Lufthansa dévoile la première pièce porteuse de charge fabriquée par impression 3D métal
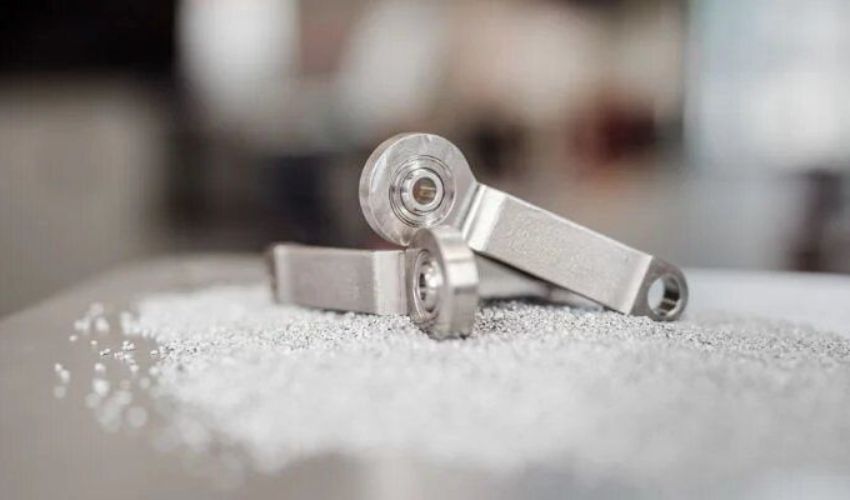
La compagnie aérienne allemande Lufthansa a annoncé que, dans le cadre de sa collaboration avec Premium AEROTEC, la fabrication additive sera utilisée pour produire de manière plus rentable des pièces de rechange pour ses avions. Plus précisément, le composant métallique conçu au centre de fabrication additive de Lufthansa Technik sera utilisé pour le système antigivre du moteur IAE-V2500. À cet effet, les deux entreprises ont déjà reçu l’approbation officielle de l’Agence européenne de la sécurité aérienne (AESA) pour les A-Links imprimés en 3D. C’est la première fois que l’industrie aérospatiale approuve une pièce de rechange métallique porteuse imprimée en 3D.
Spécialisé dans la production de pièces d’avion en métal et en fibres de carbone, Premium AEROTEC fabriquera au total neuf A-links pour fixer un conduit d’air chaud en forme d’anneau dans le capot du moteur. Ces pièces permettent d’éviter la présence de glace sur le moteur de l’avion, une nécessité lors des fortes altitudes. Cependant, bien que ces A-links soient extrêmement importants, ils s’usent souvent et doivent donc être remplacés régulièrement.
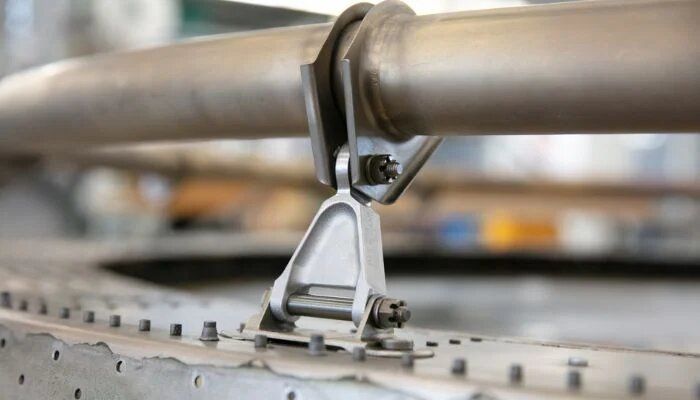
Crédits photo : Lufthansa Technik
Lufthansa et les avantages de l’impression 3D métal
La principale raison pour laquelle l’impression 3D a été choisie pour la production des A-Links est liée à l’usure. En effet, les A-Links fabriqués traditionnellement ne peuvent plus être utilisés dans le respect des normes de sécurité après quelques années en raison des vibrations subies pendant le vol. En les produisant à l’aide du procédé de fusion laser sur lit de poudre (LPBF), ils sont parvenus à réaliser de précieuses économies de matériaux et donc à réduire drastiquement les coûts de production. Cependant, pour obtenir l’approbation de l’AESA pour les pièces imprimées en 3D, un certain nombre de tests ont dû être effectués au préalable. Pour ce faire, Premium AEROTEC a réalisé de nombreux prototypes. Le résultat : un processus d’impression fiable a pu être déterminé, répondant également aux exigences les plus élevées en matière de propriétés des matériaux. Les équipes ont réussi à fabriquer des A-link dotés d’une résistance à la traction supérieure à celle des pièces conçues avec les méthodes conventionnelles.
Soeren Stark, directeur technique de Lufthansa, se réjouit de ce partenariat : « Cela fait des années que nous produisons des composants pour la cabine des avions, dont la grande majorité est en plastique, en utilisant l’impression 3D. Aujourd’hui, nous sommes en mesure de démontrer que des pièces métalliques peuvent également être fabriquées de manière additive et approuvées pour les opérations de vol. De cette manière, nous avons non seulement réalisé une économie de coûts pour le composant en question, mais aussi défini et qualifié tous les processus nécessaires à l’application de cette méthode de fabrication révolutionnaire pour les pièces métalliques structurellement pertinentes.«
Que pensez-vous de la collaboration enter Lufthansa et Premium AEROTEC ? N’hésitez pas à partager votre avis dans les commentaires de l’article. Retrouvez toutes nos vidéos sur notre chaîne YouTube ou suivez-nous sur Facebook ou Twitter !