L’impression 3D métal, pas si simple?
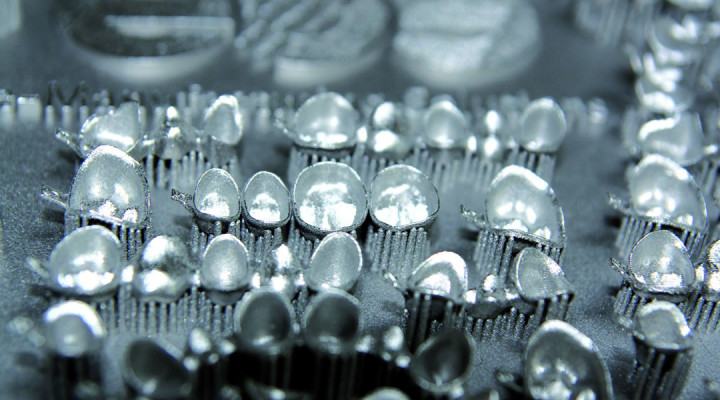
La fabrication additive de pièces métalliques, nom donné à l’impression 3D métal par les industriels, laisse entrevoir de fantastiques possibilités en terme de liberté de conception, de personnalisation de masse ou de relocalisation. Mais il ne faut pas croire que la technologie se résume à un simple bouton sur lequel il faut appuyer pour obtenir sa pièce.
Bien que le procédé soit déjà utilisé dans l’aéronautique et le biomédical, les machines ne permettent pas à elles seules de concevoir des pièces prêtes à l’emploi. Comme en fonderie ou en forge, les pièces fabriquées sont « brutes », c’est à dire qu’un certain nombre d’opérations de finition sont encore à prévoir après la phase de fabrication.
Pour illustrer ce propos, nous sommes allés à la rencontre de la Coopérative Technologies Dentaires, qui a réussi le double exploit grâce à l’impression 3D métal, de réduire les temps de fabrication de prothèses dentaires à moins de 24 heures tout en relocalisant cette production en France. Jean-Michel Bertin, fondateur de CTD, nous a ainsi décrit toutes les étapes nécessaires à la production de pièces finies, dont certaines manuelles, et l’organisation qui permet de tenir des délais aussi courts.
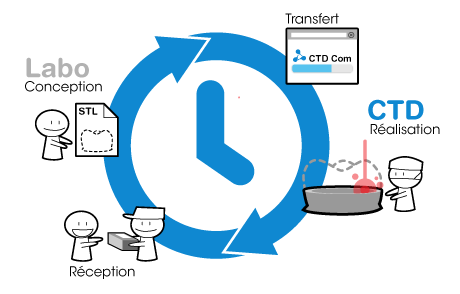
Processus de conception des prothèses dentaires
L’union fait la force
Coopérative Technologies Dentaires est née de l’union de plusieurs laboratoires de prothésistes en France. Cette structure permet à des labos d’avoir accès à des technologies qu’ils ne pourraient pas supporter seuls tels que la fabrication additive. Intégrer une machine de fabrication en interne nécessite en effet de prendre en charge d’une part de lourds investissements de départ, mais aussi les contrats de maintenance, la formation du personnel et enfin le coût d’exploitation.
Se rassembler en une coopérative permet de répartir les investissement sur tout les utilisateurs, mais également d’augmenter le volume de pièces fabriquées par la même machine et donc de réduire les coûts d’exploitations par utilisateur.
En plus de bénéficier d’une technologie de pointe, la production a été pensée de manière à livrer les prothésistes dans des temps records, seulement 24 heures pour une prothèse Chrome-Cobalt. Des délais de livraison qui seraient impensables en sous-traitant la fabrication de l’autre coté du globe.
Préparation de la fabrication
Dans un premier temps, une part importante des durées de production a été gagnée dans la phase de préparation des modèles. Fini le temps où le prothésiste réalisait à la main le moule en cire des prothèses pour fabriquer celles-ci en fonderie. Désormais le prothésiste utilise un scanner 3D fourni par CTD pour numériser l’empreinte des dents du patient réalisée par le dentiste. Un logiciel spécialisé permet de travailler directement sur ce modèle numérique. Le prothésiste peut alors reconstruire la forme des dents telles qu’elles devraient être, puis les prothèses à implanter sur le patient pour arriver à ce résultat, travail qui était auparavant réalisé à la main avec de la cire.
Une fois la forme de la prothèse définie, une option intégrée au logiciel permet d’envoyer directement le fichier à CTD pour fabrication. Le plateau de fabrication de la machine, basée sur la fusion directe de métal par laser, est suffisamment grand pour permettre de réaliser plusieurs dizaines de prothèses en une seule fois.
Chaque jour, à 10 heures du matin, CTD sélectionne l’ensemble des fichiers reçus, les prépare et les envoie à la machine. De manière assez similaire à l’impression 3D de plastique, il est effectivement nécessaire de découper la pièce en tranches de fabrication, de générer des supports pour maintenir la pièce et de générer les trajectoires du faisceau laser. Ces informations sont ensuite transmises à la machine et la fabrication peut commencer.
Étapes de finitions
Une fois l’impression terminée, la plus grosse partie du travail reste à faire pour l’opérateur. Celui-ci commence par aspirer la poudre qui n’a pas été fondue lors de la fabrication. Le plateau sur lequel sont fabriquées les prothèses est alors placé pendant deux heures dans un four de traitement thermique qui chauffe à 800°C. Cela permet à la structure du matériaux de se réorganiser et donc de réduire les contraintes présentes dans la pièce.
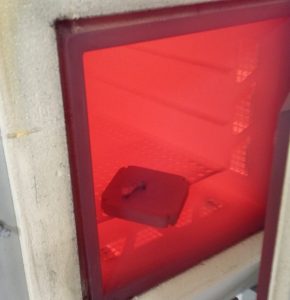
Les prothèses sont chauffés à 800°C pendant 2h pour éviter qu’elles ne se déforment lors de la séparation avec le plateau de fabrication
Un sablage est ensuite réalisé sur les prothèses, qui sont encore fixées au plateau de fabrication, de manière à décoller d’éventuelles particules de poudre restées accrochées à la surface de la pièce. Enfin les prothèses peuvent être retirées du plateau de fabrication.
Sans l’étape de traitement thermique, la relaxation des contraintes lors du retrait des supports provoquerait d’importantes déformations sur les prothèses qui ne seraient donc pas aux bonnes dimensions. Dans le cas de CTD, le retrait des prothèses du plateau est réalisé à la main avec l’aide d’une Dremel. Dans le cas de pièces plus complexes ou de dimensions plus importantes, cette opération peut être réalisée par usinage à commande numérique. Il est dans ce cas nécessaire de prévoir également un programme de fabrication pour la machine d’usinage.
Finalement, l’opérateur poli les prothèses à la main avant de les emballer dans des paquets individuels. A 17 heures, une société de livraison vient récupérer les paquets disponibles pour les livrer aux prothésistes durant la nuit. Cela permet à ces derniers de recevoir les prothèses en moins de 24h après avoir déposé le fichier en ligne sur le logiciel de CTD. Pour ceux qui auraient raté la production de 10 heures , CTD lance une deuxième série chaque jour à 17h, les pièces sont alors sorties de la machine le matin et le post traitement est réalisé pendant que la machine construit la série du matin.
Si la possibilité pour les dentistes de fabriquer eux mêmes leurs prothèses depuis leurs propres bureaux n’est encore qu’un rêve lointain, CTD nous montre comment l’impression 3D métal a bel et bien déjà commencé à modifier en profondeur les schémas de production de certaines industries. Et cerise sur la gâteau, la production reste Made in France !

Les prothèses imprimées en 3D avant finition
Pour rester informé abonnez-vous à notre flux RSS ou pages Facebook Twitter Google+ ou LinkedIn
Super cet article!
Merci guillaume. Chouette article
merci!
Article très intéressant. Merci pour ce retour d’experience.
[…] pour créer des prothèses dentaires en moins de 24 heures (voir notre interview du fondateur ICI) alors que certains hôpitaux comme le CHU de Dijon se sont équipés afin de former les futurs […]