Massivit 3D présente la solution 10000 et sa technologie Cast In Motion
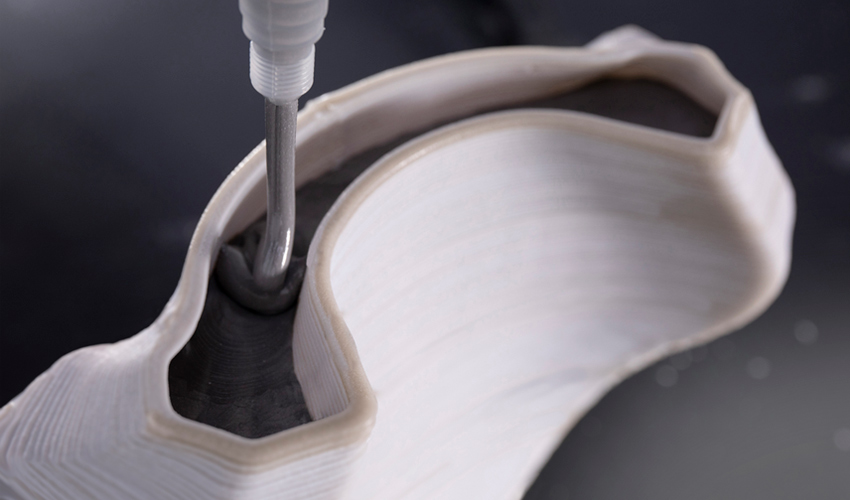
Formnext, le plus grand salon international consacré à la fabrication additive, a eu lieu à la mi-novembre de cette année. Avec plus de 800 exposants et des milliers de visiteurs venus du monde entier, l’événement a été une fois de plus le principal point de rencontre de l’industrie de la 3D. L’une des sociétés exposant ses solutions de fabrication additive grande échelle était Massivit 3D. Avec des sites en Israël, en Amérique du Nord et en Belgique, Massivit 3D est l’un des principaux fournisseurs d’imprimantes 3D grand format. Cette année, elle a profité du salon de Francfort pour présenter pour la première fois son système Massivit 10000 primé au marché de la fabrication additive. Elle a également démontré les capacités de la technologie « Cast In Motion » de cette solution pour la création de moules.
Connue pour ses solutions grand format basées sur la technologie GDP, ou Gel Dispensing Printing, Massivit est en mesure de créer de très larges pièces. Ses machines répondent également aux besoins de nombreuses industries, comme nous avons pu le constater lors de la dernière édition de Formnext. Grâce à plusieurs démonstrations en direct, la société a montré aux visiteurs son nouveau système de fabrication additive qui pourrait changer la donne en automatisant la production de moules pour les composites. L’objectif principal de Massivit 3D avec la solution 10000 et la technologie Cast In Motion est d’apporter une solution aux goulots d’étranglement courants dans la fabrication des composites en imprimant directement et en moulant des moules industriels en un seul processus.
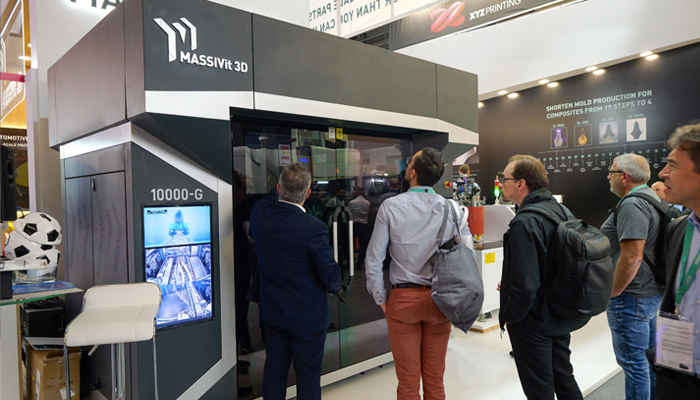
Le stand de Massivit 3D au Formnext 2022 (crédits photo : Massivit 3D)
La solution Massivit 10000 et la technologie “Cast In Motion”
Comme mentionné, la société a présenté sa machine Massivit 10000 lors du Formnext 2022. Basée sur la technologie Cast In Motion (CIM), cette méthode permet la production automatisée de moules et d’outils isotropes pour la fabrication plus rapide de composites. Le problème qu’ils essaient de résoudre avec CIM est celui de la production d’objets composites. Normalement, cette dernière nécessite un processus de fraisage CNC, puis la superposition manuelle de matériaux pour former le moule, suivi du moulage et du durcissement. Selon Massivit 3D, ce processus traditionnel peut nécessiter jusqu’à 19 étapes, tout en étant dommageable pour l’environnement. Cependant, la méthode CIM aborde ce problème d’une manière totalement différente, inédite jusqu’ici dans le secteur de l’impression 3D.
Le système fonctionne au moyen d’une tête intégrée qui imprime une coque extérieure en utilisant le matériau thermodurcissable incassable de Massivit 3D. Une deuxième tête verse par intermittence un matériau de coulée thermodurcissable dans cette coquille au fur et à mesure de sa construction. La combinaison de ces deux procédés permet de créer un moule imprimé en 3D isotrope pour les composants composites. Le matériau utilisé, appelé CIM 500, offre des propriétés mécaniques et thermiques élevées. Cela permet d’obtenir un faible coefficient de dilatation thermique (CTE) et une température de déflexion thermique (HDT) élevée. De plus, le système se caractérise par sa capacité à accélérer la production de moules de 80 %, réduisant les délais de plusieurs semaines à quelques jours seulement.
« Il ne fait aucun doute que le marché des composites attendait avec impatience une percée dans les processus de moulage« , a déclaré Erez Zimerman, CEO de la société. « La Massivit 10000 élimine les goulots d’étranglement critiques pour les fabricants, en réduisant le temps de production de leurs moules de plusieurs dizaines de semaines à quelques jours seulement. Il y avait une excitation palpable sur notre stand Formnext qui reflète le besoin profond de transformation numérique dans l’arène des composites. »
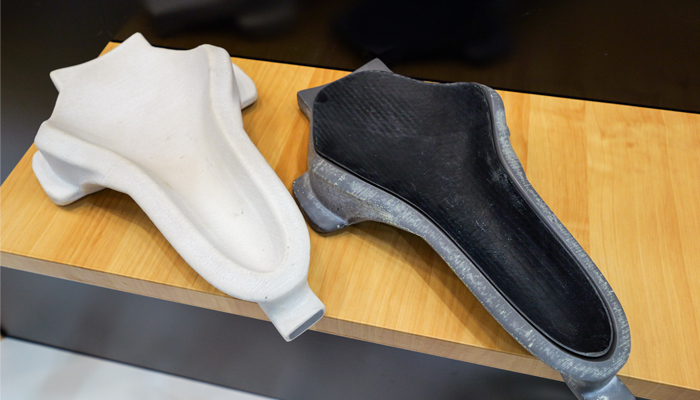
La technologie CIM premet la production automatisée de moules isotropes (crédits photo : Massivit 3D)
Les visiteurs passant par le stand de Massivit 3D pendant le salon ont eu l’occasion de voir et de manipuler des pièces imprimées en 3D avec la nouvelle solution. Il s’agissait de moules isotropes complexes, de mandrins de nettoyage, de gabarits et de montages. Une occasion unique de découvrir de visu les possibilités de la technologie de fabrication.
Applications de la technologie de Massivit 3D
La technologie brevetée de Massivit 3D ouvre la porte à une multitude d’industries pour l’intégrer dans leur activité. De toute évidence, l’une des principales applications est la création de moules complexes, notamment les moules ouverts et fermés, les moules à bain, les outils de thermoformage, le moulage par transfert de résine et le moulage par injection réactionnelle. Parmi les autres utilisations, citons la fabrication d’outils maîtres, de gabarits et de montages qui peuvent être produits numériquement à grande vitesse. Il ne faut pas oublier la possibilité de créer des mandrins de nettoyage pour les gaines et les évents. Ces applications et outils sont très utiles pour des industries telles que l’automobile, les articles de sport, le ferroviaire, la marine, la construction, la défense et l’aérospatiale.
Comme on peut le constater, tant le nouveau système de Massivit 3D que ses solutions grand format bien connues positionnent l’entreprise comme un acteur majeur sur le marché de la fabrication additive. Si vous souhaitez en savoir plus sur ses technologies et ses capacités présentées lors de Formnext, vous pouvez visiter son site web ICI.
Que pensez-vous de la solution Massivit 1000 et du procédé Cast In Motion ? Partagez votre avis dans les commentaires de l’article. Retrouvez toutes nos vidéos sur notre chaîne YouTube ou suivez-nous sur Facebook ou Twitter !
*Crédits photo de couverture : le processus Cast In Motion par Massivit 3D