KRAKEN, un nouveau système de fabrication hybride grand format et multi-matériaux
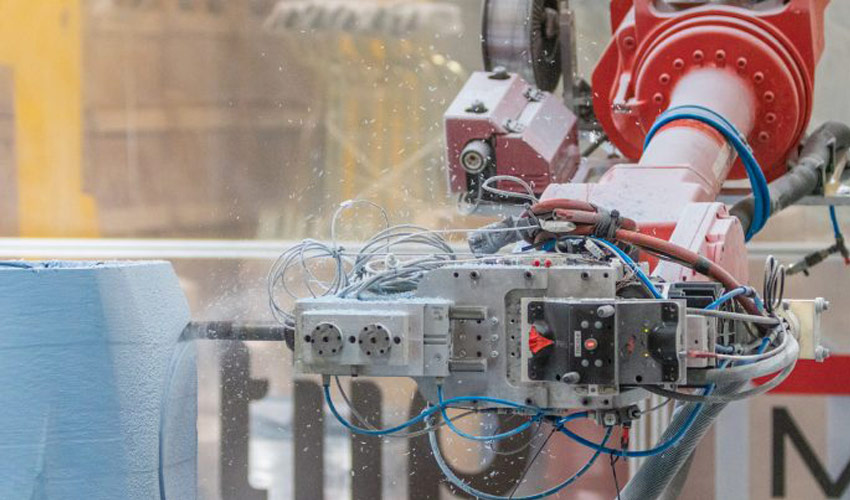
Depuis trois ans maintenant, plusieurs chercheurs européens travaillent sur le projet KRAKEN, un système de fabrication hybride combinant impression 3D et méthodes de production soustractives. Doté de trois technologies de fabrication additive interchangeables et d’une 4ème tête de fabrication soustractive, le KRAKEN serait capable de créer des objets de 20 mètres de long. Le développement de la machine s’est achevé fin septembre et elle est désormais disponible sur le marché.
Les technologies de fabrication additive sont de plus en plus employées pour produire des pièces finies : selon le dernier rapport du cabinet E&Y, 18% des entreprises impriment en 3D des produits finis et 46% prévoient de le faire d’ici 2022, preuve que les professionnels font davantage confiance en la technologie. Toutefois, il est important de souligner qu’elle est souvent employée en complément de méthodes de production plus classiques : par exemple, beaucoup l’utilisent pour créer des moules complexes et ainsi accélérer les délais de mise sur le marché. Ce n’est d’ailleurs pas pour rien qu’on observe une croissance des systèmes de fabrication hybrides où l’objectif est de combiner différents procédés pour augmenter sa productivité.
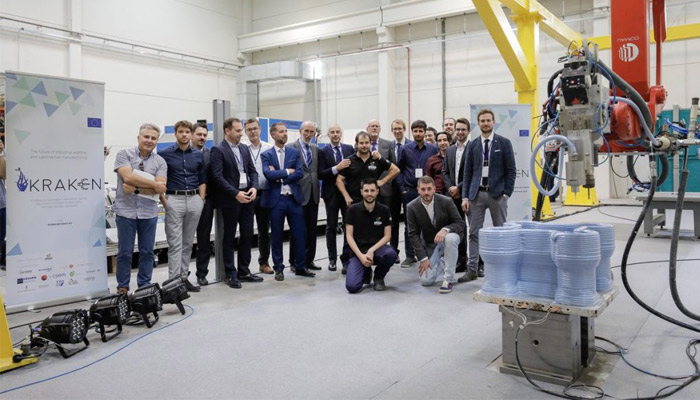
L’équipe du projet (crédits photo : KRAKEN Project)
Le projet KRAKEN n’aurait pas été possible sans le financement obtenu dans le cadre du programme-cadre de recherche Horizon 2020, ayant pour objectif d’augmenter la croissance et la compétitivité du marché. On vous parlait d’ailleurs récemment du pôle AMable, également financé par ce programme. KRAKEN est né de la rencontre entre quinze spécialistes du secteur et instituts de recherche, dont le cabinet britannique TWI, l’entreprise espagnole ACCIONA ou encore le CECIMO, l’association européenne des fabricants de machines-outils. Leur objectif était de concevoir une machine capable de produire des pièces d’une longueur de 20 mètres de long à partir de polymères thermodurcissables, d’aluminium, et des deux à la fois. Ils souhaitent aussi créer 750 emplois dans l’ensemble de l’Union Européenne.
Les caractéristiques de la machine KRAKEN
La solution KRAKEN serait équipée de plusieurs têtes interchangeables : l’une permettrait l’extrusion de résine, une autre serait capable de déposer et de souder des tiges métalliques (selon le procédé WAAM), une troisième viendrait métalliser les pièces à l’arc électrique tandis que la quatrième offrirait des fonctions de découpe, de ponçage et de polissage. Si on se penche davantage sur les procédés de fabrication additive, l’extrudeur de résine viendrait déposer une pâte de polyuréthane à une vitesse de 120 kg/h. Le procédé WAAM de KRAKEN pourrait quant à lui imprimer en 3D des pièces en aluminium à une vitesse de 15 kg / h. La métallisation par projection thermique serait intégrée pour ajouter un revêtement métallique au-dessus d’une pièce polymère. La machine 4-en-1 occupe une surface au sol de 20 x 8 x 6 mètres.
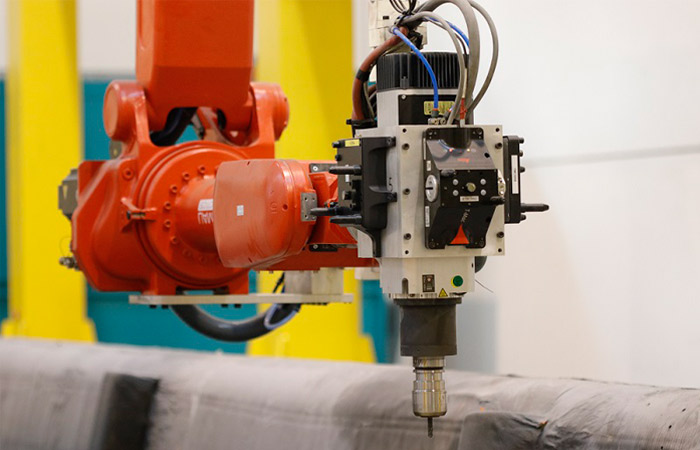
Les têtes de fabrication sont interchangeables (crédits photo : KRAKEN Project)
José Antonio Dieste, chercheur et coordinateur du projet KRAKEN, explique : “La machine est prête à être commercialisée, elle a été testée dans un environnement de fabrication réel et les démonstrateurs de projet ont été validés par des collaborateurs dans des conditions réelles. Nous pouvons maintenant livrer des pièces ou installer des systèmes KRAKEN selon la demande des clients.” Côté performances, les porteurs du projet affirment que le KRAKEN est une solution 40% plus rapide, 25% plus productive et 30% moins chère.
Quelques démonstrateurs de projet
Afin de valider le système de fabrication KRAKEN, un certain nombre d’études de cas ont été réalisées par les partenaires du projet. Par exemple, CRF a fabriqué des châssis métalliques pour le devant et l’arrière d’une Alfa Romeo 4C. ACCIONA a quant à elle créé des panneaux de revêtement imperméables pour tunnels avec câblage électrique intégré. Autre application dans le secteur automobile : une maquette de l’un des derniers modèles de voiture Pininfarina a été produite pour valider sa conception. La pièce réalisée mesure 2,2 x 1 x 0,6m et pèse 250 kg.
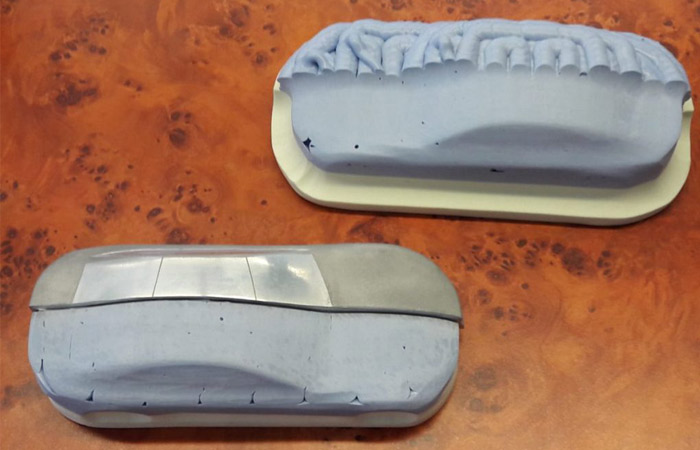
Un premier modèle de voiture créé en utilisant l’extrusion de résine KRAKEN (en haut) et le revêtement métallique (en bas) (crédits photo : KRAKEN Project)
De grands groupes industriels ont déjà exprimé leur intérêt dans la solution : le géant Airbus par exemple devrait commander des pièces d’outillage fabriqués par la machine KRAKEN. Le secteur automobile est également intéressé, notamment pour concevoir des maquettes de production. On comprend assez facilement comment la machine pourrait impacter l’industrie, en permettant la production de grandes quantités de pièces composites, complexes en termes de géométrie et optimisées en termes de poids et performance. On ne connait pas le prix d’une telle solution ; vous pouvez toutefois retrouver plus d’informations ICI.
Que pensez-vous du projet KRAKEN ? Partagez votre avis dans les commentaires de l’article ou avec les membres du forum 3Dnatives. N’hésitez pas à nous suivre sur Facebook ou Twitter !