Quelles sont les applications de l’impression 3D dans le secteur automobile ?
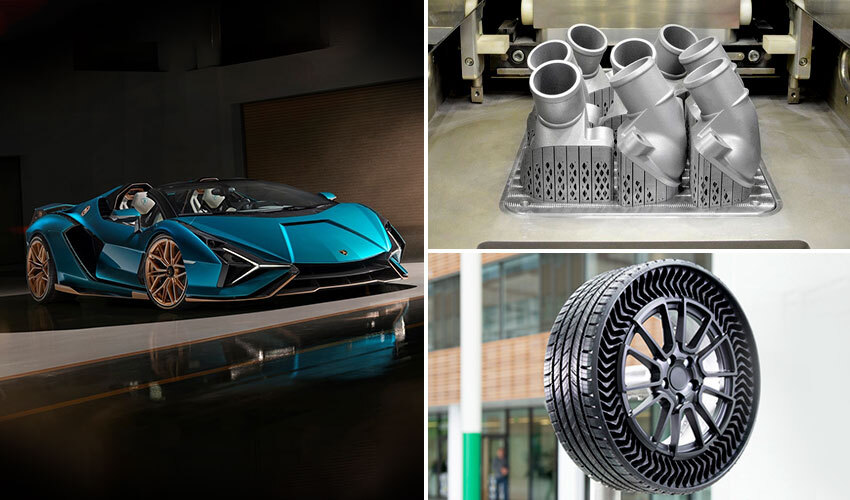
Parmi les secteurs qui utilisent les technologies de fabrication additive, l’industrie automobile est l’un de ceux qui en tirent le plus profit. Cette technologie permet aux constructeurs automobiles de réduire leurs coûts, le temps de fabrication et le poids des pièces devenues de plus en plus complexes. La fabrication additive permet également une plus grande personnalisation au niveau de la conception, transformant ainsi les modèles de voitures en des expériences d’utilisation inoubliables. Avec la croissance importante que connaît l’impression 3D dans l’industrie automobile, les revenus générés devraient atteindre les 12,4 milliards de dollars d’ici 2028. Pour mieux comprendre l’impact de cette technologie sur l’industrie, nous avons choisi quelques cas d’applications concrets qui montrent comment l’impression 3D bouleverse le secteur automobile. Ici, il s’agira davantage de pièces imprimées en 3D que de voitures conçues par impression 3D. Nous les avons classés par constructeur et par ordre alphabétique.
Audi accélère la conception automobile
Audi est une multinationale allemande qui se consacre à la fabrication de voitures haut de gamme et de sport. Elle fait partie du groupe Volkswagen depuis 1965. Il y a quelques années, l’entreprise a décidé d’utiliser les solutions Stratasys dans le but d’accélérer la conception automobile. La technologie PolyJet a permis à Audi de développer et d’évaluer différents prototypes avant de produire les pièces d’un véhicule. En intégrant l’imprimante 3D J750 dans sa gamme, le fabricant a pu étendre la production de modèles tels que les enjoliveurs de roues, les grilles, les poignées de porte ou même les cabochons de feux arrière, qui sont généralement en plastique transparent. Grâce à l’impression 3D, ils ont pu accélérer la conception automobile et la création des pièces finales, répondant ainsi aux exigences de leurs clients.
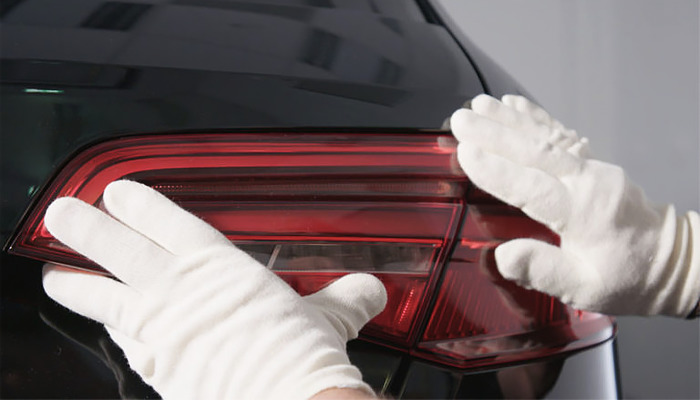
Audi a utilisé la technologie PolyJet pour concevoir différentes pièces pour ses voitures
Bentley : plus de 15 000 pièces imprimées en 3D en 2021
Si le constructeur automobile britannique Bentley est réputé pour ses carrosseries prestigieuses, l’entreprise se veut ambitieuse dans le développement de l’impression 3D au sein de son processus de production. Avec un investissement de plus de 3 millions d’euros, Bentley a imprimé en 3D plus de 15 000 pièces en 2021, ce qui a permis au constructeur de limiter la quantité de déchet générée et de gagner du temps en termes de fabrication. Outre ces avantages, la technologie offre également aux clients de l’entreprise la possibilité de bénéficier de composants entièrement individuels et personnalisés.
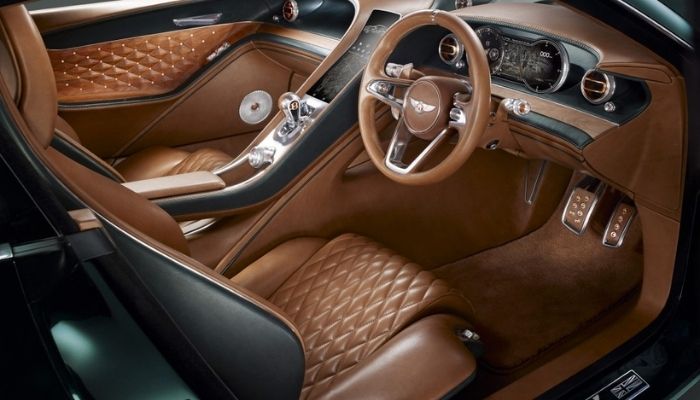
Crédits photo : Bentley
BMW opte pour la fabrication additive
La société allemande BMW, basée à Munich, utilise la fabrication additive depuis plus de 25 ans et a été l’un des premiers constructeurs automobiles à intégrer cette technologie. Pour elle, l’impression 3D dans l’industrie automobile est un pari qui s’est avéré fructueux. En juin 2020, le constructeur a ouvert son propre centre de fabrication additive dans le but de mettre en commun ses compétences de production. Ce campus compte plus de 80 employés et plus de 50 solutions de fabrication industrielle. BMW a démontré ses capacités à de nombreuses reprises, par exemple avec le modèle sportif Roadster i8. Celui-ci intègre des pièces qui sont beaucoup plus légères que si elles avaient été créées selon des méthodes traditionnelles. Des pièces telles que le support de son toit décapotable sont désormais plus solides et plus légères.
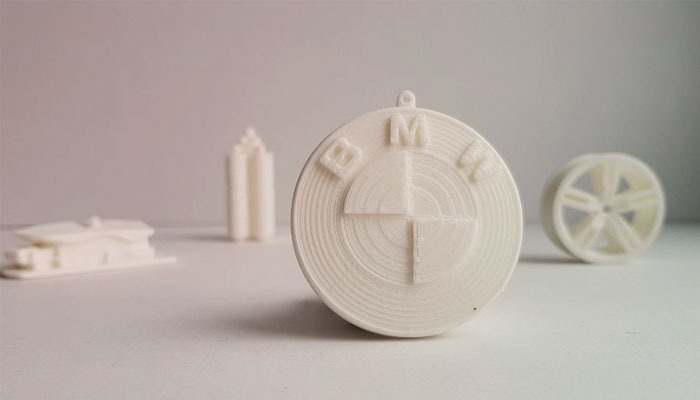
BMW est l’un des premiers constructeurs automobiles à avoir investi dans la fabrication additive
La Bugatti Bolide, un véhicule léger et rapide grâce à l’impression 3D
Afin de créer son véhicule qui est probablement le plus léger et le plus rapide à ce jour, le constructeur automobile français Bugatti s’est tourné vers la fabrication additive. Baptisée Bugatti Bolide, la voiture de sport est dotée de plusieurs pièces imprimées en 3D réduisant ainsi considérablement le poids de ses composants. Parmi les pièces conçues grâces à la fabrication additive, on retrouve par exemple des tiges de poussée de 100 grammes seulement, un support de montage pour l’aile avant ainsi que des compresseurs radiaux. Afin d’obtenir des pièces aux géométries complexes, Bugatti confie avoir utilisé l’optimisation topologique.
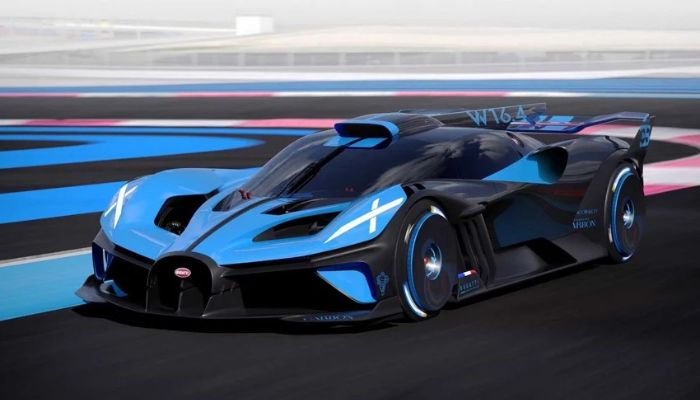
Crédits photo : Bugatti
Dallara et ses échangeurs de chaleur imprimés en 3D
Le constructeur automobile italien Dallara a fait appel à l’entreprise Conflux Technology pour fabriquer les échangeurs de chaleur de ses voitures de Formule 3. Celle-ci s’appuie sur la fabrication additive pour obtenir des pièces plus performantes et plus résistantes à la chaleur. Elle utilise plus précisément des machines de fusion laser sur lit de poudre de EOS. La particularité de ce projet réside dans la taille des échangeurs : en effet, Dallara avait besoin de composants petits qui puissent respecter les exigences du sport automobile. Conflux Technology a donc imaginé plusieurs conceptions CAO et CFD et imprimé plusieurs itérations pour valider la géométrie et étudier les caractéristiques de la pièce telle que la rugosité de surface.
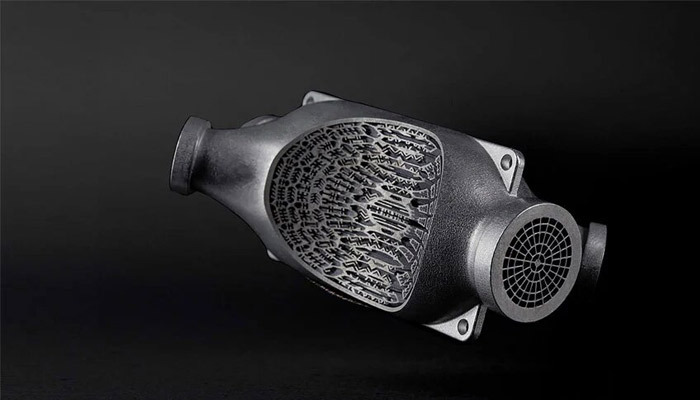
Crédits photo : Conflux Technology
Ferrari et la fabrication additive métal
La fabrication additive a un rôle clé dans le sport automobile permettant de concevoir des pièces plus légères, résistantes et performantes, dans des délais beaucoup plus courts. Le constructeur Ferrari a donc misé sur cette technologie – en particulier l’impression 3D métal – pour imaginer les pistons de l’un de ses moteurs. Ferrari explique avoir utilisé une machine EOS et de la poudre de titane et que la fabrication additive lui a permis d’imaginer une pièce beaucoup plus complexe, résistante et légère grâce notamment à l’optimisation topologique. Cette méthode augmente également le nombre d’itérations possibles : l’entreprise peut imaginer autant de designs nécessaires et accélérer sa phase de prototypage. Le constructeur a également conçu des pédales de frein imprimées en 3D avec une structure creuse – un résultat qui n’aurait pas été possible via d’autres méthodes de fabrication.
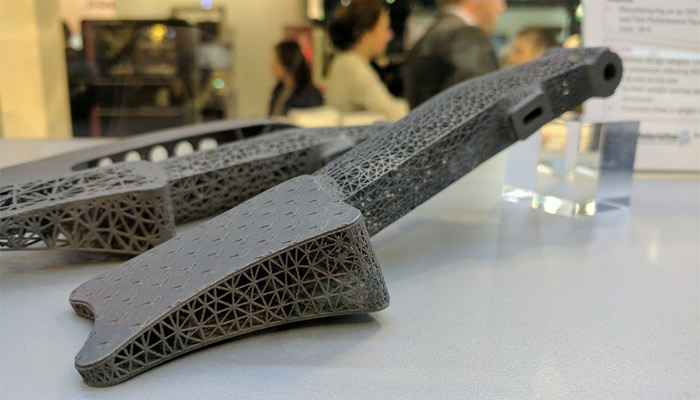
Les pédales de frein imprimées en 3D
Les projets d’impression 3D automobile de Ford
En 1988, le constructeur automobile Ford avait déjà investi dans 3 imprimantes 3D ; en 2015, il estimait sa production de pièces imprimées en 3D à 500 000, preuve que la technologie a une place de taille pour l’entreprise américaine. Et pour cause, celle-ci a noué de solides partenariats avec certains fabricants comme Desktop Metal ou encore Carbon. Si on se penche sur les pièces réalisées par Ford, on est obligé de vous parler de son collecteur d’admission d’air en aluminium, l’une des plus grandes pièces métalliques imprimées en 3D pour l’automobile. Il pèse 6 kilos et a été réalisé en 5 jours seulement. Plus récemment, l’américain a imaginé des écrous de roue sur-mesure pour protéger les jantes. Imprimés sur des machines EOS, ces écrous ont été modélisés à partir de la voix du conducteur : celle-ci est convertie en modèle 3D et imprimée à l’intérieur de l’écrou. Une méthode efficace pour lutter contre les vols puisque seule la voix du conducteur permettrait de retirer les écrous.
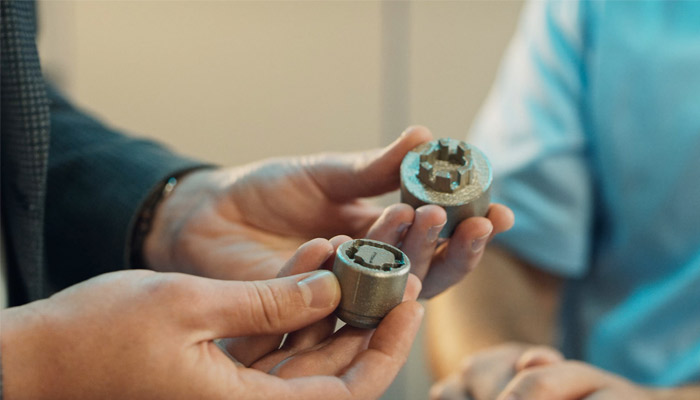
Les écrous imprimés en 3D sont modélisés d’après la voix du conducteur
Fraunhofer IAPT et l’approche « Design to Cost »
L’institut Fraunhofer for Additive Production Technologies (Fraunhofer IAPT) a dévoilé début 2022 l’importance des paramètres d’impression et des mesures d’optimisation aujourd’hui employées sur le marché. En utilisant une approche « Design to Cost », l’entreprise a démontré comment, grâce à une optimisation continue de la chaîne de valeur de l’impression 3D, il était possible d’influencer sur le coût et le poids d’une charnière de porte automobile. La Fraunhofer IAPT confie que cette méthode permettrait de réduire les coûts de production de près de 80 %. De plus, ce processus optimisé ouvrirait la porte à la production en série de pièce imprimées en 3D, et donc à la démocratisation de la technologie.
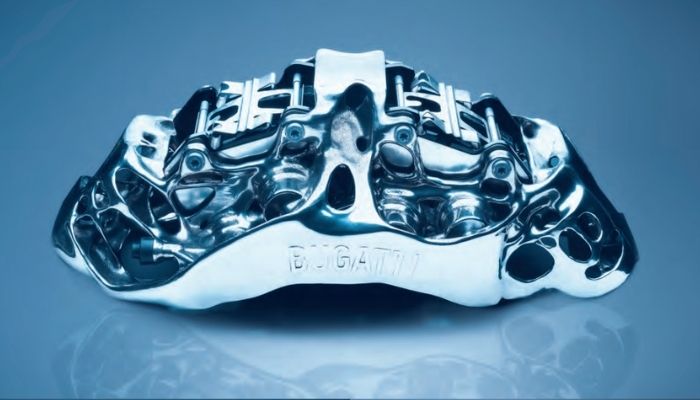
Crédits photo : Fraunhofer IAPT
Lamborghini et la Sian Roadster
Lamborghini est la définition des voitures de sport de luxe coûteuses. Le constructeur cherche à offrir une véritable expérience à chaque conducteur, à la fois en termes de performances mais aussi de confort et d’esthétique. C’est sûrement l’une des raisons qui l’a poussé à opter pour la fabrication additive : il fallait concevoir un véhicule personnalisable. Or, avec l’impression 3D, les possibilités d’adaptation sont quasi illimitées. Lamborghini offre à chaque acheteur de la Sian Roadster un contrôle total sur l’intérieur ainsi que sur certaines finitions de peinture. Par exemple, les sorties d’air redessinées ont été imprimées en 3D et permettent aux clients de les personnaliser en intégrant, entre autres, leurs initiales dans le design.
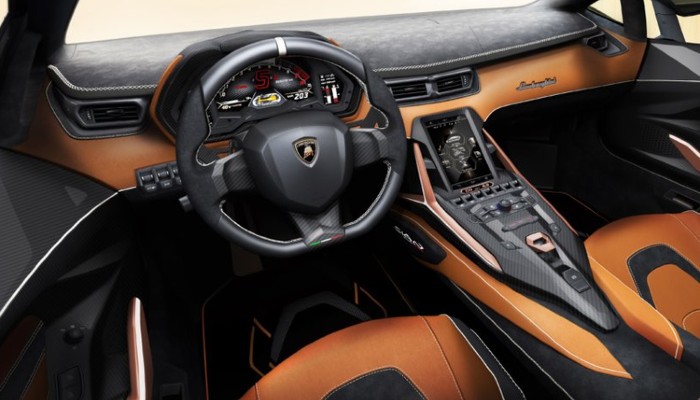
Le conducteur peut personnaliser l’intérieur de sa voiture
La nouvelle supercar hybride Artura de McLaren
Comme de nombreuses autres marques automobiles, le constructeur de voitures McLaren a recours à l’impression 3D. Pour concevoir sa première supercar hybride haute performance Artura, l’entreprise britannique a associé technologie et design. En optant pour l’impression 3D métal, McLare a fabriqué des noyaux du bloc moteur, qui permettrait à la voiture d’obtenir un meilleur refroidissement du moteur et donc de bénéficier de meilleures performances. De plus, l’équipe de conception a utilisé de la fibre de carbone pour concevoir un châssis plus léger. À travers ces différentes pièces, McLaren a souhaité rendre sa voiture plus légère, et donc plus rapide.
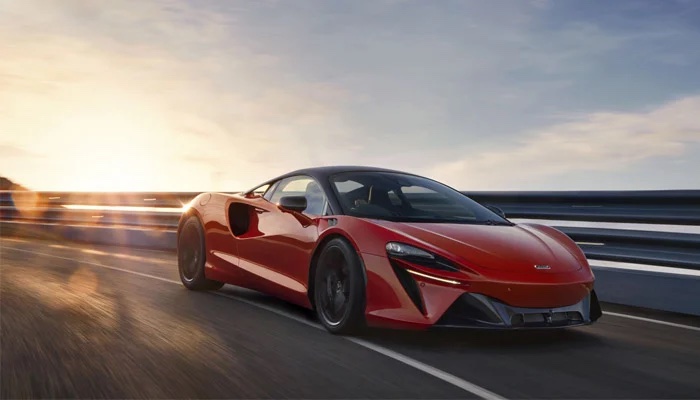
Crédits photo : McLaren
Mercedes et les usages de la fabrication additive
L’industrie automobile ne se limite pas aux véhicules pour le transport de personnes mais comprend également des véhicules pour le transport de marchandises, c’est pourquoi il nous paraissait important de parler des camions de Mercedes. Après s’être d’abord concentré avec succès sur l’impression 3D de pièces en plastique, Mercedes fabrique maintenant des pièces de camion en métal. En utilisant la fabrication additive métal, les pièces de rechange deviennent plus résistantes et plus souples. Un autre avantage est que Mercedes a la possibilité de produire ces pièces en petites quantités et à faible coût. Mercedes est la première entreprise à se concentrer sur la production de pièces détachées pour camions. Si Mercedes est la première entreprise à se concentrer sur la production de pièces détachées pour camions, elle utilise également la technologie pour optimiser certaines de ses voitures. Pour l’un de ses derniers véhicules, l’EQXX, la marque allemande a eu recours aux technologies 3D pour réduire le poids des composants et pour limiter les coûts et temps de fabrication.
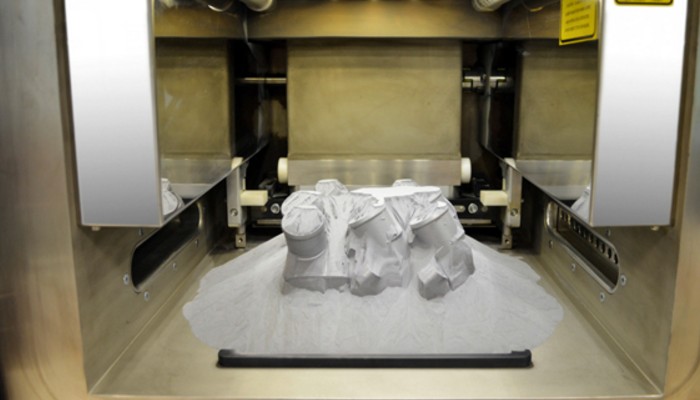
Mercedes se penche sur l’impression 3D de pièces détachées
Michelin et son pneu imprimé en 3D
Le fabricant de pneus français, Michelin, a présenté son premier prototype de pneu utilisant des technologies de fabrication additive en 2019. Appelés Uptis (Unique Puncture-proof Tire System), ces pneus ont été conçus pour être sans air afin de réduire le risque de crevaison. La société a travaillé avec l’entreprise américaine General Motors pour développer le prototype imprimé en 3D. De plus, l’entreprise confie que la fabrication additive pourrait être utilisée pour réparer si besoin la bande de caoutchouc limitant les risques de crevaison. Comme un témoigne de réussite, les pneus Uptis ont parcouru leurs premiers kilomètres en 2021. Et suite à ce succès, la société souhaite passer à la commercialisation d’ici 2024. À ce jour, l’impression en 3D n’a été utilisée que pour développer le prototype, en utilisant des matériaux renouvelables et bio-sourcés, mais si la production devait atteindre des volumes plus importants, la technologie pourrait être employée à plus grande échelle. Réduisant les déchets et promouvant une mobilité durable, les pneus Uptis intègrent une structure souple renforcée en fibres de verre et en caoutchouc, placée sur une roue en aluminium.
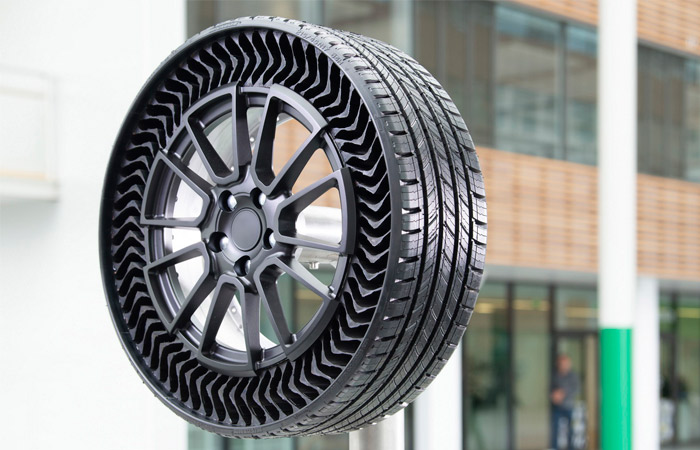
Le pneu Uptis
La MINI Strip, une voiture durable grâce à l’impression 3D
En optant pour l’impression 3D, le constructeur automobile britannique MINI confirme sa volonté de proposer des voitures plus durables. En effet, imaginée par le designer Paul Smith, la MINI Strip se veut respectueuse de l’environnement. Pour ce faire, les équipes à l’origine du projet ont imprimé en 3D différentes pièces à partir de matériaux recyclés. Parmi eux, on peut citer les tapis de sol fabriqués à partir de caoutchouc recyclé, les panneaux de dessous de porte ou encore les enjoliveurs. En plus de rendre la voiture plus durable, ces multiples pièces imprimées en 3D confèrent à la MINI Strip une géométrie simplifiée et un design épuré.
Les applications de l’impression 3D par Porsche
Tout le monde connait le célèbre constructeur de voitures de luxe Porsche, mais peu de personnes se doutent que ce dernier a recours à la fabrication additive depuis le début des années 1990. Et l’entreprise ne cesse développer de nouvelles applications. En 2020, le géant de l’automobile a imprimé en 3D des pistons de moteur pour la toute première fois. Les composants ont été conçus pour le moteur haute performance de la Porsche 911 GT2. L’impression 3D a permis d’optimiser les pistons et, par conséquent, de rendre cet élément moteur essentiel 10 % plus léger que les pistons fabriqués de manière traditionnelle. La société a également imprimé en 3D un boîtier de transmission électrique, qui serait lui 40 % plus léger. Fin 2021, Porsche a annoncé avoir investi dans Intamsys, un fabricant chinois d’imprimantes 3D spécialisé dans les matériaux haute performance.
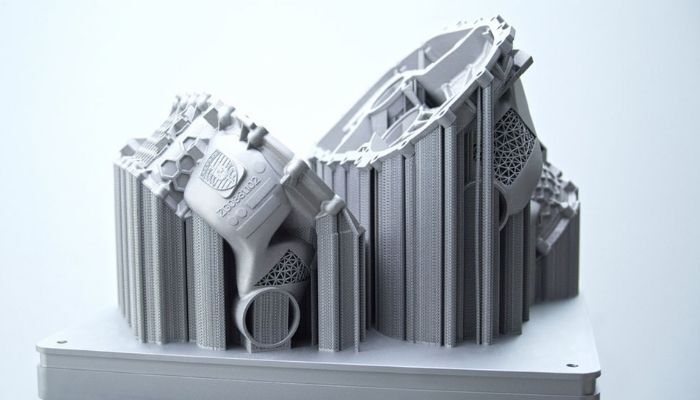
Crédits photo : Porsche
SEAT et l’impression 3D automobile
Le fabricant espagnol SEAT vient d’achever un nouveau bâtiment de 3 000 m2 qui unifiera tous les processus et activités avant la production en série d’un nouveau modèle. Un grand espace dans le nouveau centre sera consacré aux projets de fabrication d’additive. Le centre de SEAT abrite plusieurs imprimantes 3D, neuf pour être précis. Les machines comprennent : une HP Multi Jet Fusion, une machine SLS, 6 imprimantes 3D FDM et une solution PolyJet. Grâce à la diversité de ces technologies, SEAT est en mesure de produire des pièces plus ou moins détaillées, avec des propriétés mécaniques importantes et des fonctionnalités avancées. Les machines fonctionnent 24 heures sur 24 et produisent en moyenne 50 pièces par jour. Selon le constructeur, 80% des pièces sont des prototypes utilisés pour développer plus rapidement des véhicules, le reste étant principalement des composants d’outillage et de personnalisation.
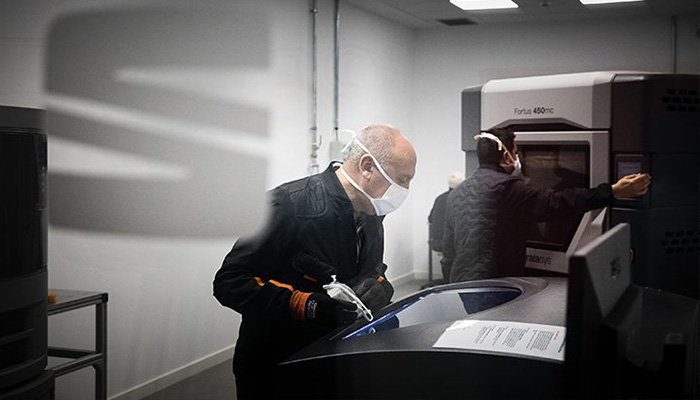
SEAT a ouvert un centre de fabrication additive
Vital Auto et les voitures du futur
Fondé en 2015, le studio de design industriel britannique Vital Auto est spécialisé dans le design automobile. Parmi les illustres clients de la société figurent de nombreux constructeurs automobiles mondiaux, tels que Volvo, Nissan et McLaren. Et afin de leur offrir des prototypes de haute qualité rapidement et à coût réduit, Vital Auto a recours aux imprimantes 3D Form 3L et Fuse 1 de Formlabs. De la conception à la production, l’entreprise a intégré la fabrication additive dans l’ensemble de son processus de production. Les équipes de Vital Auto expliquent : « Nous avons utilisé l’impression 3D dès le premier jour, non seulement pour réduire les coûts, mais aussi pour donner au client plus de diversité dans ses conceptions et ses idées. La partie la plus intéressante des imprimantes 3D est leur polyvalence, la possibilité de changer de matériau en moins de cinq minutes et la variabilité de ces matériaux, de doux et flexibles à durs et rigides, n’a pas de prix pour nous.«
YOYO, le véhicule électrique imprimé en 3D
Alors que le réchauffement climatique s’aggrave de jour en jour, de plus en plus de personnes se tournent vers des alternatives plus écologiques aux produits traditionnels, notamment les voitures électriques. Et à cet égard, l’impression 3D ne fait pas exception à la règle. L’entreprise italienne XEV a lancé en mai 2021 une voiture de ville entièrement électrique baptisée Yoyo. Conçue majoritairement grâce à la fabrication additive grand format, la voiture est selon l’entreprise la solution la plus durable en ce qui concerne la mobilité urbaine. Grâce aux technologies 3D, l’équipe à l’origine du projet explique avoir réussi à utiliser moins de pièces pour la carrosserie, moins de matériaux et à baisser les coûts de production. Idéal pour circuler en ville, Yoyo intègre un moteur 100 % électrique d’une autonomie de 160 km.
Que pensez-vous de la place de l’impression 3D dans le secteur automobile ? Partagez votre avis dans les commentaires de l’article ou avec les membres du forum 3Dnatives. Retrouvez toutes nos vidéos sur notre chaîne YouTube ou suivez-nous sur Facebook ou Twitter !
je suis entrain de cree une start-up impression 3d pour les pieces des automobiles et je veux quelques consigne et orientation concernent ce sujet
Cet article met en lumière des applications incroyables de l’impression 3D dans l’industrie automobile ! J’ai particulièrement aimé les exemples concrets sur la fabrication de pièces de rechange et la personnalisation des véhicules. Cela ouvre vraiment de nouvelles perspectives pour l’innovation et la durabilité dans ce secteur. Hâte de voir comment cela évoluera dans les prochaines années !