L’impression 3D composite : on vous explique tout !

Les matériaux composites sont issus de l’union d’au moins deux matières différentes. L’une sert de matrice et est destinée à maintenir la structure, tandis que l’autre fournit des propriétés supplémentaires en tant qu’élément de renforcement. Le but d’un composite consiste à ajouter des propriétés positives à celui qui sert de matrice et, si nécessaire, à neutraliser ses propriétés négatives. En ajoutant les propriétés du matériau de renfort respectif au matériau de matrice, ce dernier obtient de meilleures propriétés mécaniques, une couleur différente, une résistance au feu, une stabilité, une capacité de charge, etc. Les matériaux composites peuvent être globalement distingués par leurs caractéristiques matérielles (métalliques, minérales, céramiques, organiques) ou par leur géométrie. Selon les propriétés géométriques, on peut trouver :
- Matériaux composites à particules
- Matériaux composites fibreux (fibres courtes, longues ou continues)
- Matériaux composites en couches
- Matériaux composites de pénétration
Les composites de fibres sont particulièrement populaires dans la technologie des matériaux car ils permettent de renforcer les matériaux dans certaines directions. La fibre de carbone est probablement la plus populaire sur le marché, suivie de la fibre de verre, qui est également l’une des plus utilisées dans la fabrication additive.
Les propriétés des matériaux composites
Les matériaux renforcés pour la fabrication additive sont généralement à base de nylon, mais aussi d’ABS, de PLA, de PC et de PETG. Actuellement, les composites les plus couramment utilisés dans l’impression 3D sont la fibre de carbone, la fibre de verre et la fibre d’aramide Kevlar (PPD-T). Ces matériaux offrent des avantages pour réaliser des pièces légères mais résistantes. Pour les fonctions esthétiques, on peut également opter pour les fibres de bois, les particules de céramique et les fibres végétales en combinaison avec le PLA. Comme nous l’avons évoqué, il existe plusieurs types de renfort : fibre courte, longue ou continue. Dans le premier cas, les fibres courtes formées de segments de moins d’un millimètre de longueur sont mélangées à des thermoplastiques classiques pour augmenter la rigidité et la résistance des composants.
Cependant, la plus grande part des performances provient du renforcement avec des fibres continues. Le processus de fabrication des composites à fibres continues n’est pas aussi simple que celui des fibres discontinues, car elles doivent être intégrées en continu dans les thermoplastiques au fur et à mesure de leur extrusion. Les fibres peuvent également être appliquées selon des techniques de conception (DfAM) qui optimisent le rapport résistance/poids d’une pièce et la consommation de matière. Les fabricants affirment que le renforcement en fibres continues peut rendre les pièces aussi solides que le métal.
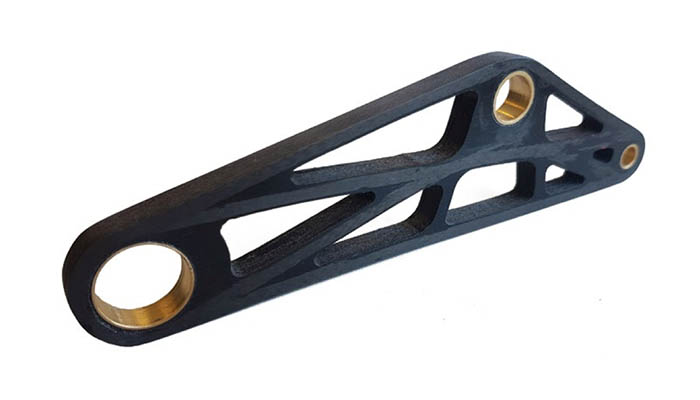
Une pièce imprimée en 3D avec renfort en fibre de carbone, obtenant un rapport pondéral plus élevé et une consommation de matière moindre (crédits photo : 9TLabs)
Les composites en impression 3D
Dans la fabrication additive, les matériaux composites se présentent principalement sous la forme d’un filament, c’est pourquoi ils sont principalement utilisés dans l’impression FDM. Cependant, les composés métalliques pour des procédés comme le procédé de fusion laser sur lit de poudre attirent également l’attention. L’Institut Fraunhofer, par exemple, teste le dépôt de métal par laser (LMD) avec des composés métalliques. Cela souligne la tendance du marché à la fabrication additive avec des matériaux composites. On s’attend également à voir encore plus de technologies permettant l’impression avec des matériaux composites à l’avenir.
La technologie varie selon le type de matériau composite choisi. Les composites à fibres discontinues peuvent être extrudés en utilisant le procédé FDM normal, puisque le filament contient déjà la fibre. Cependant, il faut tenir compte du fait que la qualité d’impression est affectée par la quantité de fibres employée. Les composites à fibres courtes renforcent uniformément l’ensemble de la pièce. Cependant, au-delà d’un certain seuil, la pièce imprimée en 3D perd en qualité de surface. D’autre part, l’impression 3D à fibre continue est un processus plus compliqué, qui nécessite deux buses pour imprimer simultanément. Typiquement, une buse extrude le thermoplastique et l’autre la fibre. Un exemple d’imprimante fonctionnant ainsi est la Mark Two, de Markforged. La machine insère les matériaux à fibres longues dans les pièces qu’elle crée à l’aide du procédé FDM. De cette manière, les pièces ne sont renforcées qu’aux emplacements nécessaires.
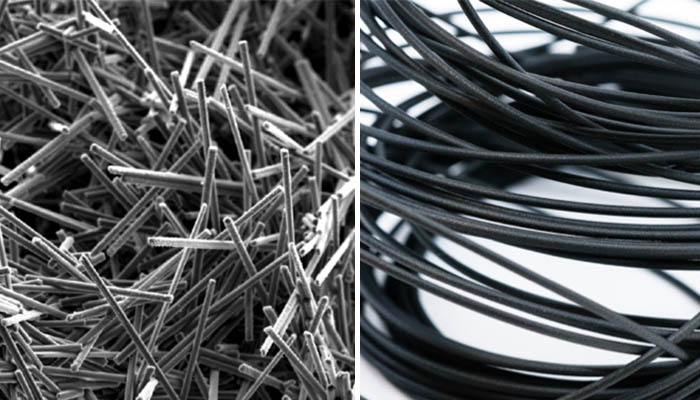
Sur la gauche, vous pouvez voir des fibres courtes, constituées de segments de moins d’un mm de longueur. A droite, le filament a été renforcé par ces fibres courtes (crédits photo : Markforged)
Dans l’impression 3D FDM avec des composites, une buse de diamètre plus important est souvent nécessaire. Normalement, le fabricant spécifie quel réglage doit être effectué. Pour la fibre de verre, la buse doit être réglée sur au moins 0,6 mm de diamètre, pour la fibre de carbone sur 0,4 mm et pour le kevlar, commencez par 0,6 mm, puis diminuez progressivement jusqu’à 0,4 mm. Si le composite contient des particules de bois, il faut régler le diamètre entre 0,6 mm et 0,8 mm.
Gardez également à l’esprit que les filaments composites peuvent entraîner une usure accrue de la tête d’impression, des tuyaux et des composants de l’extrudeur. Pour éviter cela, il est recommandé d’utiliser des buses durcies, en particulier pour les filaments de carbone, de verre et de Kevlar. Il est également important de bien positionner la bobine lors de l’impression pour optimiser le chemin vers l’extrudeur, et de s’assurer qu’elle ne soit pas trop longue. En plus de ces précautions, en raison de la viscosité plus élevée des filaments composites, la vitesse d’impression doit également être réduite. Malgré cela, les matériaux composites offrent l’avantage de ne pas se rétracter lorsqu’ils sont refroidis et sont donc moins susceptibles de produire des erreurs d’impression telles que le gauchissement.

Le cadre de vélo d’AREVO a été créé à l’aide de l’impression 3D à filaments continus (crédits photo : AREVO)
Les applications des matériaux composites
La possibilité d’imprimer avec des matériaux de renforcement a été l’un des objectifs de nombreuses sociétés d’impression 3D et start-ups. Ces dernières années, nous avons vu de plus en plus de machines et de technologies arriver sur le marché pour permettre de nouvelles applications, en particulier dans des secteurs tels que l’aérospatiale et l’automobile. Comme nous l’avons mentionné, la fibre de carbone est l’un des composites les plus largement utilisés dans l’impression 3D, en particulier pour les applications exigeantes telles que les prototypes fonctionnels, les pièces automobiles et les composants solides mais légers. Pour cette raison, les composites en fibre de carbone deviennent également de plus en plus populaires dans le secteur du sport. Les athlètes d’élite se tournent vers le carbone pour créer des vélos plus légers et donc plus rapides. Ces avantages sont également utilisés dans la Formule 1, le secteur automobile et même des sports comme le tennis et l’aviron.
Le marché des matériaux composites est en croissance et de nouvelles combinaisons de matériaux rendront possibles de nouvelles applications. Les matériaux d’ingénierie explorent l’utilisation de composants additifs de renforcement. En Chine, des chercheurs ont étudié les avantages de l’ajout de fibres de carbone à des thermoplastiques hautes performances tels que le PEEK, et Sandvik a créé le premier composite de diamant en 2019. Le diamant est normalement impossible à utiliser dans la fabrication additive car il est trop dur. Cependant, en créant un composite de diamant, les propriétés du matériau peuvent être utilisées pour de nombreux outils solides (exploitation minière, forage ou usinage) et aussi pour les implants médicaux !
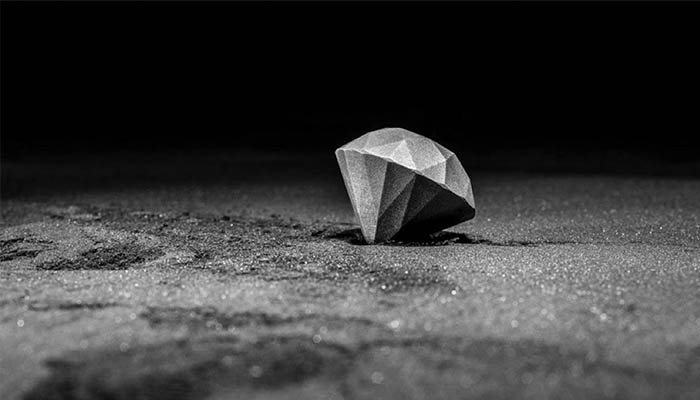
Le composé de diamant créé par Sandvik (crédits photo : Sandvik)
Fabricants d’imprimantes 3D et de filaments composites
Évidemment, les composites sont souvent plus chers que les matériaux standards. Même ainsi, les prix varient en fonction du fabricant et du composé utilisé. Le prix des coils oscille entre 150 et 500 euros. Un matériau composite nécessite également une imprimante qui possède des propriétés particulières pour son utilisation. Ces types d’imprimante sont souvent accompagnés de leur propre technologie, que les fabricants décrivent et commercialisent différemment. Markforged, par exemple, a développé la technologie CFF (Continuous Carbon Fiber) pour les imprimantes composites qu’elle propose. De son côté, Anisoprint l’a appelée CFC (Continuous Fiber Coextrusion). Un nom bien connu qui rejoint la liste des imprimantes composites est Stratasys. Avec les imprimantes 3D F190 CR et F370 CR, Stratasys a élargi la série F123 pour proposer des imprimantes compatibles avec les matériaux composites, en particulier ceux qui présentent une rigidité et une résistance élevées.
Une autre technologie intéressante est celle brevetée par AREVO. Celle-ci est basée sur la technique de distribution de puissance directionnelle, qui utilise un laser pour chauffer simultanément le filament et la fibre de carbone tandis qu’un rouleau presse les deux ensemble. La société suisse 9T Labs, par exemple, a développé un système complémentaire pour les imprimantes 3D normales qui permet l’impression 3D de composites. Ils appellent ce processus d’impression 3D AFT (Additive Fusion Technology). Enfin, Continuous Composites utilise une technologie hybride dans laquelle le fil de fibre est imprégné de résine puis durci à la lumière UV, de façon similaire à l’impression 3D SLA.
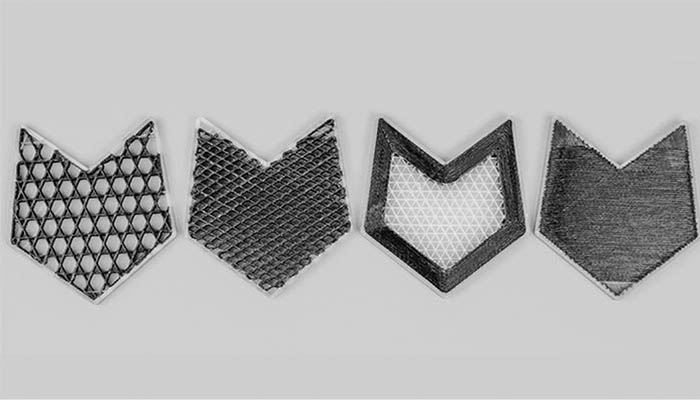
Le logiciel Anisoprint peut créer différents types de remplissages continus renforcés de fibres (crédits : Anisoprint)
Des noms bien connus peuvent également être trouvés parmi les fabricants de filaments composites. Markforged propose des composites en fibre de verre et Kevlar. Owens Corning est également connu pour ses matériaux renforcés de fibre de verre. Formfutura, BASF et XYZPrinting ont également ajouté le filament composite à leur gamme. Parmi les matériaux composites à fibres courtes, il convient de noter les fabricants de filaments Roboze, 3DXTech et ColorFabb.
Que pensez-vous du guide complet sur l’impression 3D de composites ? Partagez votre avis dans les commentaires de l’article. Retrouvez toutes nos vidéos sur notre chaîne YouTube ou suivez-nous sur Facebook ou Twitter !
*Crédits photo de couverture : SABIC