PA11 vs PA12 : quel type de nylon choisir en impression 3D ?
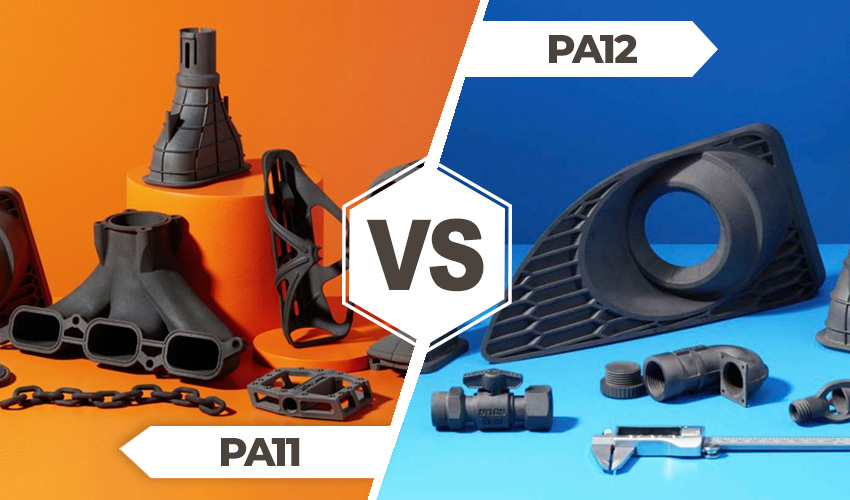
Le nylon, également connu sous le nom de polyamide (PA), est un groupe de polymères thermoplastiques ou de matières plastiques fréquemment utilisé dans l’impression 3D. Le nylon est particulièrement apprécié pour sa capacité à résister à de fortes contraintes mécaniques, sa résistance à la chaleur, à la déchirure et à l’abrasion. C’est pourquoi ce matériau est souvent utilisé dans la fabrication de pièces résistantes, par exemple dans l’industrie automobile et aérospatiale, mais aussi dans le secteur médical. L’impression 3D utilise de nombreux types de nylon, dont les noms varient en fonction du nombre d’atomes de carbone qu’ils contiennent. Le PA6 est le plus souvent utilisé dans l’impression FDM, tandis que les PA11 et PA12 sont utilisés dans les procédés à base de poudre. Bien que les domaines d’application du PA11 et du PA12 se chevauchent, les deux plastiques présentent quelques différences. On vous propose donc de comparer les deux matériaux et d’examiner leurs propriétés respectives, leur origine, leurs exigences en matière d’impression et, enfin, les applications et les catégories de prix.
Origine et propriétés mécaniques
Les polyamides sont différenciés par la nomenclature et le nombre qui suit le code commun PA est fonction du nombre d’atomes de carbone. Le PA11 et le PA12 semblent donc être assez proches l’un de l’autre. Pourtant, les deux types de nylon se distinguent à bien des égards, à commencer par leur origine et leur fabrication. Le PA12 est un thermoplastique, semi-cristallin et linéaire, obtenu à partir de gaz naturel ou de pétrole. Des procédés chimiques permettent d’obtenir du lactame de laurine, qui est la molécule de départ pour la fabrication du PA12. En 1963, les Chemische Werke Hüls AG ont présenté pour la première fois le PA12 en collaboration avec Emser Werke à Domat. Depuis lors, l’homopolymère, qui est constitué d’un seul composant monomère, s’est établi dans de nombreuses applications. Malgré cela, le PA12 se retrouve de plus en plus souvent au coeur des débats en raison de son origine et de son impact sur l’environnement.
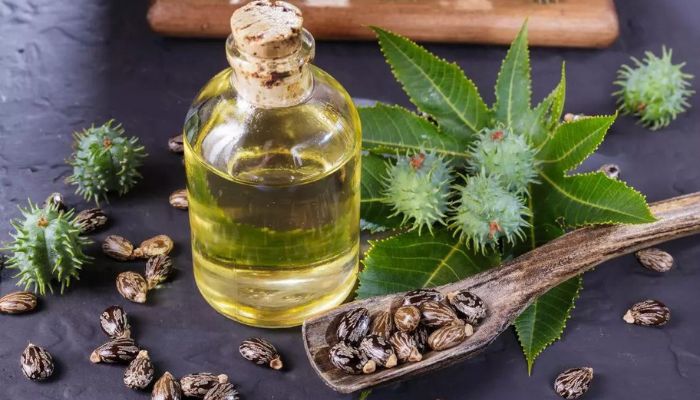
Le PA11 est obtenu à partir d’huile de ricin et est donc considéré comme une alternative plus écologique au PA12. (crédits photo : Jellypipe)
Etant à la recherche d’une plus grande durabilité et d’une production plus « verte », les entreprises se tournent vers des matériaux alternatifs aux propriétés similaires. Cela a contribué à l’essor du PA11, car l’origine de ce polyamide est biologique. Le PA11 est fabriqué à partir de matières premières renouvelables, obtenues à partir de dérivés végétaux. La plupart du temps, on utilise de l’huile de ricin, qui est elle-même obtenue à partir des graines de l’arbre miracle africain « Ricinus communis », en les pressant. L’huile de ricin est ensuite transformée en un acide aminé, l’acide 11-aminoundécanoïque, par synthèse de monomères. La polymérisation ultérieure des monomères donne ensuite naissance au PA11. Celui-ci ressemble donc plutôt au PA6 dans son origine et est très éloigné de son voisin de code, le PA12. Bien que le PA11 soit considéré comme une alternative plus durable en raison de son origine biosourcée, il n’est pas biodégradable. Comme les autres polyamides, il doit être trié dans un système de collecte spécialisé avant d’être traité pour être recyclé.
Bien que les origines du PA11 et du PA12 soient très différentes, leurs propriétés mécaniques se rapprochent, raison pour laquelle ils sont souvent utilisés dans l’industrie à des fins similaires. Les PA11 et PA12 sont ainsi considérés comme extrêmement robustes, solides et résistants et convainquent par leur comportement au glissement et à l’usure ainsi que par leur résistance chimique. Le PA12 est considéré comme le plus léger de tous les plastiques polyamides et se distingue par sa faible concentration en groupes amides. En outre, le PA12 surpasse les autres polyamides en termes de faible absorption d’eau et de densité. Bien que le PA11 absorbe lui aussi relativement peu d’eau pour un polyamide, il ne peut pas rivaliser avec le PA12 à cet égard. Ses avantages résident dans ses propriétés mécaniques, qui surpassent celles du PA12. Le PA11 présente une grande ductilité et une excellente résistance aux chocs. Il est très résistant à l’abrasion et à la fatigue, et les pièces en PA11 brillent par une isotropie plus élevée. Il résiste à des températures maximales de 190° C, même si les températures permanentes se situent entre -40° C et 125°C. Les pièces PA11 finies sont à la fois solides et flexibles, durables et présentent une surface mate de couleur opaque. Nous retrouvons également cette dernière dans les pièces en PA12. Dans les deux cas, les pièces peuvent être colorées.
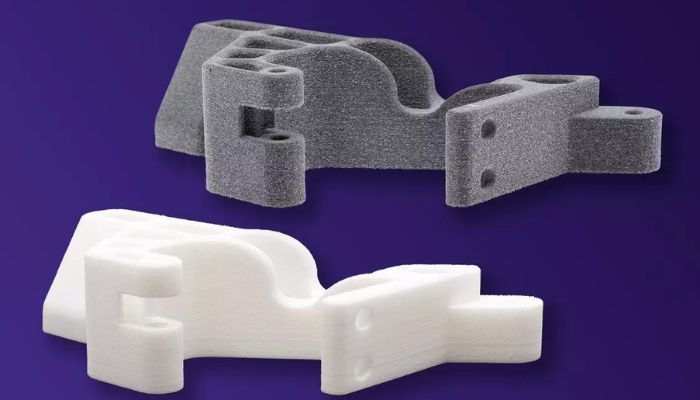
Le PA 12 (blanc) est le type de nylon le plus léger, tandis que le PA 11 (gris) présente de meilleures propriétés mécaniques. (crédits photo : Jellypipe)
En ce qui concerne la température d’utilisation, le PA12 s’en sort moins bien que le PA11, car s’il résiste à la plage extrême de -50°C – 150°C, sa température d’utilisation en continu n’est que de 50-80°C. Comme le PA11, il est également très résistant à l’abrasion et présente une résistance élevée à la fatigue. Il résiste aux graisses, aux huiles, aux solvants, aux alcalis et aux solutions salines, ce qui rend les pièces fabriquées en PA12 très résistantes à l’usure et faciles à souder et à coller. Le PA12 n’est pas seulement le PA le plus léger, il est aussi le plus résistant à la fissuration sous contrainte. Bien que le comportement aux chocs du PA12 soit très bon, il ne peut pas tout à fait égaler celui du PA11. En comparaison directe avec le PA11, le PA12 n’est pas non plus tout à fait à la hauteur en termes de résistance et de dureté. C’est pourquoi le PA12 est souvent renforcé par des additifs tels que des fibres de verre ou de carbone, afin de compenser ce défaut.
Ces deux matériaux sont généralement compatibles avec les tissus et les pièces fabriquées à partir de ceux-ci conviennent au contact avec la peau humaine. Il convient toutefois de mentionner que le PA12 de certains fabricants peut donc être utilisé pour des pièces en contact avec les aliments, ce qui n’est pas toujours le cas du PA11. Il existe cependant des poudres de PA11, comme le PA11 Blue d’APC-Tec, qui sont autorisées par la FDA pour le contact alimentaire.
Impression 3D avec du PA11 et PA12
Dans l’impression 3D, le PA est principalement utilisé sous forme de filament et de poudre. Nous trouvons également de la résine PA pour le procédé SLA, qui imite les propriétés des thermoplastiques PA. Le filament PA concerne le plus souvent le PA6, qui est principalement disponible sous cette forme et seulement de manière limitée sous forme de poudre, ce qui peut également entraîner des problèmes de traitement. En revanche, les procédés basés sur la poudre utilisent en premier lieu les PA11 et PA12. Cela s’explique par les propriétés thermoplastiques du matériau, car le nylon se laisse particulièrement bien déformer ou assembler par la chaleur. Parmi ces procédé, on retrouvera le frittage sélectif par laser (SLS), le Multi Jet Fusion, la fusion par absorption sélective (SAF) ou encore le High Speed Sintering (HSS). Ils se caractérisent par une productivité élevée et la poudre non utilisée pour les pièces peut être recyclée dans une certaine mesure.
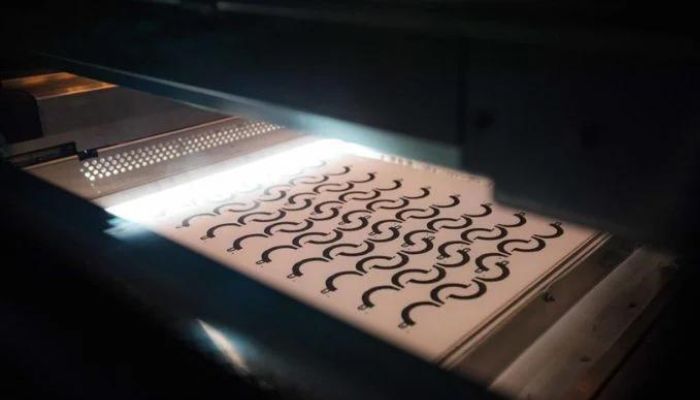
Le procédé MJF (crédits photo : Hubs)
Le PA12 a tendance à être plus souvent utilisé en fabrication additive que le PA11 de par sa disponibilité plus ancienne mais aussi par son point de fusion plus bas. Le PA12 fond à 175-180° (selon le fabricant), alors que le PA11 ne fond qu’à environ 200°. Ces différences de température de fusion expliquent également pourquoi on ne peut pas mélanger les poudres entre elles pour une même impression. Le traitement des poudres est un défi pour ces procédés d’impression 3D, bien que la plupart des fabricants proposent des solutions type Build Unit spécifiques pour chaque matériau.
Post-traitement
Quel que soit le procédé que vous choisissez pour l’impression PA11 et PA12, le post-traitement est une étape indispensable. Il n’y a donc pas de différence entre les matériaux sur ce point, car certaines étapes de finition sont obligatoires pour les deux. La première étape est le dépoudrage, qui consiste à retirer les pièces du gâteau de poudre et à aspirer la poudre tout autour. Celle-ci peut alors être recyclée dans une certaine mesure pour un nouveau batch d’impression. Différents procédés permettent ensuite d’étendre le nettoyage des pièces, car il reste toujours un peu de poudre résiduelle sur les pièces, et d’améliorer l’état de surface. Il est également possible, dans une étape ultérieure, de peindre ou de colorer les pièces en PA11 et PA12.
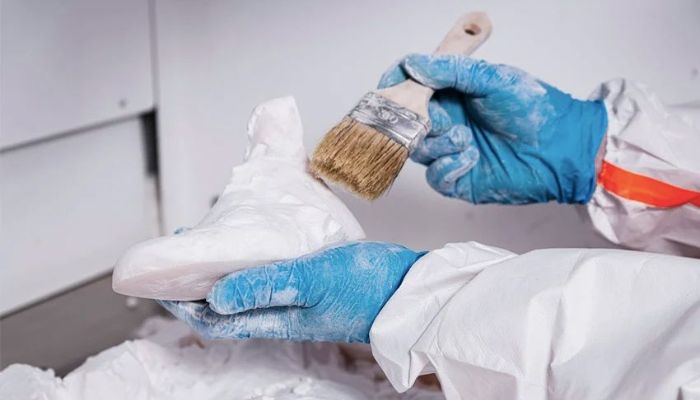
Une étape importante de tous les procédés à base de poudre est le post-traitement. (crédits photo : Protiq)
Les applications du PA11 et du PA12
Les deux matériaux appartenant au même groupe de matières plastiques se retrouvent dans une multitude d’applications dans le processus d’impression 3D, avec quelques recoupements concernant leurs champs d’application.
Dans le domaine médical, les poudres PA11 et PA12 sont utilisées dans la mesure où elles sont déclarées biocompatibles par le fabricant. Elles sont utilisées pour la fabrication de prothèses, d’orthèses, de dispositifs médicaux et d’appareils médicaux. Dans le domaine médical, le PA 11 est toutefois plus apprécié pour sa biocompatibilité et sa flexibilité que le PA12, qui présente en revanche une résistance généralement plus élevée.
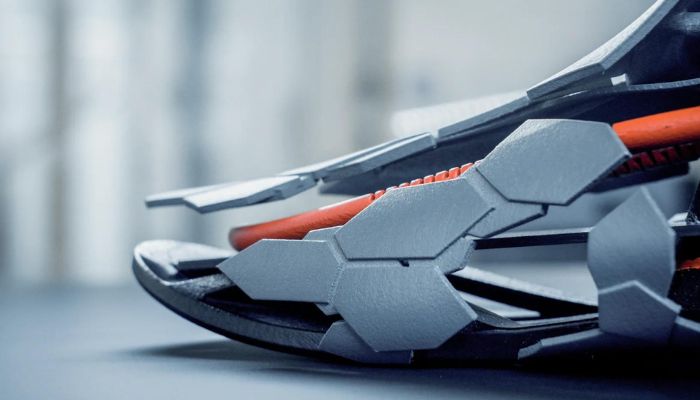
Le PA11 et PA12 sont souvent utilisés pour les prothèses et les orthèses. (crédits photo : EOS)
Les deux matériaux sont également utilisés dans l’industrie automobile. Le PA11 est prisé pour les pièces destinées au prototypage de véhicules, mais aussi pour la production en série. En raison de sa résistance aux chocs et aux produits chimiques, il est également utilisé pour la fabrication de pièces de véhicules en cas de collision, à l’intérieur (le PA11 ne se fend pas), mais aussi à l’extérieur, par exemple pour les joints, les composants de moteur et les revêtements. Le PA12 est également employé en impression 3D automobile, à savoir pour la construction de véhicules, en particulier pour les tuyaux et les tubes de précision, notamment les conduites de carburant résistantes à la pression et aux chocs. Dans l’aéronautique, le PA11 est utilisé dans l’impression 3D en raison de sa résistance aux chocs et de sa légèreté, comme les carénages et les pièces structurelles internes des avions. Le PA12 est également idéal pour la fabrication de tuyaux et tubes de précision – en particulier pour les conduites de carburant résistantes à la pression et aux chocs. Dans les secteurs de l’automobile et de l’aéronautique, le PA11 est apprécié, contrairement au PA12, pour les pièces plus légères qu’il produit et sa contribution à l’efficacité énergétique, tandis que les avantages du PA12 résident dans sa rigidité et sa dureté pour les pièces nécessitant davantage de résistance.
L’industrie du sport utilise également les deux matériaux : le PA11 pour sa résistance à l’abrasion, par exemple pour les revêtements de ski et les semelles de chaussures de football, et pour sa bonne flexibilité. Le PA12 est utilisé pour les équipements de sports d’hiver, tels que les chaussures de ski alpin et de ski de fond ou les fixations de ski, en raison de sa résistance mécanique particulière à basse température.
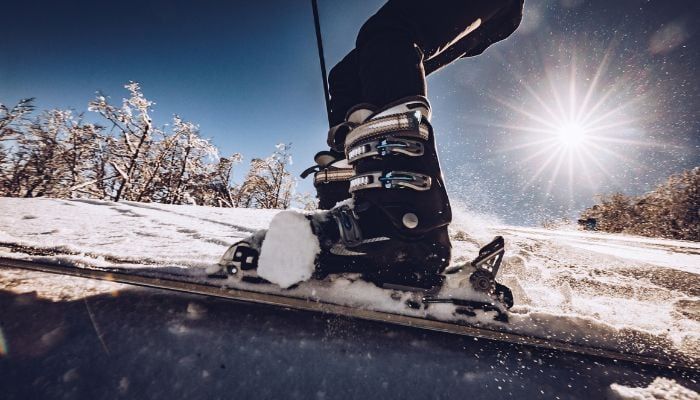
Le PA11 et PA12 sont également utilisés dans le domaine du sport. (crédits photo : Prodways/Salomon)
Dans la construction mécanique, l’électrotechnique ou l’électronique ainsi que dans l’industrie de l’emballage, les deux matériaux sont utilisés, le PA11 étant particulièrement apprécié pour sa longévité et le PA12 pour sa grande ténacité. Le PA12 est utilisé pour la fabrication de tuyaux et de tubes de précision, en particulier pour les conduites de carburant résistantes à la pression et aux chocs ainsi que pour les éléments d’entraînement en milieu humide ou les pièces de transmission sous l’eau – où une grande précision dimensionnelle est nécessaire – ainsi que pour les composants de construction mécanique tels que les charnières et les roues dentées ainsi que les films isolants. Dans l’électrotechnique et l’électronique, le PA11 est utilisé comme matériau d’isolation et de protection pour les câbles, les connecteurs et les boîtiers d’appareils électroniques et, en raison de sa longévité particulièrement élevée, généralement pour des applications hautement techniques.
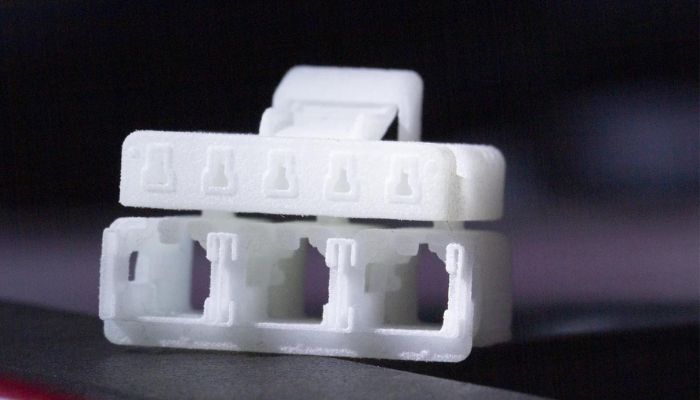
Un connecteur en nylon (crédits photo : EOS)
Fabricants et prix du PA11 et PA12
D’une manière générale, le PA12 est généralement la variante la plus chère de la famille des nylons par rapport au PA11, car la demande de PA11 est actuellement encore faible. Le PA11 peut être acheté chez certains fabricants à partir de 50 €/kg, mais chez d’autres, il faut compter 200 €/kg. Les variations de prix pour le même type de poudre sont liées au fait qu’il s’agit d’une poudre standard ou renforcée. Si l’on compare les prix des pièces finies fabriquées dans les deux matériaux différents, il est facile de constater que les pièces fabriquées en série en PA11 sont nettement moins chères qu’en PA12, d’environ 30% selon la quantité produite. En revanche, pour la fabrication de pièces uniques, il vaut la peine, du point de vue des coûts, d’utiliser le PA12.
Les deux matériaux sont disponibles auprès d’une grande variété de fabricants. Parmi ceux de PA11 les plus connus, on trouve EMS-Grivory ou le groupe français Arkema, qui vend le PA11 sous le nom de RILSAN® PA11. Arkema propose également du PA12, autrefois sous le même nom que le PA11, mais aujourd’hui sous le nom de RILSAMID® pour mieux le distinguer. Le PA12 est également souvent vendu sur le marché sous le nom de VESTAMID® ou VESTOSINT®. Le groupe chimique BASF propose également le PA12 et le PA11 sous forme de poudre. On trouve également du PA12 chez des fabricants comme Evonik, mais aussi chez 3DSystems et Farsoon, qui proposent des poudres développées en collaboration avec des entreprises chimiques, mais qui gardent ces partenariats de développement matériaux confidentiels.
Outre l’invention du matériau PA11, plus respectueux de l’environnement, de plus en plus d’efforts sont déployés par différents fabricants pour rendre la production de PA12 plus biologique et plus verte. Le fournisseur allemand d’équipements et de matériaux EOS, par exemple, propose le PA12 comme une alternative performante aux plastiques ABS ou PA6 appréciés dans le moulage par injection et a constamment amélioré l’efficacité de la production de ce matériau – par exemple en réduisant l’empreinte carbone grâce à l’utilisation d’énergies renouvelables. On trouve également sur le marché des poudres de polyamide auxquelles on a ajouté du kevlar, des fibres de carbone ou même des billes de verre. HP met par exemple à disposition un tel thermoplastique chargé de 40% de billes de verre et présentant un taux de recyclage élevé. Le matériau est disponible sous le nom de HP 3D High Reusability PA12 Glass Beads. Récemment, HP a également annoncé le lancement d’une nouvelle poudre PA12 développée en collaboration avec Arkema, appelée HP 3D HR PA 12 S, qui se caractérise par un taux de réutilisation élevé allant jusqu’à 85%, ce qui permet de réduire les déchets.
Utilisez-vous du PA11 ou du PA12 en fabrication additive ? N’hésitez pas à partager votre avis dans les commentaires de l’article. Retrouvez toutes nos vidéos sur notre chaîne YouTube ou suivez-nous sur Facebook ou Twitter !