Un procédé d’impression 3D de verre par photopolymérisation (DLP)
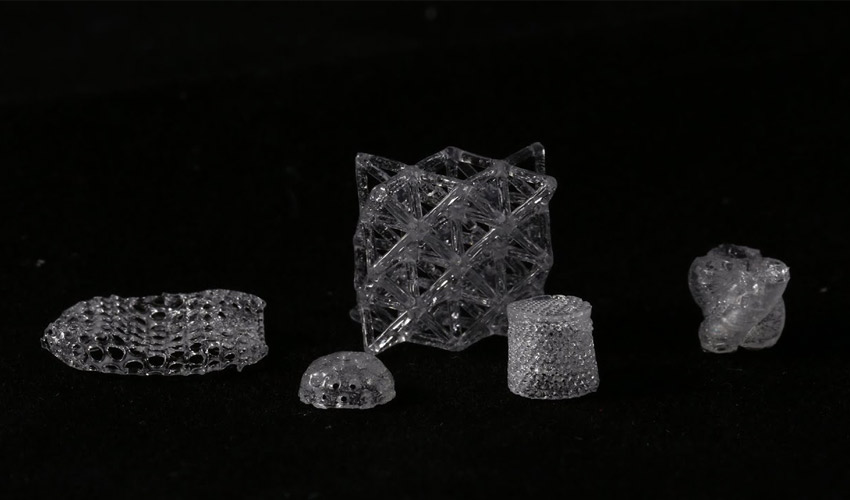
A partir d’une résine spécifique et d’un procédé de stéréolithographie, un groupe de scientifiques de l’ETH Zurich en Suisse a réussi à imprimer en 3D des objets en verre d’une grande précision, riches en détails et d’une porosité élevée. Leur méthode de fabrication additive a recours à une résine contenant un plastique et des molécules organiques qui, une fois exposés à une source de chaleur, durcissent et forment la pièce souhaitée couche par couche.
L’impression 3D de verre n’est pas un nouvel accomplissement sur le marché : on pense à la startup Glassomer qui s’est lancée sur ce créneau ou encore aux travaux du MIT. Le processus reste toutefois difficile à maîtriser, de par les températures qu’il faut savoir contrôler. La plupart des acteurs ont en effet recours à du verre fondu pour produire des pièces plus ou moins complexes ; cela nécessite un équipement très résistant à la chaleur et des températures très élevées. D’autres se penchent plutôt vers la céramique en poudre qui, frittée ensuite, crée un objet en verre. Cette méthode limite la complexité des formes obtenues et leur précision. Les travaux de l’ETH Zürich sont dans ce sens innovants puisque les scientifiques ont utilisé un procédé de photopolymérisation DLP.
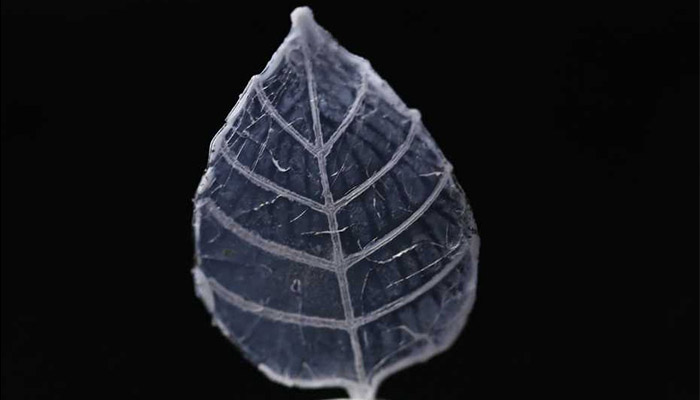
Le procédé développé permet d’atteindre un haut niveau de détails (crédits photo : ETH Zürich)
Le processus d’impression 3D de verre DLP développé par l’ETH Zürich
Les chercheurs expliquent qu’ils ont photopolymérisé une résine à base de plastique et de molécules organiques à laquelle sont liées des molécules contenant du silicone. Sous l’effet de la lumière UV, les monomères plastiques se relient les uns aux autres afin de former une structure entrelacée, créant le polymère. Le silicone permet quant à lui de remplir les trous de cette structure. Ce qui est particulièrement intéressant avec cette méthode est la possibilité pour les chercheurs de modifier certains paramètres de chaque couche, y compris la taille des pores : une faible intensité lumineuse entraînera de grands pores tandis qu’un éclairage intense produira de petits pores. Les chercheurs affirment qu’ils peuvent aussi modifier la microstructure en mélangeant de la silice avec du borate ou du phosphate et en l’ajoutant à la résine.
Une fois le processus de photopolymérisation terminée, les scientifiques attaquent le post-traitement avec deux méthodes de cuisson : une à 600°C pour brûler la structure polymère et ainsi retirer tous les résidus ; une autre à 1000°C pour densifier la pièce en verre. Pendant ces étapes, les objets rétrécissent considérablement, mais deviennent transparents et durs comme du verre à vitre.
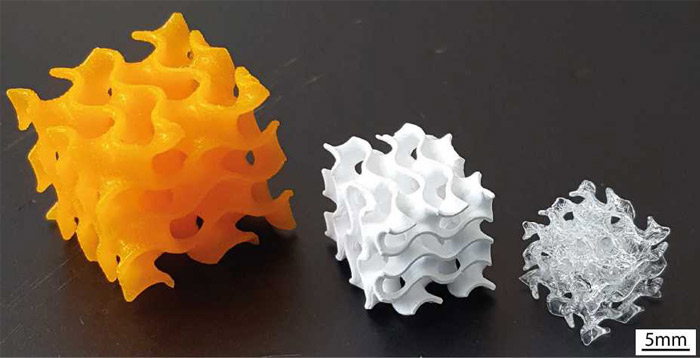
Les différentes étapes de cuisson : à droite, vous pouvez voir la pièce après la cuisson à 1000°C. La taille de l’objet a bien diminué (crédits photo : ETH Zürich)
Notez que la taille des pièces imprimées en 3D en verre est encore très petite – on est encore loin de produire des bouteilles en verre. Les chercheurs précisent que ce n’était pas leur objectif initial : ils souhaitaient surtout montrer la viabilité de leur méthode. Ils ont d’ailleurs fait leur demande de brevet – affaire à suivre ! En attendant, vous pouvez retrouver davantage d’informations sur le site de l’ETH Zürich.
Que pensez-vous de ce procédé d’impression 3D de verre DLP ? Partagez votre avis dans les commentaires de l’article ou avec les membres du forum 3Dnatives. N’hésitez pas à nous suivre sur Facebook ou Twitter !
Madame, Monsieur,
Tout d’abord, merci pour votre article.
Ensuite, attention à ne pas confondre silicone, silicium, oxyde de silicium et autres erreurs…
En effet, vous écrivez dans l’article :
« Les chercheurs expliquent qu’ils ont photopolymérisé une résine à base de plastique et de molécules organiques à laquelle sont liées des molécules contenant du silicone. Sous l’effet de la lumière UV, les monomères plastiques se relient les uns aux autres afin de former une structure entrelacée, créant le polymère. Le silicone permet quant à lui de remplir les trous de cette structure. »
Dans un premier temps, vous annoncez que les chercheurs ont utilisé « une résine à base de plastique et de molécules organiques à laquelle sont liées des molécules contenant du silicone », ce qui est inexact puisque, d’après l’article original, il s’agit en réalité d’une résine à plusieurs phases (https://www.researchgate.net/publication/337175292_Three-dimensional_printing_of_multicomponent_glasses_using_phase-separating_resins). L’une contenant le monomère qui sera photopolymérisé et l’autre contenant le précurseur de type silicone. Nous sommes donc en présence de ce que l’on pourrait assimiler à une vinaigrette où silicone et monomère sont mélangés. Il n’y a cependant pas de liaisons entre les phases, elles sont juste mélangées à la manière de l’huile et de l’eau.
Ensuite, vous parlez de « résine à base de plastique et de molécules organiques ». Là où cela m’étonne, c’est qu’un polymère, plus communément appelé plastique est normalement un matériau solide issu d’une réaction de polymérisation mettant en jeu un ou plusieurs monomères généralement en phase liquide, lesdits monomères étant effectivement constitués « de molécules organiques ». Dès lors, comment une résine pourrait-elle être « à base de plastique » et un monomère être « plastique » ?
Vous parlez également de « silicone » et de « molécules contenant du silicone »… Or, après lecture de l’article original il apparait qu’il ne s’agit pas nécessairement d’un silicone mais d’un polymère pré-céramique. En d’autres termes, un matériau qui traité dans les bonnes conditions permet d’obtenir une céramique. Parmi ces derniers on retrouve notamment les polysiloxanes qui sont à la base des silicones que l’on utilise aujourd’hui (joint rubson, lubrifiant, …). Ici, il ne s’agit donc en rien de « molécules contenant du silicone » mais de silicone, tout simplement.
Pour la partie post-traitement, la première cuisson permet certes d’éliminer la structure polymère, mais également de déclencher la pyrolyse du matériau précurseur, une réaction qui permet d’obtenir – toujours d’après l’article – des oxydes de silicium (SiO2), de phosphore (P2O5) et de bore (B2O3). La seconde phase de cuisson permet quant à elle de fusionner les oxydes obtenus précédemment pour obtenir un verre multicomposant dont la composante majoritaire est le dioxyde de silicium ou silice.