Pourquoi les industriels misent-ils sur l’impression 3D FFF céramique ?
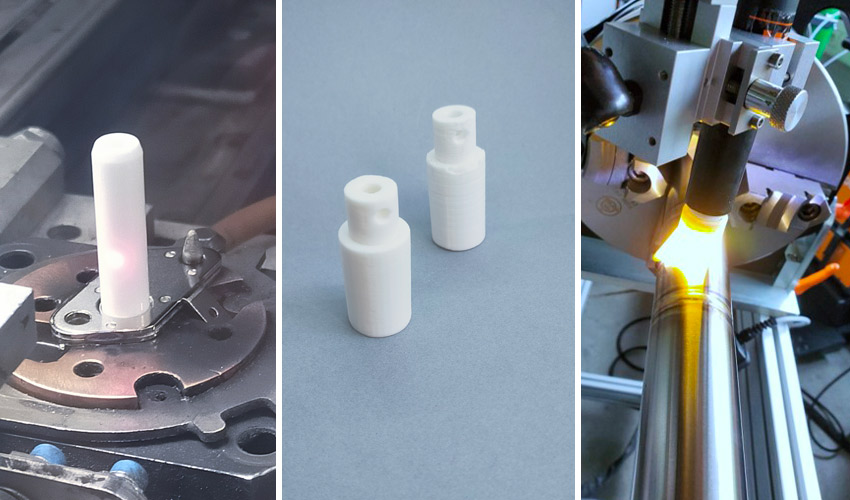
Depuis son arrivée sur le marché de la fabrication additive en 2018, Nanoe s’efforce de démocratiser l’utilisation de l’impression 3D céramique et métallique grâce à un procédé accessible et facile à mettre en place. Alors que ses filaments ont fait leur place dans les laboratoires et centres de recherche en France et à l’international, ils gagnent de plus en plus de terrain chez les industriels qui misent sur l’intégration de la fabrication additive en interne. Les matériaux céramiques du fabricant français apportent en effet plusieurs propriétés thermiques, chimiques et mécaniques intéressantes pour des activités exigeantes comme le soudage orbital, la production de pièces pour des chaudières ou encore la fabrication de pièces décolletées. Grâce aux filaments Zetamix, plusieurs industriels internationaux sont capables d’accroître leur agilité en diminuant les délais de production et les temps d’immobilisation machines, mais aussi en réduisant les coûts.
Parmi les utilisateurs des solutions de fabrication additive céramique Zetamix, on peut citer 3 industriels : MGB, SAPCO et Orbital Service. Si les technologies 3D leur offrent aujourd’hui de nombreux avantages, ils ont tous les trois été séduits par les capacités thermiques des filaments céramiques, que ce soit de la zircone ou de l’alumine. Ces trois industriels avaient en effet des problématiques très spécifiques qui étaient difficilement solutionnables via la fabrication soustractive, ou du moins à des coûts et des délais beaucoup plus élevés.
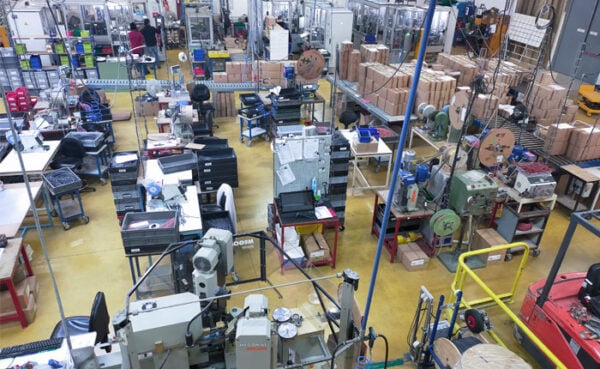
Les industriels sont de plus en plus nombreux à intégrer la fabrication additive (crédits photo : SAPCO)
L’alumine, un matériau d’impression 3D résistant aux hautes températures
MGB est une entreprise française créée en 1956, spécialisée dans la fabrication de pièces décolletées pour l’industrie de la connectique. Elle travaille principalement avec des acteurs dans le médical, l’aéronautique ou encore l’électronique, acteurs qui ont besoin de vis sur-mesure. Celles-ci possèdent des niveaux de dureté différents, avec généralement le bas de la vis qui est moins résistant que le haut. Pour produire ce type de vis personnalisée, MGB a développé une machine spécifique qui permet de recuire la partie supérieure via induction pour apporter toute la dureté nécessaire.
C’est dans cette machine que MGB a intégré une pièce imprimée en 3D à partir d’alumine. Il s’agit d’un support sur-mesure poinçonné en son extrémité dans lequel l’industriel français place la vis en question. Elle est ensuite chauffée tandis qu’un détecteur de chaleur surveille la température. Il fallait donc imaginer un guide qui puisse à la fois résister à une telle température, épouser parfaitement la forme de la vis en question et supporter la présence du détecteur électrique. Un défi qui n’aurait pas pu être relevé aussi rapidement sans l’intégration de la fabrication additive. MGB affirme que le processus de design et de fabrication d’un nouveau support de vis prend moins d’une semaine. Un délai inimaginable si l’industriel était passé par la fabrication soustractive ou par un prestataire.
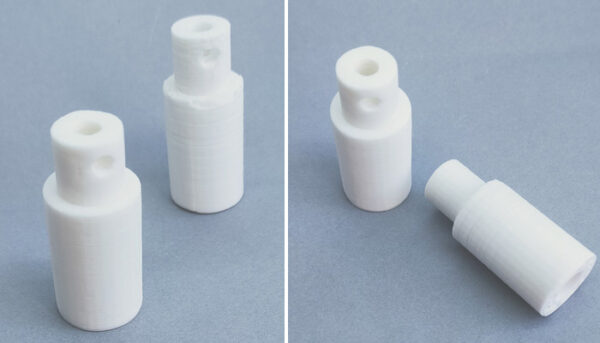
Les supports de vis imprimés en 3D (crédits photo : Nanoe)
Améliorer les procédés de soudage orbital grâce aux filaments Zetamix
Orbital Service est une société allemande spécialisée dans le soudage orbital qui a également misé sur la solution Zetamix pour produire des pièces sur-mesure. Dans le cadre de son activité, les opérations de soudage TIG (tungstène gaz inerte) posent de nombreux défis notamment pour éviter l’oxydation et la contamination de l’air. Afin d’y remédier, l’entreprise doit créer un arc électrique et pulvériser un gaz inerte de protection autour de la zone à souder. Or, dans le cadre du soudage orbital, les tubes à souder sont très volumineux et les buses de soudage TIG ne sont pas adaptées. Cela favorise alors l’oxydation et le post-traitement des pièces. La cadence est considérablement ralentie et le processus est peu fiable.
C’est là que la fabrication additive a une carte à jouer. Orbital Service s’est appuyé sur la technologie FFF et les filaments Zetamix – plus particulièrement l’alumine, afin de concevoir des buses TIG sur-mesure. Celles-ci ont désormais une forme concave, plus adaptée au volume des tubes à souder. Les défauts de soudure sont ainsi réduits ainsi que la consommation de gaz inerte nécessaire. L’industriel allemand a privilégié l’alumine pour sa résistance à la température et affirme que l’ensemble du processus de conception et fabrication ne prend qu’une semaine.
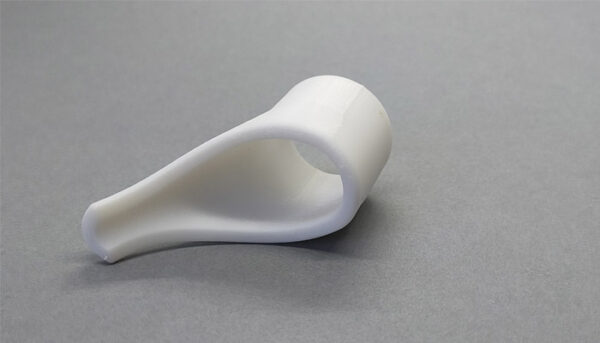
Grâce à la fabrication additive, Orbital Service peut concevoir des buses concaves plus adaptées (crédits photo : Nanoe)
Le choix de la solution Zetamix pour réduire les temps de maintenance
L’industriel SAPCO fabrique des électrodes d’allumage et d’ionisation en céramique, intégrées dans les chaudières et brûleurs industriels. Pour ce faire, la société a développé des processus de production automatisés via des machines sur-mesure, notamment en ce qui concerne l’étape d’assemblage. Toutefois, celle-ci reste complexe : pendant le soudage de l’électrode, 2 tranches métalliques sont placées autour de la pièce, tranches qui sont installées via des broches de soudage en plastique. Or, celles-ci sont très vite endommagées à cause de la température élevée, entraînant alors un arrêt de la machine en question, au moins une fois par jour. Ce temps d’immobilisation impacte l’ensemble du processus de production de SAPCO, l’obligeant à imaginer un autre moyen de produire ces broches.
Le recours à l’injection céramique a d’abord été envisagé par l’entreprise mais rapidement, elle s’est avérée être peu pratique, chère et difficile à implémenter. SAPCO s’est donc tournée vers la fabrication additive et a misé sur la céramique plutôt que le polymère. Elle a opté pour du zircone, capable de résister à des températures atteignant les 800°C. La solution Zetamix était idéale car facile à déployer et à utiliser. En 5 jours, les équipes ont pu imaginer et produire des broches de soudage optimisées. Elles doivent être changées une fois par mois ce qui réduit considérablement la maintenance des machines et le temps d’immobilisation.
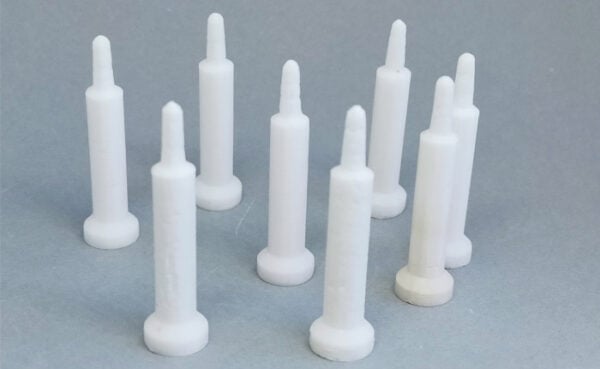
Les broches de soudage sont imprimées en 3D avec du zircone (crédits photo : Nanoe)
Une réponse aux problématiques d’outillage interne
Quand il s‘agit de produire de l’outillage interne, les industriels peuvent donc s’appuyer sur l’impression 3D FFF céramique pour gagner en agilité et augmenter leur productivité. Le choix de la céramique permet à des secteurs tels que l’aéronautique, l’automobile, la fonderie ou encore la joaillerie de résister à des températures extrêmement élevées et à d’autres contraintes chimiques et mécaniques.
Enfin, opter pour les solutions proposées par Nanoe permettra à l’utilisateur de déployer une offre peu coûteuse comparée à d’autres procédés d’impression céramique. Au-delà du prix, c’est aussi une question de facilité d’utilisation. Le procédé FFF reste simple à prendre en main et à intégrer au sein des lignes de production. Cela est particulièrement vrai quand il s’agit d’outillage interne : le choix de la solution Zetamix sera plus approprié que d’autres procédés tels que la photopolymérisation qui sera davantage préférée pour la fabrication de pièces très précises dans le biomédical par exemple. Vous pouvez vous rendre sur le site du fabricant français afin d’en savoir plus sur sa gamme de filaments.
Que pensez-vous de l’intégration de l’impression 3D céramique dans l’Industrie ? Partagez votre avis dans les commentaires de l’article ou avec les membres du forum 3Dnatives. Retrouvez toutes nos vidéos sur notre chaîne YouTube ou suivez-nous sur Facebook ou Twitter !