L’ULTEM®/PEI en impression 3D : les caractéristiques de ce thermoplastique haute performance
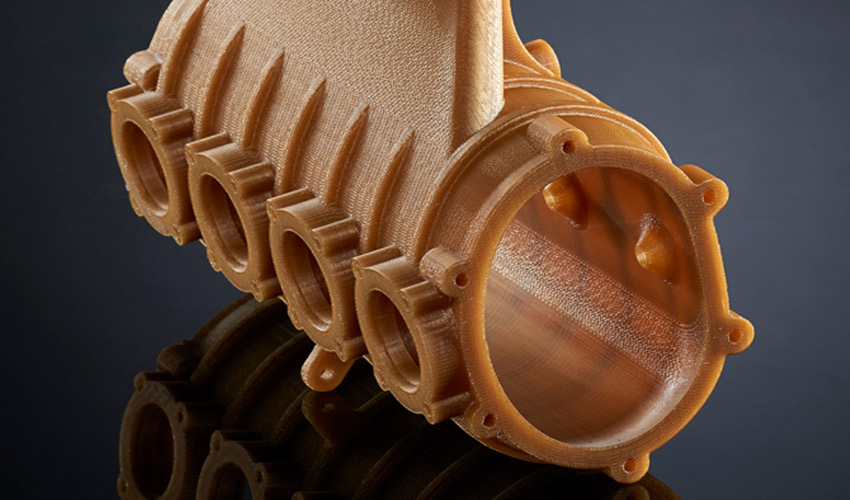
Ces dernières années, l’utilisation de thermoplastiques haute performance a pris une importance croissante dans le secteur de l’impression 3D, la technologie s’éloignant progressivement du prototypage rapide vers la production de pièces finies. En conséquence, les exigences en matière de matériaux d’impression 3D ont augmenté et les thermoplastiques haute performance sont de plus en plus répandus. Leurs propriétés en font une alternative économique à certains métaux et ils sont prisés par de nombreux secteurs comme l’aérospatial et le médical. Au sein de cette famille, on retrouve les Polyaryléthercétone (PAEK), qui peuvent supporter des températures élevées et que vous connaissez peut-être avec le PEEK et le PEKK. Il existe une alternative beaucoup moins chère, le polyétherimide (PEI), un matériau amorphe plus connu sous son nom commercial ULTEM®. Disponible sous forme de filament compatible avec des machines FDM, il est compatible avec certaines machines, notamment celles de Stratasys. Revenons ensemble sur les caractéristiques principales de l’ULTEM.
Le PEI a été développé dans les années 1980 par Joseph G. Wirth et a été commercialisé par la division Plastiques de General Electric sous le nom ULTEM. En 2007, la société cède son activité plastiques à Saudi Basic Industries Corporation (SABIC), qui récupère ainsi le brevet associé. Bien que l’ULTEM® ait convaincu de nombreux industriels grâce à ses propriétés mécaniques, il n’est devenu adapté à la production de masse qu’avec l’avènement des imprimantes hautes performances FDM/FFF. L’extrudeur de celles-ci doit être capable de monter à des températures élevées pour faire fondre le thermoplastique.
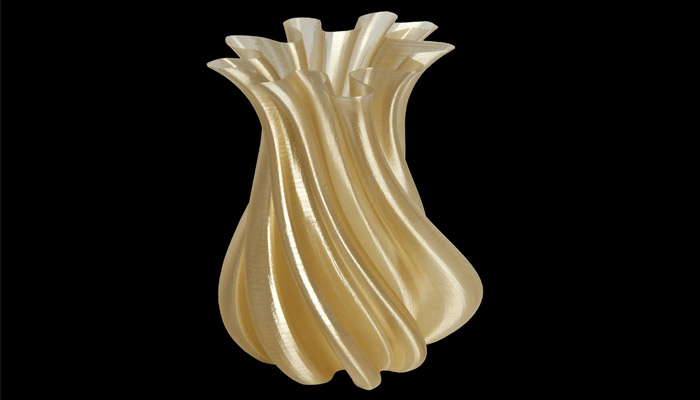
Crédits photo : GEWO3D
Production et caractéristiques de l’ULTEM/du PEI
L’ULTEM® est une famille de matériaux thermoplastiques amorphes fabriqués à partir de Polyétherimide (PEI). L’une de ses caractéristiques principales est son caractère ignifuge : il présente une résistance élevée aux flammes, un faible dégagement de fumée et une faible toxicité. Ces propriétés se manifestent par de très bons résultats aux tests FST (Flame, Smoke, Toxicity). L’ULTEM® possède donc une résistance élevée aux fortes températures, caractérisée par un indice thermique relatif (Relative thermal index, RTI) allant jusqu’à 180°C. L’ULTEM se distingue également par sa grande solidité, rigidité et stabilité dimensionnelle, sa bonne résistance au fluage et son importante résistance chimique. Les différentes variétés d’ULTEM se caractérisent en outre par un rapport poids/résistance élevé, pouvant même remplacer certains métaux grâce à leurs propriétés mécaniques et à leur haut degré d’usinabilité. Ces matériaux existent en différentes couleurs, transparentes ou opaques.
Les matériaux ULTEM conservent leur solidité et résistent à la fissuration par corrosion sous contrainte lorsqu’ils sont exposés aux fluides provenant des automobiles et des avions, aux hydrocarbures aliphatiques, aux alcools, acides et solutions aqueuses faibles. L’ULTEM® 1010 présente quant à lui une haute résistance à la traction, affichant une grande solidité et durabilité. Il est biocompatible et certifié NSF 51 pour le contact alimentaire. Il peut également résister à la stérilisation à la vapeur.
À noter également l’existence des copolymères ULTEM, qui possèdent une résistance à des températures encore plus élevées et s’adaptent aux différents besoins en matière de propriétés chimiques et d’élasticité. SABIC a également lancé une gamme renouvelable certifiée ISCC+. Ces variétés d’ULTEM, conçues à partir de déchets et de résidus, présentent des performances et une usinabilité tout aussi élevées que celles qui sont fabriquées à partir de combustibles fossiles. Mi-2023, les matériaux ULTEM renouvelables représentent plus d’un quart des matériaux ULTEM proposés par SABIC.
SABIC propose aujourd’hui 140 variétés d’ULTEM®. Citons en particulier l’ULTEM™ 9085 CG, employé dans le secteur aérospatial pour l’intérieur des cabines, mais également dans le domaine ferroviaire. L’ULTEM HU1010, pour sa part, est utilisé pour les dispositifs médicaux et les applications pharmaceutiques. Il est biocompatible.
L’ULTEM/le PEI en impression 3D
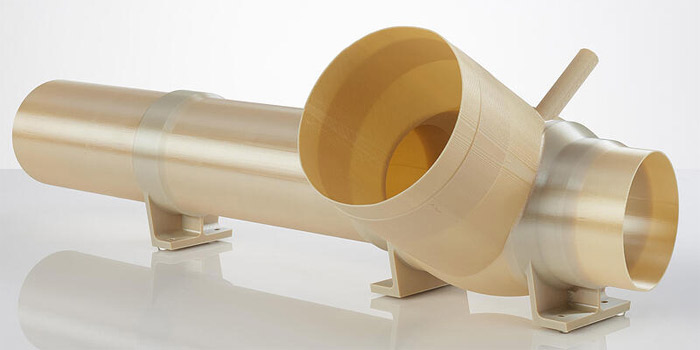
Une pièce imprimée en 3D utilisée sur un lanceur spatial (crédits photo : Stratasys)
La gestion de la température est primordiale quand il s’agit d’imprimer de l’ULTEM®. Celle de la chambre doit être maintenue en permanence, sinon des irrégularités risquent d’apparaître et l’adhésion des différentes couches d’en pâtir. La température de transition vitreuse, à laquelle un polymère amorphe passe d’un état dur/vitreux à un état mou/caoutchouteux, et vice-versa, est très élevée pour l’ULTEM, pouvant atteindre 217°C pour l’ULTEM1010 (185°C pour l’ULTEM9085). Pour un résultat optimal, la température de la chambre d’impression doit être légèrement inférieure à la température de transition vitreuse. Cela garantira que les pièces ont les bonnes dimensions et que leurs propriétés mécaniques sont conservées. Une température trop basse risquerait de conduire à des déformations de la pièce, voire à sa fissuration. Une fois l’impression achevée, la chambre d’impression doit être refroidie lentement et de manière uniforme afin que le refroidissement de la pièce se fasse également de façon progressive.
Les applications de l’ULTEM/PEI
Vous l’aurez compris, le PEI est très employé dans le secteur aérospatial, particulièrement l’ULTEM® 9085 en raison des caractéristiques évoquées ci-dessus. C’est également un matériau de choix dans l’automobile, le médical et le secteur alimentaire, plus particulièrement dans la conception d’ustensiles de cuisine. Ce thermoplastique est aussi très employé dans l’outillage, que ce soit pour concevoir des moules, des gabarits ou fixations diverses. L’entreprise Bombardier, par exemple, a recours à ce matériau pour fabriquer ses outils sur-mesure, personnaliser des composants sur ses chaînes de production mais aussi pour produire des pièces finies pour ses trains.
Les principaux fabricants et les prix
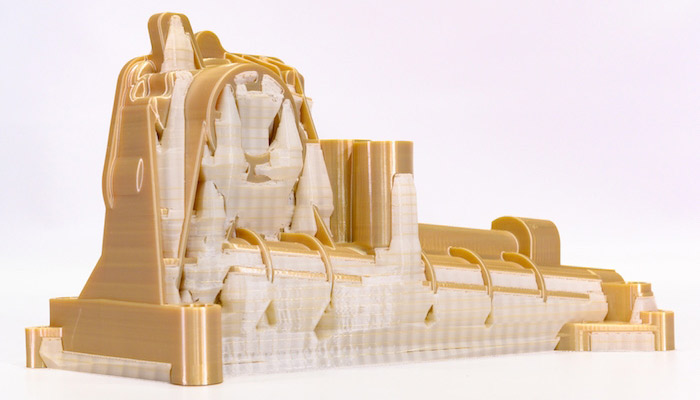
SABIC a développé un support d’impression 3D pour l’ULTEM
Côté fabricants, SABIC fournit la matière brute de l’ULTEM. L’entreprise fabrique ses propres filaments pour la fabrication additive : historiquement, ils n’étaient compatibles qu’avec la gamme de machines de Stratasys mais depuis quelques années, SABIC a noué d’autres partenariats comme avec Roboze, qui peut imprimer le filament ULTEM™ AM9085F. Certains fabricants proposent leurs propres filaments comme KIMYA, 3DXTech ou 3D4Makers.
Enfin, sachez que si vous envisagez d’imprimer avec de l’ULTEM®, le fabricant SABIC a lancé un filament de support détachable, l’AMS31F, plus facile à retirer que les autres matériaux de support, qui nécessitent souvent d’être réchauffés. Ainsi, la pièce peut conserver toutes ses propriétés mécaniques et l’utilisateur gagne un temps précieux.
Si on le compare au PEEK, sachez que le PEI est moins cher : il faut compter 150 euros pour un kilo contre au moins 300 euros pour la même quantité de PEEK. C’est un matériau qui a l’avantage d’être certifié pour un certain nombre d’applications aérospatiales, répondant à des exigences très normées. Toutefois, le PEI présentera une plus faible résistance à l’impact et à la température.
Utilisez-vous l’ULTEM comme matériau d’impression 3D ? N’hésitez pas à partager votre avis dans les commentaires de l’article ou avec les membres du forum 3Dnatives. Retrouvez toutes nos vidéos sur notre chaîne YouTube ou suivez-nous sur Facebook ou Twitter !
Bonjour quelle imprimante 3d serait la mieux adaptée pour ces matetiaux tel que PEI ULTEM 1010