La fabrication additive métallique pour améliorer le moteur de fusée E-2 Liquid
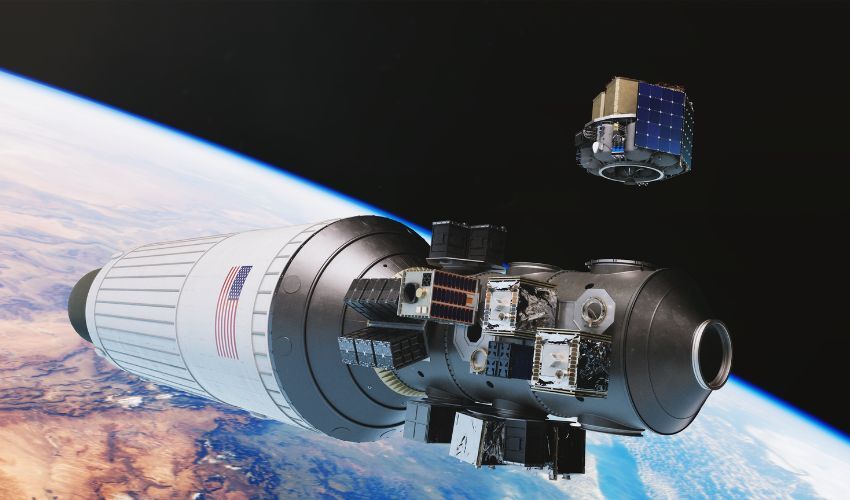
Il ne fait aucun doute que les satellites jouent un rôle essentiel dans nos vies. Non seulement, ils fournissent des informations sur les nuages, les océans, l’air et la Terre (permettant ainsi aux scientifiques de prévoir le temps et le climat), mais ils sont également essentiels pour les communications mondiales et bien plus encore. Mais saviez-vous que la taille des satellites a diminué ? Aujourd’hui, les satellites sont moins chers à produire car ils sont plus légers que les versions précédentes, ce qui permet de réduire les coûts de lancement. Par conséquent, les entreprises s’efforcent également de créer des fusées plus petites et moins coûteuses pour les soutenir. L’une des plus remarquables sur le marché est celle imaginée par l’entreprise Launcher.
La start-up californienne Launcher a été fondée en 2017 pour répondre à la demande croissante, qui dépasse l’offre sur le marché des lanceurs de satellites (qui devrait passer de 8 à 38 milliards de dollars d’ici 2030). L’entreprise combine une technologie de propulsion liquide et le recours à l’impression 3D métallique pour créer efficacement des fusées et des vaisseaux cargo permettant de mettre en orbite de petits satellites. Elle a notamment conçu le moteur de fusée Launcher Engine-2 (E2) à faibles coûts, qui a été spécialement optimisé pour être produit en série. Il vise à être le moteur de fusée liquide le plus performant de sa catégorie et est destiné à être le composant de poussée central de la fusée Light de Launcher. Et pour le mettre au point, Launcher s’est tourné vers Stratasys Direct Manufacturing et la technologie d’impression 3D métal de chez Velo3D.
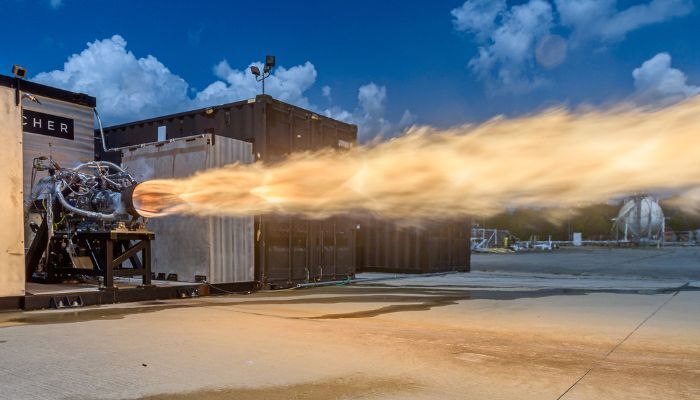
Test du moteur (Crédits photo : Lanceur/John Kraus Photography)
Focus sur le moteur de fusée Launcher
Comme précédemment mentionné, le moteur de fusée E-2 Liquid a été conçu pour faire partie des fusées à haute performance de Launcher. Ce moteur de 22 000 lbf (pound-force), propulsé au LOX (oxygène liquide)/RP-1 (kérosène), est considéré comme le plus performant au monde pour des lanceurs de petite taille. Imprimé en 3D avec un alliage de cuivre, il offre un rendement de combustion de 98% et une performance de 365s Isp (impulsion spécifique). De plus, grâce à son équilibre élevé, la turbine de pompe LOX peut tourner à 30 000 tours/minute dans des conditions cryogéniques, tout en transportant l’oxygène liquide.
Cependant, l’innovation et les performances offertes par la fusée E-2 impliquent qu’elle n’est pas si simple à fabriquer. La turbopompe, y compris sa turbine, représente un défi particulier. Max Haot, fondateur et PDG de Launcher, explique la difficulté du projet : « Si l’on considère n’importe quel moteur-fusée « liquide » capable d’atteindre une orbite, la turbopompe est l’une des parties les plus difficiles du projet… ou tout du moins, la moitié du défi. Et si vous parlez d’une turbopompe pour un cycle fermé à combustion étagée, ce niveau de défi augmente. »
Et bien que la fabrication additive métallique ait été choisie pour le projet, les erreurs ne sont pas possibles à ce niveau de haute performance. M. Haot ajoute : « Je tiens à préciser l’importance de ce point. Nous avons affaire à de l’oxygène liquide et à une turbine tournant à 30 000 tours/minute pour produire environ un mégawatt d’énergie. Dans ce type d’environnement, avec une pression de refoulement de quatre mille psi, toute anomalie, tout frottement entre le rotor et le stator, peut entraîner un démontage immédiat, rapide et non planifié. » Les technologies de rupture seraient donc la clé.
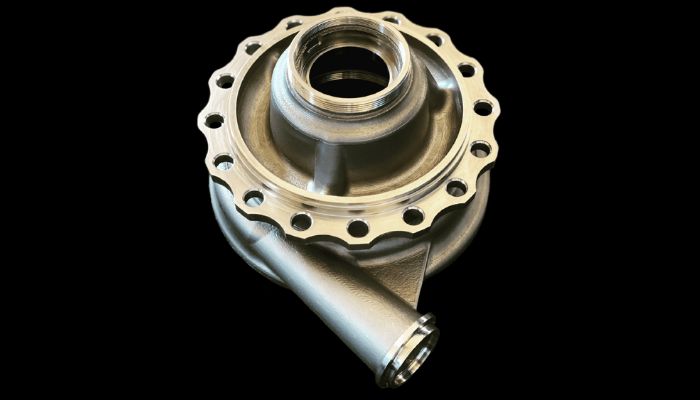
Section de la turbine de la pompe à oxygène liquide alimentant le moteur E-2 (crédits photo : Launcher)
Launcher s’est donc tourné vers Stratasys Direct Manufacturing qui a lui-même utilisé la technologie Sapphire® de Velo3D pour créer la turbine de l’inducteur. Ce composant essentiel accélère et entraîne le LOX vers la chambre de combustion, créant ainsi un plus grand débit de fluide et davantage de poussée pour la fusée. Plus précisément, la roue de l’E-2 a été créée en intégrant deux pièces imprimées en 3D distinctes, un inducteur et une turbine, pour en faire un seul composant co-joint et efficace. Le matériau choisi est l’INCONEL 718, un matériau résistant à la corrosion qui présente une bonne compatibilité avec le LOX et une excellente résistance mécanique aux températures cryogéniques.
Pourquoi la fabrication additive métallique ?
Si Launcher pouvait choisir n’importe quelle technologie, pourquoi l’entreprise s’est-elle tournée vers la fabrication additive métallique et plus particulièrement vers la solution de Velo3D ? La fabrication additive métallique, comme on peut s’en douter, présente plusieurs avantages, notamment en termes de réduction des coûts et de liberté de conception. Cependant, n’importe quelle solution n’aurait pas fait l’affaire. Principalement, parce que pour obtenir les propriétés nécessaires, la pièce ne pouvait pas être réalisée avec des supports internes ou en étant imprimée de manière inclinée. Dès lors, Stratasys Direct a décidé de recourir à la technologie Sapphire® de Velo 3D pour sa capacité à imprimer des pièces sans supports.
En particulier, la possibilité d’imprimer à plat était essentielle pour l’équipe, car l’inclinaison de la pièce pendant le processus d’impression l’aurait empêchée d’obtenir un composant bien équilibré. Mais cela ne serait pas possible avec d’autres solutions, car généralement, si les utilisateurs veulent éviter les supports internes (qui sont nécessaires pour la plupart des géométries complexes sur de nombreuses solutions d’impression 3D en métal), ils doivent incliner la pièce. Ce n’est toutefois pas le cas avec le système Sapphire®.
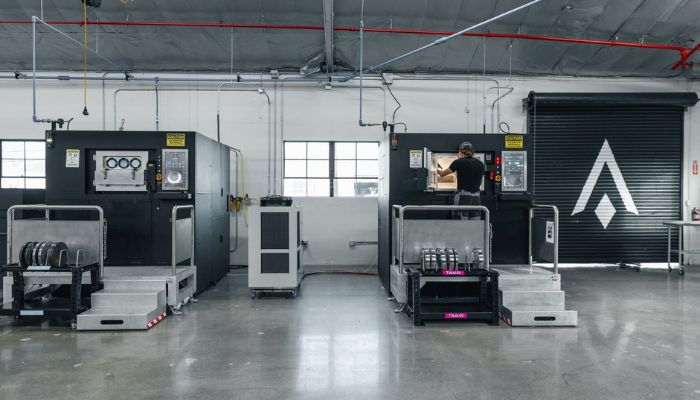
Les deux imprimantes Sapphire de Launcher (crédits photo : Launcher)
Comme mentionné, la solution de Velo3D est unique dans le secteur de la fabrication additive pour sa liberté de conception, incarnant ainsi la devise de l’entreprise : « Print the part you want and need – without compromise » (« Imprimez la pièce que vous voulez et dont vous avez besoin – sans compromis »). Cette liberté est le résultat de plusieurs facteurs, notamment le fait que Velo3D propose une solution avancée d’impression 3D métal entièrement intégrée comprenant son logiciel de préparation d’impression dénommée Flow™ et son logiciel Assure™ pour la validation de la qualité. De plus, elle est capable d’imprimer des angles fermés, proches de zéro degré. Ce dernier point était particulièrement important pour Launcher car il implique que la pièce pouvait être imprimée à plat.
Incliner la pièce aurait compromis la qualité en raison de l’accumulation de contraintes pendant l’impression, cela aurait notamment empêché la fabrication d’un composant capable de réaliser une rotation parfaitement équilibrée. Selon Stratasys Direct, avec le système Velo3D, il a été possible d’imprimer des hélices dans l’orientation idéale tout en évitant de recourir à des supports internes qui auraient également pu endommager la pièce finale. Andre Ivankovic, Ingénieur Mécanique chez Launcher, expliquait : « En imprimant la pièce à plat, nous avons obtenu une distribution symétrique de la masse de la pièce par rapport à cet axe de rotation central. »
Quel est le résultat ?
Dernière étape avant finalisation, la pièce obtenue a dû subir des opérations personnalisées de post-traitement avant de passer par un process de validation complet. Pour ce faire, Stratasys Direct a partiellement usiné le composant afin notamment d’éliminer toute poudre des canaux internes avant de lui faire subir des traitements certifiés de résistance à la chaleur. L’étape suivante consistait à s’assurer que la turbine répondait aux exigences de densité et d’intégrité du matériau avant les traitements thermiques.
L’expertise en fabrication additive de Stratasys Direct associé à un post-traitement additionnel rigoureux et la capacité de Velo3D à imprimer sans support a permis de construire avec succès une pièce hautement complexe et fonctionnelle. Jusqu’à présent, les essais se sont avérés concluants. Launcher a récemment testé avec succès la turbopompe du moteur E-2 pour l’U.S. Space Force lors d’une campagne au Centre Spatial Stennis de la NASA. L’équipe de test du E-2 a pu atteindre et même dépasser tous les objectifs de puissance, de pression d’entrée et de sortie, d’efficacité et de vibration au cours de 11 tests. Vous pouvez en savoir plus sur la façon dont le E-2 a été fabriqué à l’aide de la solution Sapphire® de Velo3D ICI.
Que pensez-vous de la fabrication du moteur de fusée E-2 de Launcher ? Partagez votre avis dans les commentaires de l’article. Retrouvez toutes nos vidéos sur notre chaîne YouTube ou suivez-nous sur Facebook ou Twitter !
*Crédits photo de couverture : Launcher