À la découverte des matériaux d’impression 3D : les composites
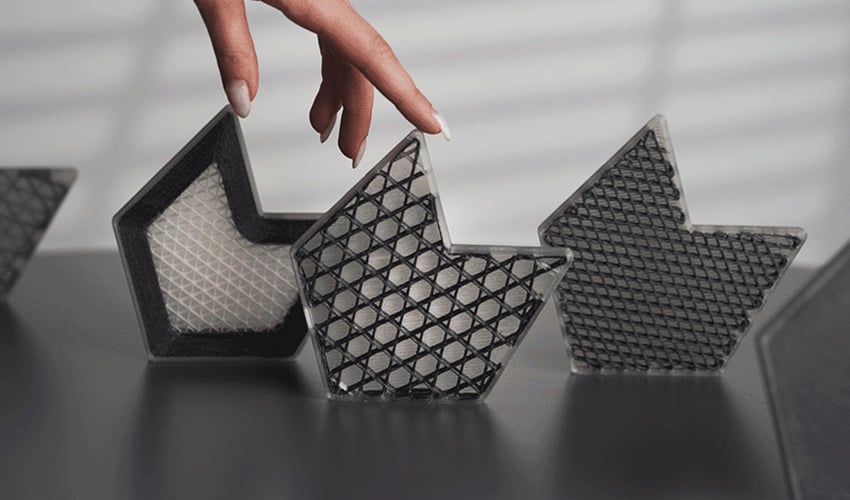
Ces dernières années, l’impression 3D composite est devenue de plus en plus populaire. Cette branche de la fabrication additive est aujourd’hui utilisée par de nombreuses entreprises de l’industrie grâce aux propriétés intéressantes qu’elle offre pour une grande variété d’applications. A tel point que certaines études estiment que le marché de l’impression 3D de composites atteindra une valeur de 1,73 milliard de dollars en 2030. Logiquement, ce mode de production fait référence à des imprimantes compatibles, ainsi qu’à des matériaux composites. Ces derniers se caractérisent par le fait qu’ils sont composés de deux éléments : un matériau de matrice qui maintient la structure principale et un autre matériau de renfort qui apporte des propriétés supplémentaires. Néanmoins, nous verrons ci-dessous en quoi consistent ces matériaux et les types qui existent dans la fabrication additive.
La plupart du temps, ces matériaux sont obtenus à partir d’un polymère associé à des fibres, qui peuvent être courtes ou longues. Au sein de ces catégories, il existe de nombreux types, mais les plus utilisés dans l’impression 3D sont la fibre de carbone, la fibre de verre et le Kevlar. En fonction des besoins de chaque pièce, des fibres courtes ou longues seront choisies. Les plus courts sont intégrés dans toute la matrice et offrent une plus grande résistance à la pièce finale. Les fibres longues, en revanche, sont déposées pendant le processus d’impression lui-même et ne sont pas coupées en petits morceaux, ce qui permet un renforcement uniquement là où c’est nécessaire. Alors que les premiers sont compatibles avec une grande variété d’imprimantes 3D, les seconds ne sont compatibles qu’avec celles dotées de capacités spéciales. Grâce à l’utilisation de ces matériaux, les pièces imprimées en 3D obtiennent une meilleure stabilité dimensionnelle, une plus grande légèreté et une moindre susceptibilité à la déformation. De plus, en combinant des fibres avec des plastiques standard, les températures d’impression seront légèrement plus élevées pour créer des modèles précis et de qualité. Analysons maintenant en détail les trois types de matériaux composites que l’on peut trouver.
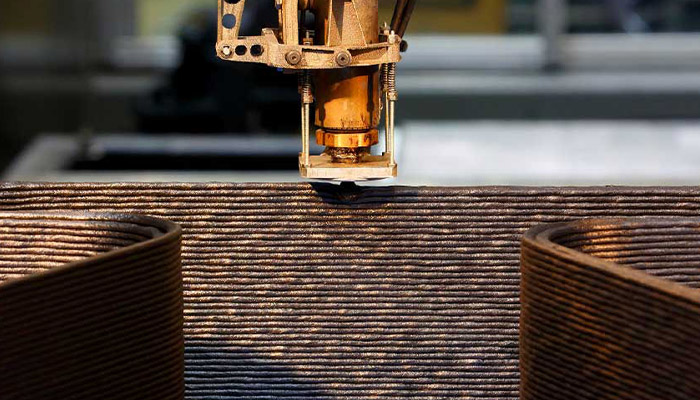
L’impression 3D de matériaux composites gagne en popularité sur le marché (crédits photo : SABIC)
Les matériaux composites en fibre de carbone
Comme nous l’avons mentionné, les renforts en fibres de carbone sont les plus utilisés dans la fabrication additive des composites. Créée en 1860 par le chimiste Joseph Swan, la fibre de carbone est composée d’atomes de carbone liés entre eux, dont la structure cristalline est alignée en brins, ce qui la rend incroyablement résistante. Elle est considérée par beaucoup comme la fibre la plus efficace car elle possède l’un des rapports résistance/poids les plus élevés qui existent (deux fois plus élevé que l’aluminium). C’est intéressant lorsqu’il s’agit de créer des pièces finies qui allient légèreté et résistance. De plus, les matériaux qui composent cette fibre disposent d’une grande rigidité, d’une grande résistance à la traction et d’une bonne résistance chimique.
Lors de l’utilisation de la fibre de carbone avec l’impression 3D, il y a certaines exigences à garder à l’esprit. Parmi celles-ci se trouve la buse, qui doit être en acier trempé pour permettre la création de pièces de qualité. Les mêmes recommandations s’appliquent au matériau de matrice auquel le renforcement en carbone est ajouté. Il existe des matrices telles que le PLA, le PETG, le nylon, l’ABS ou le polycarbonate, qui deviennent plus résistantes et plus légères. En plus d’être compatible avec les thermoplastiques, la fibre de carbone peut également être mélangée à la céramique. La création de ces matériaux composites a permis le développement d’applications nouvelles et innovantes. Les composites à base de fibres de carbone se retrouvent dans de nombreux secteurs, tels que l’aérospatiale et l’automobile.
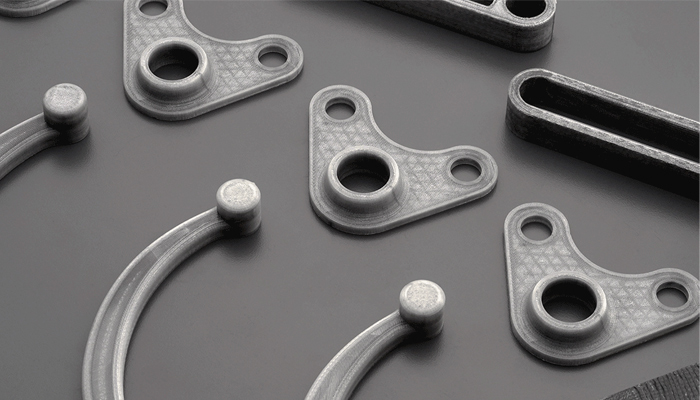
Crédits photo : Anisoprint
Les composites à base de fibre de verre
Brevetée en 1930, la fibre de verre est utilisée pour renforcer de nombreux polymères thermoplastiques. Ce matériau permet de produire des pièces dix fois plus résistantes que l’ABS s’il est appliqué sur le matériau de base approprié. Contrairement aux matériaux qui intègrent du carbone, les composites en fibre de verre sont moins rigides, mais moins cassants. Ils sont également moins chers. La fibre de verre détient, en outre, de bonnes propriétés mécaniques, constitue un bon isolant électrique et dispose d’une faible conductivité thermique. En plus d’être disponible en plusieurs couleurs, ce matériau est sujet à une rétraction moindre, ce qui réduit les risques de déformation. Comme pour la fibre de carbone, un filament renforcé de fibre de verre est abrasif.
Les filaments d’impression 3D renforcés de fibre de verre sont idéaux pour les prototypes d’ingénierie et les pièces d’utilisation finale qui nécessitent une résistance mécanique et thermique optimale. Que ce soit dans le secteur de la construction, du maritime ou encore du sport, ce matériau composite est aujourd’hui très répandu. Par exemple, en collaboration avec Autodesk, Catmarine, Micad et Owens Corning, la société Moi Composites a créé le bateau MAMBO par impression 3D avec de la fibre de verre. On se souvient aussi de la société néerlandaise MX3D qui a utilisé ce matériau pour créer un pont renforcé grâce à l’impression 3D.
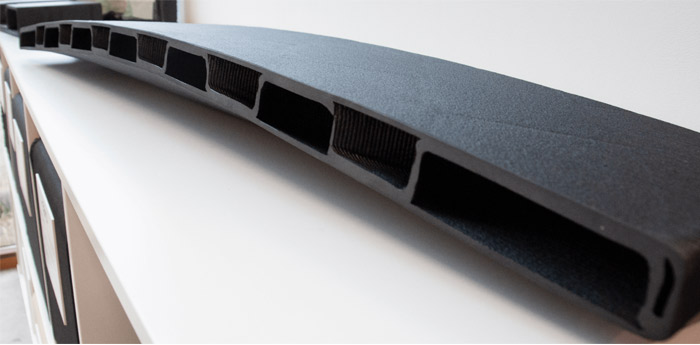
Prototype monobloc pour un pont imprimé en 3D en fibre de verre (crédits photo : CEAM)
Matériaux composites Kevlar
Kevlar est une marque déposée de DuPont de Nemours, commercialisée pour la première fois en 1971 et inventée par Stephanie Kwolek. Il fait partie de la famille des fibres aramides et constitue l’un des matériaux les plus résistants à l’usure. Ces types de matériaux sont obtenus par polymérisation, c’est-à-dire qu’ils sont construits en joignant de longues chaînes de molécules. Ceux de Kevlar sont disposés en lignes parallèles régulières très rapprochées, et c’est de là que viennent leur résistance. Comme pour les autres fibres, le Kevlar se trouve généralement mélangé à divers types de plastique pour obtenir des matériaux composites. Il possède de bonnes propriétés mécaniques en termes de traction et de fatigue, et il est principalement utilisé pour fabriquer des pièces soumises à de fortes vibrations et qui doivent résister à l’abrasion. En plus d’être cinq fois plus solide et plus léger que l’acier, il possède également une forte résistance à la chaleur. En effet, il est capable de supporter des températures allant jusqu’à 400°C.
Entre autres caractéristiques, ce matériau a une faible densité, une grande polyvalence en termes d’applications et une structure moléculaire longue et régulière, ce qui se traduit par l’impression 3D de pièces très lisses et de haute qualité. Nombreuses sont les industries qui utilisent la fabrication additive avec Kevlar. Dans l’industrie automobile, par exemple, il est intéressant pour la création de pratiquement n’importe quelle pièce. Nous avons déjà vu comment la société américaine Aptera Motors a imprimé en 3D une partie d’une voiture avec ce matériau composite. Cela montre les possibilités des matériaux avancés et renforcés d’aujourd’hui.
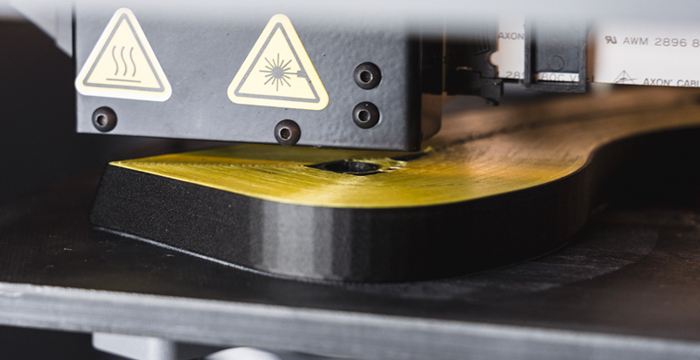
Impression 3D d’un matériau composite kevlar (crédits photo : Markforged)
Que pensez-vous des différents composites sur le marché de l’impression 3D ? Partagez votre avis dans les commentaires de l’article. Retrouvez toutes nos vidéos sur notre chaîne YouTube ou suivez-nous sur Facebook ou Twitter !
*Crédits photo de couverture : Anisoprint
Si Ont pourrait faire avancé avec la 3D robot , l’architecture jusqu’à 2 niveau , faciliterai la tache , limiterai un nombre de matériaux, et utiliserai du ré-emploi , avec surtout un coup faible pour réalisé , plus d’autres avantages pour évité la pénurie des matières avenir.
Cordialement à tous , de Gérard Montérin Économiste de la construction dans l’alternatif, et le réemploie des matières.