L’impression 3D dans le processus de développement des fusées
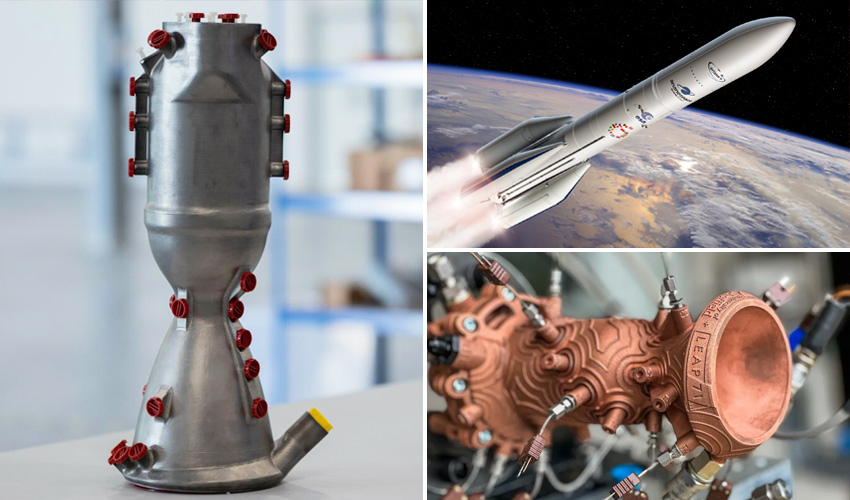
Depuis l’alunissage de 1969, l’humanité n’a jamais cessé de viser les étoiles. Ce qui a changé, en revanche, ce sont les moyens d’y parvenir. Depuis Apollo 11, les fusées ont énormément évolué, l’innovation étant le maître mot et, ces dernières années, le marché a vu apparaitre la fabrication additive. Nous voyons de plus en plus de fusées imprimées en 3D, qu’elles soient en cours de développement ou qu’elles aient déjà été envoyées dans l’espace. Dans la liste suivante, aléatoirement triée, nous avons examiné certains des projets les plus passionnants, allant des fusées entièrement imprimées en 3D aux moteurs et autres pièces fabriquées et optimisées grâce aux technologies 3D.
Agnibaan d’Angikul Cosmos
Agnibaan est l’un des plus récents projets de fusée imprimée en 3D. Il émane directement d’Agnikul Cosmos, un fabricant indien de matériel aérospatial qui estime que l’accès à l’espace devrait être à la portée de tous. C’est pour cette raison que l’entreprise s’est tournée vers l’impression 3D. Agnibaan (qui signifie « flèche de feu » en sanskrit) est, selon l’entreprise, la première fusée au monde dotée d’un moteur imprimé en 3D d’une seule pièce, bien qu’Agnikul n’ait pas annoncé quelles technologies ont été utilisées pour ce projet. Le lancement réussi d’Agnibaan le 30 mai à 7h15 marque un grand pas en avant pour la fabrication additive dans l’industrie spatiale indienne.
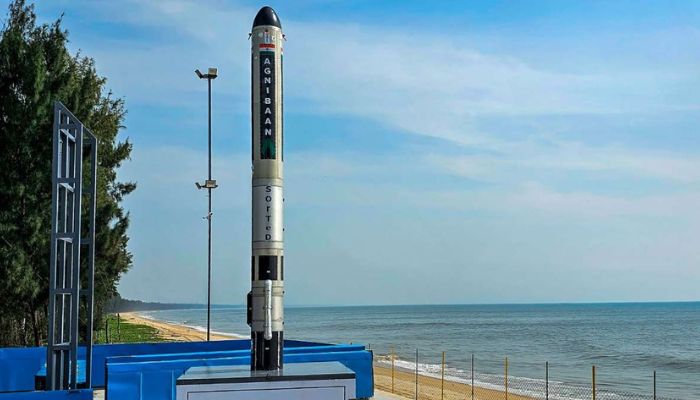
Crédits photo : Angikul Cosmos
Le moteur-fusée E-2 de Launcher
Launcher est une entreprise fondée en 2017 qui a travaillé en partenariat avec l’US Space Force, l’US Air Force et la NASA sur le développement de fusées et de véhicules de transfert orbital de haute performance. L’intégration d’une technologie de pointe en matière de propulsion liquide et l’utilisation de l’impression 3D ont donné naissance au moteur-fusée à propergol liquide E-2. Il s’agit d’un moteur à combustion fermée dont la chambre de combustion est constituée d’un alliage de cuivre, de chrome et de zirconium, ce qui réduit les coûts ainsi que la dépendance vis-à-vis des chaînes d’approvisionnement. Launcher est ainsi la première entreprise dans le domaine des lanceurs à utiliser des alliages de cuivre imprimés en 3D pour la fabrication de la chambre de combustion d’un moteur-fusée. En outre, cette dernière est dotée de canaux de refroidissement intégrés destinés à améliorer l’efficacité thermique. En collaboration avec l’AMCM, Launcher a développé l’imprimante 3D AMCM M 4K, qui a ensuite été utilisée pour imprimer la chambre de combustion. L’injecteur coaxial du moteur E-2 a été produit sur l’imprimante 3D Sapphire de Velo3D. En avril 2022, le moteur E-2 imprimé en 3D a atteint sa pleine poussée lors de tests effectués au Stennis Space Center de la NASA, à la suite de quoi Launcher a annoncé la réussite de l’essai.
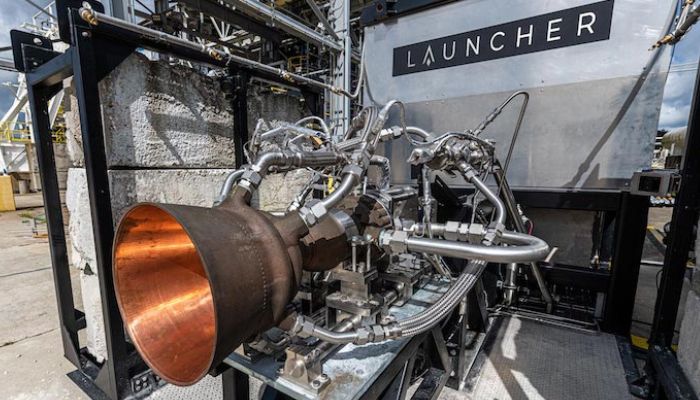
Crédits photo : Launcher
La fusée ArianeGroup réalisée en partie par impression 3D
ArianeGroup est une entreprise commune d’Airbus Group et de Safran. Avec Ariane 6, ArianeGroup a produit le lanceur lourd le plus récent d’Europe, dont le premier lancement a été un succès en juillet 2024. Arian 6 a une structure flexible et peut transporter de très grandes charges. Pour la fabrication d’Ariane 6, ArianeGroup a eu recours à l’impression 3D industrielle. De nombreux composants du moteur ont ainsi été fabriqués de manière additive, ce qui a permis de réduire les coûts et de minimiser les cycles de production. La chambre de combustion a été conçue et fabriquée en Allemagne. L’enveloppe du liner a été imprimée par exemple par projection à froid et la tête d’injection monobloc a été imprimée par frittage laser. Cette tête d’injection, avec tous ses éléments, a été fabriquée par EOS.
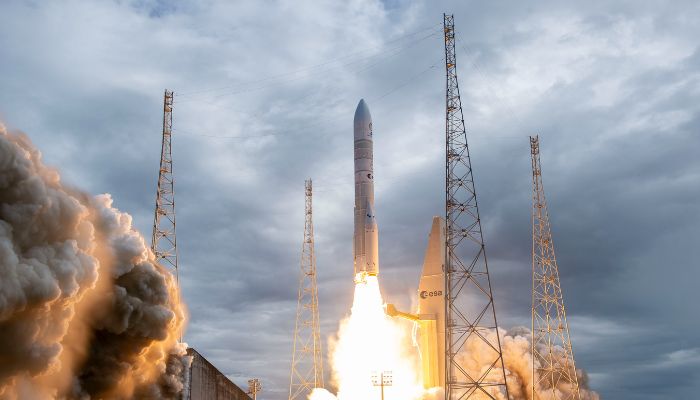
Crédits photo : ArianeGroup
Skyroot Aerospace et son moteur imprimé en 3D
Créée en 2018, l’entreprise indienne Skyroot Aerospace s’est donnée comme objectif d’ouvrir l’espace à tous en proposant des lanceurs spatiaux rapides, précis et abordables. Elle a développé plusieurs modèles sous sa gamme Vikram. Mais ce qui nous intéresse plus particulièrement sont les moteurs de ces fusées. Baptisé Dhawan, il s’agit d’une pièce imprimée en 3D. C’est un moteur cryogénique qui utilise à la fois du gaz naturel liquide et de l’oxygène liquide. Ces deux propergols nécessitent des températures inférieures à -150°C pour être stockés et fonctionner. Qu’il s’agisse du Dhawan-I ou de la seconde version, c’est donc la fabrication additive métal qui a été retenue. Les deux moteurs ont été testés avec succès. Le moteur Dhawan-II devrait être installé dans la fusée Vikram-II qui devrait décoller à la fin de l’année.
Le moteur Hadley imprimé en 3D par Ursa Major
Ursa Major est une autre startup américaine qui a attiré l’attention pour son travail sur les fusées imprimées en 3D. En mars 2024, l’entreprise a annoncé que son moteur Hadley, partiellement imprimé en 3D, avait réussi à s’envoler, frôlant Mach 5. Bien que l’on ne sache pas exactement quelles technologies et quels matériaux ont été utilisés pour créer le moteur Hadley, nous savons que l’impression 3D a joué un rôle important et qu’elle a probablement été réalisée à partir de cuivre, très probablement par fusion laser sur lit de poudre en raison des travaux antérieurs de l’entreprise avec EOS.

Essai à chaud du moteur Hadley (crédit photo : Ursa Major)
Le moteur-fusée à détonation (RDRE) de la NASA
La NASA ne cesse d’établir de nouvelles références en matière de technologie de propulsion. Elle a ainsi fabriqué le premier moteur de fusée à détonation rotative (RDRE) en taille réelle à l’aide de l’impression 3D. À l’avenir, ce moteur pourrait redéfinir la conception des systèmes de propulsion. Le RDRE utilise un concept de propulsion avancé dans lequel la poussée est générée par le phénomène de combustion supersonique. Cela permet d’obtenir une puissance plus élevée tout en consommant moins de carburant. Le moteur a été fabriqué par fusion laser sur lit de poudre, en utilisant l’alliage de cuivre GRCop-42 développé par la NASA, qui permet au moteur de fonctionner pendant de longues périodes dans des conditions extrêmes. En automne 2023, la NASA a effectué une série de tests au Marshall Space Flight Center afin de vérifier si le moteur pouvait résister aux températures extrêmes et aux exigences typiques, comme l’intégration d’une sonde lambda. Les tests ont été concluants et le RDRE offre ainsi le potentiel nécessaire pour soutenir les futures missions vers la Lune ou Mars.
EOS et Hyperganic impriment un moteur de fusée Aerospike
En 2022, EOS et Hyperganic ont annoncé avoir réussi à fabriquer un moteur de fusée Aerospike au design particulièrement complexe à l’aide de l’intelligence artificielle et de l’impression 3D. Hyperganic, une entreprise allemande fondée en 2015, a réussi à reproduire un design inspiré de la nature grâce à son logiciel de conception algorithmique. Le moteur de fusée Aerospike se distingue donc par son design exceptionnel et extrêmement complexe. Dans un premier temps, le moteur a été imprimé en 3D à partir d’un alliage de nickel, en utilisant la machine EOS M 400-4 et l’alliage NickelAlloy IN718. Dans un deuxième temps, le moteur a été fabriqué à plus grande échelle en cuivre.
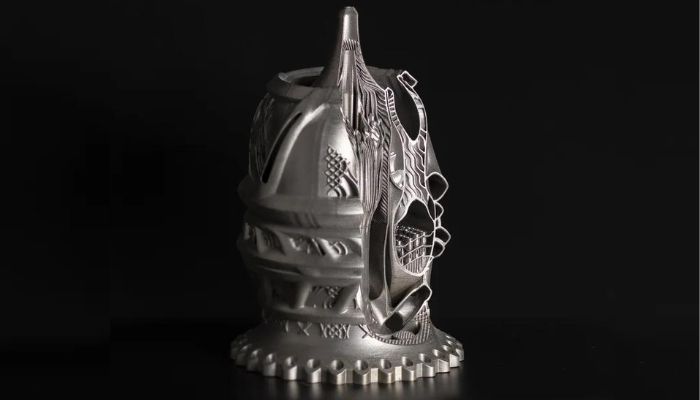
Crédits photo : EOS
IA et impression 3D pour le moteur-fusée à propergol liquide TKL-5
Grâce à l’utilisation de l’ingénierie informatique et de la fabrication additive, LEAP 71, une entreprise basée à Dubaï, a réalisé des progrès significatifs dans la technologie spatiale. En effet, l’entreprise a développé un moteur de fusée au moyen du logiciel Noyron basé sur l’IA. L’objectif du projet était de démontrer les capacités du logiciel qui a permis de concevoir et de produire le moteur de fusée TKL-5 de manière entièrement numérique, sans intervention humaine. Grâce aux algorithmes d’intelligence artificielle, aucune conception CAO n’a été nécessaire, ce qui a permis d’optimiser la production totale du moteur en seulement deux semaines. Le moteur a été produit par AMCM sur une imprimante 3D EOS M290 en cuivre, ce qui, combiné à un refroidissement actif, a permis d’obtenir un moteur performant. L’équipe « Race to Space » de l’université de Sheffield a ensuite procédé au post-traitement et le moteur a été testé avec succès sur le site d’Airborne Engineering. Il y a atteint une poussée de 20 000 CV et convient donc parfaitement à une utilisation dans des fusées orbitales.
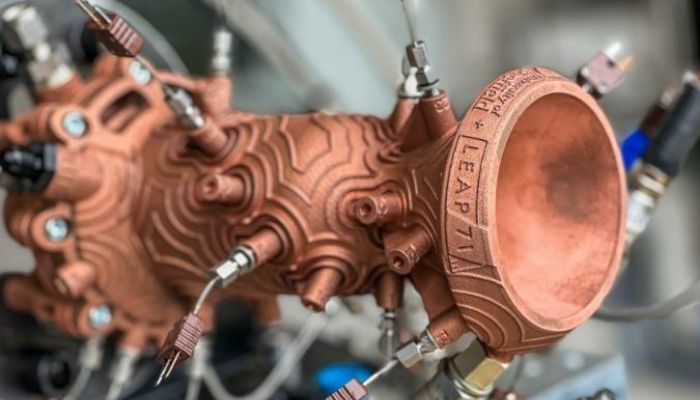
Crédits photo : LEAP 71
La fusée Orbex Prime
La société aérospatiale britannique Orbex a mis au point une fusée à haute performance et à faible émission de carbone, Orbex Prime. La fusée a été construite à l’aide de l’imprimante 3D métal SLM800 de Nikon SLM Solutions. Prime est alimentée par un carburant 100 % renouvelable, le biopropane, qui permet de réduire les émissions de CO2 de 90 %. En outre, la fusée est conçue pour être réutilisable grâce à un système de récupération, également programmé pour ne laisser aucun débris en orbite autour de la Terre. Prime a été dévoilé publiquement pour la première fois en 2022 au Royaume-Uni.
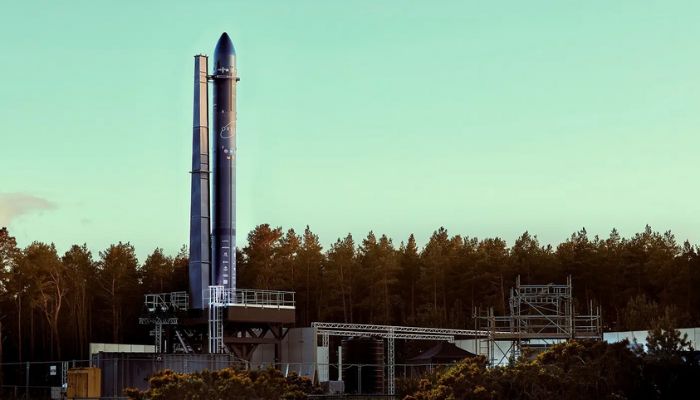
Crédits photo : Orbex
Les fusées Terran 1 et Terran R imprimées en 3D par Relativity Space
Qui, à l’heure actuelle, n’a pas entendu parler de Relativity Space ? L’entreprise californienne s’est rapidement fait un nom depuis sa création en 2015, en travaillant à son objectif de créer une fusée entièrement imprimée en 3D. Et elle y est presque ! Terran 1, la première fusée de l’entreprise, a été lancée avec succès en mars 2023, sans toutefois atteindre l’orbite. Cette fusée a été presque entièrement imprimée en 3D à l’aide de la technologie DED et de la fusion laser sur lit de poudre. Au moment de son lancement, elle était la plus haute structure métallique imprimée en 3D jamais construite. Les travaux de l’entreprise se poursuivent avec le Terran R, qui devrait être imprimé à 90 % en 3D et capable de transporter une charge utile 20 fois supérieure à celle de son prédécesseur. La Terran R sera lancée depuis le complexe de lancement 16 de la base spatiale de Cap Canaveral à partir de 2026, s’envolant directement vers l’avenir de l’exploration spatiale.

Crédits photo : Relativity Space
Navier, le moteur français réalisé par fabrication additive
Latitude (anciennement Venture Orbital Systems) est une startup française spécialisée dans la conception de microlanceurs. Son premier modèle est le Zephyr qui mesure 19 mètres de long pour un diamètre de 1,5 m. Il est équipé d’un moteur fabriqué par impression 3D métal – plus particulièrement par fusion laser sur lit de poudre. Baptisé Navier, il mesure 45 centimètres de hauteur et pèse 30 kilos, le tout pour une poussée de 1,2 tonne. Il a été fabriqué à partir d’Inconel 718 sur une machine SLM 500 en quelques jours seulement. Au début de l’année 2023, Latitude avait réussi la mise à feu de Navier, une belle avancée pour la startup basée à Reims.
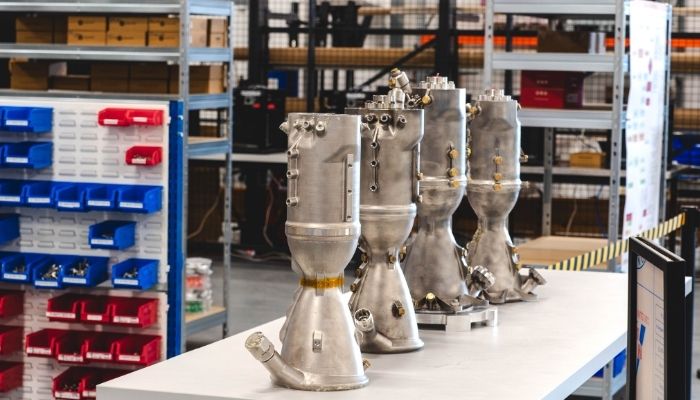
Crédits photo : Latitude
Le moteur Rutherford de Rocket Lab
La startup californienne Rocket Lab, une entreprise aéronautique privée, a développé la première fusée au monde alimentée par une batterie, la fusée Electron, qui a effectué avec succès son premier lancement en 2017 avec un moteur Rutherford imprimé en 3D. Il porte le nom du scientifique néo-zélandais Ernest Rutherford et les composants imprimés en 3D comprennent la chambre de poussée, deux pompes, l’injecteur et les principales valves de carburant. Pour le premier vol, Rocket Lab a utilisé une fenêtre de lancement de dix jours pour lancer la fusée depuis la péninsule de Mahia en Nouvelle-Zélande. Le deuxième vol, qui a eu lieu en 2018, était un vol spatial orbital. Après celui-ci, l’entreprise a décidé de passer à l’exploitation commerciale. L’utilisation de la fabrication additive pour la production du moteur Rutherford a permis de gagner du temps et du poids.
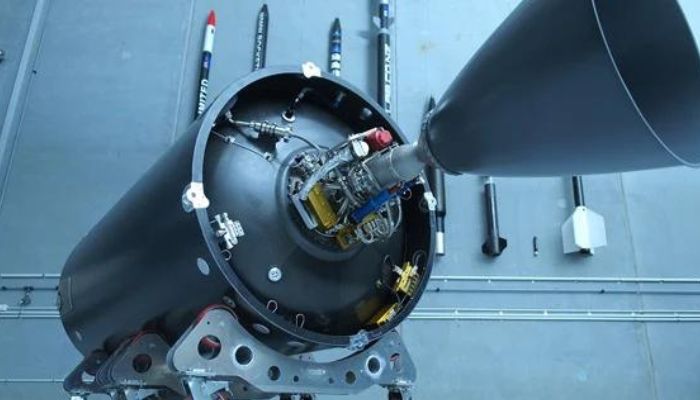
Crédits photo : Rocket Lab
Une chambre de combustion imprimée en 3D
OPUS Aerospace est une autre entreprise française spécialisée dans la conception de lanceurs et engins spatiaux. Elle a développé deux lanceurs différents, Mesange et Sterne. Le premier est en réalité le démonstrateur de la jeune pousse française. Mesange servira en effet de test et ouvrira la voie à Sterne. Dans les deux cas, le lanceur intègre le moteur Torgos dont la chambre de combustion a été imprimée en 3D métal en une seule fois. Le lancement de Mesange est prévu en 2024 depuis la Guyane et permettra donc de perfectionner le lanceur Sterne.
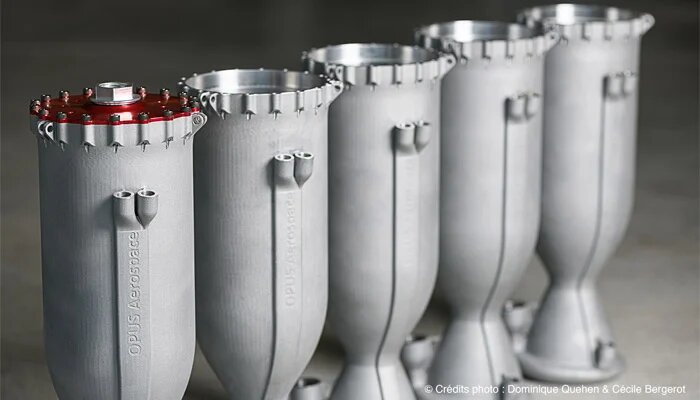
Crédits photo : Dominique Quehen et Cécile Bergerot
Stoke Space imprime des chambres de combustion pour des fusées réutilisables
Avec NOVA, l’entreprise américaine Stoke Space propose une fusée entièrement réutilisable pour des vols quotidiens dans l’espace. Pour y parvenir, l’entreprise mise également sur l’impression 3D. Stoke Space imprime des chambres de combustion en cuivre afin, d’une part, de les produire rapidement et, d’autre part, de permettre leur réutilisation. L’alliage de cuivre des chambres de combustion est en effet particulièrement conducteur et peut donc être réutilisé. En raison des canaux de refroidissement régénératifs, les chambres de combustion présentent des tubes de distribution courbés et des cavités internes. La fabrication additive rend toutefois possible la réalisation de ce design complexe.
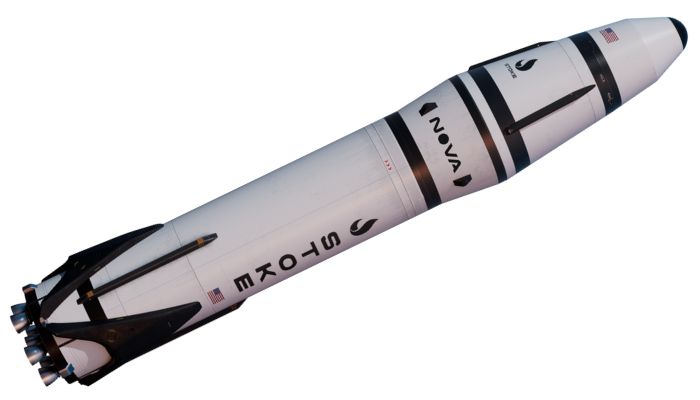
Crédits photo : Stoke Space
Que pensez-vous de l’utilisation de l’impression 3D pour concevoir des fusées, lanceurs et engins spatiaux ? Partagez votre avis dans les commentaires de l’article. Retrouvez toutes nos vidéos sur notre chaîne YouTube ou suivez-nous sur Facebook ou LinkedIn !
Le moteur Navier de Latitude développe une poussée de 45 kN (4,5 tonnes) et non 1,2 tonnes.
https://fr.wikipedia.org/wiki/Z%C3%A9phyr_(fus%C3%A9e)
j’adore