Application du mois : le moteur MPGE imprimé en 3D propulse l’Italie dans la course à l’espace
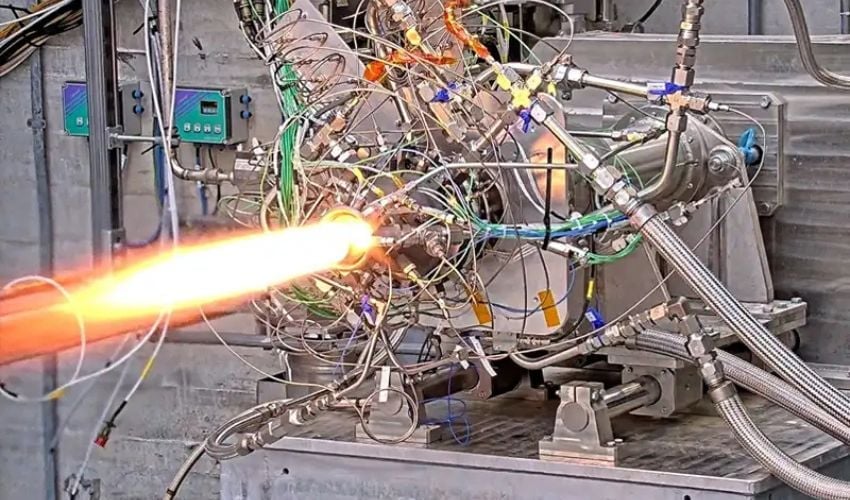
L’humanité ne cesse de viser les étoiles. Et l’utilisation de l’impression 3D rend cette conquête plus facile que jamais ! Dans le prolongement de projets antérieurs utilisant la fabrication additive pour les moteurs de fusée, voici une nouvelle étude de cas : la société italienne AVIO SpA a achevé avec succès les essais de son MPGE (moteur vert polyvalent). L’impression 3D SLM a été utilisée pour sa création.
Le projet a été réalisé dans le cadre du programme PNRR du gouvernement italien, qui s’inscrit dans un mouvement visant à renforcer le potentiel de croissance du pays. Plus précisément, il relève du thème « Technologies satellitaires et économie spatiale », dans le cadre d’un sous-investissement dans l’économie en orbite, l’Italie cherchant à accroître son rôle dans la course à l’espace. En particulier, il semble que le MPGE participe aux efforts visant à accroître les capacités de l’Italie dans le domaine de la logistique spatiale pour la surveillance de l’environnement spatial (Space Situational Awareness) et la gestion du trafic spatial (Space Traffic Management).
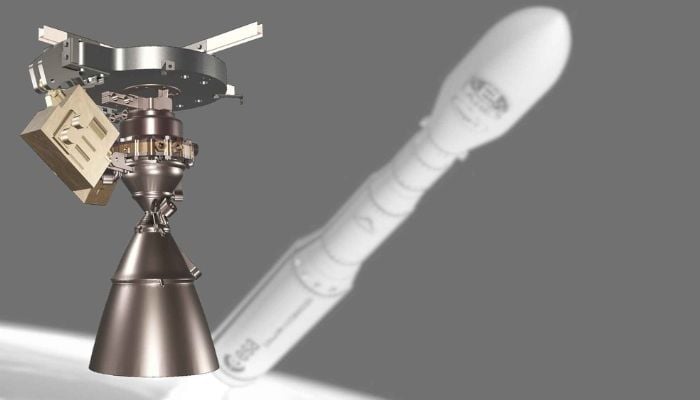
Image conceptuelle du moteur de fusée MPGE (crédits photo : AVIO SpA)
AVIO s’est vu confier le projet MPGE, dans le cadre d’un contrat de l’Agence spatiale italienne, et y a travaillé en collaboration avec Sòphia High Tech. La fusée bi-propulsive a effectué ses premiers essais de mise à feu le 24 février 2025. Mais comment a-t-elle été fabriquée ?
Utilisation de l’impression 3D et de la fabrication traditionnelle pour créer le MPGE
Comme nous l’avons dit, l’essai réussi du moteur MPGE est un grand pas en avant pour l’industrie spatiale italienne. Il est d’autant plus intéressant à utiliser que l’objectif du moteur MPGE est d’être plus « vert » que de nombreux moteurs de fusée. Comment ? En utilisant à la fois du peroxyde d’hydrogène et du kérosène comme carburant. Et la fabrication additive a eu un rôle à jouer.
Selon les informations fournies par Sòphia High Tech, qui a été chargée de créer la chambre de combustion, le système de contrôle thermique, l’extension de la buse et la section d’injection, l’impression 3D et l’usinage CNC ont été employés pour fabriquer le MPGE. Plus précisément, Sòphia High Tech indique que son équipe a utilisé la fusion par laser, qui a été qualifiée et est capable de respecter les certifications avancées prescrites par les normes ECSS-Q-ST-70-80C de l’ESA, ainsi qu’un matériau à base de nickel. Bien que l’imprimante 3D utilisée ne soit pas explicitement mentionnée, l’entreprise aérospatiale a régulièrement recours à une TruPrint 3000 de Trumpf et il est probable qu’elle ait également été utilisée dans ce cas.
En plus de la fabrication additive, chaque pièce mécanique a nécessité plusieurs phases de contrôle dimensionnel et de validation à différents stades. Par exemple, le traitement thermique, le dépoudrage et la finition mécanique par usinage CMC ont été autant d’étapes nécessaires. Sòphia Tech a créé ses propres cycles de production afin de garantir le respect des tolérances mécaniques strictes, tant géométriques que dimensionnelles, des pièces.
Quoi qu’il en soit, l’essai réussi du projet MPGE montre clairement les avantages de la combinaison de la fabrication additive et de la fabrication traditionnelle pour créer des pièces de fusée. Elle insiste également sur la force du secteur manufacturier italien, puisque l’ensemble du moteur respectueux de l’environnement a été fabriqué dans le pays. À terme, le projet MPGE vise à qualifier un système de propulsion innovant destiné aux systèmes de lancement et aux applications spatiales orbitales et suborbitales.
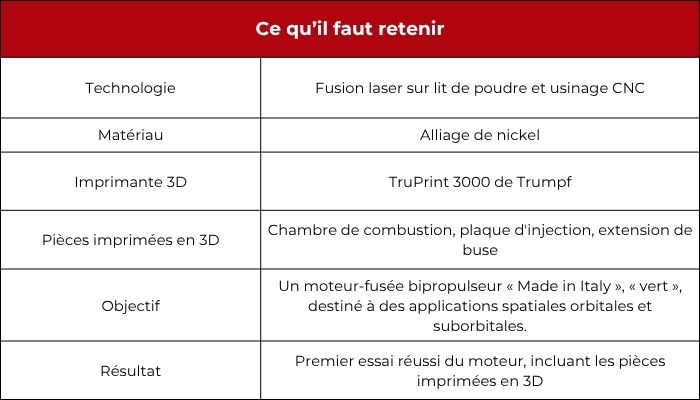
Crédits tableau : 3Dnatives
Que pensez-vous du moteur MPGE ? N’hésitez pas à partager votre avis dans les commentaires de l’article. Vous êtes intéressés par l’actualité de l’impression 3D dans l’aérospatiale ? Cliquez ICI. Vous pouvez aussi nous suivre sur Facebook ou LinkedIn !
*Crédits photo de couverture : AVIO SpA