maintenir le niveau de qualité et assurer le bon fonctionnement de la pièce. Vous vous en doutez, toutes ces étapes sont chronophages, coûteuses et peu efficaces. Face à ce constat, les partenaires du projet se sont penchés sur la fabrication additive, notamment de par sa capacité à produire des composants en un seul bloc, évitant ainsi les étapes d’assemblage et leurs contraintes.
Ils expliquent : “À terme, des segments complets comprenant les quatre « ailettes » du système RFQ pourraient être construits en une seule pièce, évitant ainsi le brasage et permettant la fabrication optimale d’éléments complexes tels que les canaux de refroidissement internes et les ports externes. Les progrès réalisés dans les équipements de fabrication additive, les capacités de conception (y compris les outils de simulation) et la méthodologie de fabrication elle-même ouvrent de nouvelles voies pour l’optimisation de la conception du RFQ et la production à grande échelle, même en utilisant du cuivre pur, qui est considéré comme un matériau difficile pour les processus d’impression 3D laser.” En effet, le cuivre est un métal qui va réfléchir la lumière du laser, si bien qu’il va aussi réfléchir une partie de l’énergie nécessaire à la fabrication de la pièce.
Un prototype de quadripôle radiofréquence optimisé
Les partenaires ont choisi la fusion laser sur lit de poudre, plus spécifiquement une machine TruPrint1000, pour répondre à toutes les contraintes de production, notamment en termes de précision géométrique, de rugosité de surface mais aussi de conductivité électrique. Ils ont reproduit un quart du quadripôle radiofréquence actuellement utilisé par le CERN. Le prototype imprimé en 3D mesure 95 mm de longueur et reprend l’extrémité de l’aube, les surfaces internes, les canaux de refroidissement améliorés et la structure interne redessinée. C’est un motif en nid d’abeille qui a été choisi dans la phase de conception, ce qui a réduit de 37% le volume de matériau nécessaire et de 21% le poids total. Il aura fallu 16h30 d’impression pour fabriquer le prototype en question – celui-ci à une épaisseur de couche de 30 microns et une hauteur de 98,01 mm.
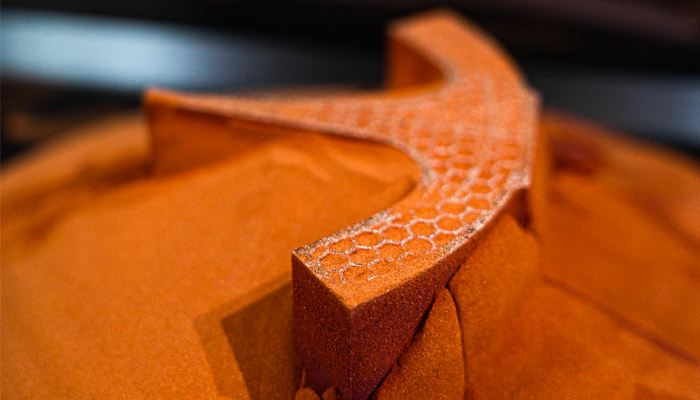
Les partenaires ont opté pour la fusion laser sur lit de poudre (crédits photo : Christoph Wilsnack/Fraunhofer IWS)
Les équipes concluent : « La technologie de fabrication additive est particulièrement adaptée à la complexité mécanique requise pour les RFQ et offre une grande liberté de conception et d’optimisation pour répondre aux exigences strictes de fabrication qui ne peuvent être atteintes par les technologies conventionnelles. Cela ouvre également la voie à des améliorations majeures du RFQ et, à terme, une production en taille réelle, même en utilisant du cuivre pur, qui est un matériau technologiquement exigeant. » L’impression 3D pourrait donc avoir un impact significatif dans la fabrication des accélérateurs de particules de demain ! Retrouvez l’ensemble des travaux de l’équipe ICI.
*Crédits photo de couverture : Christoph Wilsnack/Fraunhofer IWS
Que pensez-vous de ce prototype de quadripôle radiofréquence imprimé en 3D ? Partagez votre avis dans les commentaires de l’article ou avec les membres du forum 3Dnatives. Retrouvez toutes nos vidéos sur notre chaîne YouTube ou suivez-nous sur Facebook ou Twitter !