#3DExpress : Honeywell se tourne vers l’impression 3D à la française pour ses aubes de turbine
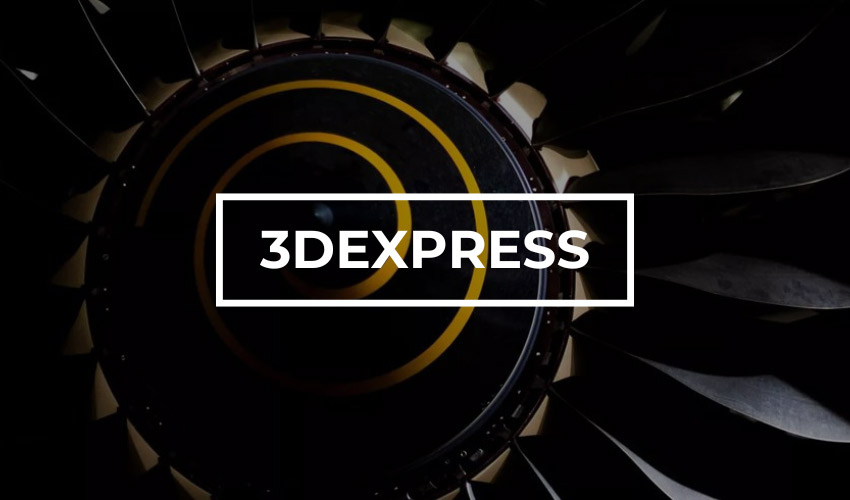
Cette semaine encore le marché de la fabrication additive a été marqué par de nombreuses annonces, lancements de produits et nouveaux partenariats. On peut citer par exemple celui entre le fabricant français Prodways et Honeywell : l’entreprise américaine utilise désormais la technologie d’impression 3D céramique pour concevoir des moules pour ses aubes de turbine. Un processus qui lui permet de réduire ses délais et coûts. On en profitera pour vous présenter également la nouvelle solution de post-traitement de Solukon et les résultats de recherche quelque peu surprenants d’une université espagnole autour de l’alimentation. Bonne lecture à tous !
Honeywell se tourne vers Prodways
La société américaine Honeywell, connue pour ses solutions dans les secteurs du nucléaire, de l’aérospatiale et du bâtiment, s’est tournée vers le fabricant français Prodways pour améliorer le processus de fabrication de ses turbopropulseurs. Elle s’est intéressée à la technologie d’impression 3D céramique pour concevoir des moules servant à produire des aubes de turbine. Avant le recours à la fabrication additive, Honeywell utilisait le processus conventionnel du moulage à la cire perdue, beaucoup plus long et coûteux. Les équipes expliquent en effet qu’elles fabriquent désormais une aube de turbine en 7 à 8 semaines contre un à deux ans auparavant ! De plus, les moules imprimés en 3D seraient plus résistants à l’usure et à la corrosion et permettraient de faire toute une série de tests et de validations beaucoup plus facilement.
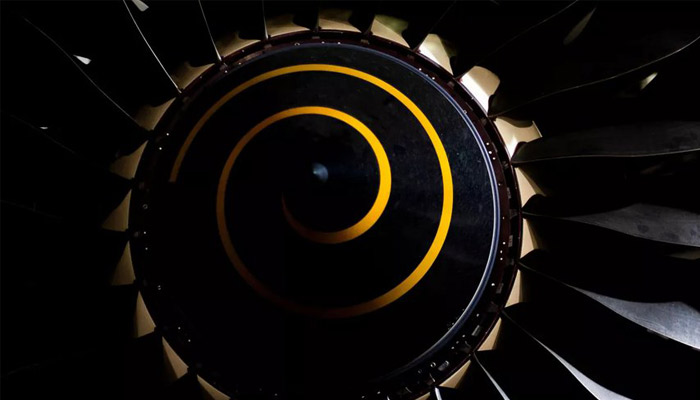
Crédits photo : Honeywell
Solukon améliore sa solution SFM-AT350
Lancée en octobre 2021, la solution de post-traitement SFM-AT350 développée par Solukon a été mise à jour pour offrir une capacité accrue. Le système de dépoudrage est désormais capable de traiter des structures plus grandes et plus lourdes. Alors qu’à l’origine, il ne pouvait traiter que des pièces de 60 kg et de 350 mm sur l’axe X, la nouvelle version prend désormais en charge des pièces de 100 kg et de 400 x 400 x 400 x 400 mm ou de 500 x 280 x 400 mm. Grâce à l’adaptation de la conception du bras, cette nouvelle version conserve le volume de la chambre et la consommation de gaz inerte d’origine. La solution SFM-AT350 est désormais compatible avec des imprimantes 3D telles que l’EOS M 400 et la Nikon SLM® 500, ce qui la rend adaptée aux pièces de taille moyenne dans le cadre de la fabrication additive. Selon l’équipe de Solukon, cette amélioration positionne la SFM-AT350 comme une solution optimale pour les composants complexes dans des industries telles que l’aérospatiale et le médical.
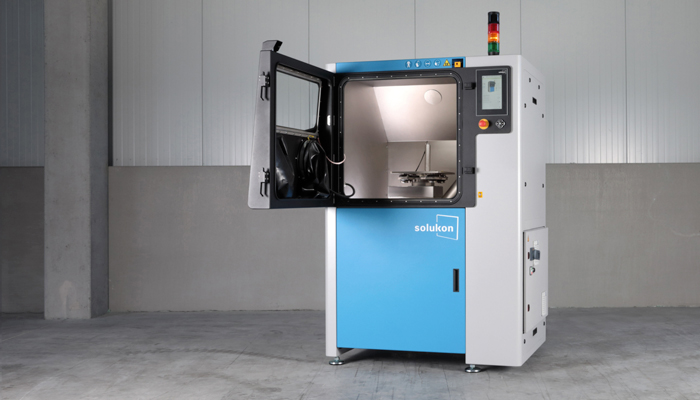
Crédits photo : Solukon
NEVO3D et KIMYA lancent un nouveau matériau pour l’industrie ferroviaire
Comme nous le savons, l’impression 3D est de plus en plus utilisée dans le secteur ferroviaire, car la fabrication additive permet de mettre en œuvre des réparations et d’imprimer des éléments qui ne sont plus fabriqués de manière traditionnelle. Cela contribue à prolonger l’utilisation des éléments existants dans les trains et l’impression 3D permet une maintenance efficace. Les matériaux utilisés doivent toutefois être conformes aux normes en vigueur, notamment les normes de sécurité incendie EN-45545-2 R1/HL3. NEVO3D (anciennement EVO-tech) s’est associé au fabricant de matériaux KIMYA pour aider les Chemins de fer fédéraux autrichiens à appliquer la fabrication additive dans les trains avec un matériau certifié. La nouvelle solution des partenaires est basée sur le polycarbonate et le E-140 et permet d’économiser jusqu’à 80% des coûts. Ce résultat est obtenu d’une part grâce aux coûts réduits des matériaux, et d’autre part grâce aux exigences moins élevées imposées aux imprimantes 3D de traitement. L’objectif des partenaires est de soutenir les Chemins de fer fédéraux autrichiens dans leurs objectifs et de proposer des solutions de matériaux prometteuses pour l’industrie ferroviaire.
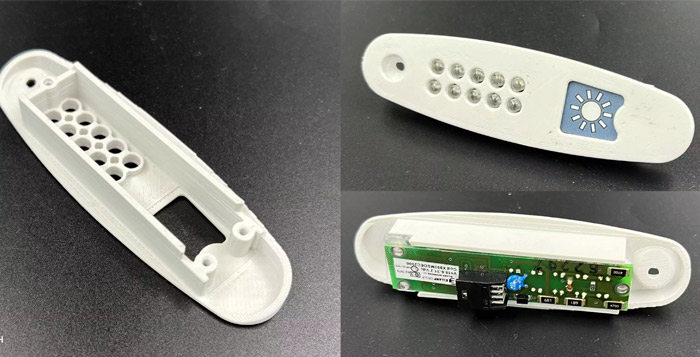
Crédits photo : Chemins de fer fédéraux autrichiens
Impression 3D et préservation de nos océans
Ce n’est plus un secret pour personne, l’impression 3D est de plus en plus utilisée pour préserver notre planète, trouver des solutions de recyclage ou encore sauver nos océans et la biodiversité. Le projet mené par Eke Panuku et QOROX en Nouvelle-Zélande est un nouvel exemple des possibilités offertes par les technologies 3D, ici plus spécifiquement par l’impression 3D béton. Les deux partenaires ont imaginé des banales artificiels, c’est-à-dire des crustacés marins, qui forment des microhabitats et donc servent de refuge à différentes espèces marines. Les deux entreprises ont eu recours au procédé développé par CyBe Construction.
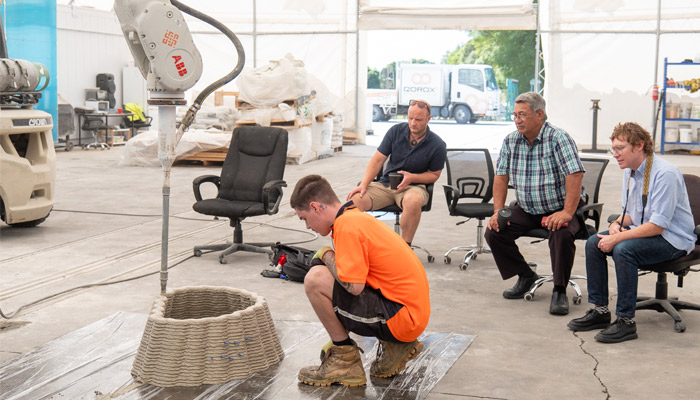
Crédits photo : QOROX
Une étude alimentaire menée grâce à l’impression 3D
En Espagne, plus spécifiquement à l’Universitat Rovira i Virgili à Tarragone, une équipe de chercheurs s’est penchée sur les effets de la poudre d’insectes comestibles ajoutée dans des produits alimentaires. Pour cela, elle a conçu plusieurs snacks salés à partir d’une imprimante 3D alimentaire et de différentes pâtes contenant cette fameuse poudre. La première intégrait du ver de farine tandis que l’autre comportait de la poudre de criquet. Les résultats de ces recherches montrent que la poudre d’insectes modifie les propriétés technologiques et sensorielles des aliments et pourrait ouvrir à de nouvelles innovations dans le secteur alimentaire. Un projet qui montre également comment l’impression 3D peut être utilisée à des fins de recherche, même en cuisine !
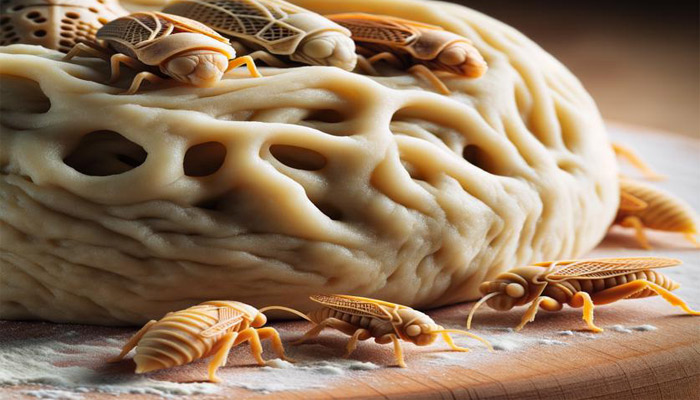
Crédits photo : Natural Science News, 2024
Que pensez-vous du partenariat entre Prodways et Honeywell ? N’hésitez pas à partager votre avis dans les commentaires de l’article. Retrouvez toutes nos vidéos sur notre chaîne YouTube ou suivez-nous sur Facebook ou Twitter !