Quels sont les projets d’impression 4D ?
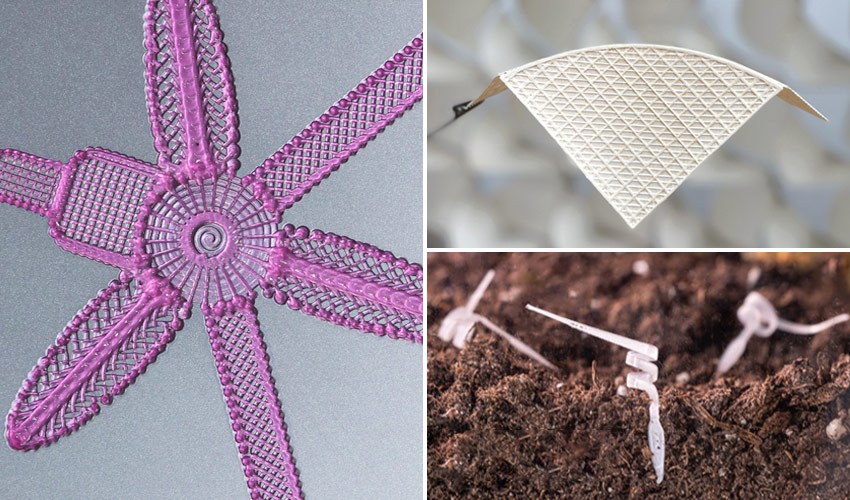
Avez-vous déjà entendu parler de l’impression 4D ? Elle s’appuie sur l’impression 3D traditionnelle et intègre une dimension supplémentaire : le temps. Cela signifie que l’objet fini ne reste pas statique, mais peut changer de forme, de couleur ou de taille en réaction à un stimulus externe. Lancée en 2013, l’impression 4D doit ses origines à Sklyar Tibbs du Self-Assembly Lab du MIT, qui fait toujours partie des chefs de projet les plus actifs, même si le domaine a beaucoup évolué entre-temps. Mais quels sont les projets existants ? Dans notre liste ci-dessous, nous avons examiné de plus près différents projets d’impression 4D qu’ils concernent des applications et des matériaux.
Mizzou Engineering développe un implant grâce à un matériau intelligent
Dans le cadre d’une étude publiée au début de l’année, une équipe de chercheurs de Mizzou Engineering a réussi à développer un implant médical par impression 4D. L’implant peut être entièrement personnalisé et, grâce à la composition de son matériau, il favorise également la régénération des tissus mous. Dans ce cas, les scientifiques ont misé sur un élastomère à mémoire de forme biorésorbable. Cela a permis de répondre aux besoins du patient et d’indiquer un traitement optimal : « Nous avons conçu un modèle in vitro du patient et l’avons implanté par voie intravasculaire dans un cœur imprimé en 3D du patient afin de montrer une preuve de concept de la manière dont le matériau pourrait être utilisé pour ce problème », explique Alireza Mahjoubnia, doctorant en génie mécanique. « Le matériau peut changer de comportement en fonction des conditions physiologiques. Nous programmons sa forme pour qu’il passe par un cathéter et, une fois qu’il est passé dans l’oreille gauche du cœur, il peut revenir à sa forme initiale, en présentant un comportement de mémoire de forme« .
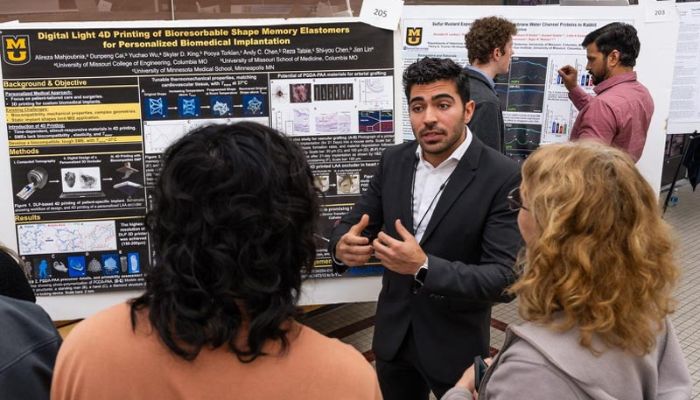
Crédits photo : université du Missouri
Impression 4D pour la régénération osseuse
En Chine, un groupe de chercheurs a étudié la possibilité de créer des échafaudages biopiézoélectriques 4D intelligents pour la régénération osseuse. La piézoélectricité dans les os humains est un facteur clé de la régénération osseuse. C’est pourquoi les matériaux biopiézoélectriques ont suscité une grande attention dans la réparation des os endommagés. Cependant, les stratégies de fabrication traditionnelles se heurtent encore à des limites dans la production d’échafaudages sur mesure, ce qui entrave leur application clinique. Les chercheurs ont donc étudié l’utilisation de l’impression 3D et 4D pour la fabrication d’échafaudages biopiézoélectriques dans des structures de forme plus complexe. En particulier, les échafaudages 4D peuvent fournir des tissus programmables en fonction du temps en réponse à des stimuli externes pour la régénération osseuse. Ces implants intelligents modifient la forme, les propriétés et la fonctionnalité lors de l’ingénierie du tissu osseux et pourraient donc être utilisés comme implants de nouvelle génération.
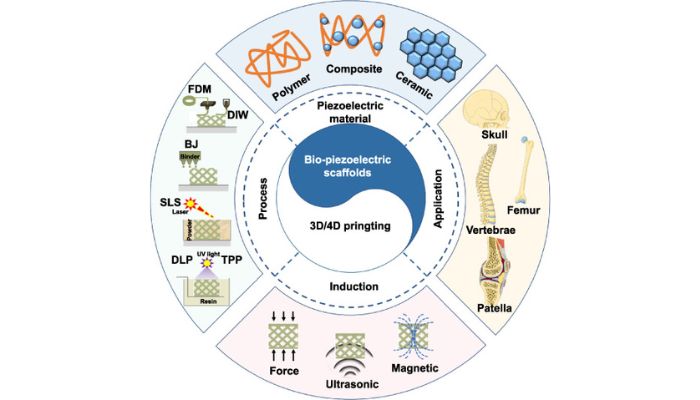
Matériaux piézoélectriques, procédés d’impression et applications possibles pour les implants 4D. (crédits photo : Annan Chen et al 2023 Int. J. Extrem. Manuf.)
Des dispositifs 4D qui imitent le mécanisme des plantes
La prochaine application de l’impression 4D vient d’un groupe de chercheurs de l’Institut Wyss et de la School of Engineering and Applied Sciences, deux institutions de l’Université de Harvard. L’équipe a trouvé un moyen d’imiter les changements dynamiques des plantes et des fleurs en réponse à l’humidité et à la température à l’aide de composites hydrogels imprimés en 4D. À cette fin, ils ont mis au point une encre composée de fibrilles de cellulose alignées, extraites du bois et configurées selon le modèle mathématique de l’impression 4D. Cette encre encode des propriétés d’expansion et de rigidité qui permettent de programmer le comportement d’expansion lorsque les impressions sont immergées dans l’eau. De même, il est possible d’utiliser différents matériaux hydrogels et de remplacer les fibres de cellulose par d’autres charges, par exemple conductrices. Parmi les applications, on peut citer les dispositifs médicaux qui prennent des formes programmées au contact de fluides corporels, les textiles intelligents, l’électronique souple, les capteurs et les actionneurs électriques.
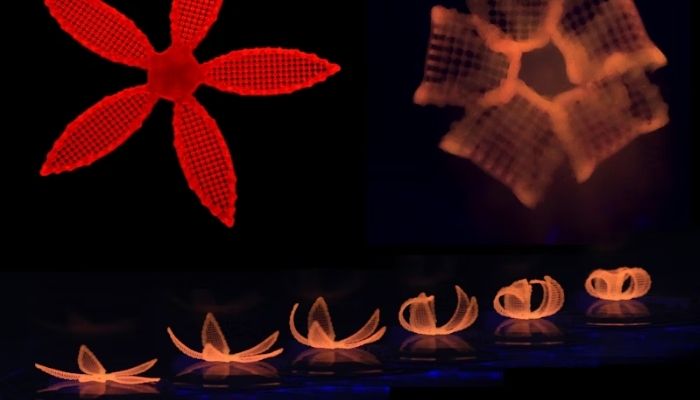
Crédits photo : Wyss-Institut
Technologie d’impression 4D pour la robotique
Les chercheurs Dr Liwen Zhang et Dr Ruirui Quiao de l’Université du Queensland ont développé une technologie d’impression 4D qui produit des métaux liquides pour la robotique qui changent de forme à l’aide d’une lumière proche de l’infrarouge. Les polymères métalliques, qui peuvent effectuer des tâches mécaniques grâce à un laser infrarouge, en sont au stade de la recherche, mais offrent un potentiel pour l’aérospatiale et la médecine, par exemple pour la fabrication de muscles artificiels. Les résines d’impression sont fabriquées avec des nanoparticules métalliques rondes qui réagissent à la lumière infrarouge. Elles peuvent ainsi être contrôlées et déplacées. Les nouvelles méthodes de fabrication du laboratoire permettent de créer des designs flexibles tout en étant solides. Le Dr Zhang souligne : « L’impression 4D ajoute une nouvelle dimension à l’impression 3D traditionnelle – la dimension du temps. Notre méthode nous permet de créer des métaux liquides intelligents qui peuvent être personnalisés, façonnés et modifiés au fil du temps, sans avoir besoin de câbles ou de circuits« . La technologie sera en outre utilisée pour la robotique douce et les technologies connexes afin d’imiter les mouvements et les interactions naturels.
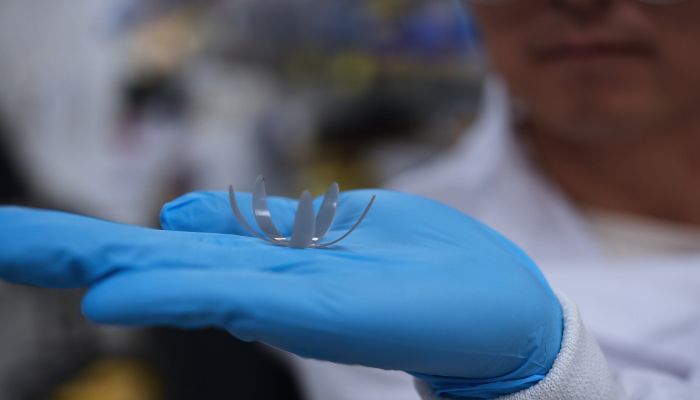
La structure 4D qui se met en mouvement sous l’effet de la lumière proche infrarouge. (crédits photo : Institut australien de bioingénierie et de nanotechnologie Université du Queensland)
L’impression 4D pour l’espace
Zortrax a travaillé pendant plus d’un an sur un projet d’impression 4D financé par l’Agence spatiale européenne afin de développer des mécanismes électriques par impression 3D permettant le pliage, la rotation et le déploiement. En 2013 déjà, des structures insérables en 4D avaient été étudiées, qui devaient bouger sous l’effet de la chaleur. Cependant, le projet a rencontré de nombreuses difficultés, car le processus était difficilement contrôlable et s’activait déjà à 40°C. Ce problème a été résolu grâce à l’utilisation de nouveaux matériaux, logiciels et imprimantes 3D. Les matériaux utilisés sont des polymères à mémoire de forme, dont la température de transition vitreuse est de 75°C, et le filament conducteur FIBERFORCE NYLFORCE Conductive, qui agit comme un chauffage et déclenche l’effet de mémoire de forme. Côté imprimante 3D, c’est la M300 Dual qui a été choisie. Le design a été conçu pour ressembler à un ressort afin de générer un couple suffisant pour que le châssis imprimé en 3D puisse tourner sans frottement. Cette avancée offre un grand potentiel dans le domaine spatial, car elle pourrait réduire le poids des antennes ou des capteurs et le processus pourrait être appliqué à des mécanismes plus grands. Actuellement, le projet en est encore au stade de la recherche.
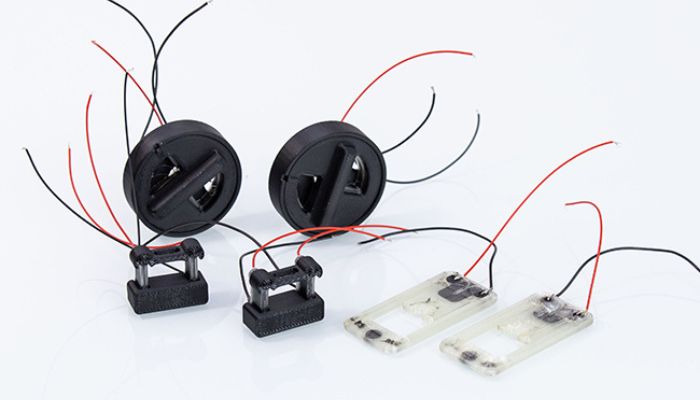
Démonstrateurs de la technologie d’impression 4D. (crédits photo : Zortrax)
Le robot I-Seed
Des chercheurs de l’Institut italien de technologie (ITT) ont mis au point le robot I-Seed à l’aide de l’impression 4D. Inspiré des graines de plantes, ce robot est capable d’analyser et de surveiller la température et l’humidité du sol et de l’air, et de détecter la présence de polluants. Concrètement, I-Seed a été construit en imitant le fonctionnement d’un géranium sud-africain et est capable de changer de forme lorsqu’il absorbe de l’humidité. Les chercheurs ont imprimé le robot en utilisant le procédé FDM avec des polymères biodégradables à base de polycaprolactone. Lors de la conception de I-Seed, ils ont imité les propriétés biomécaniques de la plante africaine afin que ses dimensions et ses performances soient aussi proches que possible de celles d’une vraie graine.
Objets auto-assemblés imprimés en 4D par le MIT
Comme nous l’avons déjà mentionné, les origines de l’impression 4D peuvent être attribuées à Skylar Tibbs et au MIT Self-Assembly Lab. Il ne faut donc pas s’étonner que ce laboratoire reste extrêmement important dans le domaine de l’impression 3D, avec de nombreux projets différents, dont un projet plus ancien (datant de 2013 !), mais qui jouit d’un statut culte dans le secteur : des cubes auto-assemblés imprimés en 4D. Ceux-ci sont constitués de polymères composites hydro-réactifs contenant des éléments hydrophiles et des éléments rigides non actifs. Lorsque la chaîne entre en contact avec de l’eau, elle est capable de prendre une nouvelle forme, celle d’un cube. Depuis, le laboratoire a poursuivi ses travaux et, plus récemment, a notamment mis au point un vêtement en tricot 4D.
Structures bistables imprimées en 4D
À l’EHT Zurich, le doctorant Tim Chen s’est penché sur la conception de systèmes imprimés, utilisables et actifs dans le cadre d’un projet de recherche. Il s’est d’abord concentré sur l’exploration de la conception de ces structures imprimées en 4D et visait à contrôler ses matériaux de manière à ce que les pièces réagissent à l’environnement. Il a misé sur des liaisons bistables au sein de ses structures, qui peuvent provoquer un changement de forme des structures. De telles modifications souhaitées des formes pourraient s’avérer profitables pour diverses applications, dont l’architecture, la robotique logicielle, l’aérospatiale et l’industrie automobile.
Structures d’hydrogel 4D pour une implantation précise
Une étude récemment publiée dans la revue Nature Communications décrit le développement de polyuréthanes dynamiques et thermodurcissables pour l’impression multi-matériaux 4D dans le but de créer des structures de soutien pouvant être implantées de manière peu invasive. L’équipe de recherche a mis au point des structures dotées d’une mémoire de forme qui est activée par la température du corps et qui se déforme au contact de l’eau. L’application de ces supports fonctionne de la manière suivante : un modèle 2D est imprimé, qui peut être temporairement réduit à une forme unidimensionnelle pour faciliter l’insertion par un cathéter. Après l’implantation, la température du corps fait revenir le matériau à sa forme 2D initiale. Après hydratation, le matériau se dilate et se transforme en la structure 3D souhaitée, car il ne gonfle plus. Cette combinaison de mémoire de forme, de déformabilité programmable et de propriétés d’expansion et de rigidité rend les polyuréthanes thermodurcissables développés prometteurs pour la fabrication de supports de matériaux de remplissage pour les implants mini-invasifs.
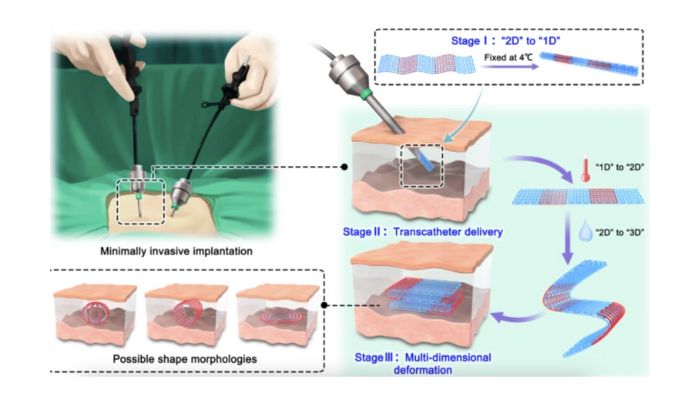
Crédits photo : Nature Communications
Impression 4D et DLP
On vous parle cette fois-ci d’un projet de recherche à partir de résine à mémoire de forme. Les chercheurs ont développé un matériau à base de résine photosensible et de cristaux liquides. Ces derniers permettent à la future pièce imprimée en 3D de se modifier sous l’effet de la température. Concrètement, ils mélangent 5 % en poids de cristaux dans une cuve et de toluène, à une température de 70 °C. Le mélange est refroidi pendant toute une nuit, ce qui permet au toluène de s’évaporer. Le matériau obtenu est alors utilisé avec une imprimante 3D DLP. Et les résultats sont au rendez-vous ! Quand elles sont soumises à de plus fortes températures, les pièces imprimées en 3D se déforment, puis reprennent leur forme initiale quand la température baisse.
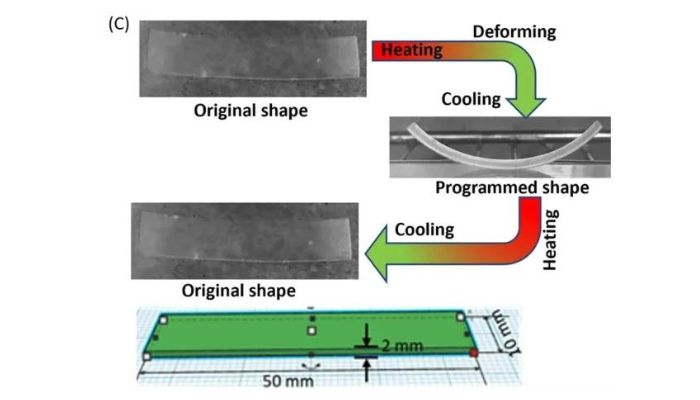
Crédits photo : Nature
Actionneurs magnéto-actifs
Une équipe de scientifiques du CEA-Iramis en France a mis au point des actionneurs en polymères magnéto-actifs grâce à l’impression 4D de matériaux intelligents. Ils ont d’abord mené des expériences et des simulations pour analyser la manière dont les nanoparticules de magnétite s’auto-assemblent en structures câblées dans des résines photosensibles. Les propriétés mécaniques des photopolymères peuvent être ajustées en faisant varier la composition de la résine, et la réponse magnétique peut être modifiée en ajustant la charge des nanoparticules dans la couche imprimée. Les scientifiques ont adapté une imprimante DLP afin d’appliquer un champ magnétique d’intensité et de direction différentes pendant la production de chaque couche. De cette manière, ils ont produit une série d’objets au comportement programmé, comme des actionneurs qui tournaient ou se courbaient sur commande. Ils ont également combiné des roues magnétiques avec des éléments non magnétiques pour créer des actionneurs linéaires ou des pinces actives.
Un procédé d’impression 4D pour les structures hygromorphes
Le comportement hygromorphe est défini par Harvard comme « la réponse aux changements d’humidité de l’environnement par la modification de la géométrie« . C’est pourquoi les structures intelligentes hygromorphes sont très demandées en raison de leurs nombreuses applications possibles, allant des peaux architecturales sensibles aux conditions météorologiques aux « wearables » adaptatifs. Et maintenant, il pourrait être possible de fabriquer ces structures à l’aide de l’impression 4D. Dans un récent article de recherche, des scientifiques montrent comment la fabrication de filaments fusionnés avec des filaments biosourcés remplis de cellulose, de rigidité et de sensibilité à l’humidité variables, combinée à une structuration à mésoéchelle des éléments imprimés, peut contribuer à un actionnement dépendant de l’humidité. Avec une imprimante 3D FFF standard à deux extrudeurs, il a été possible de produire des pièces qui réagissaient à l’humidité relative ambiante et qui pouvaient se plier sur elles-mêmes. Un processus intéressant pour la production de structures imprimées en 4D et réagissant à l’humidité.
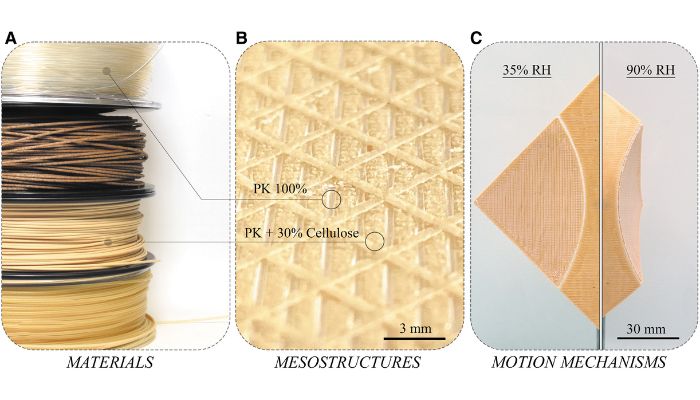
Images montrant les matériaux utilisés, la conception des mésostructures et les résultats des structures hygromorphes. (crédits photo : Tahouani et al.)
Que pensez-vous de ces projets d’impression 4D ? Partagez votre avis dans les commentaires de l’article. Retrouvez toutes nos vidéos sur notre chaîne YouTube ou suivez-nous sur Facebook ou LinkedIn !