Liquid Additive Manufacturing, un procédé d’impression 3D silicone idéal pour la production de joints
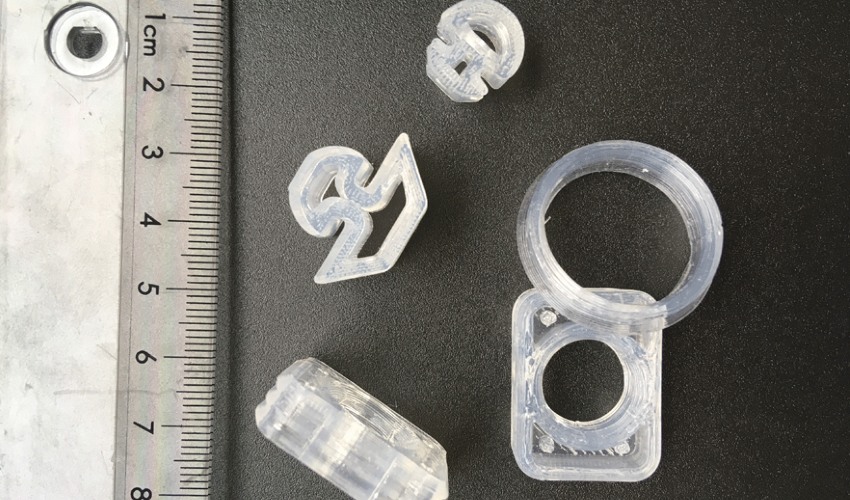
La plupart du temps, les joints sont destinés à empêcher ou à réduire la fuite ou l’infiltration de liquides, de gaz ou de substances solides telles que la poussière, aux points de séparation des composants. Dans ce contexte, il est important qu’ils soient en plastique et élastiquement malléables, chimiquement résistants, résistants à la température, au vieillissement ainsi qu’à l’usure. Un matériau qui convient donc comme matériau pour fabriquer des joints est le caoutchouc de silicone.
Ce matériau est un élastomère composé de silicone, d’hydrogène, de carbone et d’oxygène. Pour le processus de moulage par injection, on utilise du caoutchouc de silicone sous forme liquide, qui n’était auparavant pas utilisable comme matériau pour l’impression 3D. Cependant, grâce à l’imprimante 3D LiQ320 d’InnovatiQ, qui est basée sur le procédé Liquid Additive Manufacturing, cela appartient désormais au passé. Avec la LiQ320, il est possible pour la première fois d’utiliser du silicone liquide de moulage par injection pour l’impression 3D industrielle.
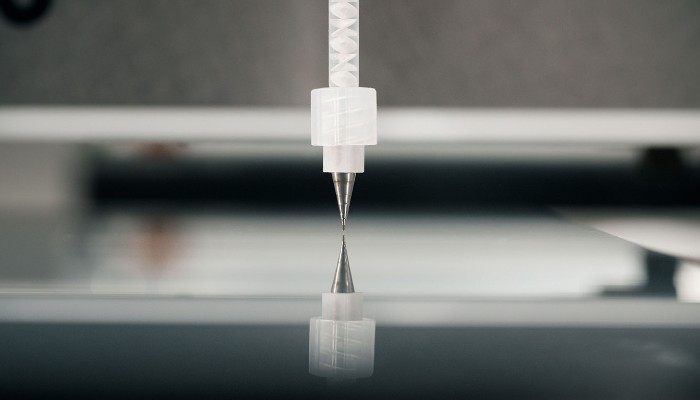
La tête d’impression permet un dosage très précis (crédits photo : InnovatiQ)
Comment fonctionne le procédé Liquid Additive Manufacturing de la LiQ320 ?
Le Liquid Additive Manufacturing est, comme son nom l’indique, un procédé de fabrication additive pour les liquides et les matériaux visqueux tels que le caoutchouc de silicone liquide. Comme tout processus de fabrication additive, tout commence par la création du modèle 3D. Pour cela, les données CAO sont converties pour le logiciel de programmation et les paramètres sont optimisés. Ensuite, les données finales sont transférées à l’imprimante 3D LiQ320. Lorsque le processus d’impression démarre, la LiQ320 commence l’extrusion volumétrique de la matière. Le matériau est constitué de deux composants qui sont mélangés dans la tête d’impression. Grâce à la technologie de la tête d’impression, un dosage précis et une bonne proportion du mélange sont possibles, de sorte que l’impression 3D de la structure peut être contrôlée au niveau moléculaire. Sachez que la plate-forme de matériaux est ouverte.
Comme pour le procédé FDM, le matériau est appliqué couche par couche sur le lit d’impression par l’extrudeur. En revanche, la matière première est déjà sous forme liquide et ne doit pas être fondue au préalable. Chaque couche individuelle est durcie pendant le processus d’impression à l’aide d’une lampe halogène à haute température d’environ 2 000 watts, qui réticule thermiquement le matériau. Cette réticulation thermique peut être influencée et contrôlée avec une grande précision. Par exemple, des porte-à-faux peuvent être générés en polymérisant le matériau très rapidement et de manière cohérente. En revanche, pour générer des structures vitreuses, la photopolymérisation n’est lancée qu’à la fin du processus d’impression. Un autre avantage de cette réticulation thermique est que le temps d’impression est considérablement réduit. Lorsque le processus d’impression est terminé, l’objet peut être retiré et utilisé directement sans post-traitement.
Liquid Additive Manufacturing convient aux prototypes, aux pièces sur-mesure et à la production industrielle de petites séries. L’éventail des applications s’étend de l’industrie automobile à la technologie médicale. Les joints sont particulièrement intéressants, car ils sont utilisés dans de nombreuses industries différentes.
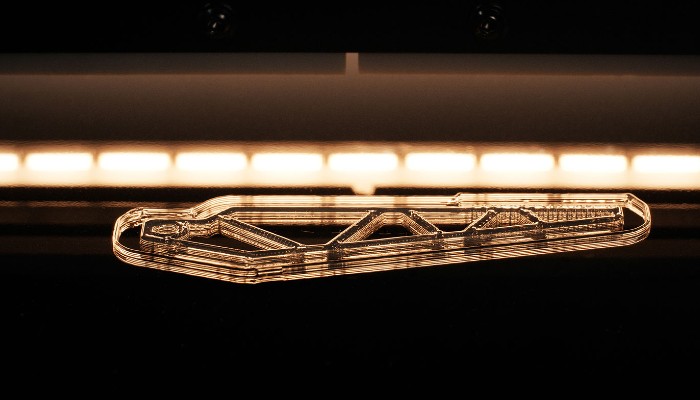
La lampe halogène à haute température durcit les différentes couches, ce qui provoque la réticulation thermique du matériau (crédits photo : InnovatiQ)
Impression de joints en silicone liquide
Comme nous l’avons déjà mentionné, l’utilisation de joints est multiple. Par exemple, ils sont utilisés dans l’industrie du bâtiment pour les fenêtres, les portes, les isolants, mais aussi dans l’industrie électrique pour protéger les composants électroniques contre les grosses chaleurs, le sel, la corrosion et la contamination. En conséquence, leurs formes varient, tant en termes de taille que de complexité.
Dans l’industrie électrique en particulier, la demande de petits joints complexes est de plus en plus importante, et généralement en série de petite taille. Avec le procédé de moulage par injection, il est difficile de réagir avec souplesse et rapidité à de telles exigences, car il faut d’abord fabriquer le moule approprié. Cela signifie également des coûts supplémentaires qui ne sont pas rentables pour cette quantité.
Le procédé Liquid Additive Manufacturing élimine ces délais et ces coûts de mise en place, ce qui permet aux entreprises de répondre rapidement aux exigences et de s’adapter à des cycles d’innovation toujours plus courts. Les propriétés techniques restent comparables à celles des pièces moulées par injection, quelle que soit leur géométrie. Il est également possible d’imprimer le joint directement sur un élément existant. Pour ce faire, le composant est placé dans l’imprimante, le joint en caoutchouc de silicone liquide est appliqué et durci directement pendant le processus d’impression grâce à la réticulation thermique. Le composant fini peut être retiré et est prêt à être utilisé immédiatement. Dans la vidéo ci-dessus, vous pouvez voir différents joints qui ont été fabriqués à l’aide de ce procédé.
Que pensez-vous de cette technologie développée par InnovatiQ ? N’hésitez pas à partager votre avis dans les commentaires de l’article ou avec les membres du forum 3Dnatives. Retrouvez toutes nos vidéos sur notre chaîne YouTube ou suivez-nous sur Facebook ou Twitter !