Production de masse et impression 3D : où en sommes-nous ?
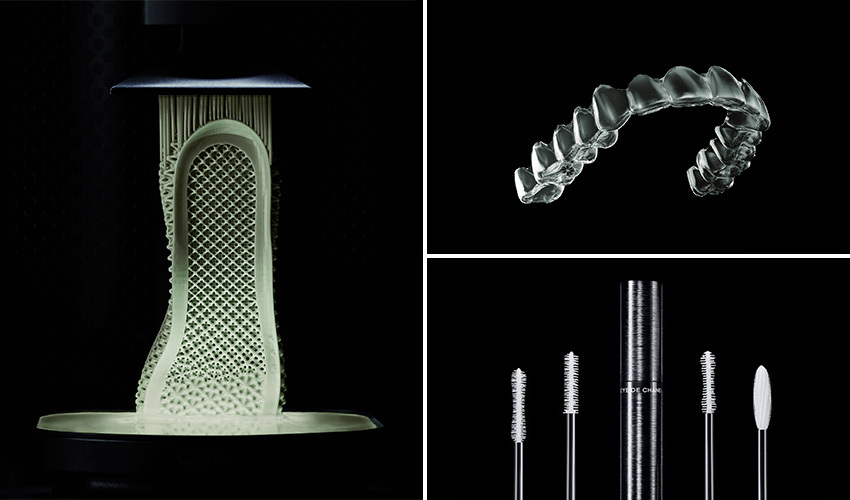
L’impression 3D ne se limite plus à la création de prototypes ; elle s’invite désormais dans la fabrication de pièces finales. Longtemps perçue comme inadaptée à la production en grande série en raison des coûts et des délais, cette technologie prouve aujourd’hui qu’elle peut allier qualité, personnalisation et efficacité. De nombreuses entreprises exploitent déjà son potentiel pour produire en masse, qu’il s’agisse de composants industriels ou d’articles sur mesure. Nous avons ainsi étudié plusieurs exemples où la fabrication additive a permis de réaliser des milliers de pièces en série, bousculant ainsi les méthodes traditionnelles de production.
Adidas et Carbon : production de masse de baskets
En 2016, Adidas s’est allié à Carbon pour transformer la fabrication des chaussures de course. L’année suivante, ils ont dévoilé la Futurecraft 4D, une semelle intermédiaire en maille imprimée en une seule session. Ensemble, ils ont produit 100 000 paires équipées de cette technologie d’impression 3D. En 2018, ils ont introduit l’AlphaEDGE, une version améliorée avec des renforts sous le talon pour mieux absorber la pression exercée par le coureur. En 2021, la collaboration a donné naissance à l’Adidas 4DFWD, une semelle de troisième génération exploitant l’anisotropie pour optimiser confort et performance. Fabriquée grâce au procédé Carbon DLS™ et composée de l’élastomère EPU 44 – une évolution plus résistante et durable du EPU 41 –, cette semelle est en partie biosourcée (40 %). L’Adidas 4DFWD représente ainsi l’alliance entre innovation, design et durabilité, marquant une nouvelle étape dans l’évolution technologique de la marque.
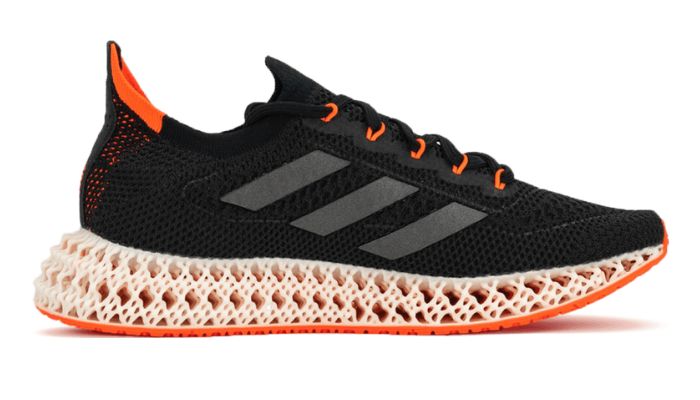
Crédits photo : Carbon
Align Technology utilise l’impression 3D pour la production de masse de dispositifs dentaires
Align Technology illustre parfaitement l’application de l’impression 3D à grande échelle. Spécialisée dans les solutions orthodontiques, cette entreprise américaine est notamment à l’origine des aligneurs Invisalign. Depuis longtemps engagée dans la numérisation et la fabrication additive, elle a acquis en 2011 iTero, un fabricant de scanners intra-oraux, puis en 2024 Cubicure, spécialisé dans les imprimantes 3D à polymères. Partenaire de longue date de 3D Systems, Align Technology utilise l’impression 3D pour produire des moules destinés à ses aligneurs, ainsi que pour concevoir des dispositifs comme un extenseur palatin, directement imprimé en 3D. Avec une capacité de production atteignant un million d’aligneurs personnalisés par jour et plusieurs centaines de milliers de moules fabriqués quotidiennement, l’entreprise démontre comment l’impression 3D peut allier personnalisation et production de masse avec une efficacité impressionnante.
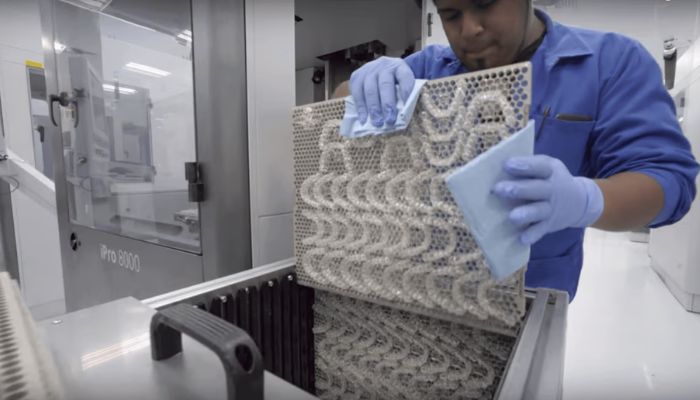
Crédits photo : Align Technology
BOSH Advanced Ceramics
Il est de notoriété publique que la céramique s’est imposée comme un élément clé de l’industrie de la fabrication additive. Bosch Advanced Ceramics a su exploiter les atouts de ce matériau et de l’impression 3D pour accroître la production de composants médicaux de haute précision. Parmi eux, des manchons isolants destinés aux instruments laparoscopiques utilisés en chirurgie invasive. Après une phase d’échantillonnage réussie, l’entreprise est parvenue à imprimer 1 400 composants en un seul lot, lui permettant ainsi de satisfaire une demande annuelle pouvant atteindre 20 000 unités. Le développement de ces manchons a représenté un défi en raison de leurs dimensions réduites, avec un diamètre extérieur de seulement 1,3 mm et une épaisseur de paroi de 90 microns. Pour garantir ce niveau de précision, Bosch Advanced Ceramics a eu recours à la technologie DLP de Lithoz, un procédé de photopolymérisation couche par couche permettant la fabrication de géométries complexes avec un contrôle qualité et une exactitude optimaux.
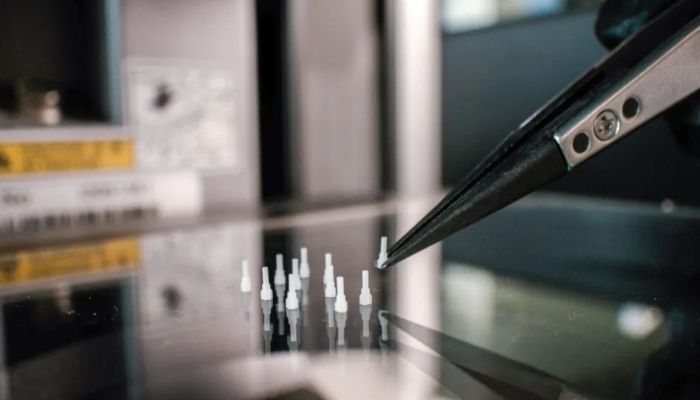
Composants céramiques imprimés en 3D prêts à être utilisés dans des instruments de laparoscopie (Credits photo : Lithoz)
Chanel et ses brosses de mascara imprimées en 3D
Vous vous souvenez peut-être du mascara Volume Révolution de Chanel : lancé en 2018, celui-ci a la particularité d’intégrer une brosse imprimée en 3D. Le projet avait fait couler beaucoup d’encre à l’époque parce qu’il s’agissait d’une véritable production en série. En effet, Erpro 3D Factory, la startup à l’origine de l’impression des brosses, affirmait qu’elle pouvait concevoir 250 000 brosses chaque semaine grâce à une quinzaine de machines. Depuis ce projet, les deux marques ont lancé E.Y.E, un service sur-mesure de mascaras imprimés en 3D. Concrètement, grâce à une application sur tablette, il est possible de choisir sa brosse mascara parmi 10 modèles, en fonction de ses besoins et de ses envies de maquillage. Celle-ci est alors imprimée en 3D avec du PA 11. On ne sait pas exactement combien de brosses ont été imprimées en 3D à ce jour, mais ce qui est sûr, c’est que cet exemple montre bien tous les avantages de la fabrication additive et qu’il est possible d’allier personnalisation et production de masse !
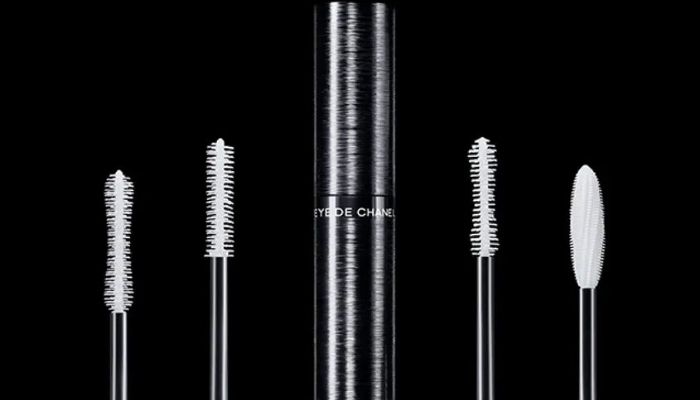
Crédits photo : ERPRO / Chanel
Cobra transforme le monde du golf grâce à l’impression 3D en métal
L’entreprise a dévoilé le premier putter fabriqué en série à l’aide de la technologie HP Metal Jet, ouvrant ainsi la voie à une nouvelle ère pour l’équipement de golf. Son objectif : allier innovation et production à grande échelle tout en maintenant des coûts maîtrisés. Depuis plusieurs années, Cobra Golf explore les possibilités offertes par la fabrication additive pour concevoir des clubs toujours plus performants. Grâce à la technologie HP Metal Jet, ses ingénieurs bénéficient d’une liberté de conception inédite, leur permettant d’imaginer des structures impossibles à produire avec des méthodes traditionnelles. Jadis limitée aux prototypes, l’impression 3D métallique atteint désormais une qualité et une rapidité suffisantes pour une production à grande échelle. En collaboration avec HP, Cobra a pu accélérer le développement de ses clubs et les rendre accessibles au grand public.
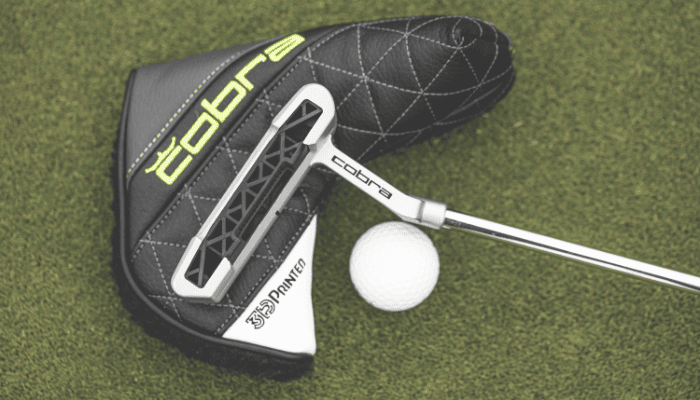
Crédits photo : HP
GE Aviation
GE Aviation a réalisé des avancées majeures dans la fabrication additive. Son usine d’Asheville, en Caroline du Nord, a produit plus de 100 000 composants de turbines en composites à matrice céramique (CMC), tandis que celle d’Auburn, en Alabama, a fabriqué plus de 100 000 composants de tuyères grâce à cette technologie. Le CMC, un matériau composé de fibres de carbure de silicium, est trois fois plus léger que les alliages métalliques classiques et résiste à des températures deux fois plus élevées. Ces propriétés améliorent l’efficacité thermique des moteurs, réduisant ainsi la consommation de carburant et les émissions de carbone. L’usine d’Asheville, pionnière dans la fabrication additive de composants de moteurs à réaction en CMC, a lancé sa production en 2014. De son côté, le site d’Auburn a débuté en 2015 la fabrication en série de buses de carburant, devenant ainsi le premier centre de production de masse de l’industrie pour les pièces de moteurs d’avion imprimées en 3D.
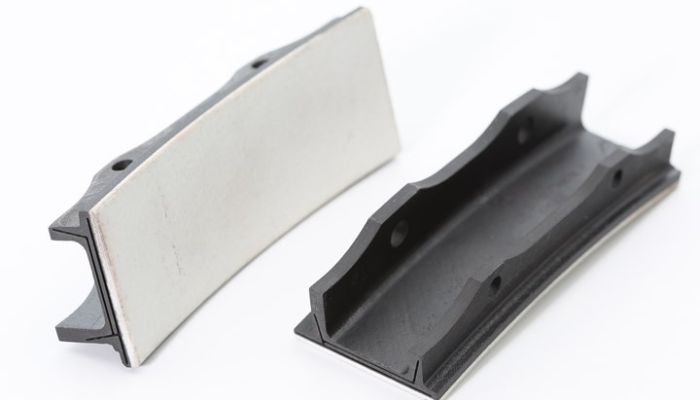
Composants de turbine imprimés en 3D dans le CMC (Crédits photo : GE Aviation)
Photocentric imprime en 3D des badges pour Badgemaster
Un autre exemple d’application de l’impression 3D à la production en série est la collaboration entre Badgemaster, une entreprise britannique, et le fabricant d’imprimantes 3D Photocentric. Face à l’urgence de produire des badges personnalisés dans un délai très court, Badgemaster a opté pour la technologie d’impression 3D à base de résine de Photocentric, en utilisant ses machines LC Magna. Cette approche a permis de fabriquer 30 000 pièces finales rapidement et avec une qualité optimale, sans recourir aux moules ou aux outils traditionnels. Le choix de cette solution s’explique en partie par les contraintes logistiques imposées par la pandémie, qui ont entravé les méthodes de production classiques. Cette collaboration illustre le potentiel de la fabrication additive pour répondre aux besoins industriels en proposant des solutions rapides, flexibles et efficaces, même en situation de forte demande.
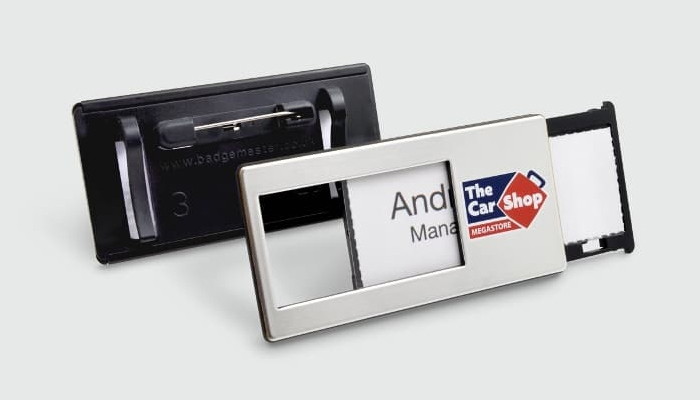
Crédits photo : Badgemaster
Les implants Stryker
Le secteur médical illustre également l’alliance entre impression 3D et production de masse. Depuis 2013, l’entreprise irlandaise Stryker a fabriqué environ 2 millions de prothèses grâce à cette technologie, optimisant ainsi sa production. Elle a mis au point un matériau exclusif, le Tritanium, un alliage de titane spécialement conçu pour l’impression 3D, utilisé pour développer une prothèse de genou sans ciment, le Triathlon Tritanium, ainsi que trois types de prothèses rachidiennes.
Mais en quoi consiste le Triathlon Tritanium ? Cette prothèse associe une conception avancée à une structure hautement poreuse favorisant la fixation biologique. Conçue à l’aide des outils SOMA et fabriquée avec la technologie additive propre à Stryker, elle illustre parfaitement les avantages de l’impression 3D : réduction des coûts, optimisation des ressources et impact environnemental moindre. Allant plus loin dans son engagement, Stryker a rejoint l’Additive Green Manufacturing Trade Association pour encourager l’adoption de procédés de fabrication plus durables dans l’industrie grâce à l’impression 3D.
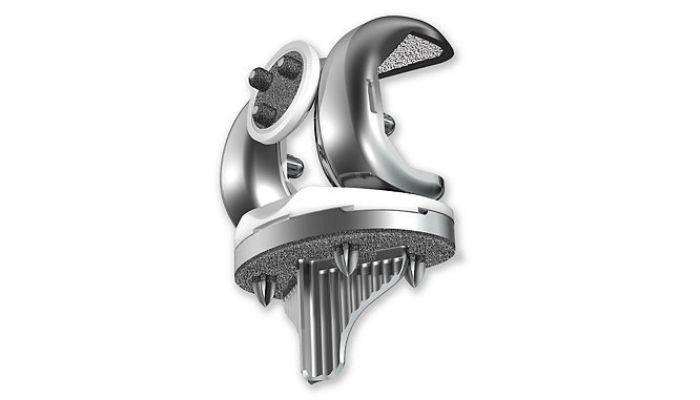
La photo montre le modèle Triathlon Tritanium, l’orthèse de genou non cimentée.
Selon vous, l’impression 3D permet-elle une production de masse ? Partagez votre avis dans les commentaires de l’article ou avec les membres du forum 3Dnatives. Retrouvez toutes nos vidéos sur notre chaîne YouTube ou suivez-nous sur Facebook ou Twitter !